A Compatibility Guide for Inks and Substrates
If you’re new to the world of additive electronics or flexible hybrid electronics, you probably have a lot of questions when it comes to materials compatibility.
When you’re printing with materials, you typically begin with one of two questions:
- I have this thing and I want to print on it — what ink can I use?
- I have this ink — what can it print on?
For some categories of inks, there are a lot of variables that determine what you can print on — especially if you’re printing onto soft, stretchable, or flexible substrates. Thermoplastic Polyurethane (TPU), for example, is a stretchable material that can be used to incorporate electronics into textiles — but there are many kinds of TPU and they need to be paired with compatible ink.
When you’re innovating in the field of flexible hybrid electronics, trying to figure out how to choose materials for your next project can feel a bit like the wild west. If you want to make informed decisions, you need to understand the factors that influence materials compatibility — ink composition, functional compatibility, curing method, and surface energy.
Conductive ink composition
Conductive inks are typically composed of three main parts:
- Filler — this gives the ink its function — making it conductive, resistive, etc.
- Binder — this gives the ink its structural property after it cures, usually a polymer, to hold the filler particles in place.
- Vehicle — this is a liquid phase that carries everything else to its destination. It can be composed of many different materials like solvents, curing initiators, and other substances that give the ink its particular rheology and flow.
Different kinds of inks have different ratios of filler, binder, and vehicle. These formulations and ratios determine the conductivity of the ink, whether it is rigid, flexible, or stretchable, informs processing conditions and storage conditions, and more. Fortunately, you don’t have to be a materials science expert to figure this stuff out. Datasheets provide details about an ink’s physical properties, composition, processing details, substrate compatibility, etc.
Here are some examples of conductive ink datasheets from Novacentrix, ACI Materials, and Dupont.
Screen printable inks can have up to 80% filler by weight — they’re thick, high-viscosity inks. These inks are also compatible with NOVA and the V-One’s direct ink writing technology.
Inkjet inks have less than 20% filler, with a higher proportion of vehicle and binder — they’re watery, low-viscosity inks.
Sci-Snack:
What is viscosity? Viscosity is the measure of a fluid’s resistance to flow, due to the internal friction of the fluid. The viscosity of an ink impacts how it interacts with a substrate and how it interacts with your printing technology, and is a key determining factor when you’re choosing printing technology.
Conductive inks’ functional compatibility
Conductive ink has two primary jobs — to stay where it’s put and to conduct electricity.
Your ink may have other functions too, like stretching or flexing. If you want your ink to do its jobs properly, there are three general considerations for pairing an ink with a substrate.
How to match an ink with a substrate
If you’re looking for specific functional performance, like flexibility or stretchability, you need to print on a stretchable or flexible substrate using an ink that has flexible or stretchable properties.
Here are some rules of thumb for functionally matching an ink and a substrate:
- Rigid ink doesn’t work on flexible or stretchable substrates, because the ink doesn’t have flexible or stretchable properties.
- Flexible ink doesn’t work on stretchable substrates, because the ink is formulated to flex, but not formulated to stretch.
- Stretchable, flexible, or rigid ink can all be used on a rigid substrate.
Functionally speaking, will it work?* | Rigid ink | Flexible ink | Stretchable ink |
---|---|---|---|
Rigid substrate | Yes | Yes | Yes |
Flexible substrate | No | Yes | Yes |
Stretchable substrate | No | No | Yes |
*Other properties will impact ink/substrate compatibility, beyond what is depicted in this chart. Read on for more details.
Note: If you’re printing on TPU, you must use an ink that is formulated to match the stretchability of the TPU. If you print onto TPU with an incompatible ink, your traces will crack apart when strain is applied. Also note that TPU can swell due to solvents in certain inks. When you’re choosing a stretchable conductive ink, ask the ink supplier to recommend a compatible TPU.
How does curing temperature affect my substrate?
Some inks just don’t work with some substrates because the temperature required to cure the ink will destroy the substrate.
Most conductive inks are thermally cured. They need to be raised up to a certain temperature in order to evaporate the solvents in the ink and bind the remaining contents together into cured traces. Some substrates can’t withstand high temperatures. Kapton can be heated to 300°C and be perfectly fine, but TPU, polyethylene terephthalate (PET), or FR4 would melt and burn at such a high temperature.
How to ensure the ink adheres to the substrate
Adhesion is a surface property — the way that two surfaces interact. In order for your ink to do its job, it has to adhere to the substrate.
If you print with conductive ink onto super smooth non-stick Teflon, the ink won’t adhere and your cured traces will just pop off the surface. In order to promote adhesion, it’s best if your substrate has micro-scale roughness incorporated into the surface itself, or via a coating. For example, PET can be coated with silica flakes to promote adhesion.
