Bioelectronics
Bring your bioelectronics printing in-house
Bioelectronics is a multidisciplinary field that combines biology, computer engineering, materials science, chemistry, and electrical engineering to develop devices that monitor or control biological processes. It integrates electronic components like sensors and circuits with biological systems like cells, tissues, and organs.
Common bioelectronic applications include biomedical sensors, energy storage and harvesting devices, implantables, and soft robotics [1]. These innovative devices support treatment, drug delivery, glucose monitoring, and neuroprosthetics for restoring lost functions.
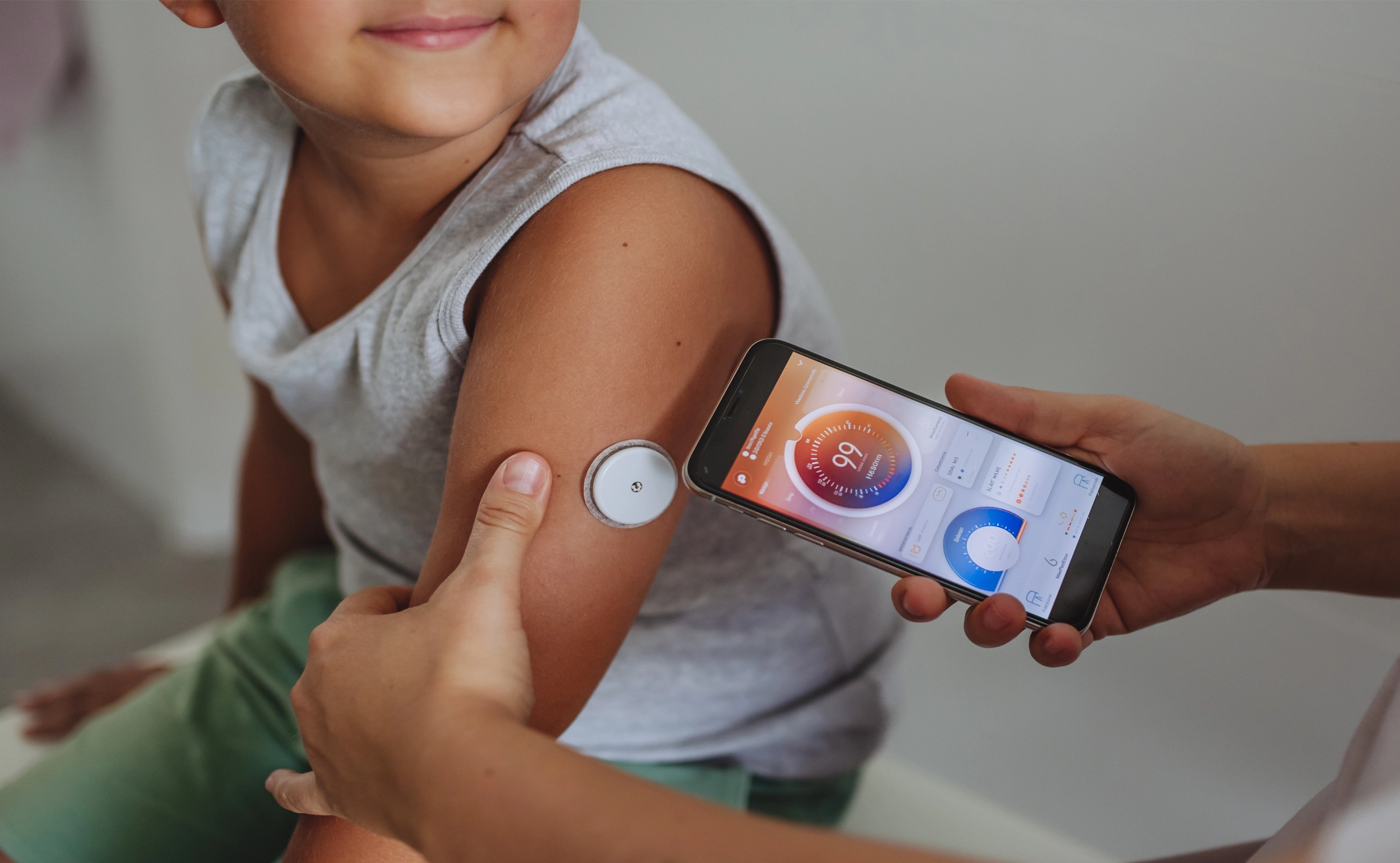
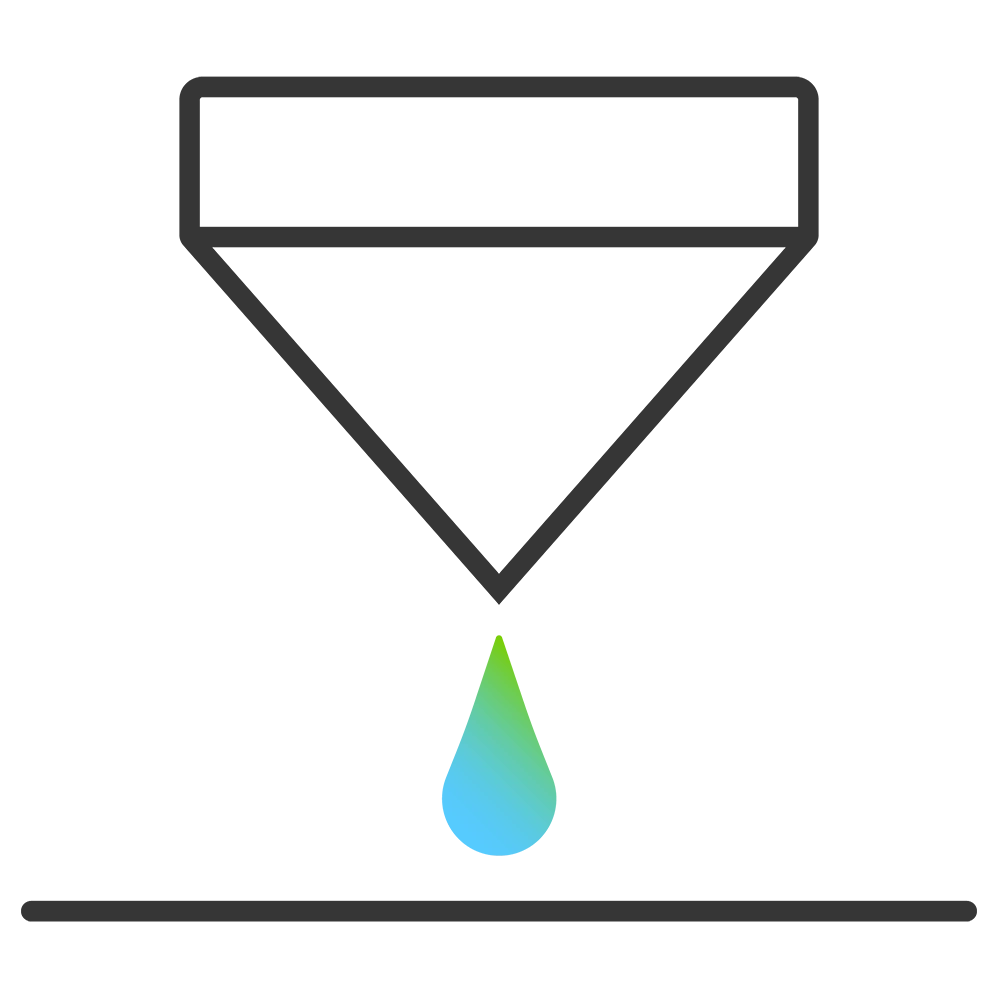
- Medical
- Prosthetics
- Pharmaceutical
- Consumer electronics
- Silver-based inks
- Copper-based inks
- Carbon-based inks
- Gold-based inks
- Polymer-based dielectric inks
- Ceramic-based dielectric inks
- Polydimethylsiloxane (PDMS)
- Polycarbonate (PC)
- Polyethylene terephthalate (PET)
