What Is In-Mold Electronics?
Twenty years ago, the idea of integrating electronics into devices seemed impossible — or, at least, very expensive. As new additive manufacturing methods like Voltera’s NOVA platform are introduced to the market, those newer, lighter, smaller, and more complex designs are becoming a reality.
Definition of in-mold electronics
In-mold electronics (IMEs) is the process of incorporating electronic elements into molded plastic objects. It typically consists of the following process:
- Printing a thermoformable circuit
- Thermoforming the circuit into a designated 3D shape
- Injecting a thermoplastic polymer to encapsulate the electronic devices
Depending on their end use, IMEs can include all the surface-mount devices (SMDs) included in traditional electronics to increase functionality, such as sensors, LEDs, and microcontrollers. SMDs are usually placed on the circuit before thermoforming. The final product is a functional, rigid plastic component.
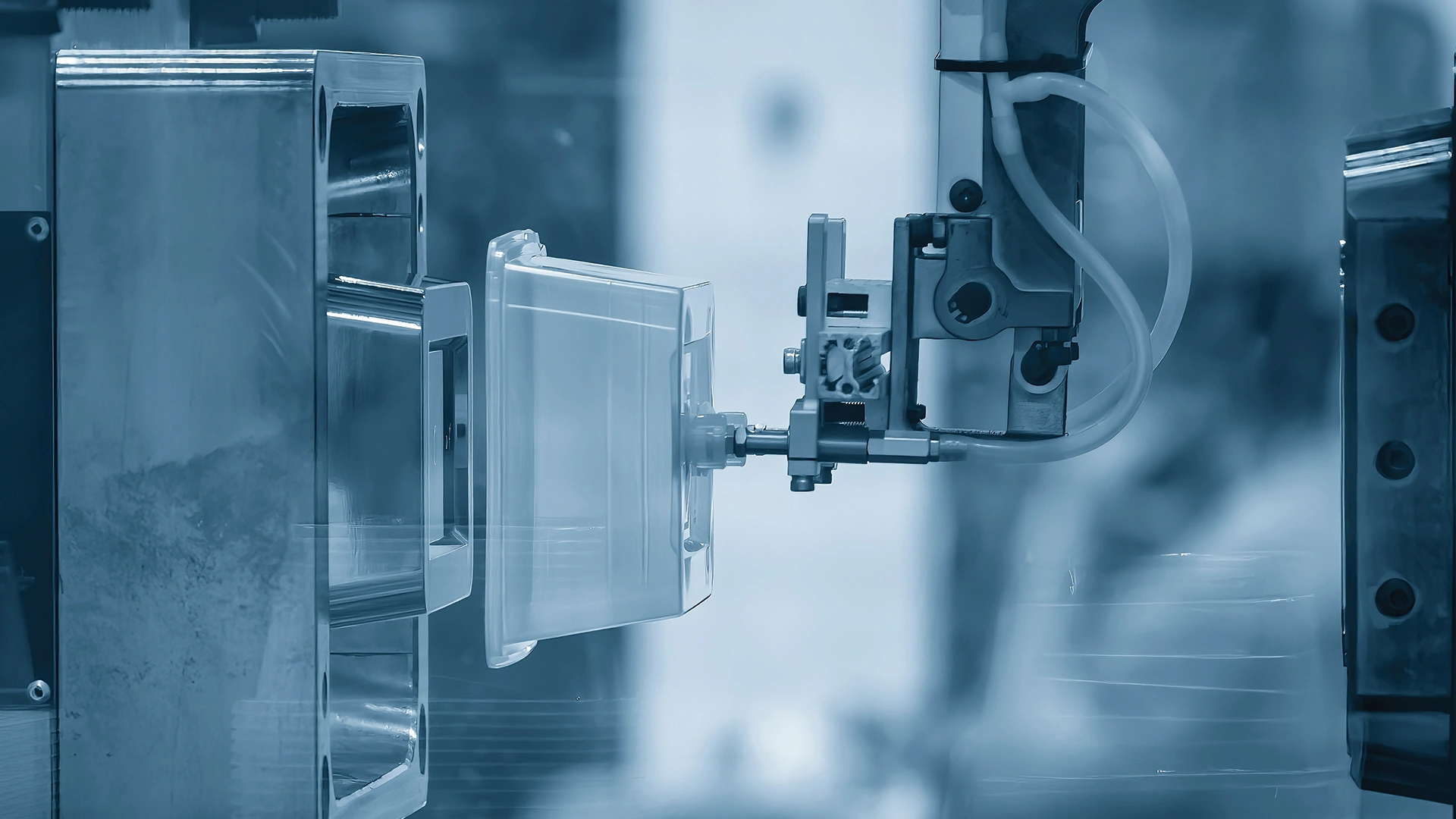
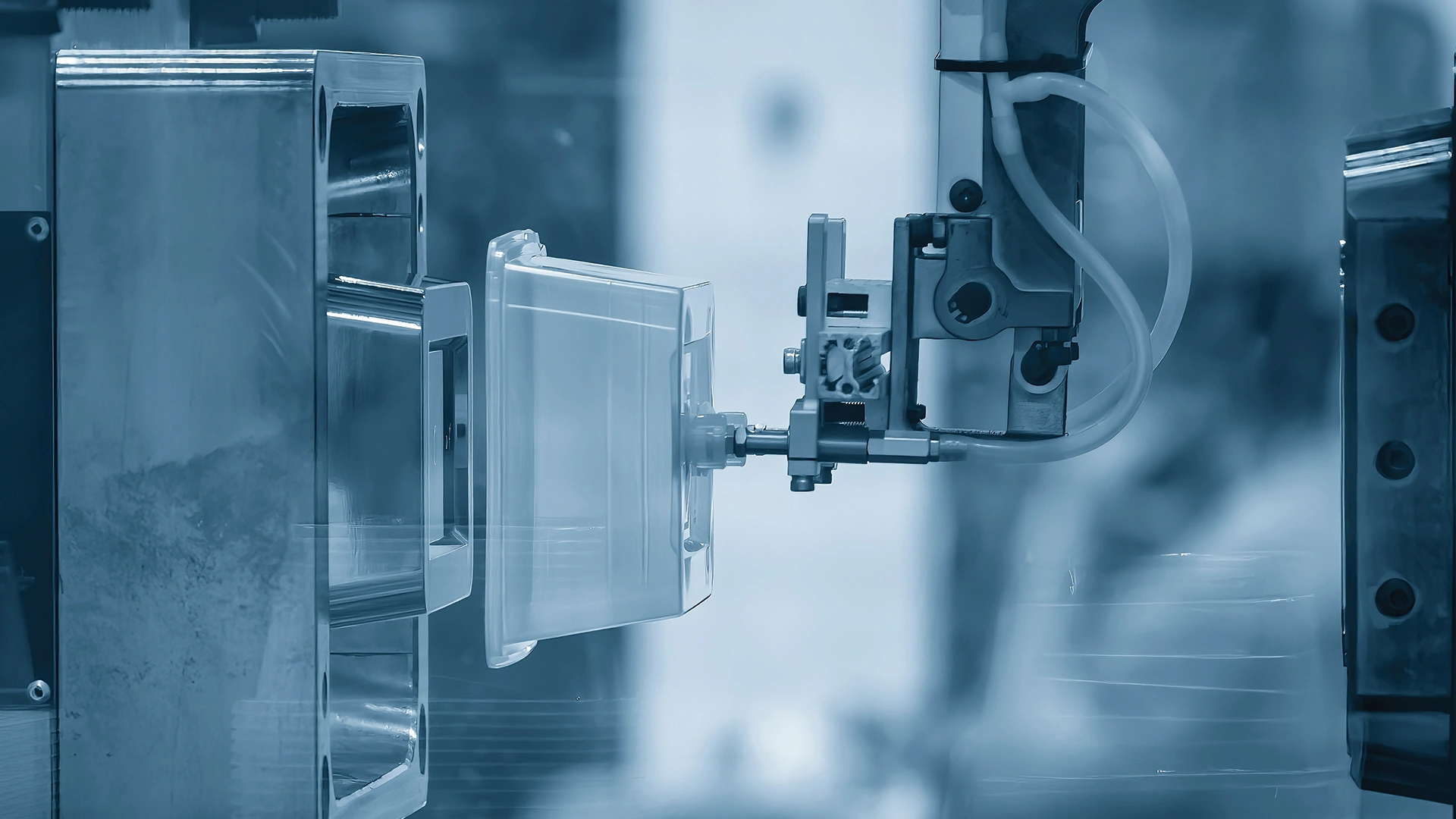
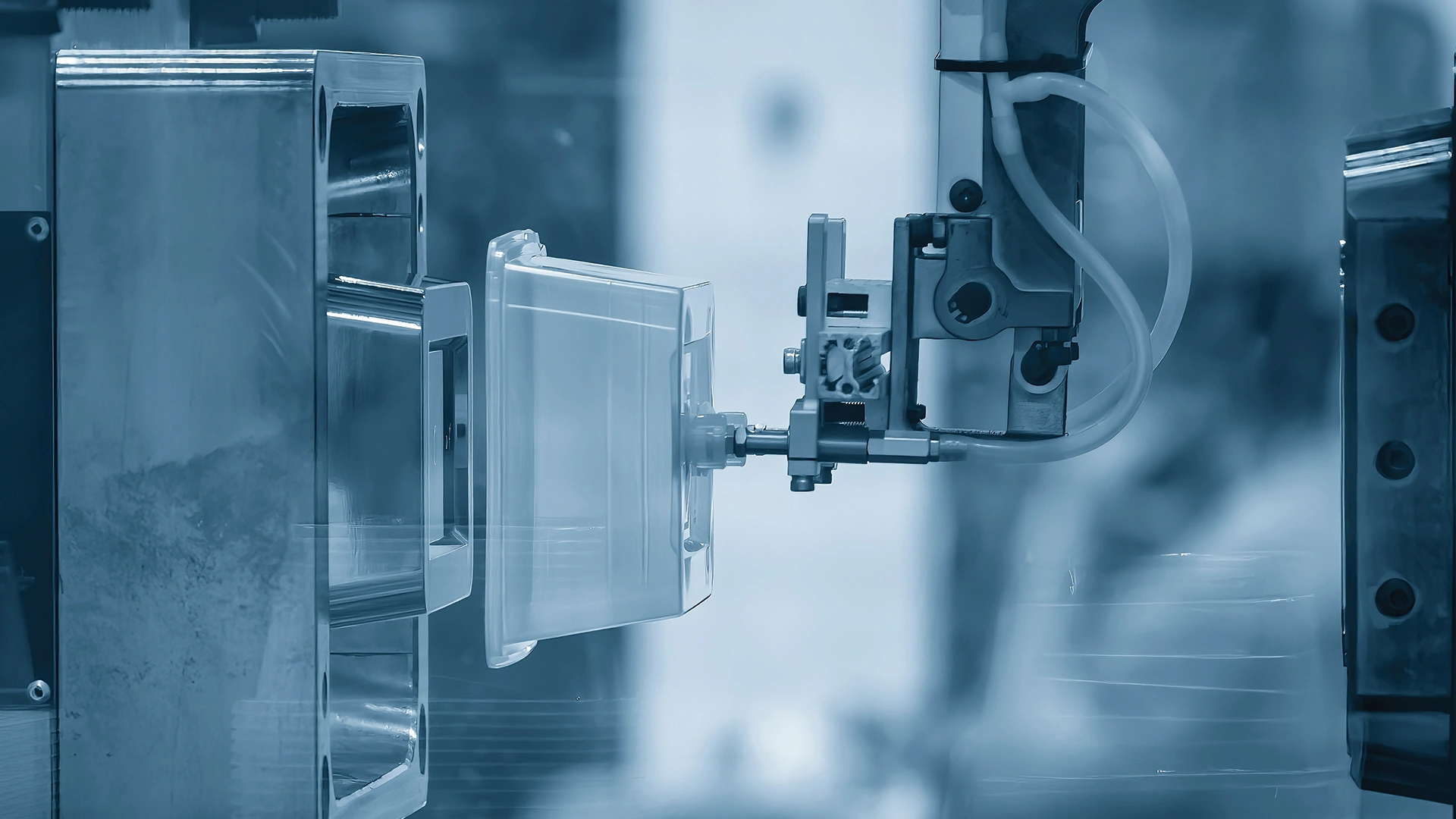
Market potential of in-mold electronics
IMEs offer unparalleled design freedom, allowing for sleek, modern, and lightweight designs that maintain high functionality, creating an excellent user experience. These electronics are water, scratch, and chemically resistant, making them highly durable and ideal for applications in harsh environments. Additionally, the highly automated workflow of IMEs can reduce manufacturing, assembly, and maintenance costs.