Curing methods
There are two methods to cure ink — thermal heat energy or ultraviolet light energy. Curing converts an ink from its wet, non-functional state to its solid, functional state. The thermal curing process changes the volume of your traces, whereas UV curing does not. It’s important to understand how each process impacts your traces, because ink needs to maintain a particular shape after curing in order to effectively conduct electricity.
Thermal curing
Thermal curing is the most common way of processing an ink. Thermal inks are cured by applying heat to evaporate the solvents in a vehicle, and the remaining binder polymers hold the filler particles in place.
Thermal curing evaporates the solvents in the ink, reducing the volume of the material. You should account for this if you have a specific thickness target after curing.
UV curing
Ultraviolet (UV) inks have a different vehicle makeup than thermal inks. Their uncured phase contains monomers. When exposed to UV light, photoinitiators cause the monomers to bind together, converting them into polymers that hold everything together.
UV-cured inks retain their full volume — nothing evaporates — so the volume of your ink and the shape of your traces remains the same through the curing process.
Surface energy
If you’re using high-viscosity screen-printable inks, then surface energy isn’t a particularly important factor. The friction between the molecules in high-viscosity ink negates the forces of surface energy.
If you’re using inkjet technology, the surface energy of your ink and the surface energy of your substrate — and how those two energies interact — will dictate if your ink spreads out on the substrate, forms nice contained traces, or beads up like water on a non-stick frying pan. You can learn more about surface energy here.
Surface energy, by definition, is the amount of energy required to increase the surface area of a material. In other words, it’s the energy required to increase the space between the molecules. Each material has its own surface energy based on the chemical composition of the material.
If you have specific questions about how to pair an ink with a substrate, reach out and talk to one of our experts. We love to nerd out on this stuff and want to help you get the answers you need to make your next project a success.
Until next time…
The Voltera Team
P.S. Was this blog post helpful? Is there a different topic you’d like to learn more about? Let us know! We love answering questions, sharing knowledge, and helping to make the printed electronics industry more accessible to everyone.
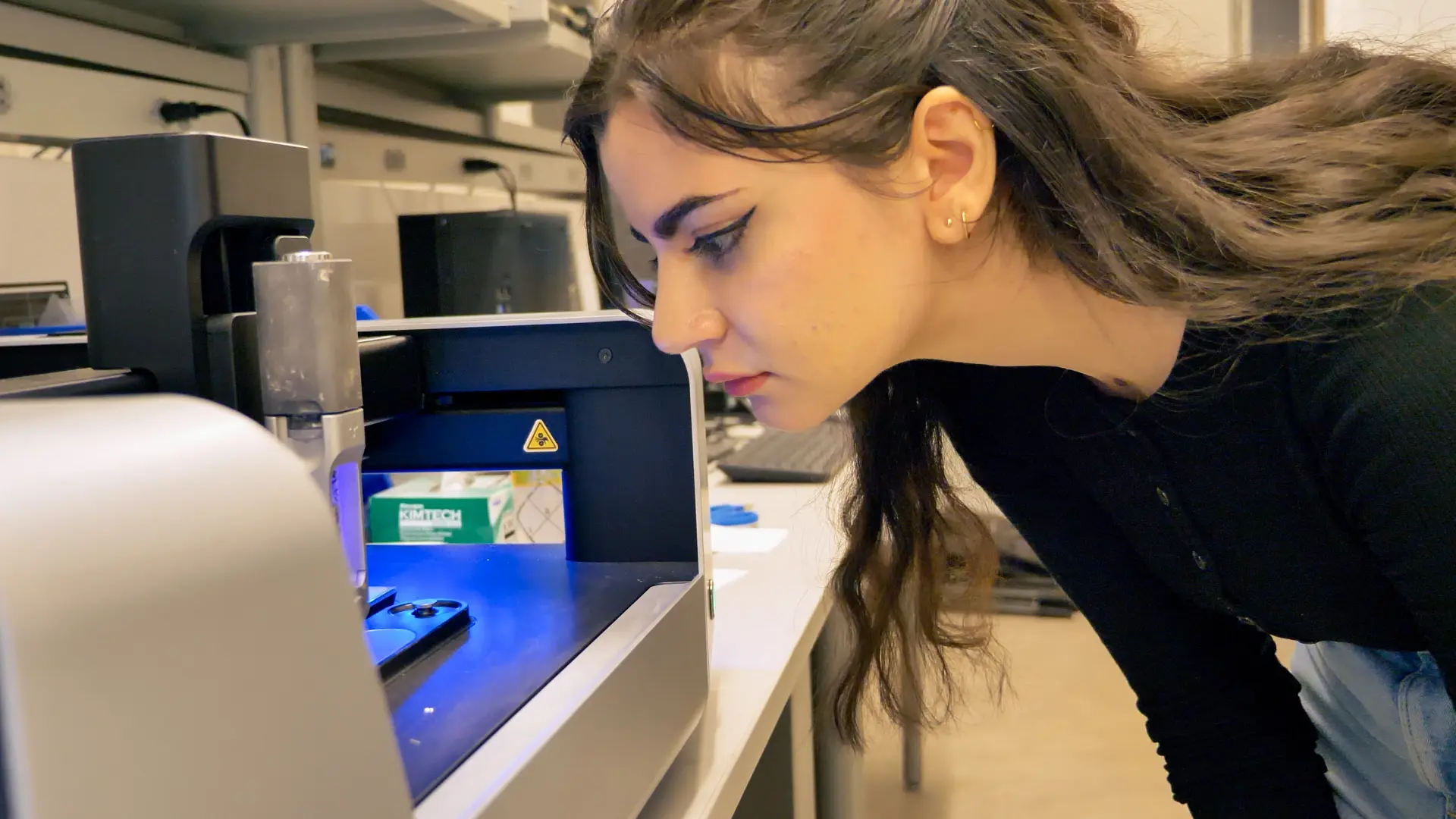
Check out our Customer Stories
Take a closer look at what our customers are doing in the industry.
