What are Conductive Inks?
Flexible Hybrid Electronics (FHE) offer a whole new dimension of possibility in electronics and hardware design. Trying to keep up with the ever-shrinking requirements of consumer electronics? Looking to cut every milligram of fuel-wasting weight in automotive and aerospace? Chasing the next big opportunity in wearable sensors, structural electronics, or soft robotics? The design options printed electronics offer go far beyond what can be achieved with the rigid PCBs of the past.
But what does it take to get from an idea in your head to a product in your hand? What tools do you need to add to your engineering toolbox? How can you prototype electronics with exotic substrates? What's possible with FHE?
At Voltera, we’re always interested in exploring what it takes to go from board-in-a-box electronics to additively printed and produced-at-scale FHE devices – and offer some helpful, practical insights along the way. In this blog, we walk you through one of the key components of any printed electronic device: conductive ink.
What is conductive ink?
A conductive ink is a material which is printed, processed, and conducts electricity. More specifically, conductive inks are:
- Printed: Different inks exist for different printing technologies, which have their own pros and cons. Printing inks means additively patterning your surface in some way.
- Processed: Most inks aren’t actually conductive until they’re processed, which usually means applying heat. In this blog, we’re only going to be talking about low-temperature inks (< 250 °C).
- Electrically conductive: Conductive inks are actually a subset of functional inks – meaning inks that are useful outside of purely aesthetic or structural needs. Conductive inks are by far the largest branch — their job is to provide a path for electrons to get from A to B.
What are conductive inks made of?
Conductive inks have two major parts:
- Filler: This is the conductive part – typically metal particles – which give your ink its electrical properties.
- Vehicle: This is everything else – the binders, dispersants, solvents, and additives – that suspend your particles, allow the ink to flow and dry, give it structural stability and flexibility, and all the other properties your ink needs to perform at its best..
Filler Material
Filler material typically comes down to two options – silver and everything else. When it comes to choosing a filler, silver often wins out for the factors most people care about:
- Conductivity vs. cost
- Accessibility
- Ease of use/stability
Silver
Silver typically gives you the best bang for your buck in terms of conductivity, but just as important as the performance is the fact that silver inks are ubiquitous. Silver grandfathered into the industry, and since most major ink suppliers offer silver-based inks, you have far more options for chemistries and configurations to suit your specific needs.As for ease of use, it’s best to illustrate by comparing with silver’s closest competitor: copper.
Copper
Copper deserves a mention because it’s usually the first alternative people consider – typically because copper is technically a cheaper metal than silver, on paper. Additionally, if you come from traditional electronics, copper is everywhere.
The thing is, inks are NOT bulk metal. Just like a computer’s cost is more than the sum of its parts, an ink’s overall cost includes processing cost for raw materials, R&D cost, and any capital cost you might incur to use it.
The biggest detractor for copper is oxidation. Copper inks will oxidize when curing in air, which stops your copper particles from conducting. To prevent oxidation, you’d need to pump in a reducing agent, such as nitrogen gas, adding cost and complexity which usually outweighs the raw material cost.
There are some workarounds, such as coating copper particles in silver, for example, but the additional processing cost for these options, and their relative scarcity, means that silver still usually comes out on top in the conductivity/cost balance.
With that being said, there are some contenders who are working on ambient-curing copper inks, and for good reason. In concept, if processing cost was comparable, copper promises more robust solderability than silver, which can be attractive for compatibility with standard surface mount technology (SMT) processes.
Carbon inks, conductive polymer, and molecular inks
There are many other varieties of conductive ink fillers – carbon nanotubes, graphene, conductive polymer, or particle-free molecular inks – and each have their own particular pros and cons. If you’re going down one of those routes, you probably have a really good reason to do so, such as conducting research or publishing a paper.
Particle sizing, shape, and loading (weight %) are major decisions when formulating an ink, and provide tradeoffs in terms of conductivity, processing temperature, cost, and flow properties.
That said, unless you’re getting into the nitty-gritty and elbows deep into formulation, it’s one of those things that is best left up to the manufacturer.
