White paper
Printing Silver Conductive Ink on Cotton Fabric
Printing on fabric is a popular method for creating wearable electronics, with one key application being heated gloves and mittens that use heating elements to keep hands warm. Commonly used in outdoor activities like skiing, they also have medical uses, such as improving blood circulation.
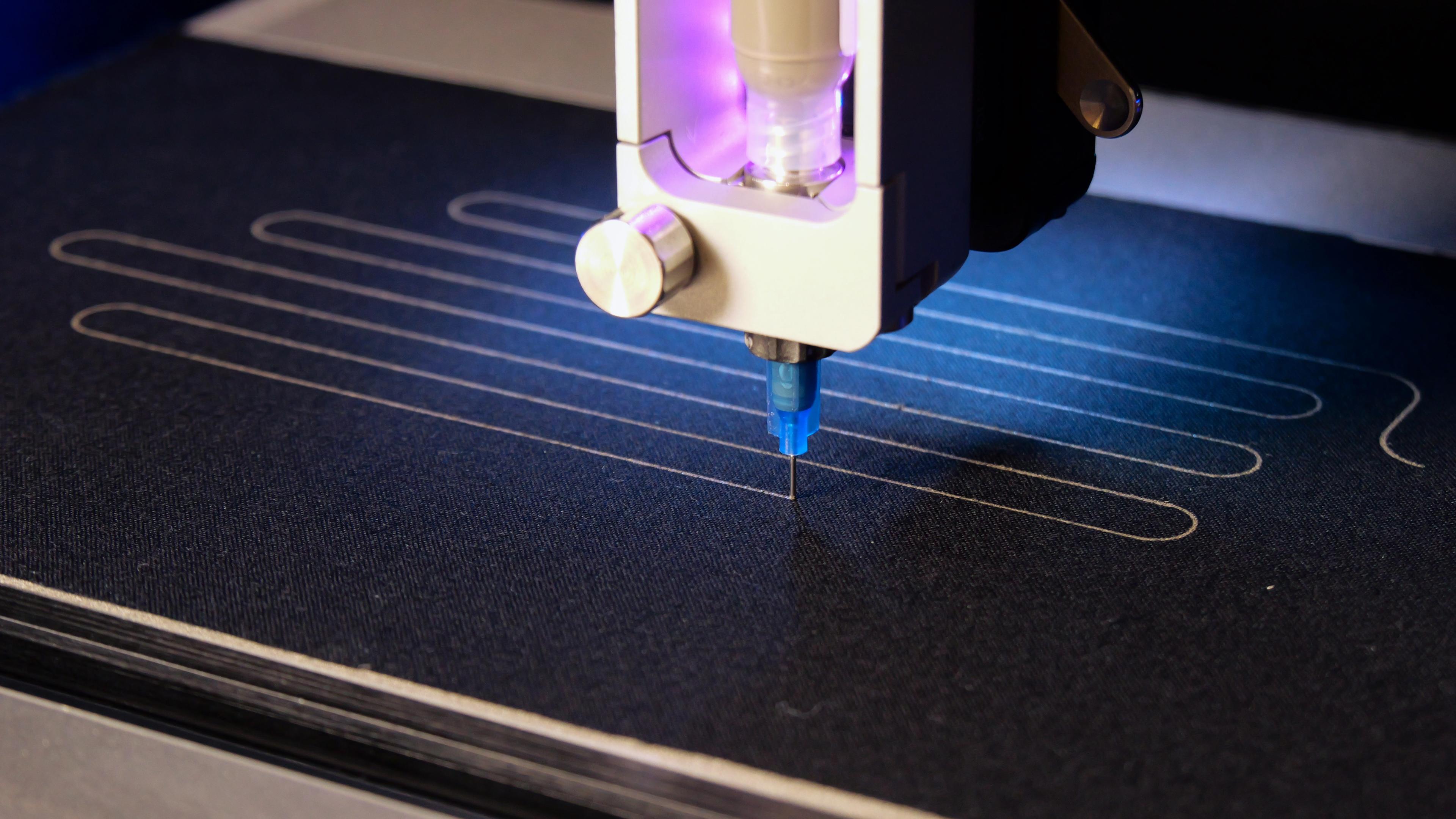
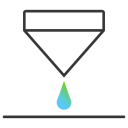
- Cotton fabric
- NOVA materials dispensing system
- Heat press machine
- Voltera branded mitten
- Fleece liner
- Kapton tape
- Metal snaps
- FLIR TG165 thermal camera
Project Overview
Purpose
The purpose of this project was to create a heated mitten utilizing silver conductive ink printed directly onto cotton fabric, as well as validate optimal print settings for working with cotton fabric as a substrate.