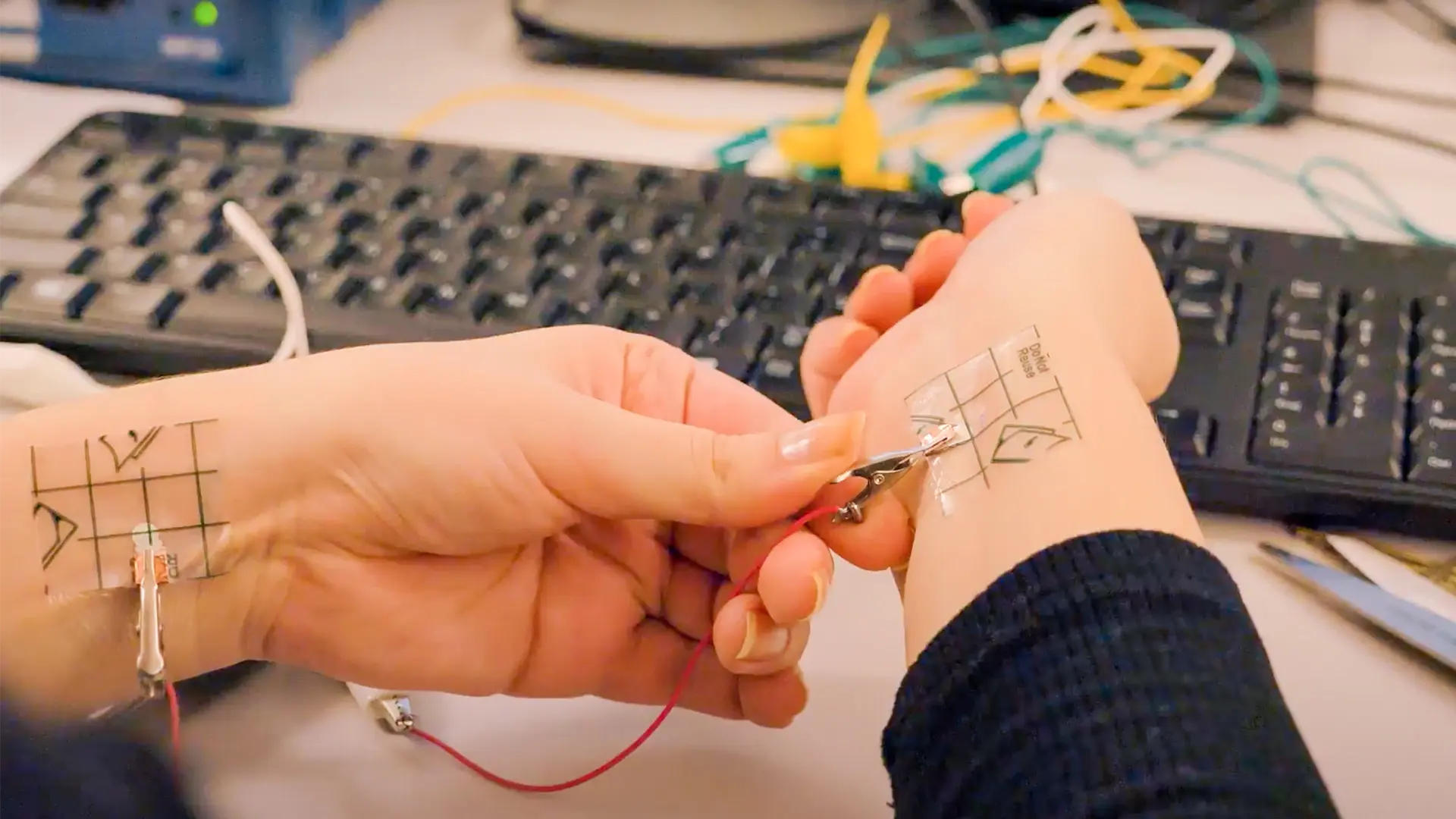