Introduction to Gravure Printing Technology
As you probably already know, here at Voltera we’re really big fans of making the field of printed electronics more accessible — and teaching people how to navigate without needing a PhD in materials science! That’s why we’ve been taking the time to break down different printing technologies — like inkjet, aerosol, flexography (affectionately nicknamed, “flexo”), our personal favorite, direct-ink-write technology.
The focus of this article is to introduce the concept of rotogravure printing technology (AKA gravure), walk you through the pros and cons, and hopefully give you all of the information you need to decide if this is the printing technology that will help you bring your idea to life!
Let’s go.
What is gravure printing technology?
Gravure printing technology is an analog process — meaning it doesn’t use a digital file, it uses a physical rendering of the pattern that you’re trying to print. On the surface of things, it’s a stamping technique; conductive ink is applied to an impression and stamped onto your substrate. It was given life in the magazine industry since it is better suited for porous substrates — like paper.
But of course, there’s a little more to it — so let’s take a deeper look!
How does gravure printing work?
Gravure uses an anilox roll — a hard cylinder with a steel, or aluminum core — where your pattern is engraved directly into the roll. The engraving allows you to have pitch differences depending on how tall you want your traces to be. The resolution is measured in lines per inch. Once you have your anilox roll, you apply your conductive ink to the roll, and the conductive ink gets deposited in the grooves — an important distinction because of gravure’s printing technology cousin, flexographic printing. Once the conductive ink is applied, there’s something called a doctor blade which is used to scrape off any excess conductive ink and ensures that the only thing printed will be your pattern.
Next, the anilox roll is applied to the roll that has your substrate on it, in order to “stamp” the pattern on your substrate.
Important to note: Traditional rotogravure uses the capillary force of the substrate to wick the conductive ink out of the wells of your anilox roll and onto the substrate, therefore you need a porous substrate. Because of this capillary action, you get absorption of your ink into the substrate. This isn’t ideal for conductive inks — which is why printing conductive ink on paper has been such a challenge, and why gravure isn’t our favorite technique for printed electronics.
FUN FACT: Gravure printing technology was the printing technology that was traditionally used to print banknotes!
In printed electronics, gravure technology uses applied force to transfer the ink to the surface of your substrate — not capillary action — so it does work on non-porous substrates like glass, PET, and FR4. With gravure printing technology, you can get pile heights below one micron, and you’ll need a conductive ink with viscosity ranging from 10-100 centipoise.
Benefits and challenges of gravure
BENEFITS
- It’s quite fast! Because it’s on a roll, the limit for how quickly you can print is basically how fast you can spin the roll.
- The resolution on patterns printed by gravure printing technology can get quite fine.
- Because the pattern is etched into the anilox roll, you get pretty good consistency between prints.
- For a mass production method, it’s quite cost-effective.
CHALLENGES
- Can be tricky with longer traces — uneven roll pressure can cause conductive ink to wick along the ridges of the cylinder, leading to gaps in your traces.
- Iterating is pricey. The anilox roll costs thousands of dollars to have made (an outsourced process, generally speaking — so don’t drop it!) and any changes in your pattern will require another entire roll.
- RK Instruments offers something called a K Proofer which is a machined steel plate with your pattern etched into it. It will give you a sense of how your conductive ink is behaving — is your solvent evaporating? Is the viscosity going to work? — but it’s still pretty pricey for getting to proof of concept.
- Limits your material choices! You need to pick a conductive ink that doesn’t have a solvent that will damage the roll or leach metal out of the anilox roll. One degrades the roll — and your pattern — meaning you’ll need another one to keep printing. The second can cause unpredictability in the conductivity of your traces due to the added metal content.
Materials and performance
With gravure printing technology, you can work with conductive inks that are a bit more viscous than those required for inkjet printing technology — but you won’t have access to the conductive inks that are viscous enough to use with screen-printing technology. As mentioned previously, you’re also limited by the solvent content of your conductive inks because they may have an unintended effect on the anilox roll — to the detriment of your roll and your traces.