As a more sophisticated solution compared to the traditional approach of mounting rigid printed circuit boards (PCBs) inside rigid enclosures, IMEs are becoming increasingly popular in human-machine interface (HMI) applications in the automotive, medical equipment, aerospace, and consumer electronics industries. According to the report "In-Mold Electronics 2023-2033" by IDTechEx, the market for IMEs is forecasted to reach around USD $2 billion by 2033.
Applications
Automotive industry
IME technology in the automotive sector is used to design sophisticated HMIs, including touch-sensitive dashboards, integrated lighting, and control panels. These designs eliminate traditional mechanical buttons, wires, and connectors, allowing for a streamlined, button-free interface. The resulting designs are not only visually clean but also functionally integrated, blending seamlessly with the vehicle's interior.
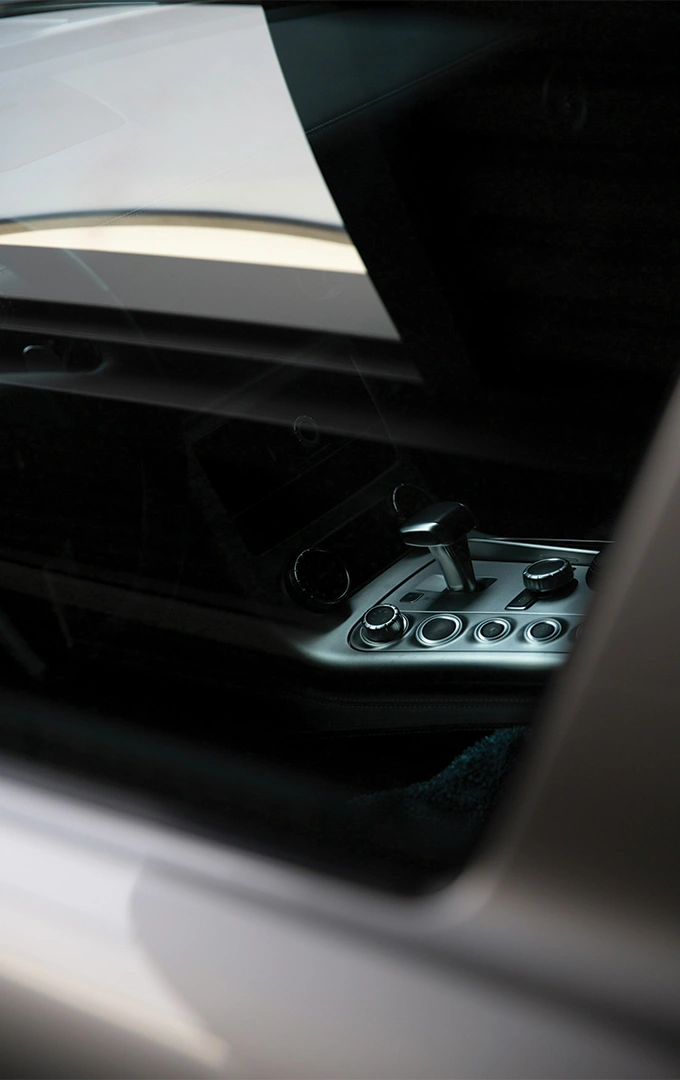
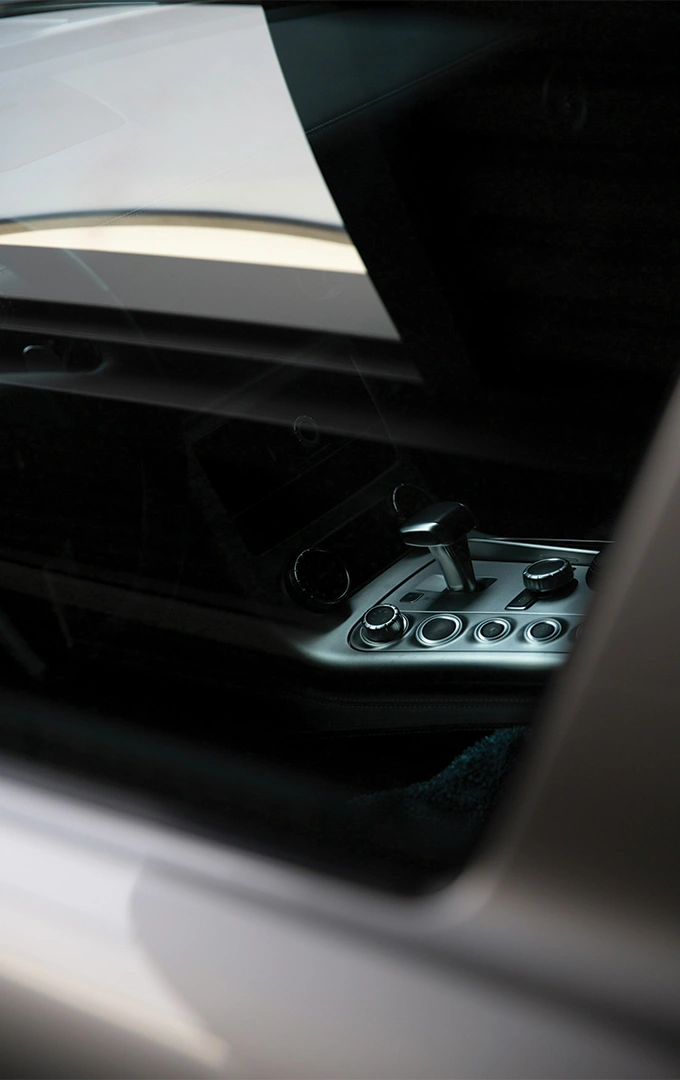
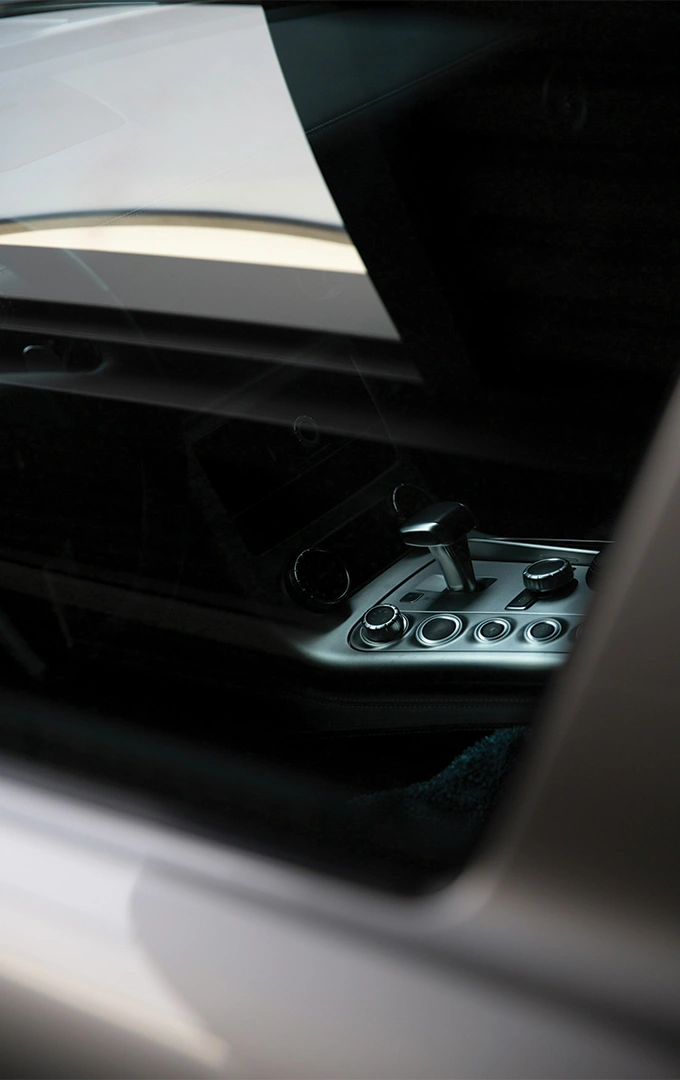
Consumer Electronics
In consumer electronics, IME is applied to products such as headphones, smartwatches, fitness trackers, and smart home devices. Tactotek, for example, has utilized IME technology to develop headphones with a thin, transparent user interface set into a curved plastic frame. This design emphasizes minimalism and subtle integration of electronic controls. The touch controls and responsive lights are discreetly incorporated, providing an intuitive and straightforward user experience.