Here are some general best practices to keep in mind:
- Metal loading: Higher metal content generally means more conductive and higher viscosity. For example, low-viscosity, water-like inkjet inks will usually top out in the 10%-20% range, while thick screen printing pastes can get up to around 80% silver by weight.
- Particle size and shape: In general, the smaller the particles, the higher the conductivity and the higher the cost. For convenience, we’ve grouped size ranges in a few rule-of-thumb categories:
- Micrometer-sized (1-5 μm): Most common, cheapest, lowest conductivity due to contact resistance.
- Sub-micrometer-sized (~0.3-1 μm)
- Nano-sized (<0.3 nm)
When speaking about shape, you’re typically safe to assume that you’re working with flakes – but not always. Check out the scanning electron micrograph below, courtesy Alejandro Marangoni at the University of Guelph.
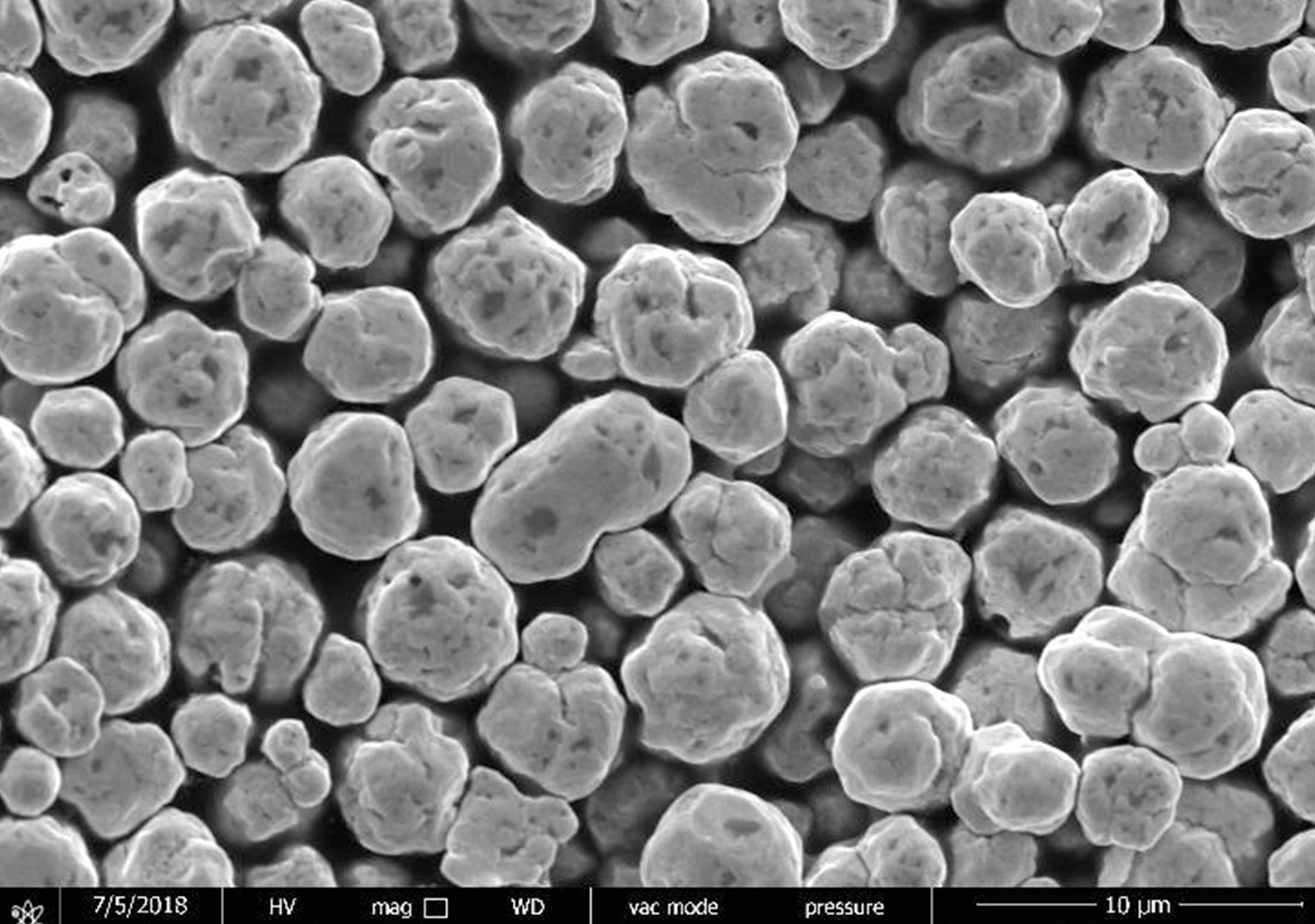
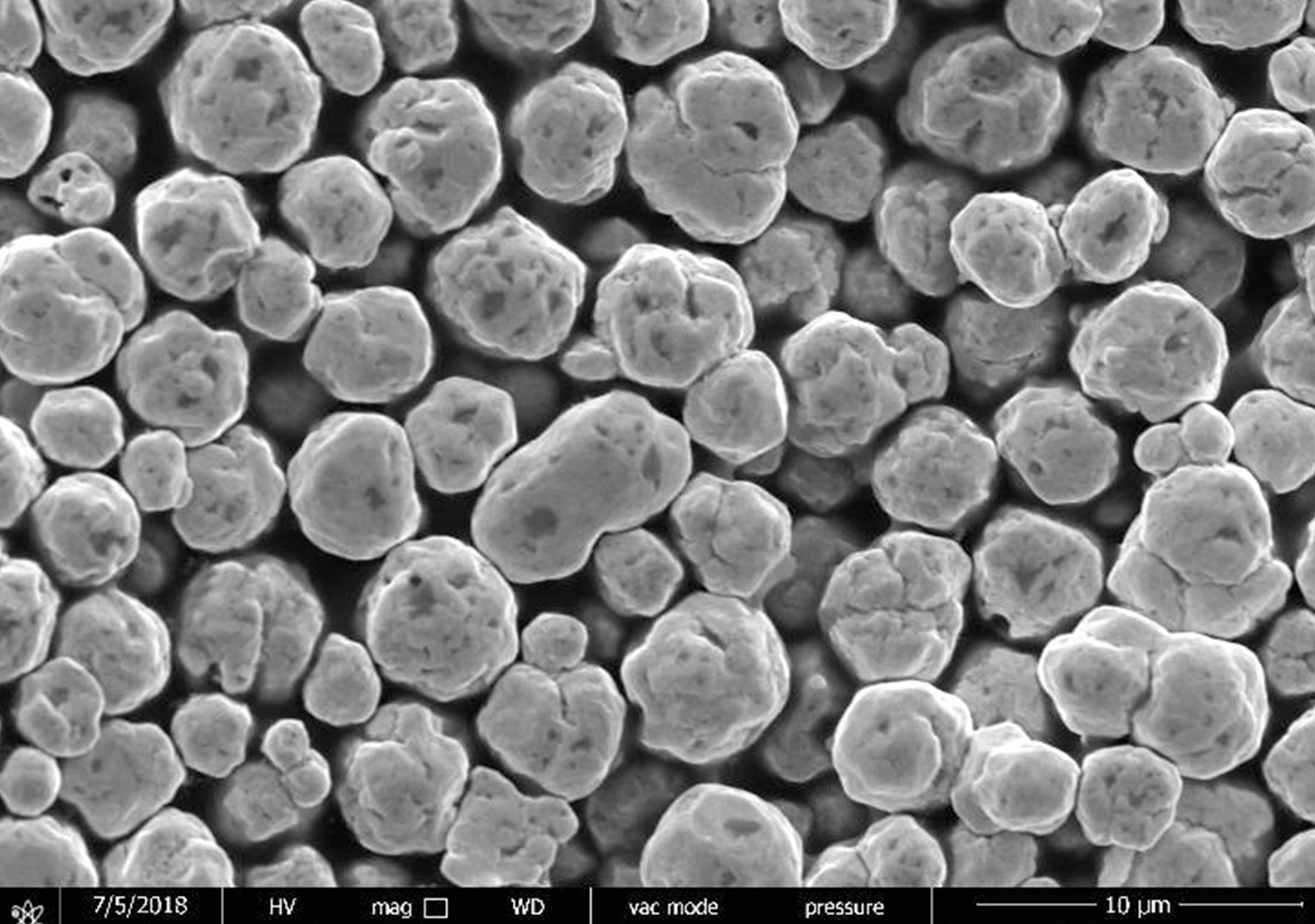
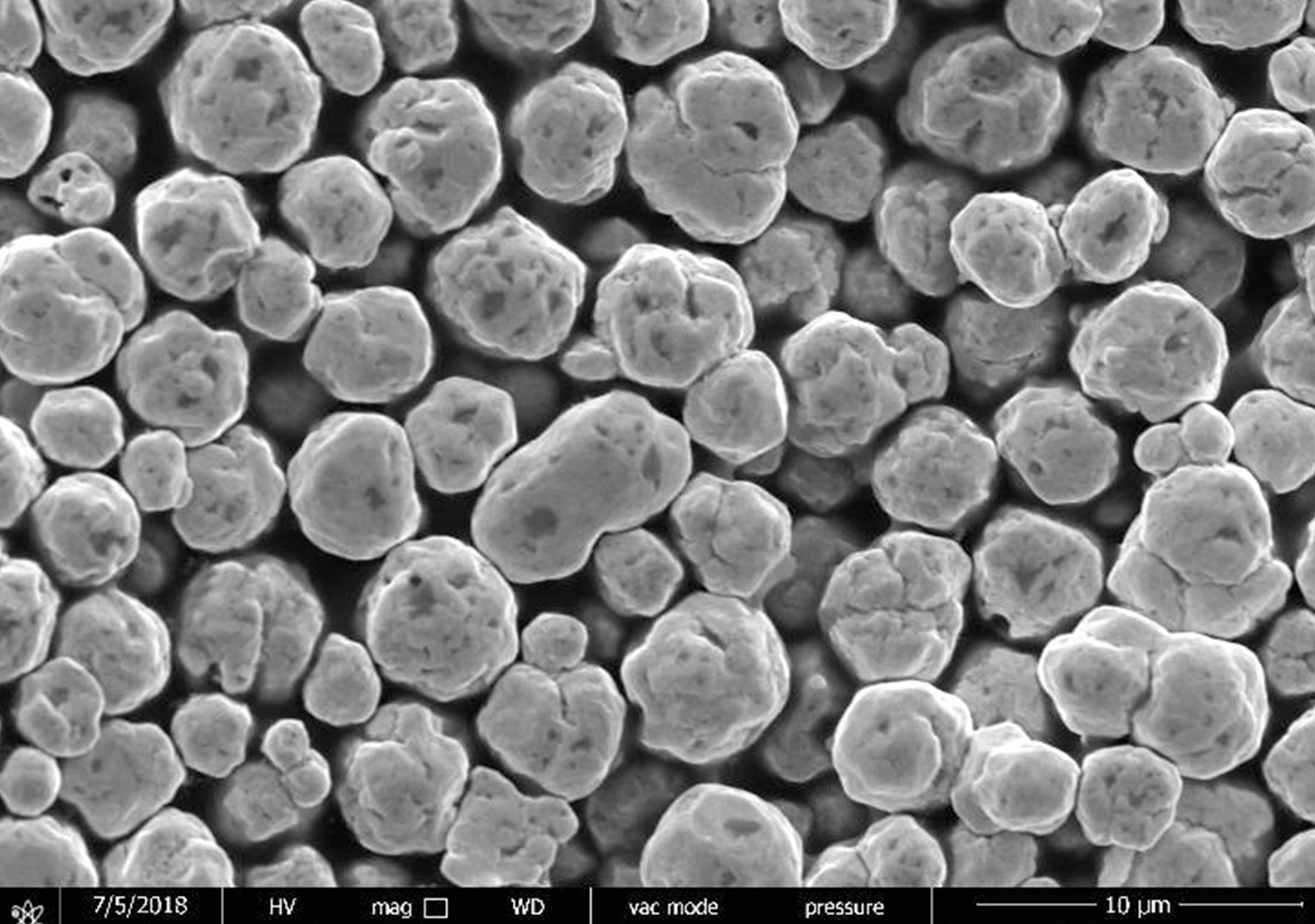
When working with low-temperature inks, your conductive network forms by evaporating solvent during thermal processing, suspending your filler particles in your binder, and allowing the particles to come in contact in a percolated network – essentially, a random web of connections which allow electrons to get from one end to the other.