In terms of substrates, you have a fairly diverse pool of substrates to choose from, as long as they’re non-porous. Porous substrates will absorb the conductive material and the consistency of your traces will be suspect at best. Not great from a reliability standpoint — and that’s one of the major selling features of gravure printing technology, to begin with.
Conclusion
That’s about all we have to tell you about gravure printing technology — but we’re always willing to learn more! If you or someone you know is an expert in the field of gravure printing for printed electronics, we would love to hear from you.
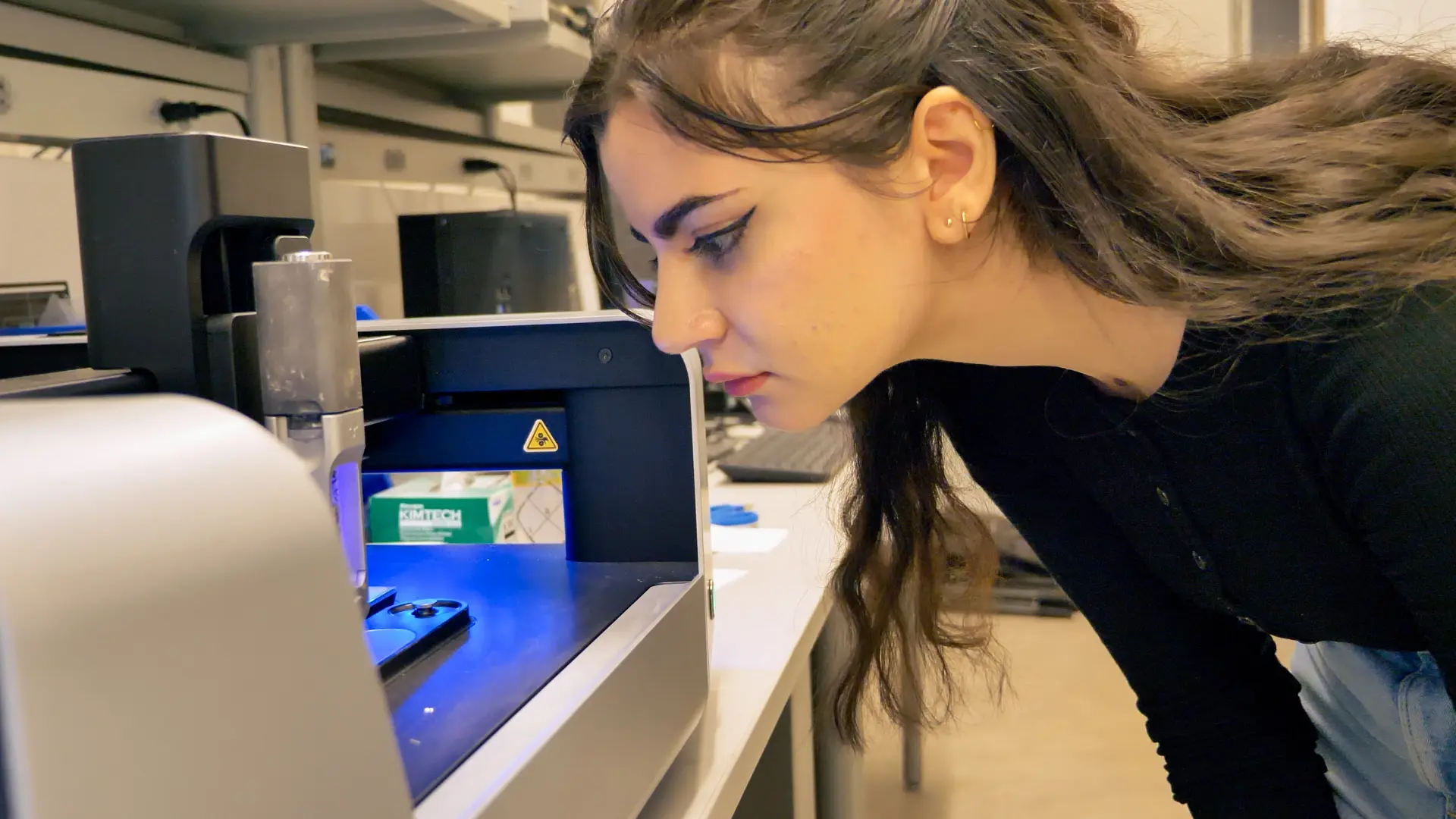
Check out our Customer Stories
Take a closer look at what our customers are doing in the industry.
