White paper
Printing an RFID Tag with Copper Ink on Paper
Radio Frequency Identification (RFID) is a technology that leverages wireless communication over radio waves to transfer data and locate objects. It is widely used in inventory management, asset tracking, access control, smart packaging, and increasingly, agriculture and crop management.
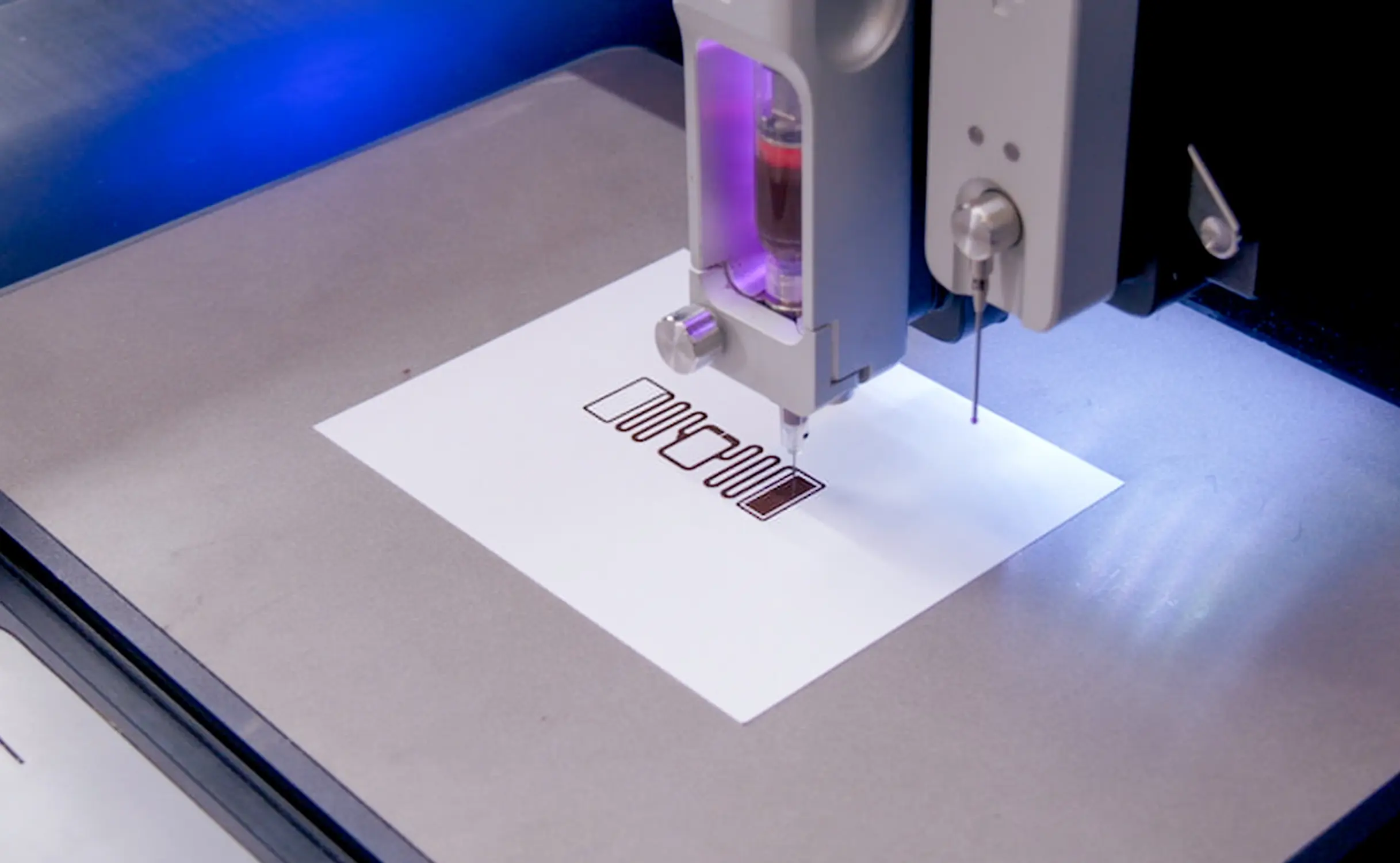
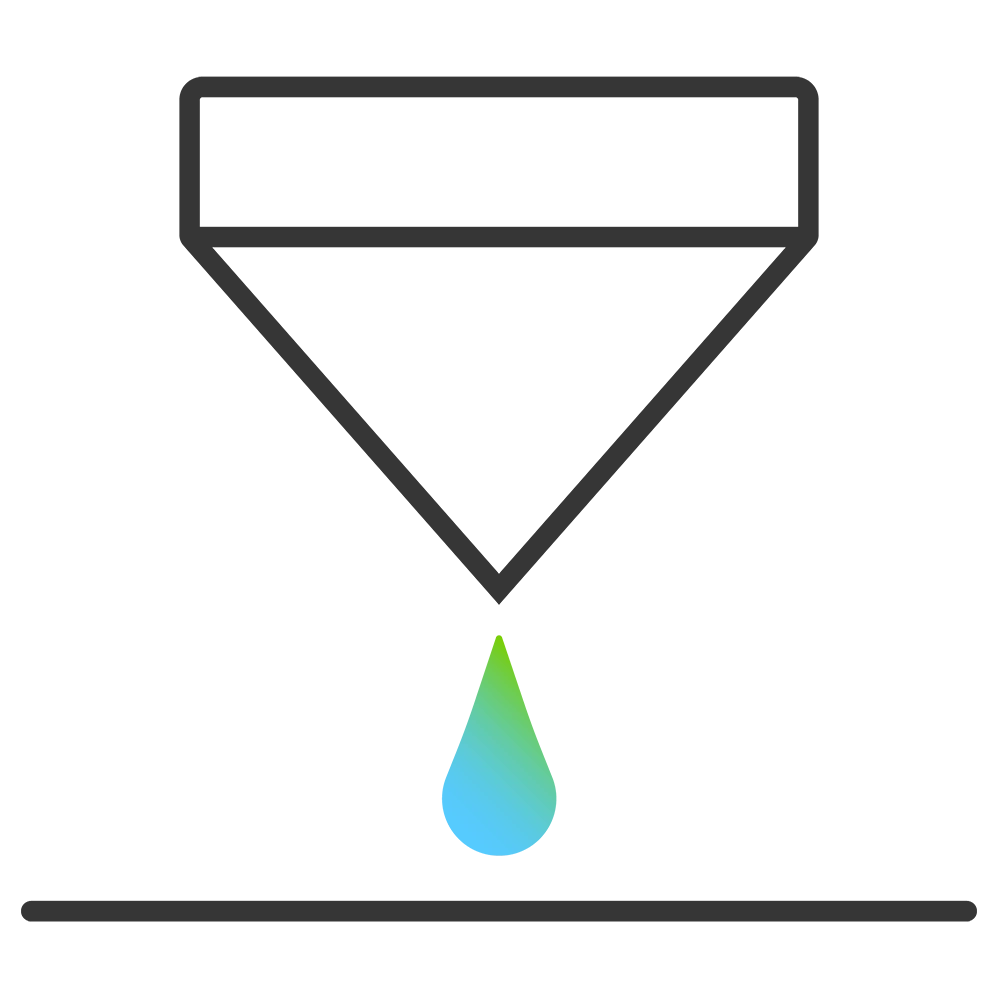
- Cardstock paper (0.26 mm)
Video
Project Overview
Purpose
The purpose of this project was to demonstrate how we used the Voltera NOVA materials dispensing system to create an ultra-high frequency (UHF) RFID tag using nano copper ink on a paper substrate.