In the vast majority of cases, that’s all there is to it – your particles are sitting there, touching each other while electrons find the shortest path through the network. That means that your conductivity is limited by contact resistance. If your particles get small enough (in the nanoparticle range), you begin to open up the possibility of necking and sintering, which blurs the line between individual particles. At that point, your conductivity can increase, but it’s usually a tradeoff between price and performance.
The vehicle
This is where a lot of the formulator’s magic comes into play. Choosing the right combinations and ratios of additives, binders, solvents, and dispersants to make sure that your ink is shelf-stable, mechanically robust, and printable is both an art and a science.
Luckily, this isn’t an article on making an ink, so we’re not going to dive too deep into specifics. Instead, let’s get familiar with what each component does:
- Solvent: The solvent dissolves your binder and particles, and contributes to flow characteristics of the ink.
- Binder: The binder matrix is a polymer or mix of polymers which provide the ink with structural properties – adhesion, flexibility, mechanical robustness, working temperature, and others.
- Dispersant: If you want your ink to flow right, cure right, and stay shelf-stable, you have to make sure your particles stay separated and well-dispersed throughout your material. Clumped, agglomerated particles will cause a lot of headaches.
- Additives: All the other stuff. Additives often include some modifiers to tune the flow properties of your ink for optimal print properties.
How do I choose a conductive ink?
The most important thing is that you can’t choose ink in isolation. Ink selection is an engineering decision. It means starting from your requirements, looking at your available options, and then optimizing for your desired outcomes and available resources.
Important questions you want to ask are:
- What are your performance criteria?
- How do you plan to make it?
- How much are you willing to spend?
- How does it have to interact with the user and the environment?
- Does it need to comply with any regulations?
In the same way, choosing an ink means making a number of important decisions, all of which stem from what you need your device to do. Once you know your application specifications, you then make an ink choice — which is really 3 decisions:
- An ink
- A substrate
- A printing technology
Our journey with conductive inks
Conductive ink is the lifeblood of our product line. Voltera has developed a rare expertise in the materials science of ink, the methods by which you’d print a conductive ink, and the practical applications and uses of the products or research you’re trying to create.
While many innovations in conductive ink are working towards a distant fully-printed future, the fact is that you likely interact with conductive inks pretty regularly. A membrane keyboard in your laptop, RFID tags, glucose strips, solar panels, printed heaters... Conductive inks are a staple component in many mature industries. Depending on your definition, even SMT resistors fall under the “conductive ink” family (fired thick film pastes, specifically).
When we were building what would eventually become our first product, the V-One PCB printer, we went through this exact situation. When we realized at the very early stages that conductive inks were a key component of our product — and they continue to be.
Luckily, after 12 years, hundreds of ink formulations, thousands of hours testing, and a lot of elbow grease, we’re here to help guide you through datasheets with vague specifications and uncertainty around material compatibility.
Do you still have questions? Book a meeting to talk to our in-house experts.
Conclusion
Working with conductive inks? Check out these resources:
- Materials Feature: Silver/Silver Chloride Ink
- A Compatibility Guide for Inks and Substrates
- The Role of Conductive Inks in Additive Electronics Manufacturing
- Dispensing systems for electronics prototyping from Voltera
And if you're curious about the latest Voltera content, don’t forget to subscribe to our newsletter!