Design
We designed a heating element pattern made up of meander lines that resemble a hand with a trace width of 5 mm. We left an opening near the wrist for inserting metal snaps that connect the printed circuit to the power source. We planned to print on both sides of the fabric to allow the ink to penetrate the fibers evenly.



Desired outcome
The goal was to create a functional heated mitten capable of reaching 40°C when powered by a 12V power source, with the duration depending on the battery used and ambient temperature. The cured ink should remain both conductive and stretchable, maintaining its integrity as the hand flexes and relaxes.
Functionality
The printed conductive traces heated up to 40°C when powered at 12V, with the mitten’s temperature adjusting based on different voltage inputs. An internal liner protects the user from direct contact with the heat element, ensuring both comfort and safety.
While this proof of concept was not designed to be wireless, integrating an embedded power supply could make the mitten portable. It could be further customized with a thermistor and LEDs for temperature control and status indication, along with water- and scratch-resistant materials to withstand extreme weather conditions.
Printing the heat-generating conductive traces
Preparing the fabric substrate
Before printing, we ironed the cotton fabric substrate using a heat press machine at 200°C for about 10 seconds to eliminate any wrinkles or surface irregularities, as a smooth surface is essential for optimal ink adhesion. We then used Kapton tape on the bottom side of the fabric to secure the porous fabric to the vacuum bed for the printing process.
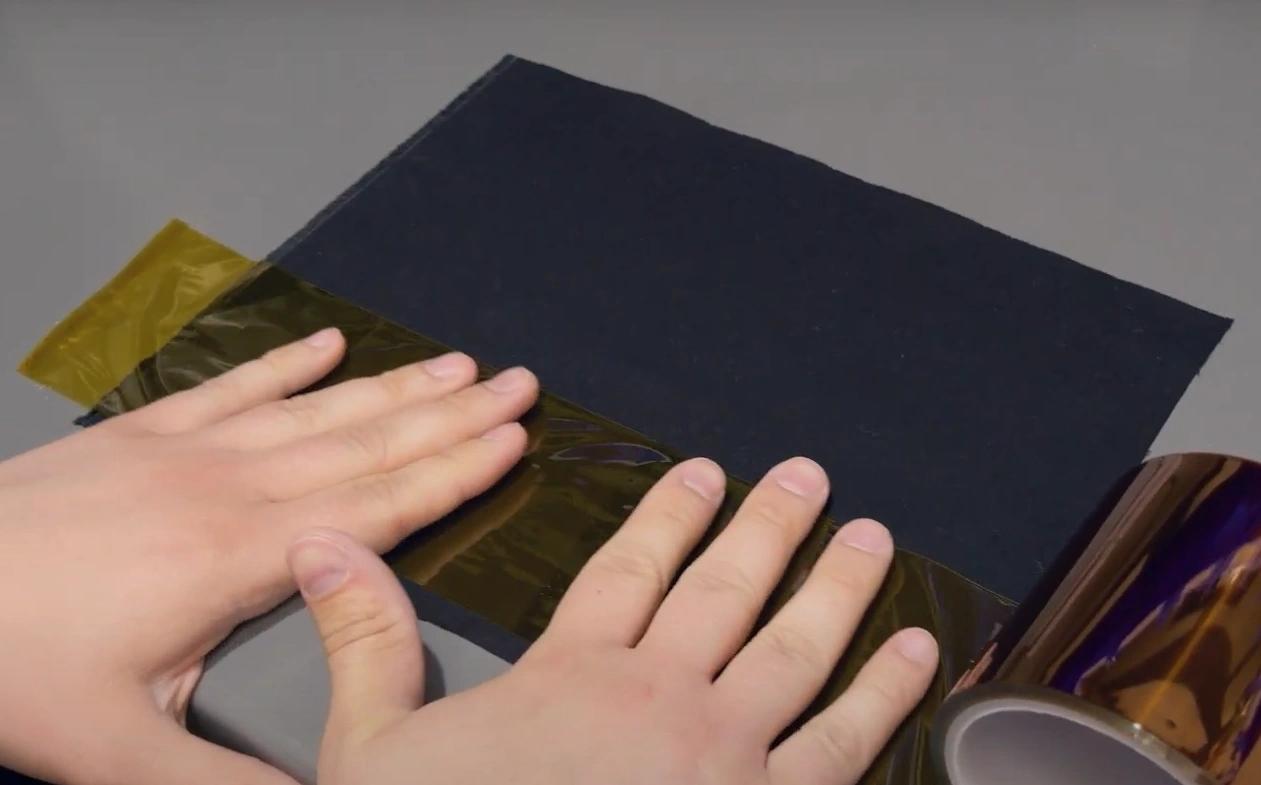

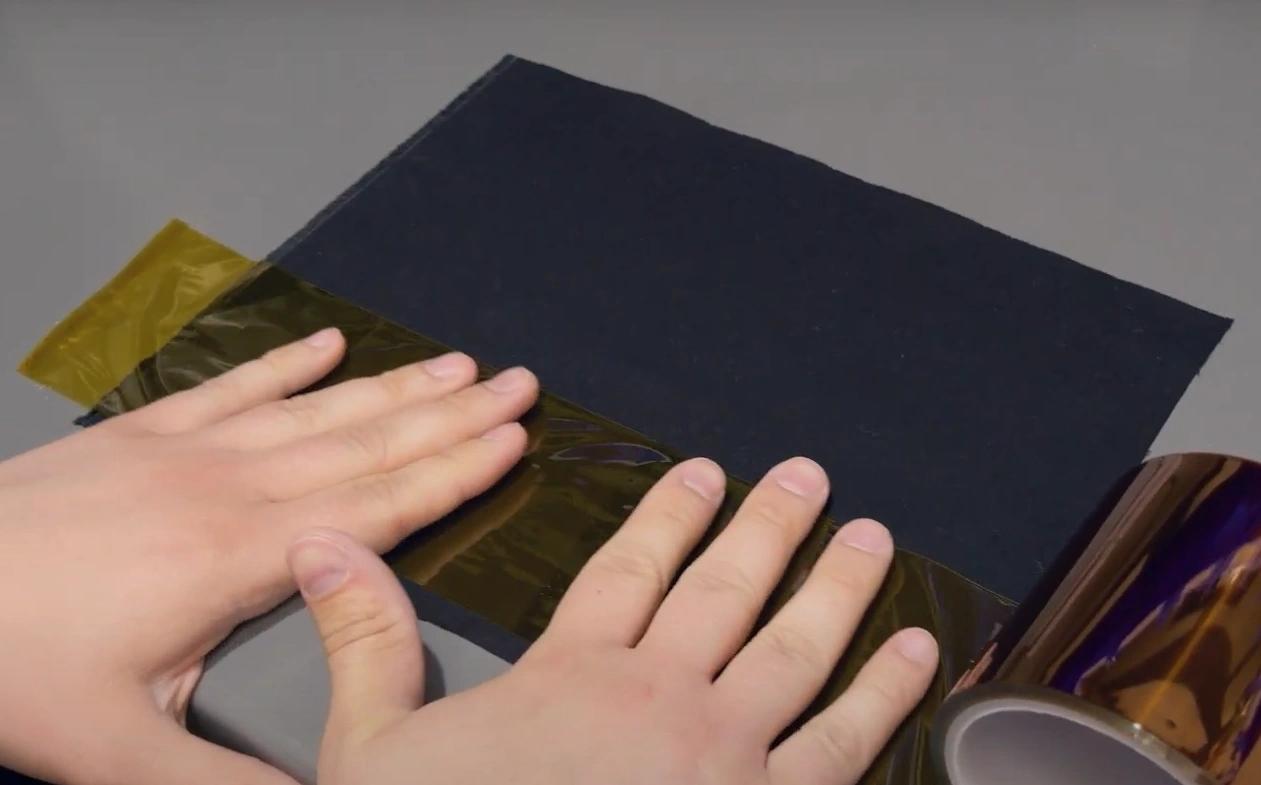
Printing the circuits
We chose the ACI SH5025 Printed Fixed Resistance Heater Ink to print the heating pattern on both sides of the cotton fabric, because this ink is optimized for heating applications integrated onto elastomeric substrates. It not only exhibits a prescribed resistance value when cured, it also has excellent stretchability.