Design
We designed a meander half-dipole antenna with an opening at the center to place and solder a transceiver, which controls the antenna and responds to incoming RFID signals. The length of the meander trace was adjusted to ensure we could easily fine-tune the antenna and achieve the best performance.
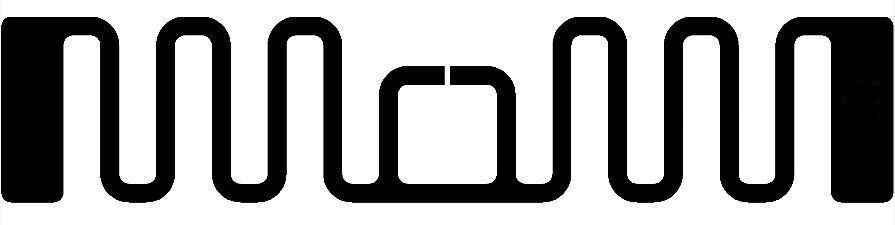
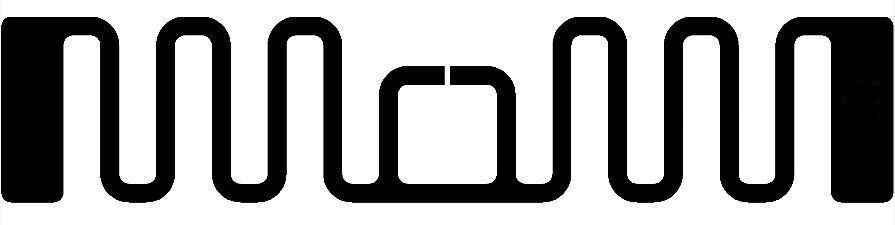
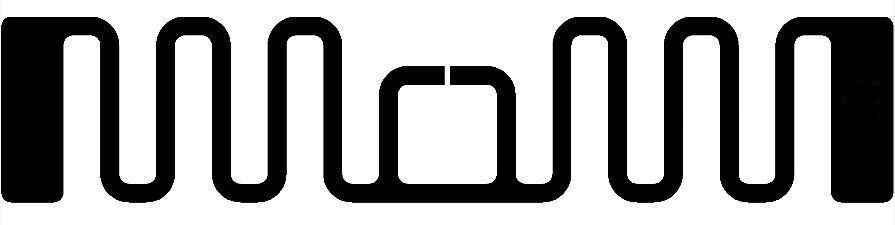
Desired outcome
Our hypothesis was that we could develop an omnidirectional RFID tag that would be readable from a long range (6 meters) and from all orientations relative to the reader.
Functionality
The meander half-dipole antenna design was selected due to its ability to increase the trace length of the antenna without significantly increasing its physical size (95 mm L × 15 mm W).
This design allows for effective tuning of the antenna within a compact package. Additionally, the half-dipole design was intentionally made symmetrical to ensure balanced radiation, thereby minimizing the risk of interference and signal distortion.