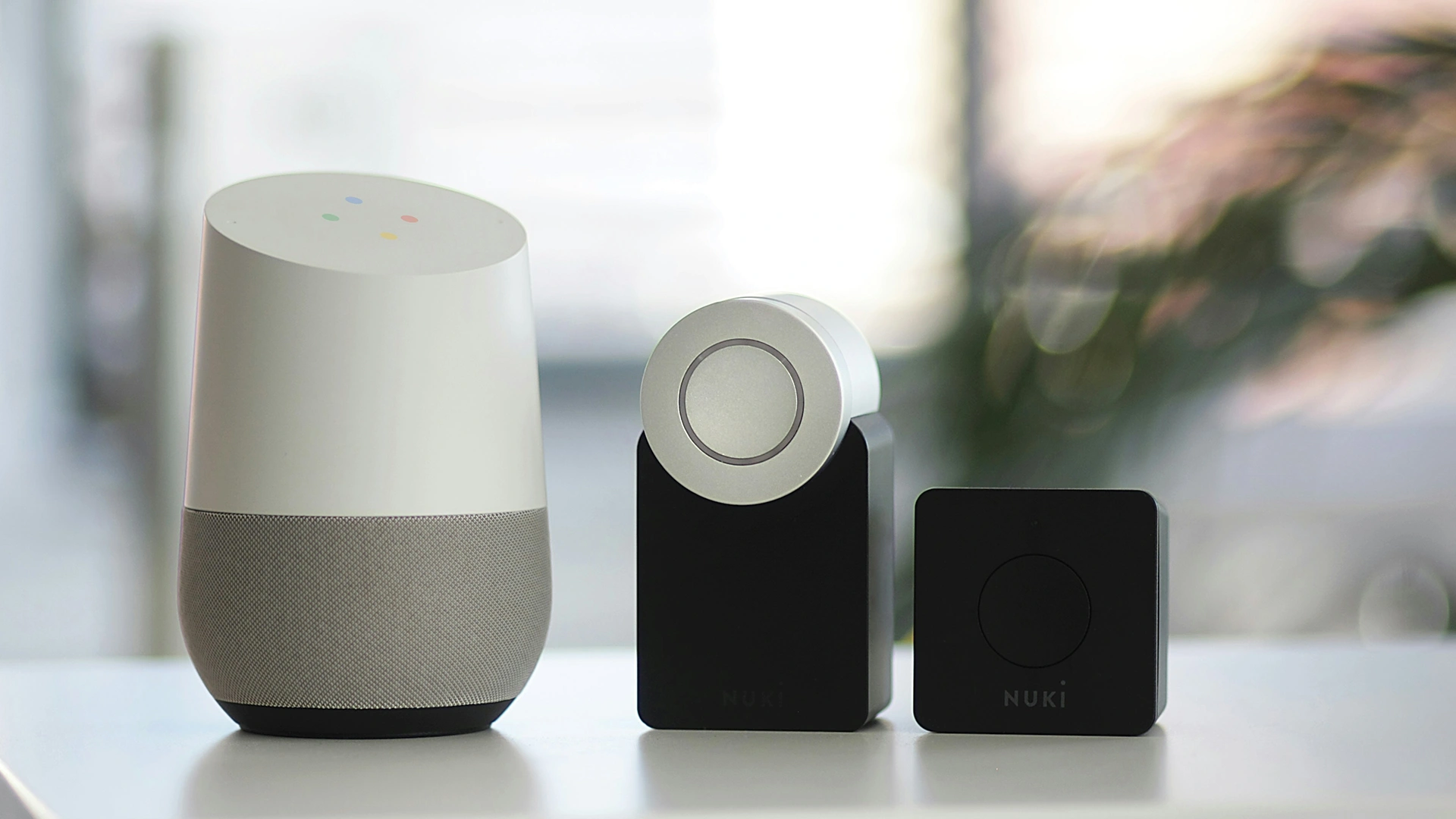
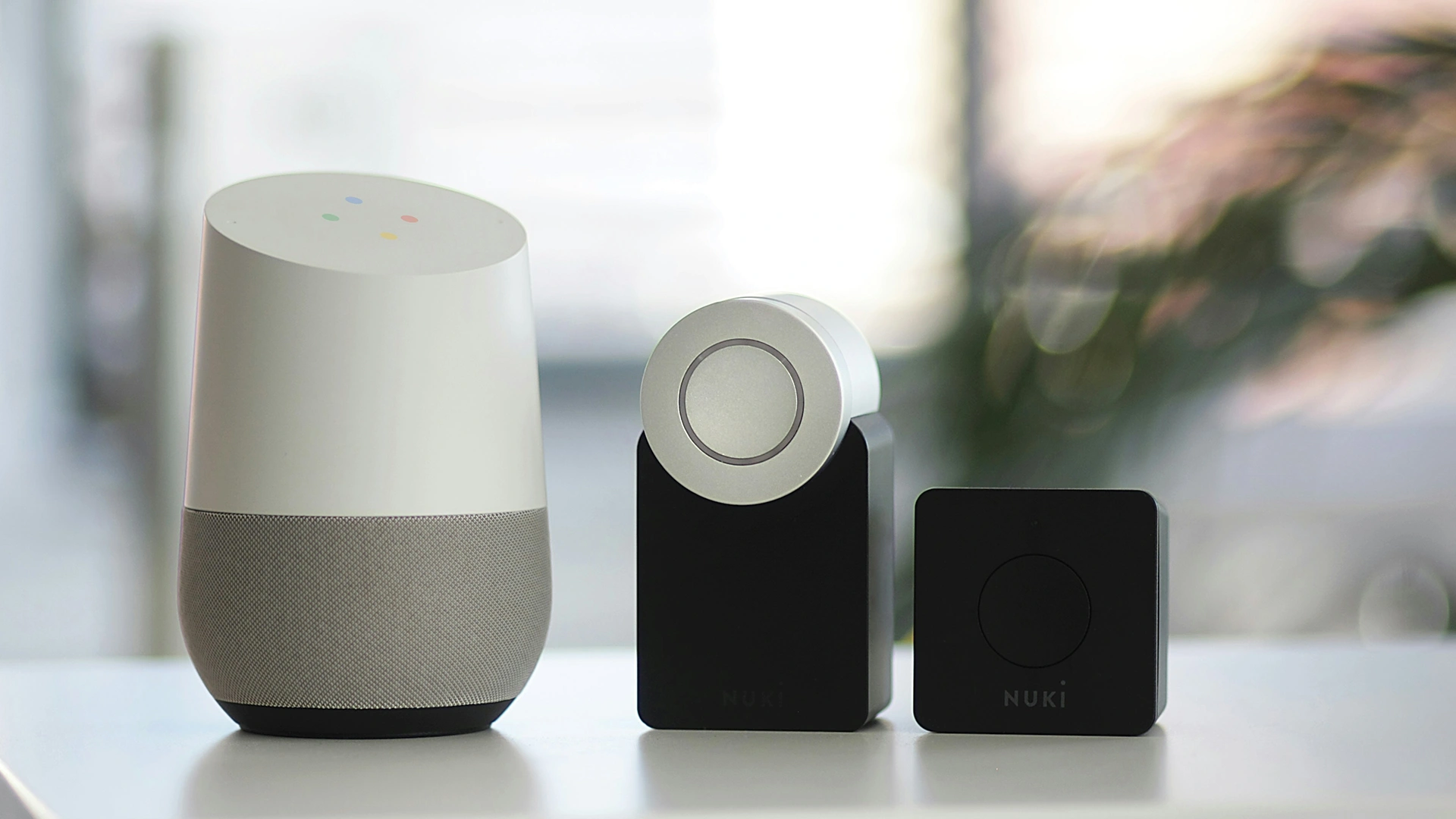
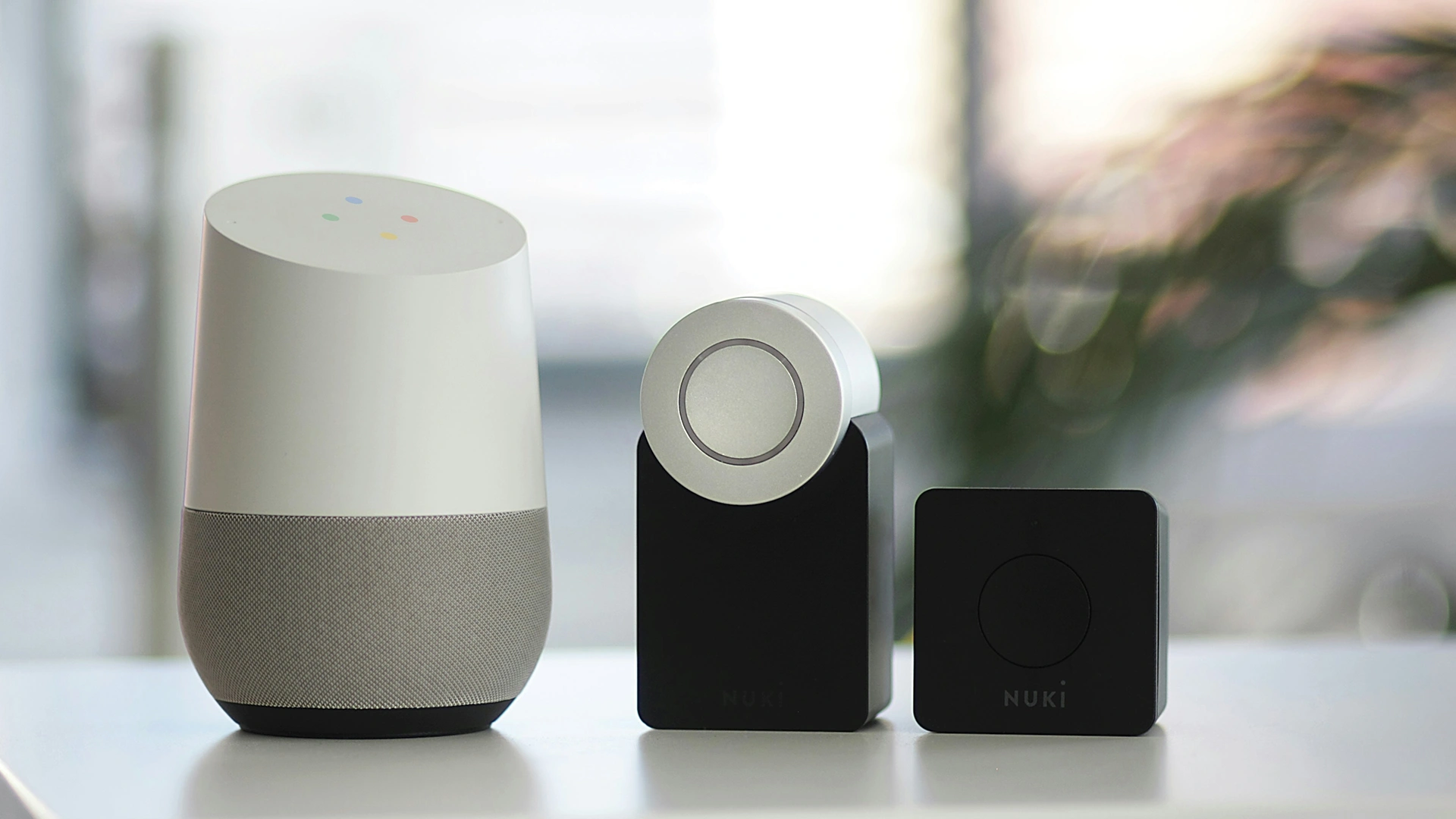
Inks for in-mold electronics
Conductive inks, dielectric inks, and conductive adhesives used in IMEs must withstand the thermoforming and injection molding processes, requiring resistance to high temperatures, pressure, and elongation. Conductive inks, in particular, need to provide high electrical conductivity, low