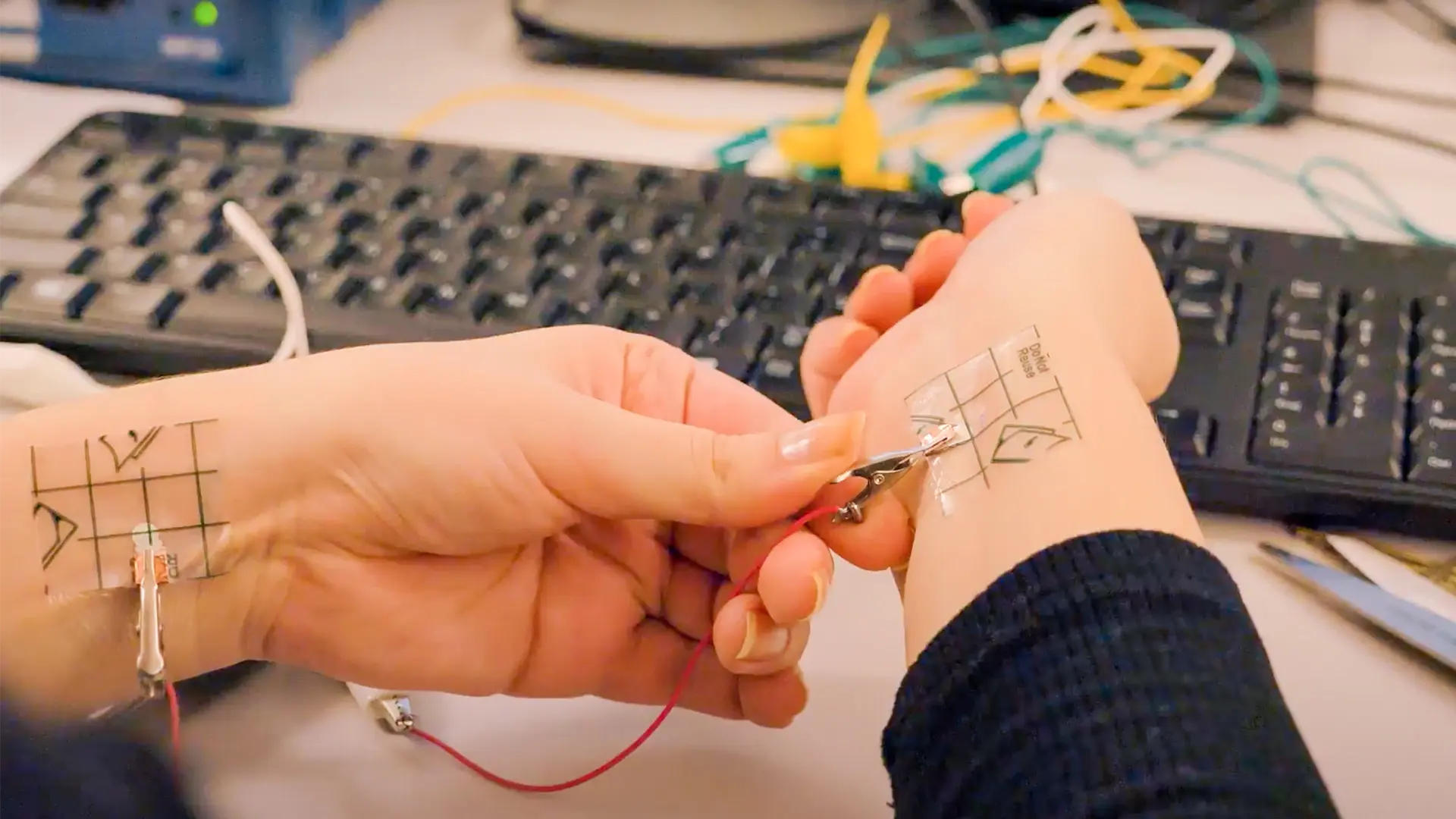