Printing and post-processing of the RFID antenna
Printing the antenna
We chose the Copprint LF-301 copper ink because it’s more cost-effective than silver (3–5 times cost savings), and the ink provides excellent conductivity (< 0.003 Ω/square for a 25 μm thickness). It contains a special sintering agent that prevents the nano copper mixture from oxidizing, thereby ensuring long-term conductivity after production. It took NOVA 15 minutes to print the antenna, including the time to create the height map for the paper substrate.
Ink | Copprint LF-301 copper ink |
Substrate | Yardstick paper |
Nozzle type | Nordson EFD 7018395 dispensing tip, 200 µm inner diameter |
Probe pitch | 5 mm |
Cure time and temperature | About 5 minutes at 80°C for drying |
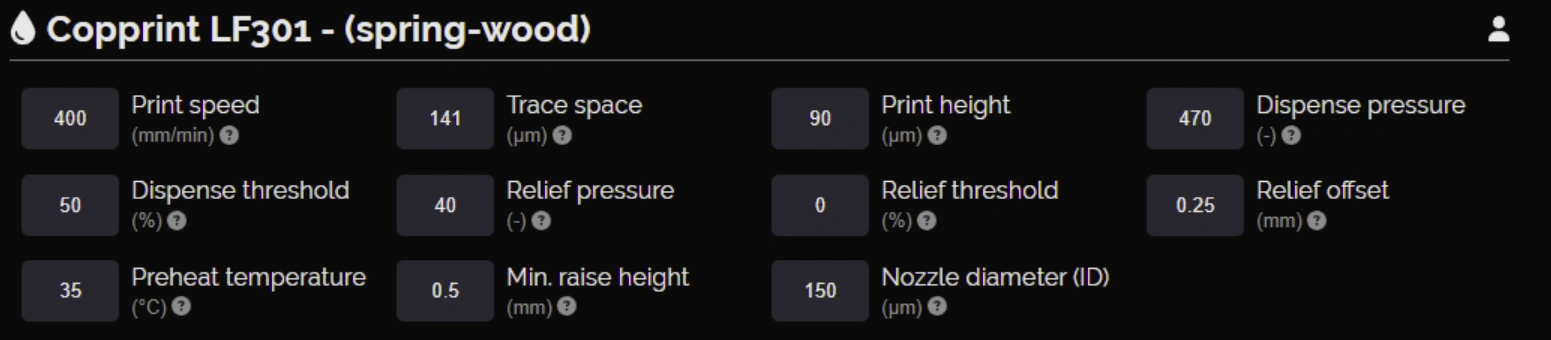
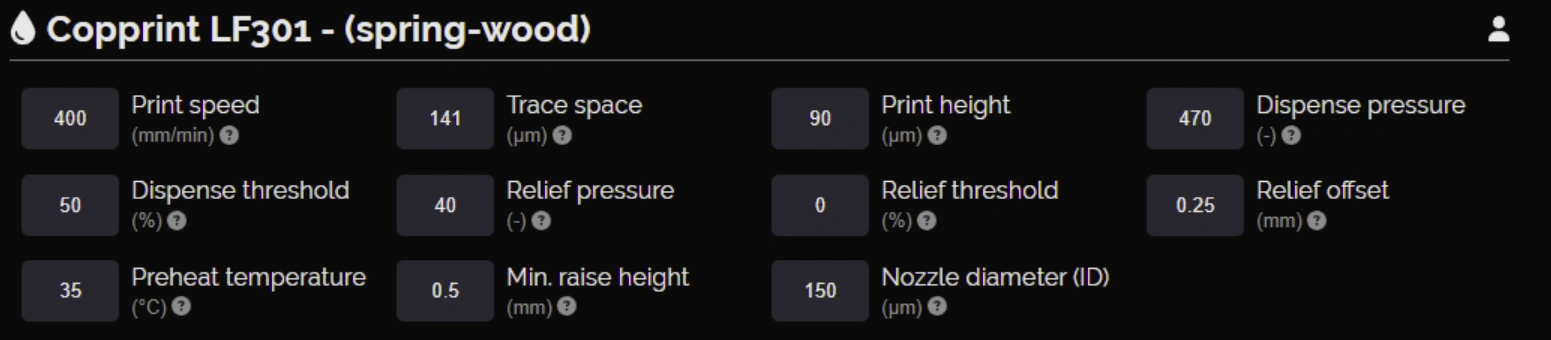
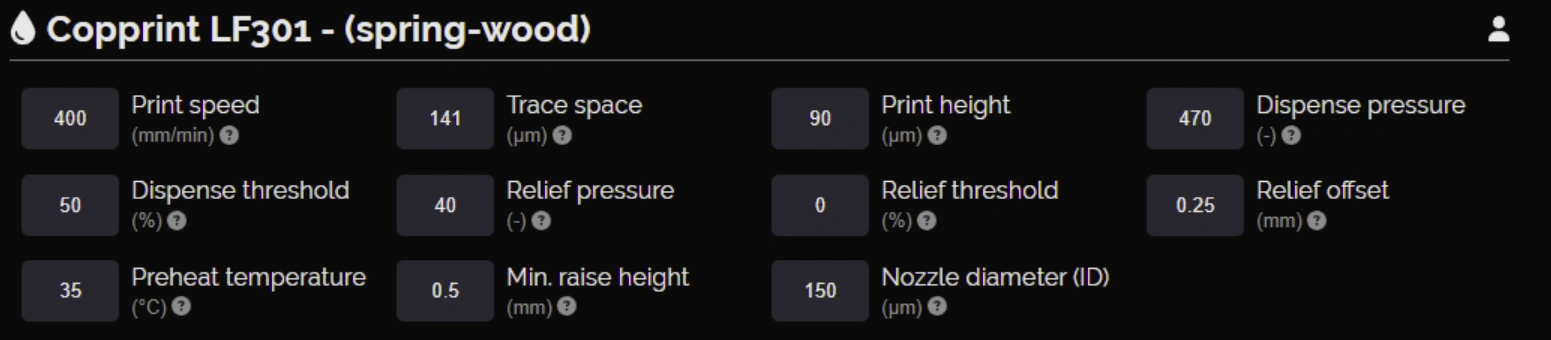
Sintering the copper ink