- Hydrogels
- Silicon
- Fabric
Our white papers
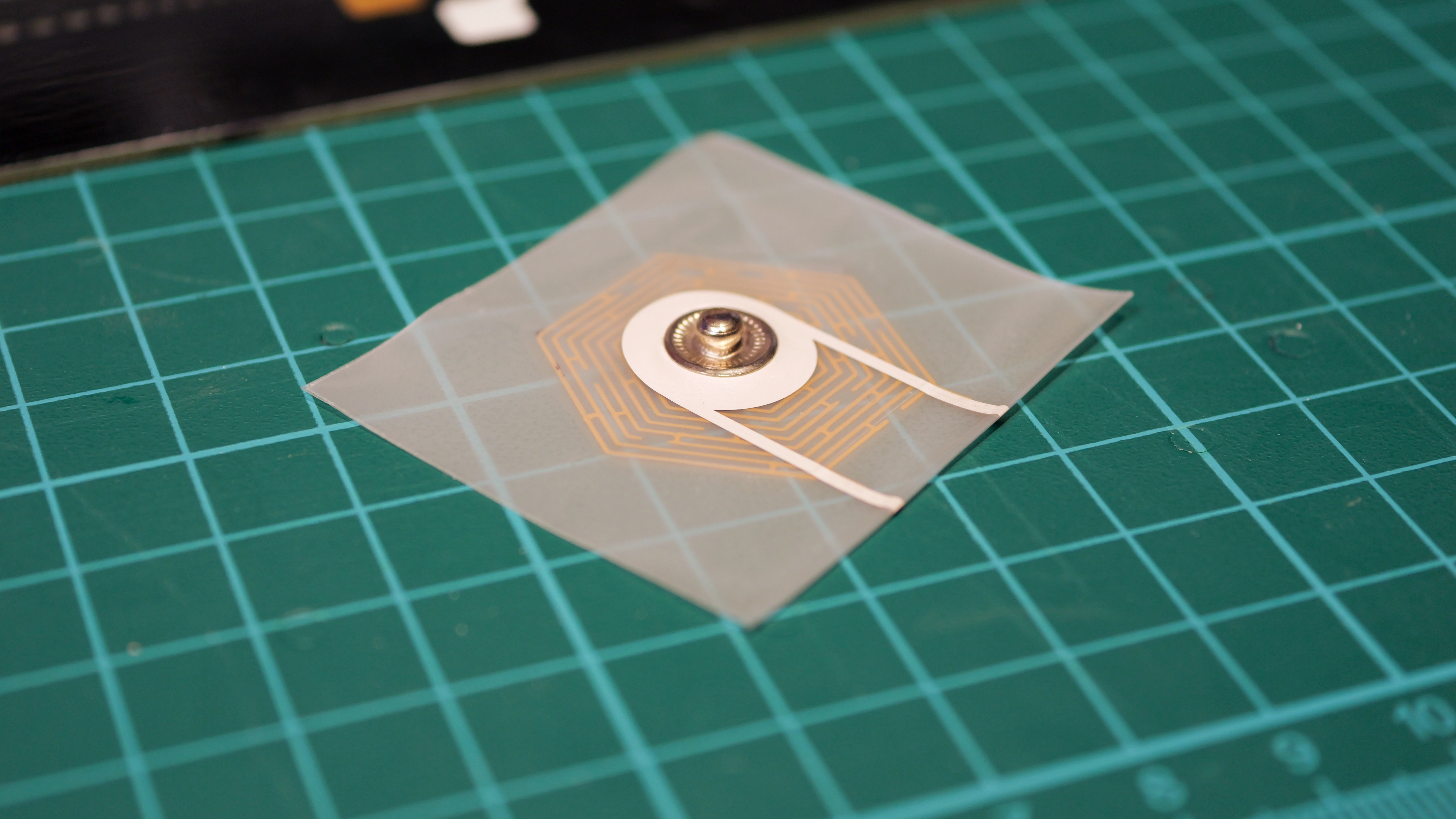
Printing ECG Electrodes with Biocompatible Gold Ink on TPU
This project demonstrates how we validated the effectiveness of printing ECG electrodes on TPU using biocompatible gold ink and stretchable silver ink.
Additional resources
Frequently asked questions
What types of devices are considered bioelectronics?
Can I use Voltera’s printers to prototype bioelectronic devices?
What does “bioelectronics” actually mean in this context?