contact resistance, and good adhesion. To ensure compatibility and optimal performance, it is advisable to select inks from the same supplier.
A few ink suppliers that make inks for IMEs include:
Conclusion
As the market for IME technology continues to grow, its potential to enhance user experiences and improve product performance is increasingly recognized. To learn more about IMEs, check out these resources:
- In-Mold Electronics 2023-2033
- Unravelling Competing In-Mold Electronics Manufacturing Methodologies
- In-Mold Electronics (IME) Market Report
Want the latest news in printed electronics? Subscribe to our newsletter. If you have questions about additive prototyping and low volume manufacturing of electronics , please contact us.
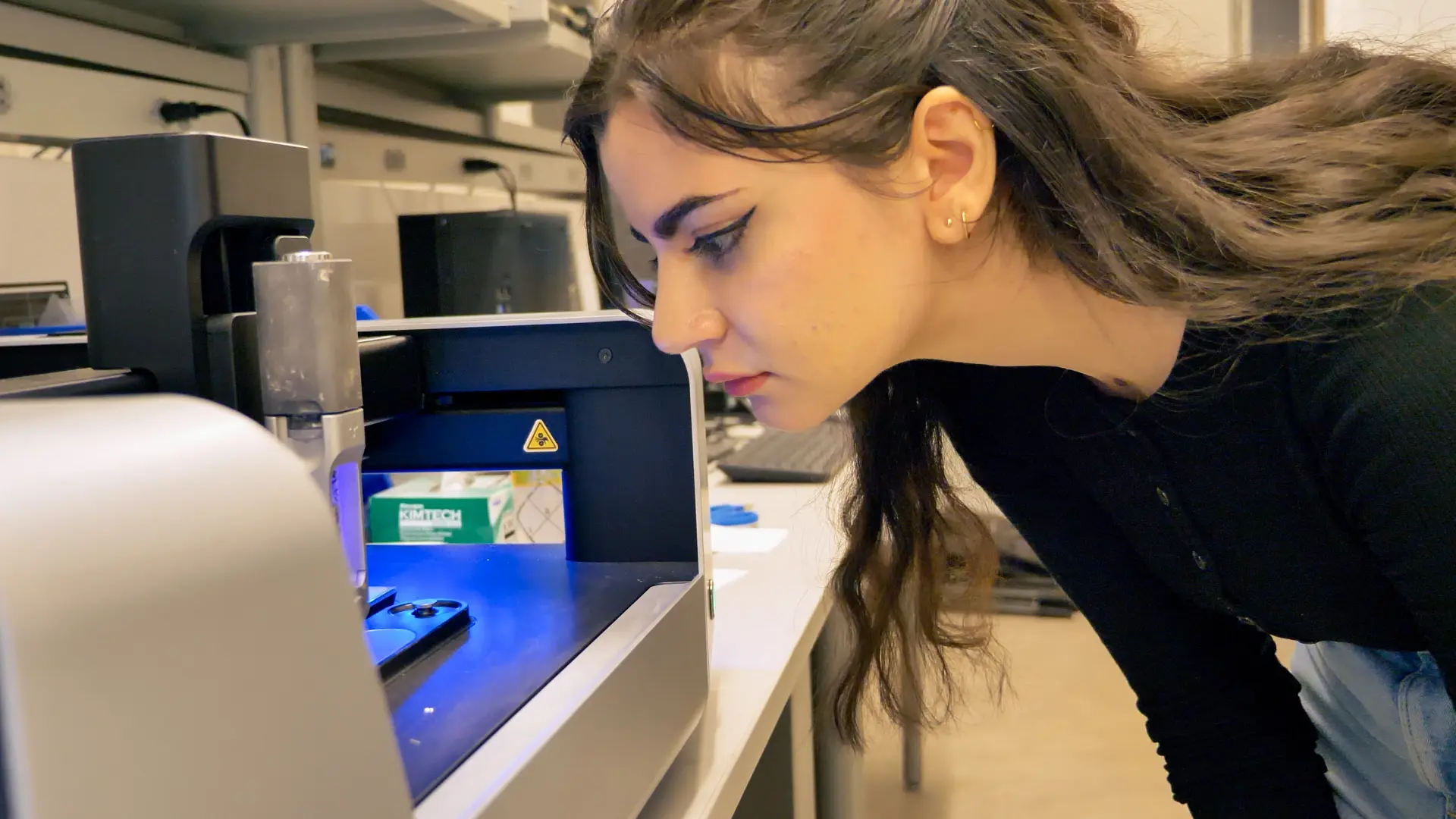
Check out our Customer Stories
Take a closer look at what our customers are doing in the industry.