Once printed, we followed the sintering instructions provided by Copprint. Sintering is a critical process for nano copper inks, as it transitions the particles from a separated state to a cohesive particle matrix. We placed the final print into an oven and left it to dry for 5 minutes at 80°C before using a heat press to sinter it for 15 seconds at 270°C.
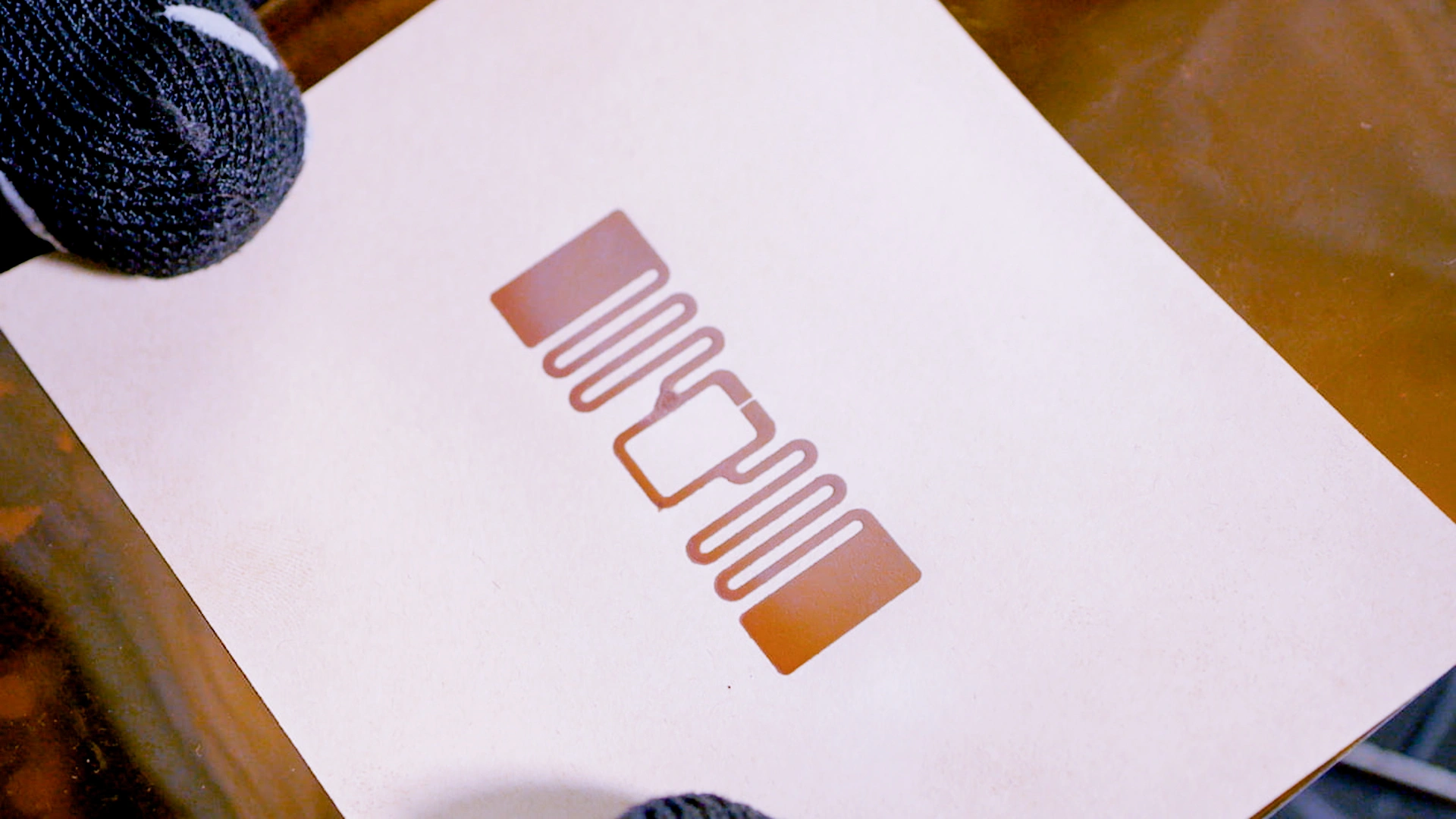
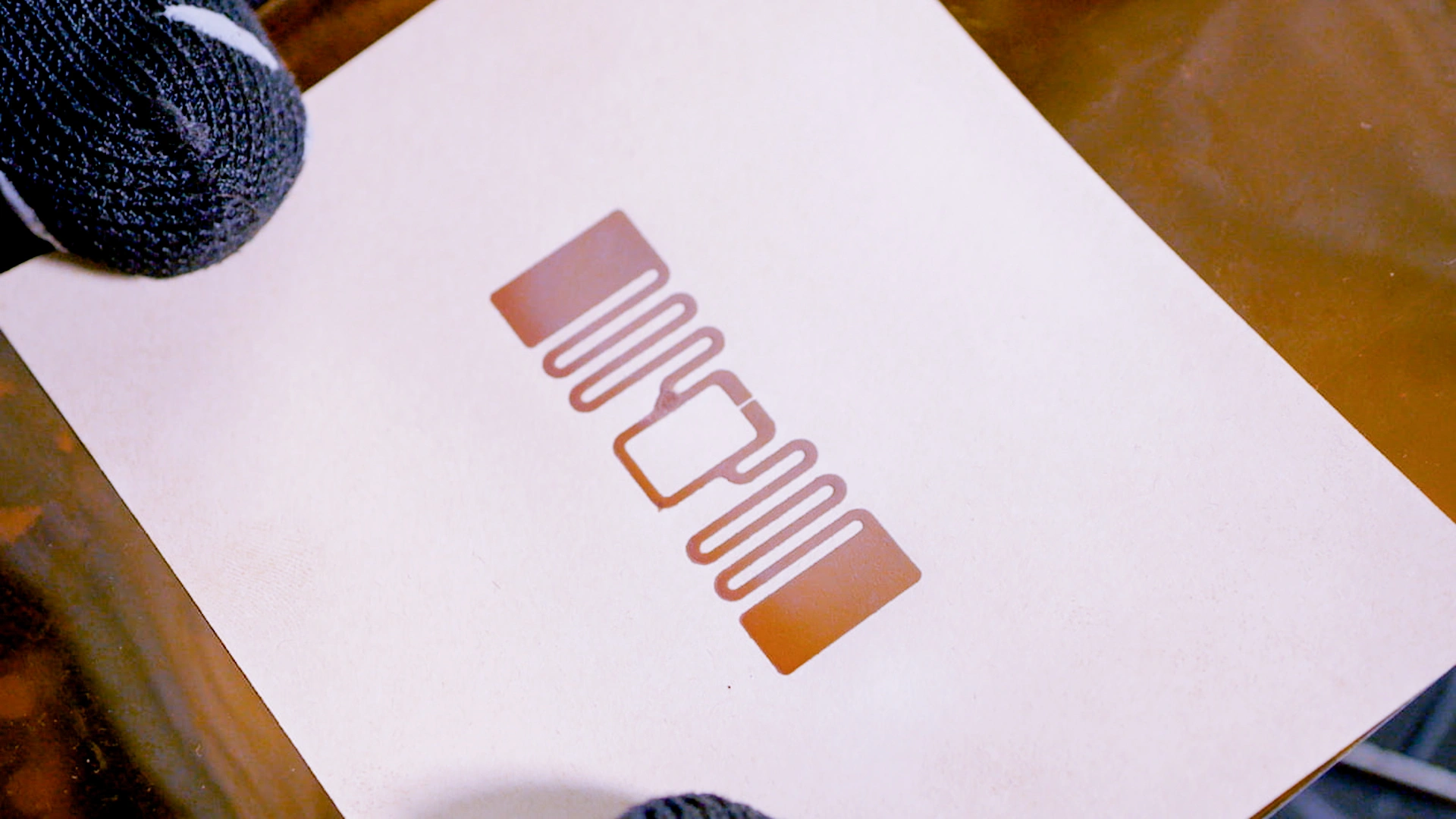
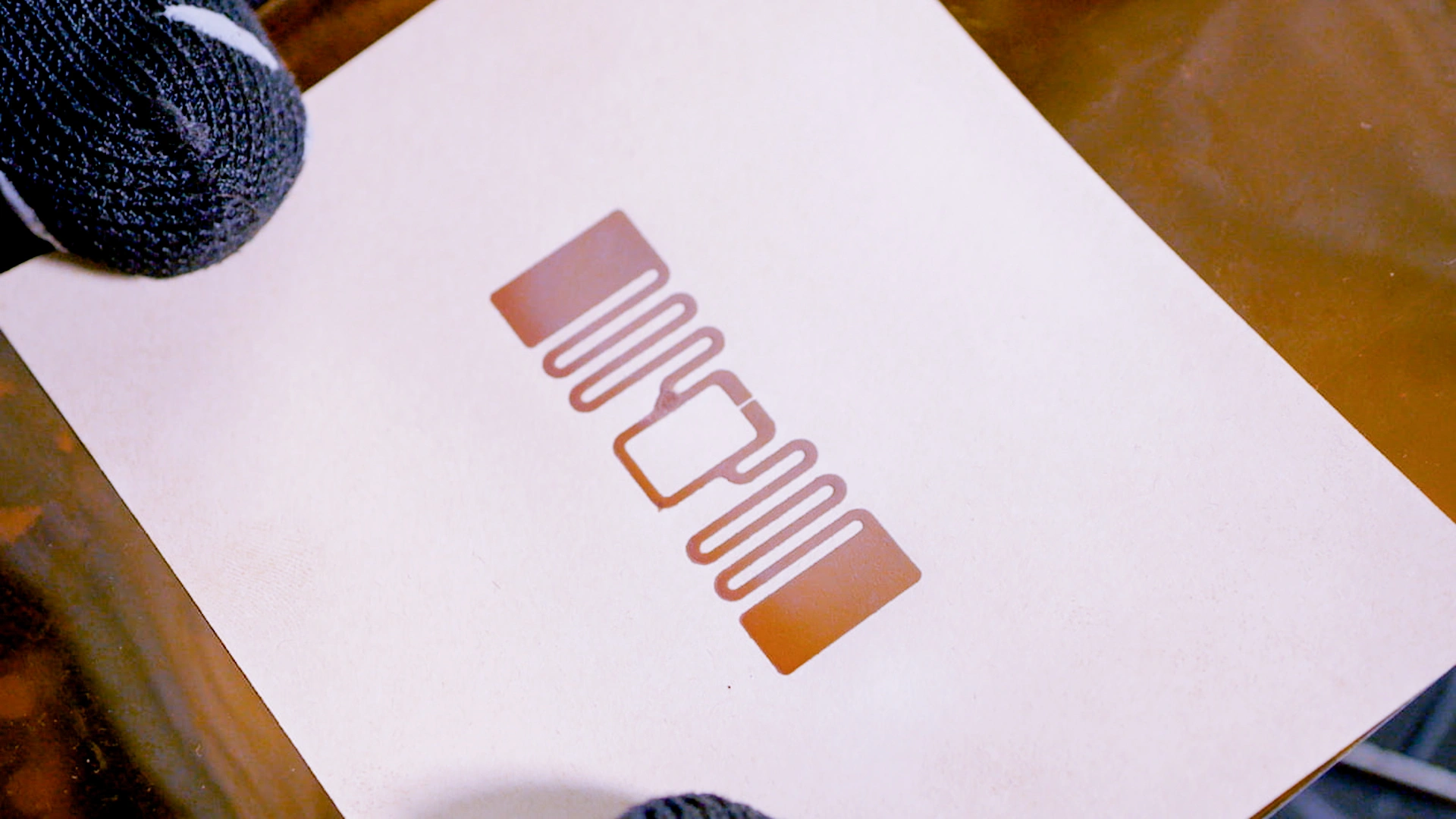
Soldering the transceiver
Due to the high copper content of Copprint LF-301, the resulting sintered antenna exhibited excellent solderability. Consequently, the transceiver was successfully soldered onto the antenna after the sintering process was completed. To ensure a solid solder connection to the transceiver, we used a burnishing pad to burnish the surface of the print before placing the transceiver onto it. We then manually soldered the transceiver to the opening in the center and cured it with an air reflow station.