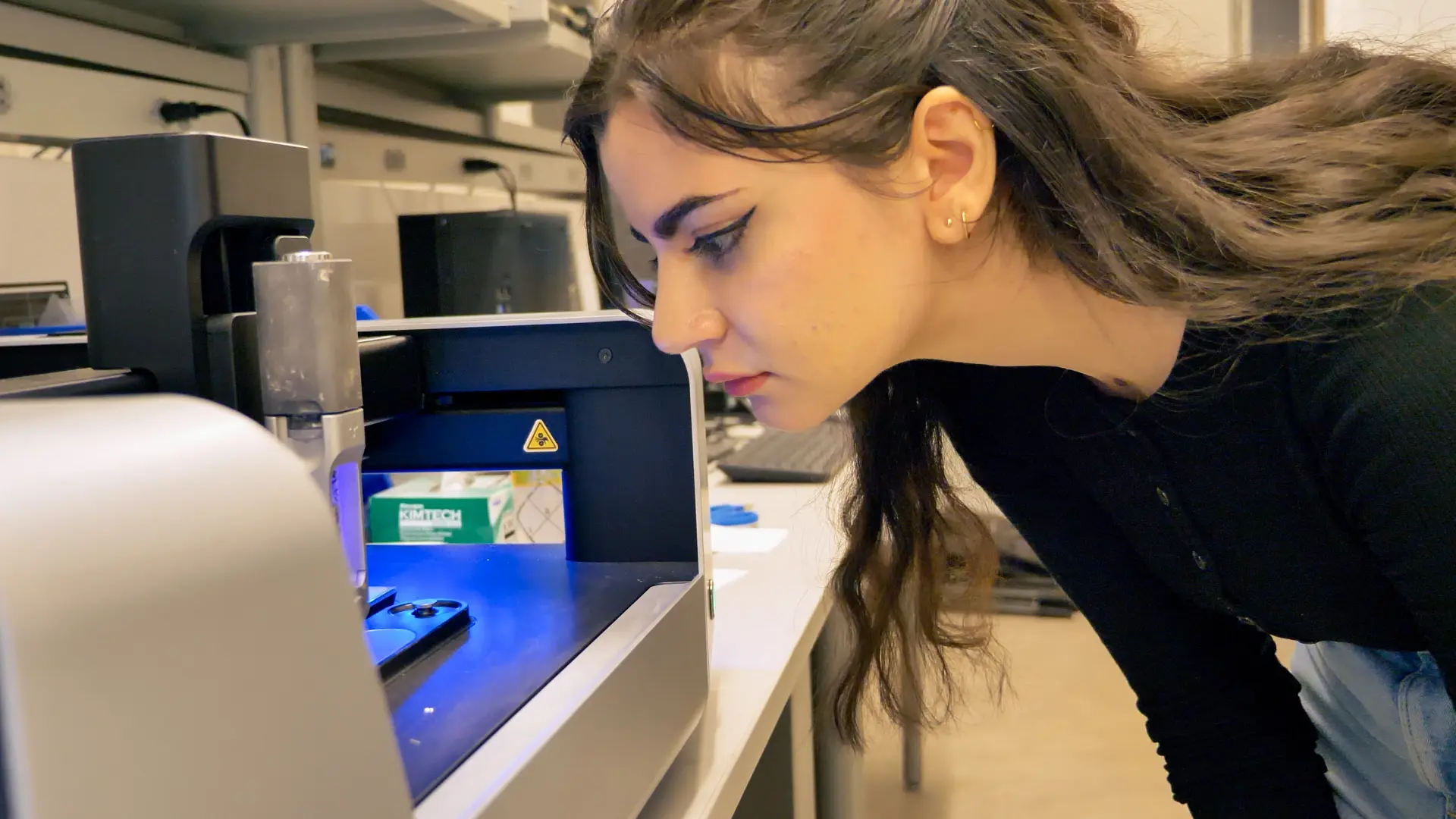
Check out our Customer Stories
Take a closer look at what our customers are doing in the industry.