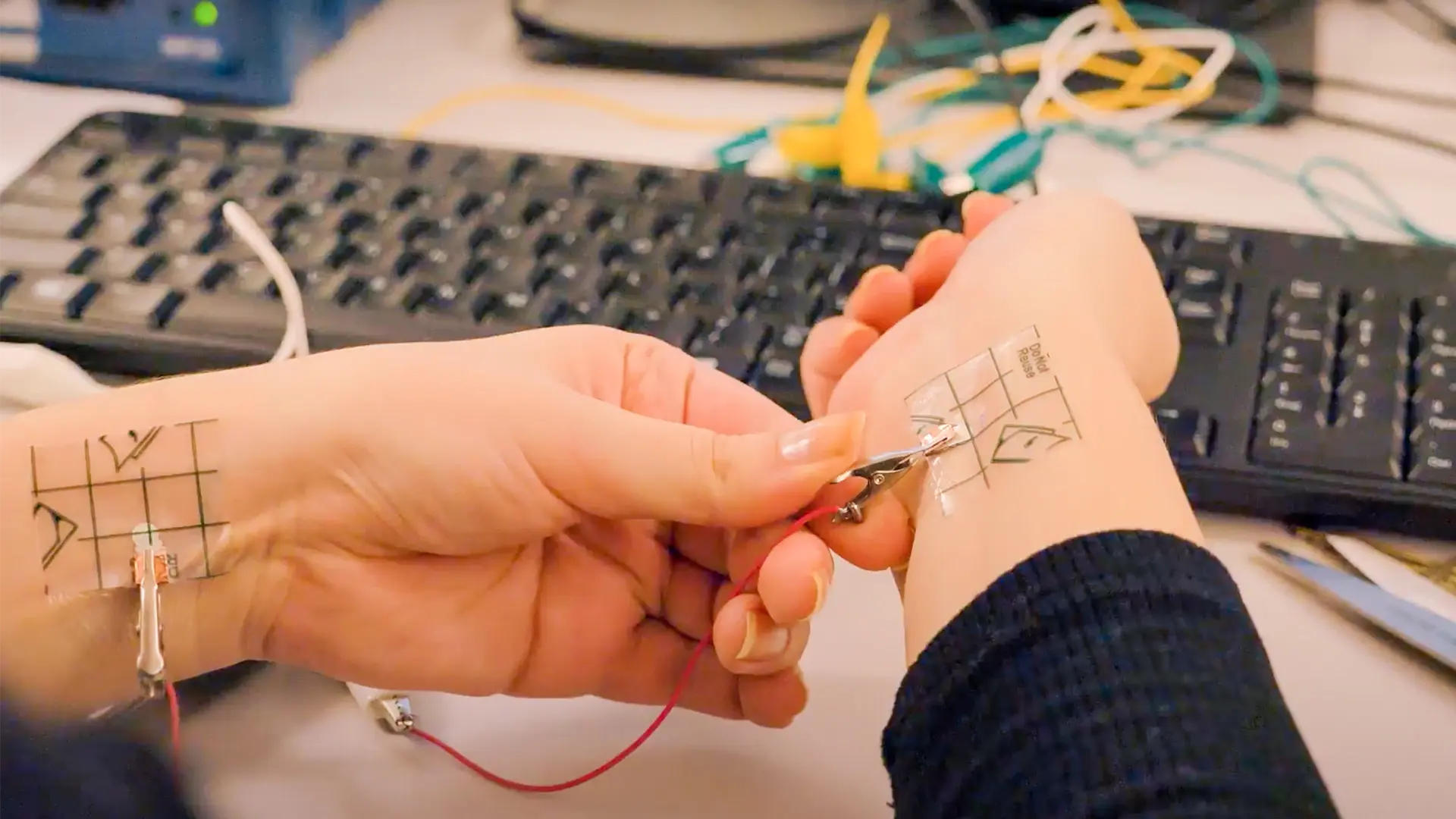