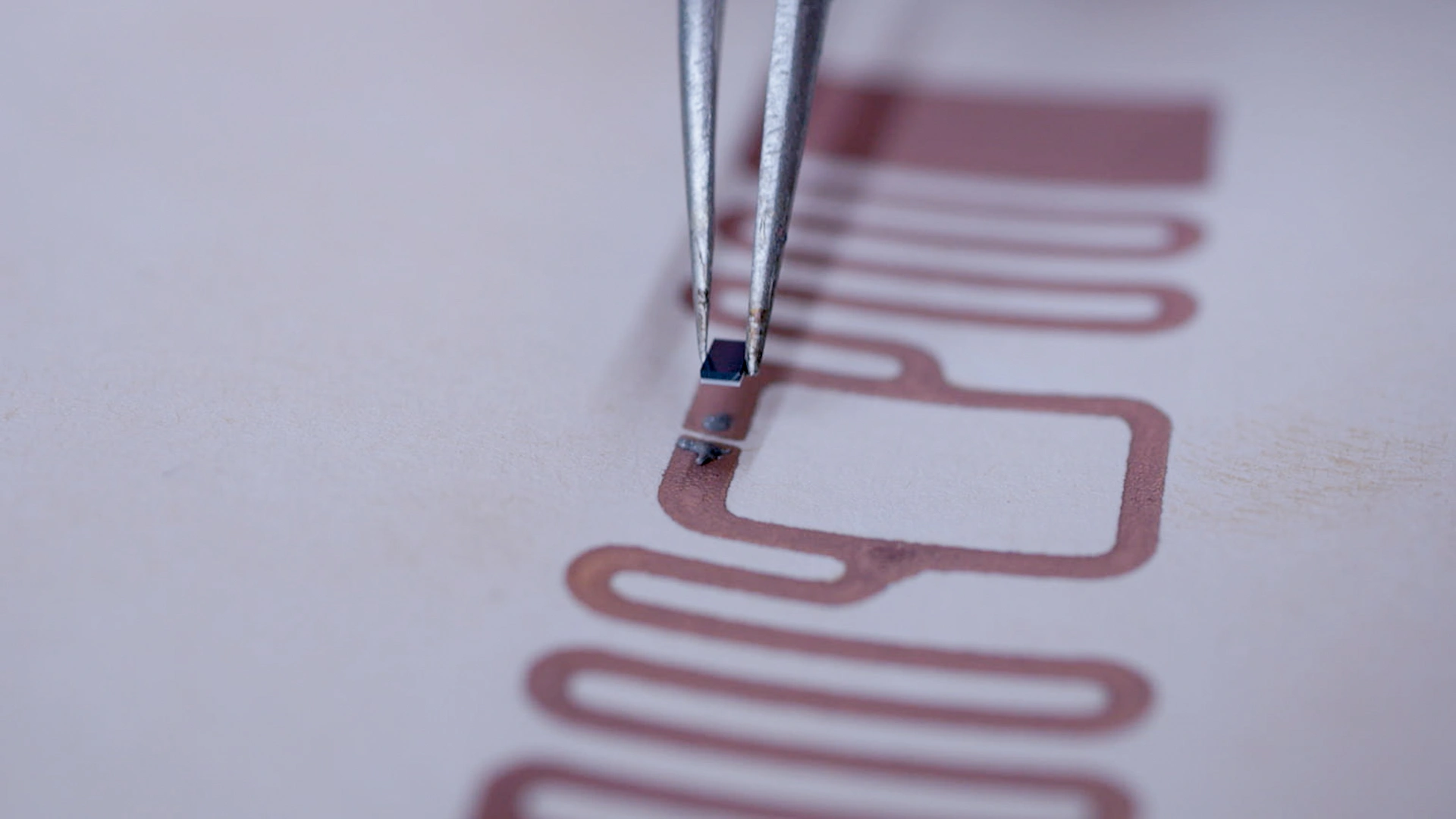
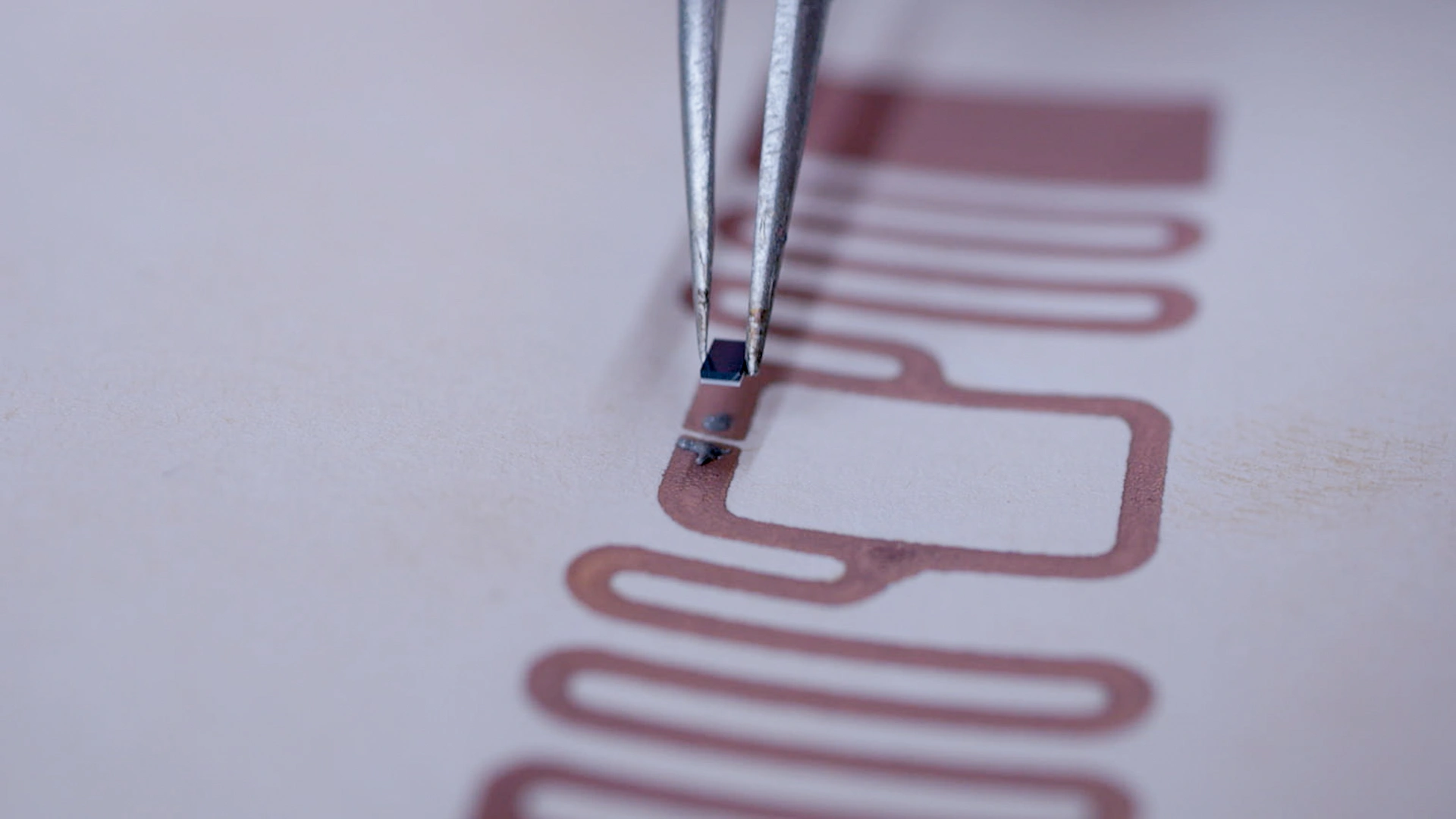
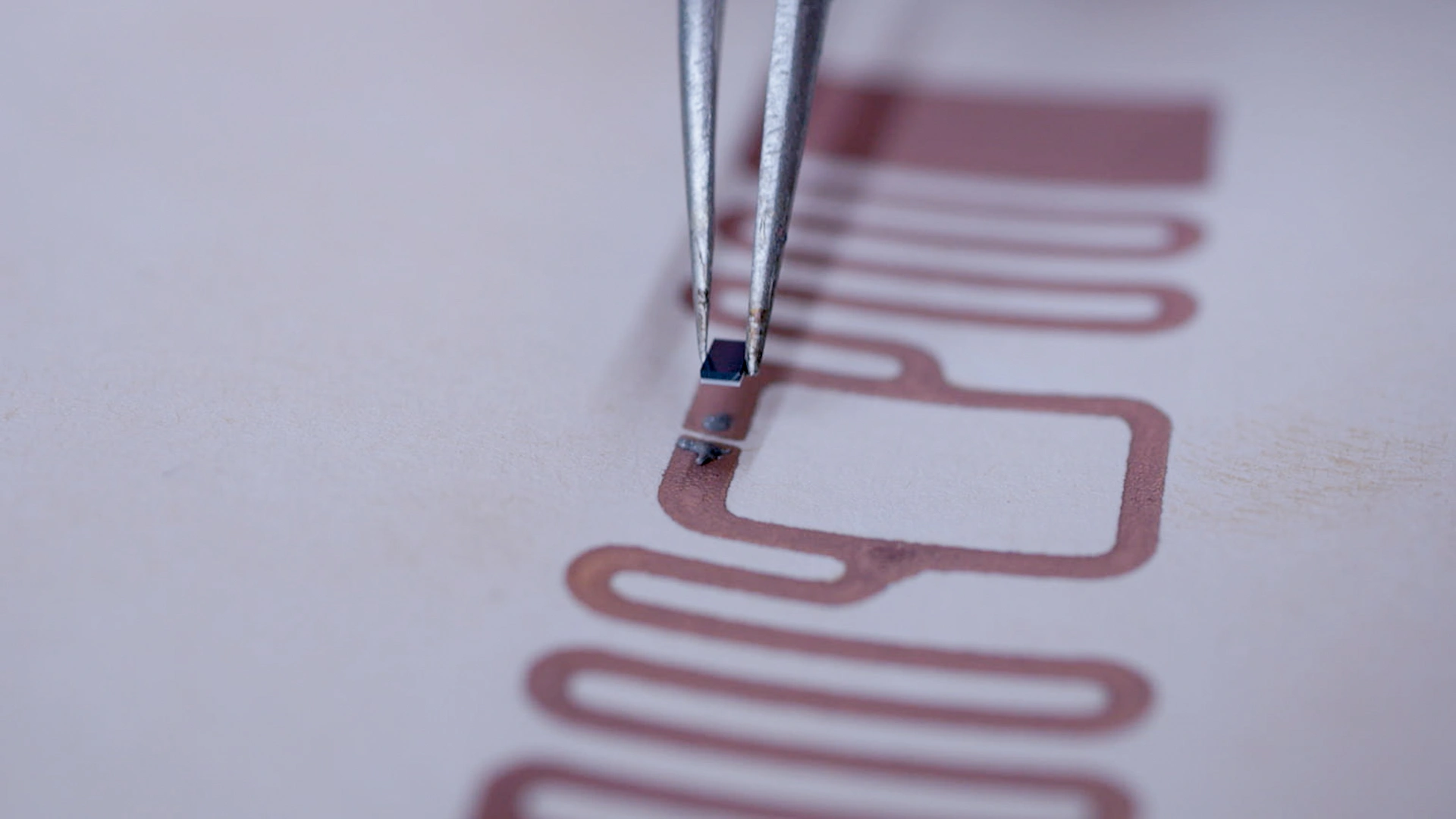
Challenges and advice
Using NOVA to print the RFID tag turned out to be straightforward. We were able to modify designs promptly to achieve optimal performance for the desired frequency range. One minor challenge was characterizing the performance of the RFID tag. Given its compact size, even slight alterations in geometry had a significant impact on the results.
To minimize rework, we used the MATLAB® Antenna Toolbox™ to simulate the design performance, including sensitivity and directionality. We then refined the antenna's dimensions and geometry based on simulation outcomes. This allowed us to achieve the optimum design within only three iterations.