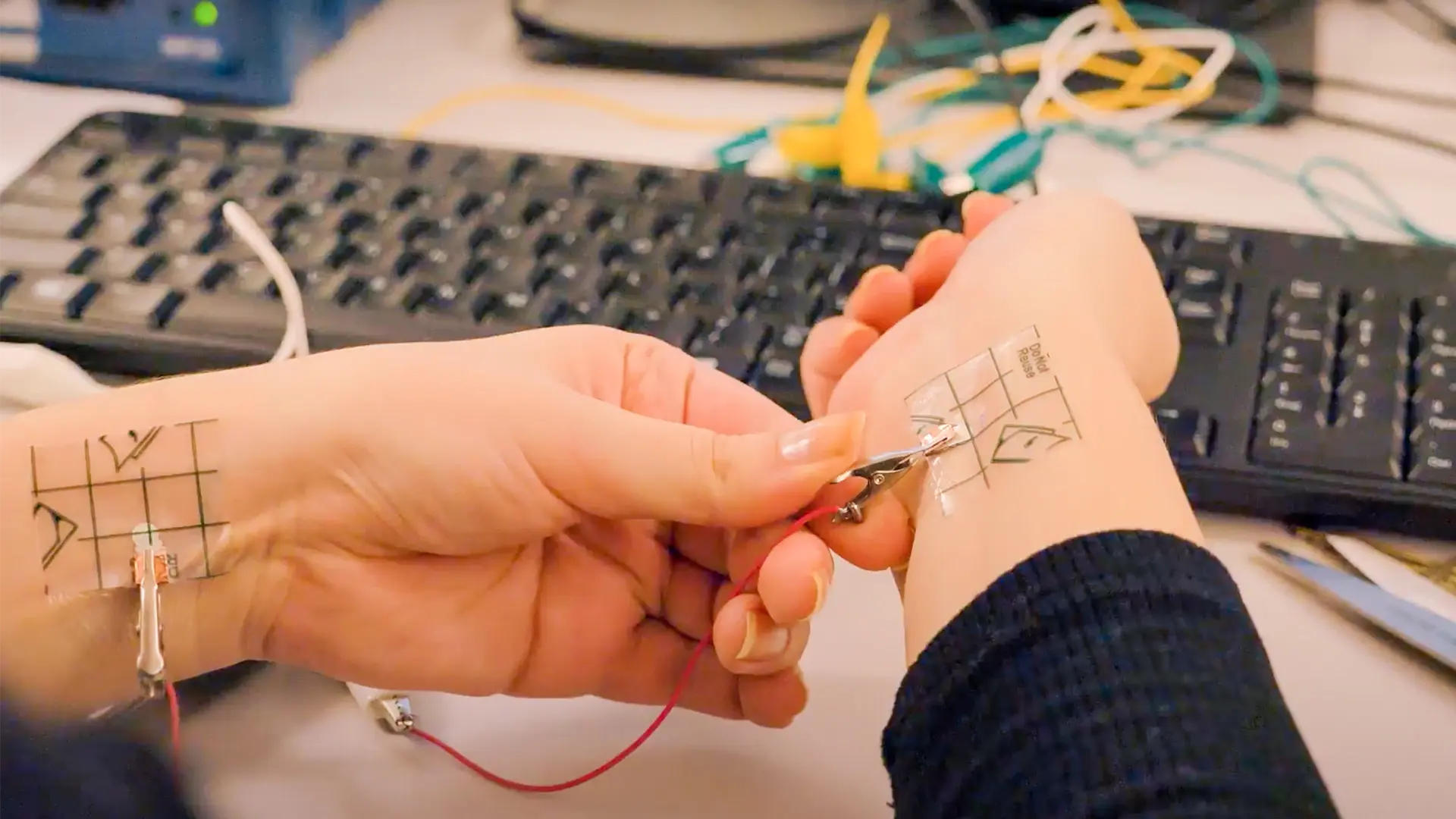