Ink | ACI SH5025 Printed Fixed Resistance Heater Ink |
Substrate | Cotton fabric |
Nozzle Type | Nordson 410um straight barrel general dispensing tip |
Probe Pitch | 10 mm |
Cure Time and Temperature | 5 minutes at 135°C |



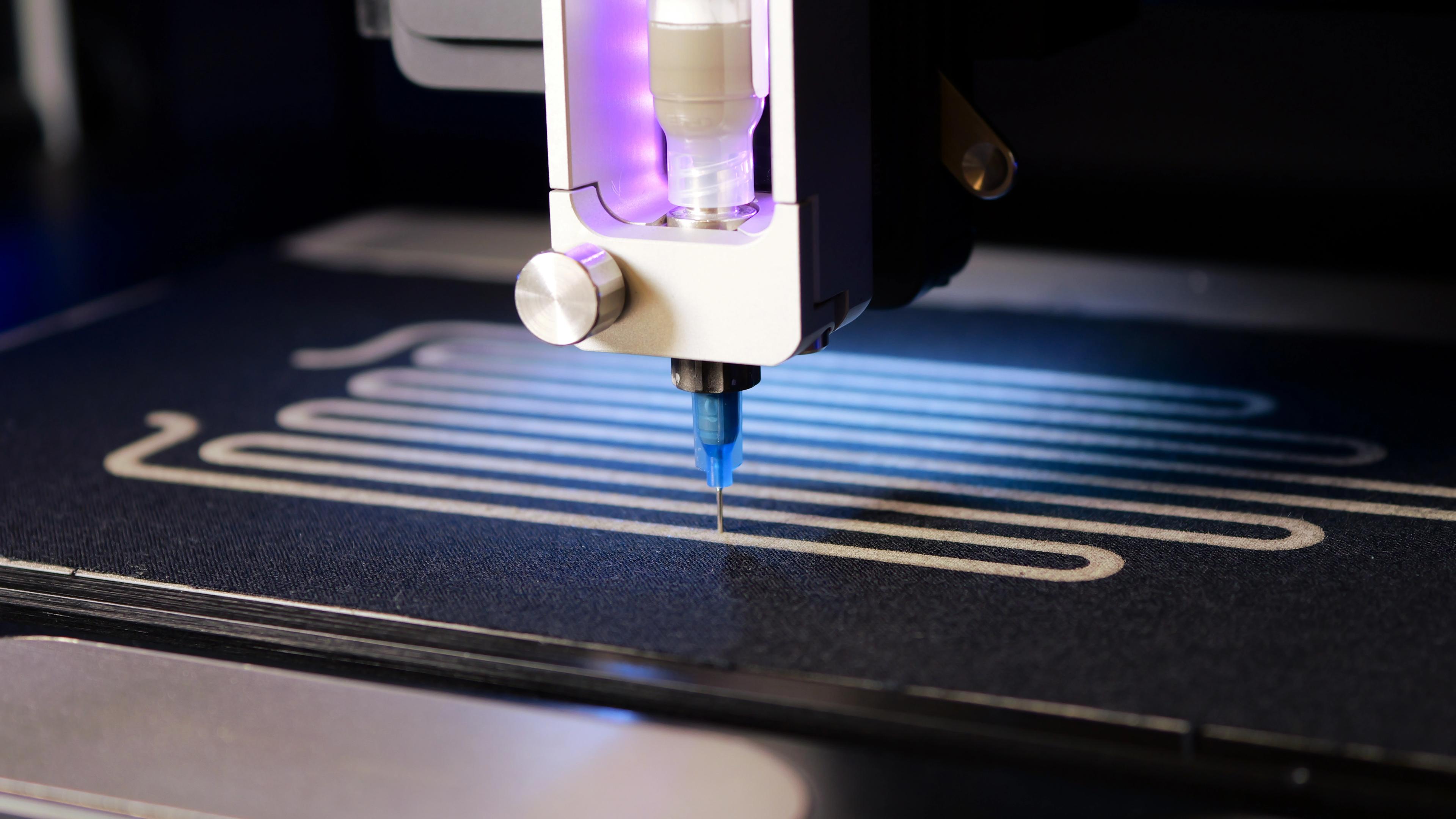

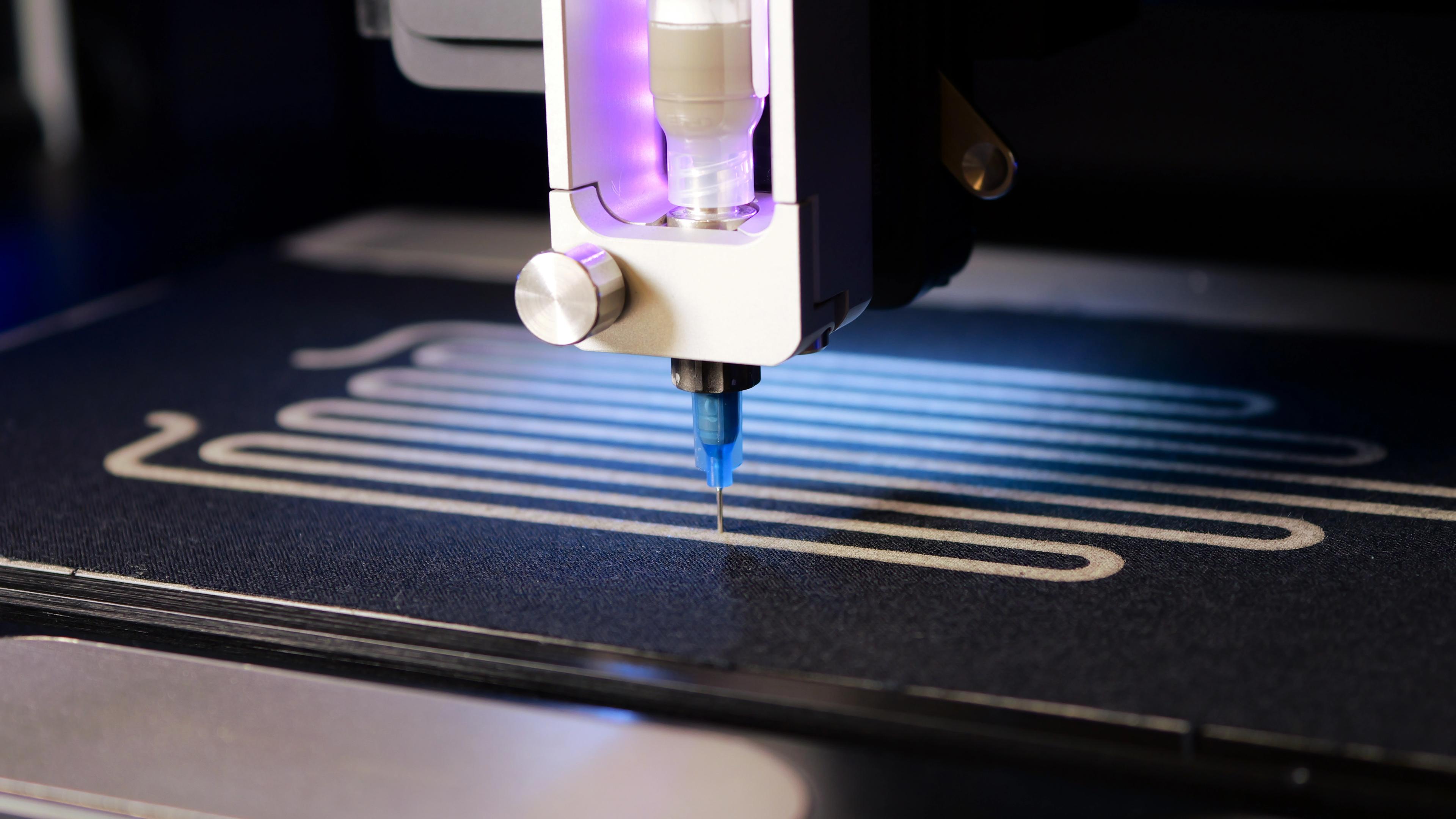
Once the first side was printed, the circuit was cured in an oven for 5 minutes at 135°C. We then took out the fabric, removed the Kapton tape, and applied it to the opposite side. With the aid of a marker, we aligned the features in the software with the printed features on the mitten, and started printing on the opposite side to ensure full connectivity and coverage of the heating elements.



Post-processing the mitten
Because the heated element could reach up to 60°C with a high voltage, we sewed the printed pattern to a liner to protect the user from direct contact with the heated element. We then put the liner into a Voltera branded mitten, inserted a pair of metal snaps, and connected them to power. The mitten heated quickly, as shown by our thermal camera.



Challenges and advice
Choosing the right fabric
Printing on fabric presented several challenges. First, loose weaves can cause the tip of the nozzle to snag or lead to poor ink permeability. As such, choosing tightly woven fabric was critical to the success of this project. We also found that ironing the fabric ensured a uniform surface, and significantly improved print quality.
Retaining conductivity for stretchability
During our first few attempts, we discovered that while the ink is labeled stretchable, it relies heavily on the fabric's properties for flexibility. Setting the nozzle to a low height with a slow print speed and high pressure greatly improved the durability of the printed circuits, as it allowed the ink to saturate the fabric, rather than sitting on the surface.
Conclusion
The printed traces of the mitten reached temperatures of 40°C when powered by a 12V source, and the mitten's temperature could be adjusted by varying the voltage. By optimizing print settings, such as lowering the nozzle height, using high pressure, and printing on both sides of the fabric, we achieved strong ink penetration and conductivity.
While this proof of concept was not wireless, it opens the door for future upgrades. The ability to print directly onto fabric opens up numerous possibilities for consumer and research applications, such as heated clothing for outdoor activities, medical wearables for circulation improvement, and smart textile electronics for advanced monitoring and control.
As we continue to explore the possibilities of wearables, we invite you to view the other projects we’ve completed.