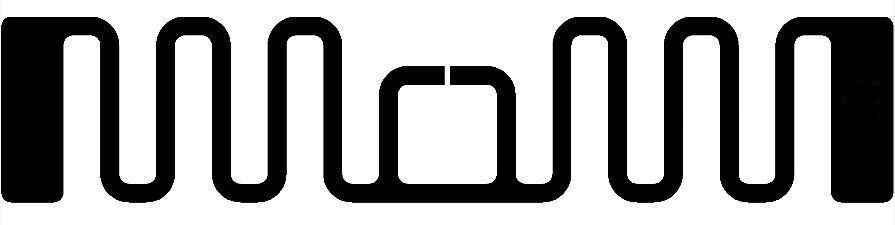
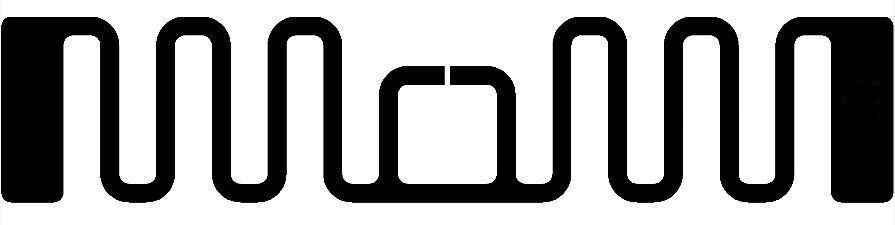
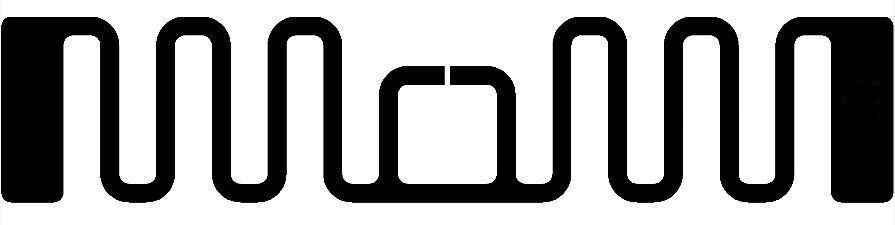
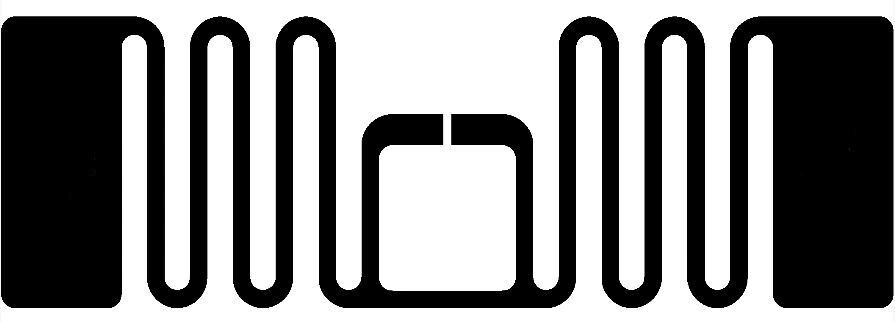
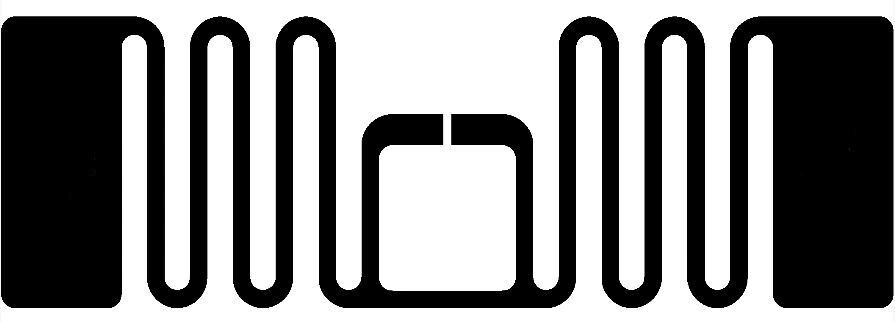
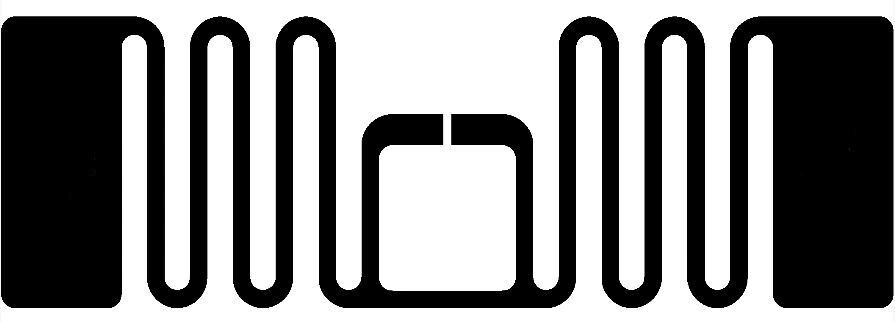
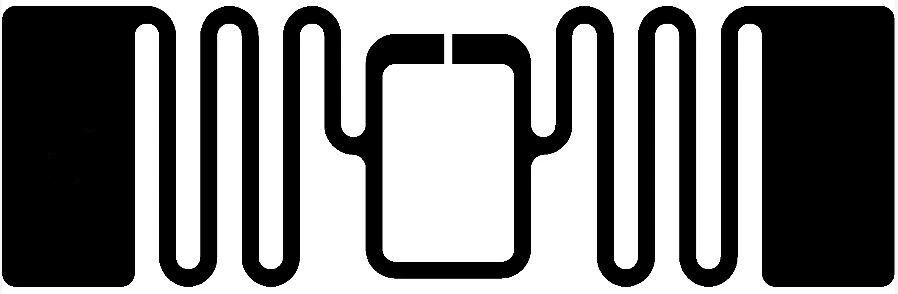
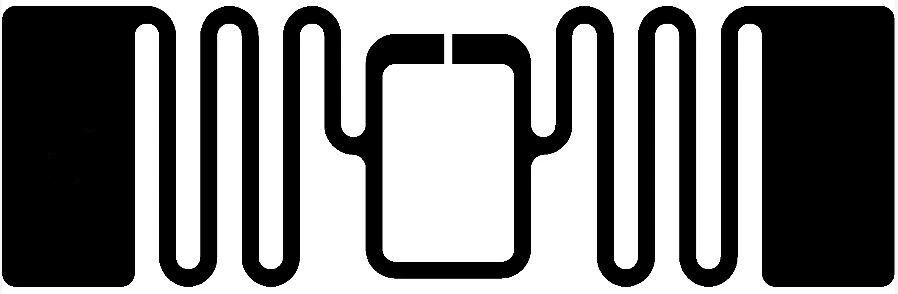
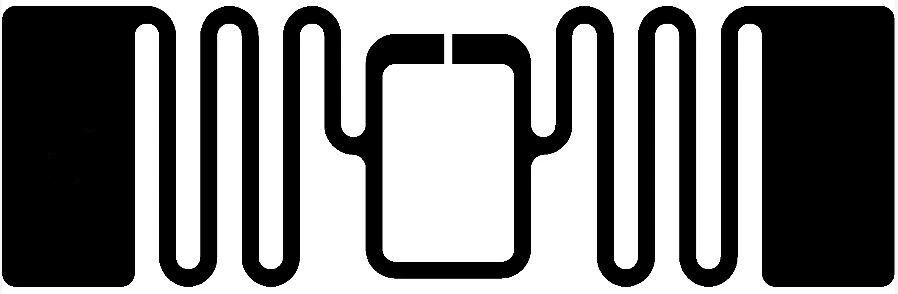
Conclusion
The final RFID tag exhibited a minimum self-reflection coefficient (S11) of -29.42 dB at 922.50 MHz, surpassing the required maximum of -10 dB. This value represents the resonant frequency where the tag will function best — well within the 902 MHz to 928 MHz frequency bandwidth for North American RFID tags. Its performance exceeded that of off-the-shelf RFID tags from market leaders.
The tag is well-suited for applications requiring reliable, long-range, and orientation-independent reading capabilities, such as tracking the inventory of electronics, furniture, luggage, and vehicles. In addition, while the commercial tags we acquired were made of non-recyclable laminate, our design was composed of paper and copper ink, making the RFID tag compostable. This highlights an emerging use case for copper inks in RFID or NFC applications.
As we continue to explore the possibilities of printing antennas, we invite you to view the other projects we’ve completed.
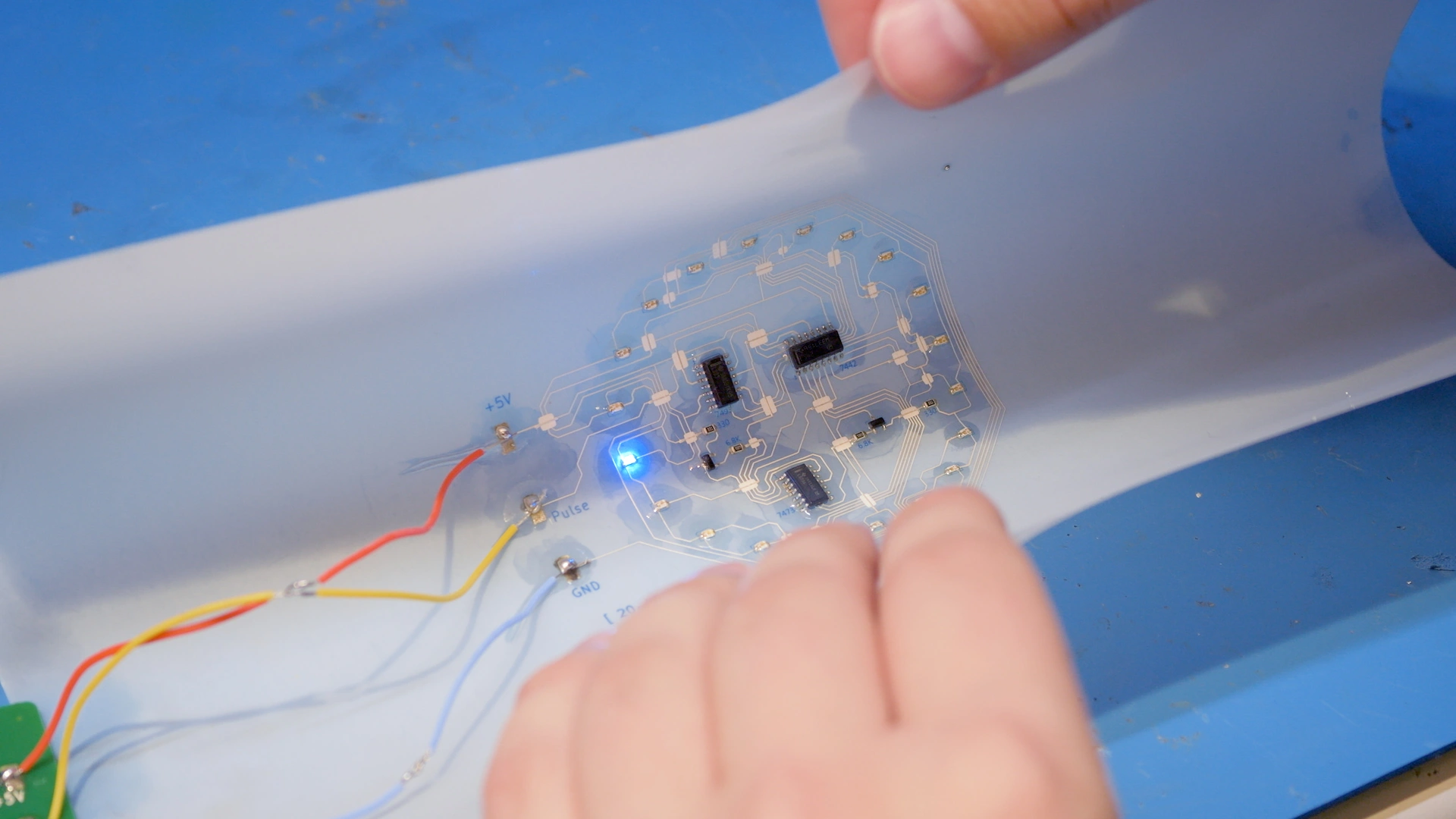
Printing multilayer flexible, stretchable, and conformable electronics?
NOVA’s Plan feature makes it easy.
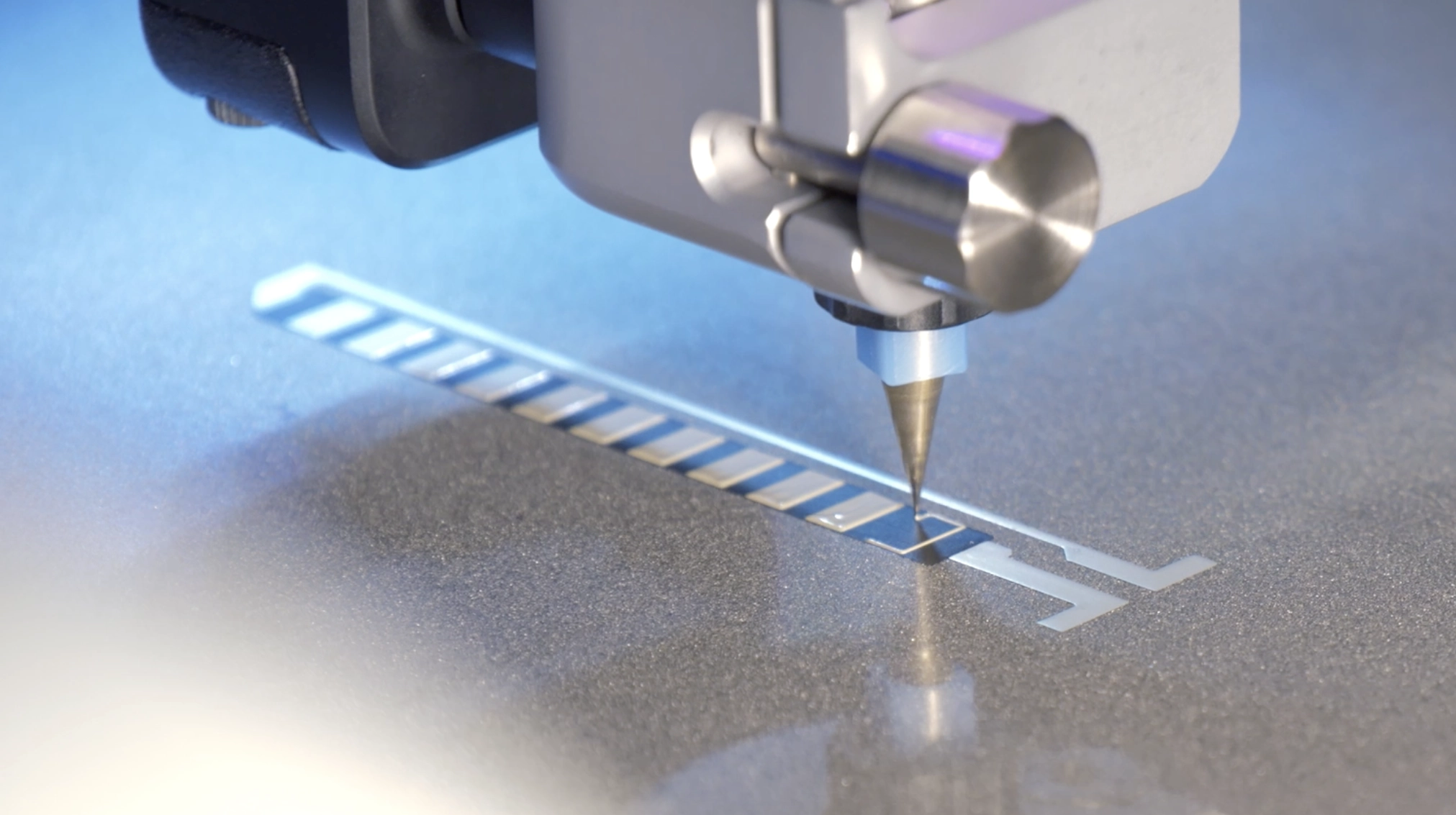