What are Precision Fluid Dispensing Systems?
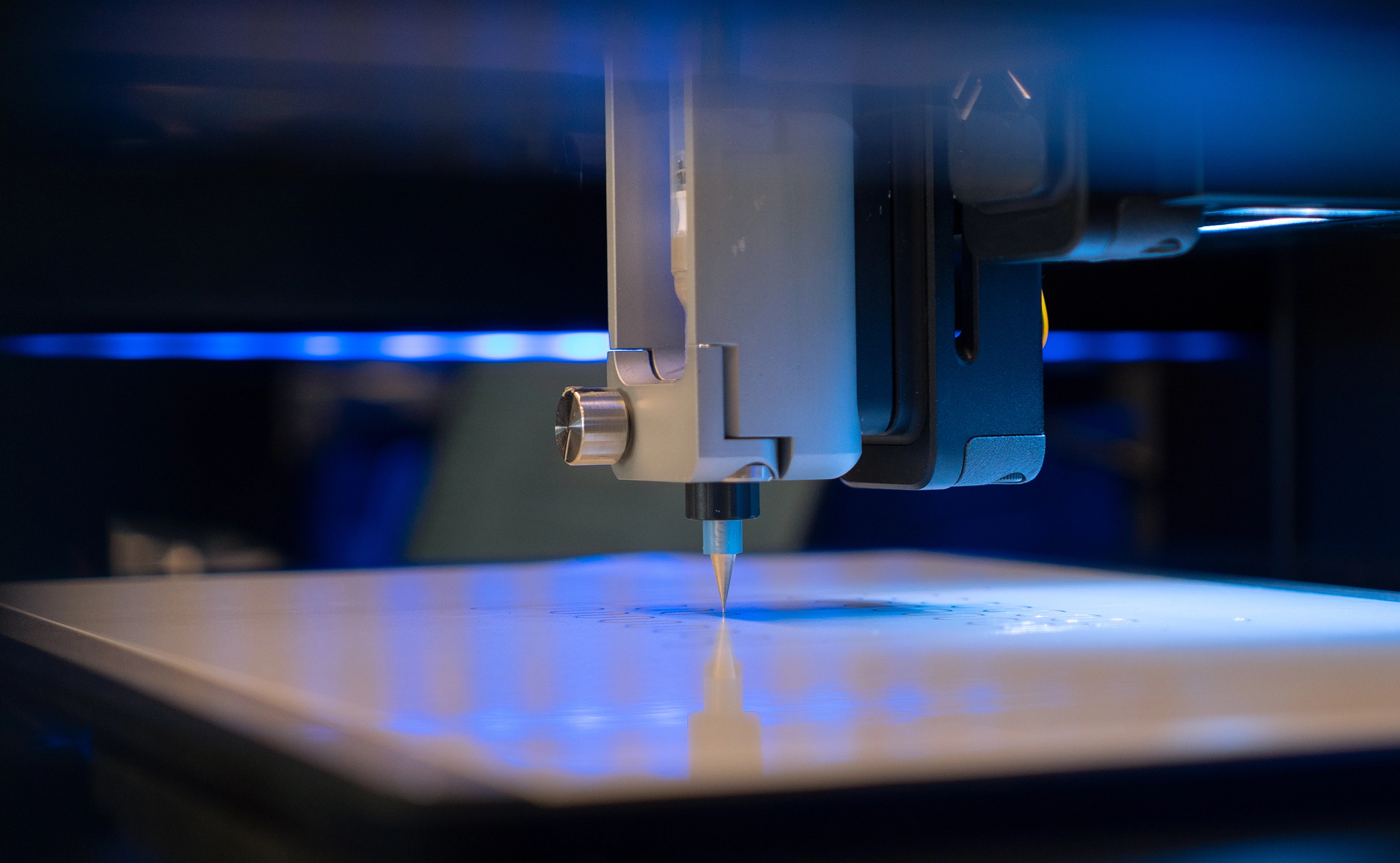
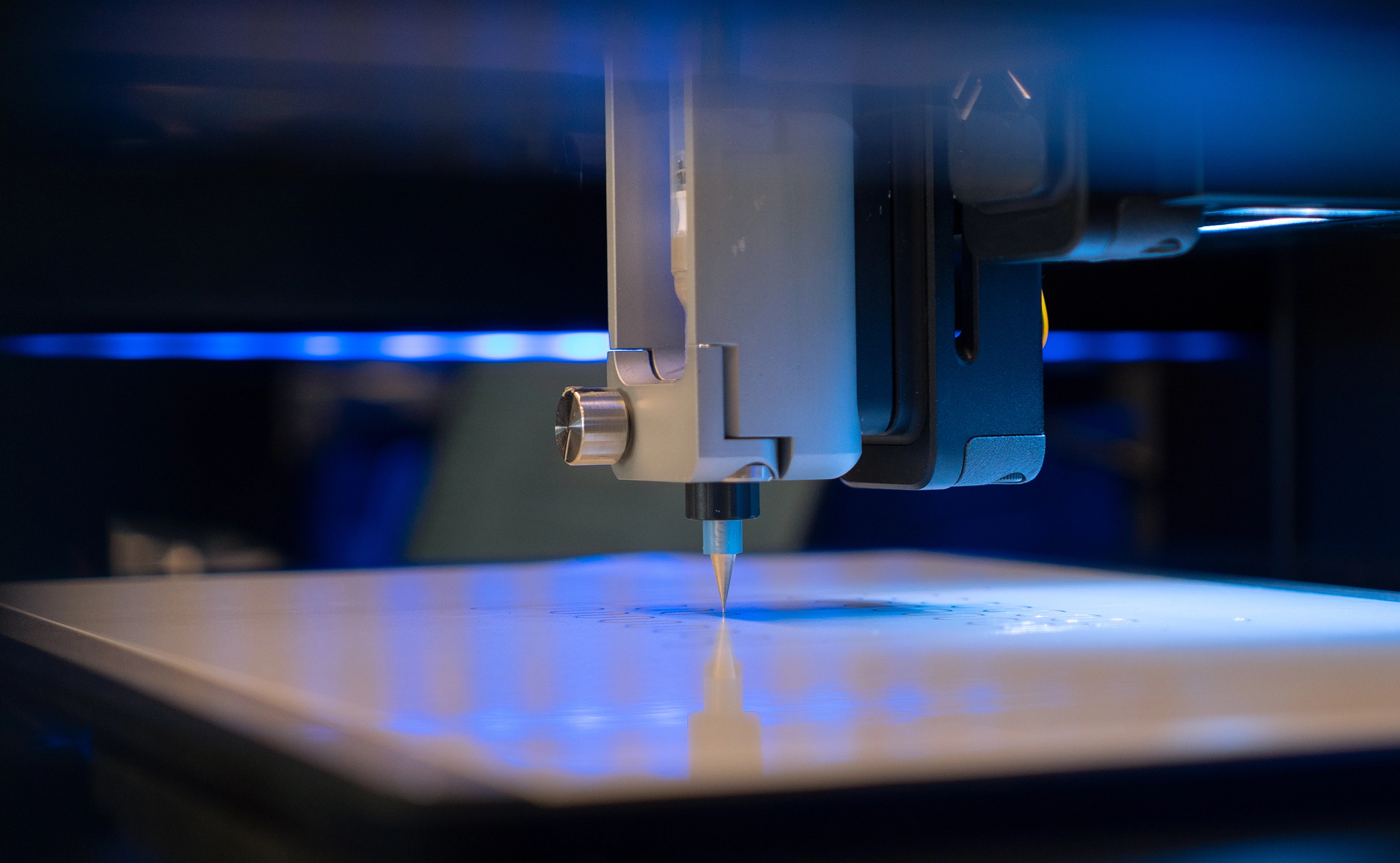
Precision fluid dispensers play a crucial role in manufacturing the products we interact with regularly. They are used in a wide range of industries, so much so, we often forget their role in our everyday lives.
In this article, we will provide a brief overview of fluid dispensing systems, highlight their applications, discuss common challenges with the technology, and share an overview of NOVA, our materials dispensing system.
What are precision fluid dispensing systems?
Precision fluid dispensing systems allow users to deposit micro amounts of assembly fluids onto a substrate in targeted areas. When dealing in microlitres or nanolitres, the amount of fluid deposited is often nearly impossible to control with most manual pumps and flowmeters. These systems were developed to implement control, precision, accuracy, and consistency in applications requiring microdispensing.
The two most common types of systems for fluid dispensing are:
Non-contact
Also known as jet dispensing or jetting. In a jetting system, the fluid is deposited or “jetted” onto the substrate from a distance.
Contact
This method uses a valve to deposit material in a highly controlled manner. It offers compatibility with a wider range of fluids compared to non-contact systems. Some examples of contact systems include:
- Pneumatic/time pressure: Pulses of air engage the top of the plunger in a specific pattern, driving the plunger forward in the syringe and depositing material.
- Mechanical positive displacement: A rod or piston that forces fluid out of the cartridge.
- Auger: A motor enables the auger screw to rotate, pulling material from the reservoir and guiding it towards the nozzle.
- Progressive cavity (PC) pump: Similar to an auger system, PC pumps utilize a rotor and stator to fill tightly sealed cavities with precise amounts of fluid which are then pushed towards the nozzle, enabling larger consistent deposits with high viscosity fluids.
Fluid dispensing applications
Numerous industries utilize dispensing systems for depositing materials, such as:
- Electronics: Solder pastes, conductive adhesives, conductive inks, flux, coatings, underfill adhesives, and dam and fill.
- Medical: Biomarker detection, and in- and on-body biomedical sensors.
- RFID: Eco-friendly and cost effective non-contact data transfer and localization systems.
Recent research indicates the electrical and electronics assembly segment was the leading global market for fluid dispensing equipment in 2024.
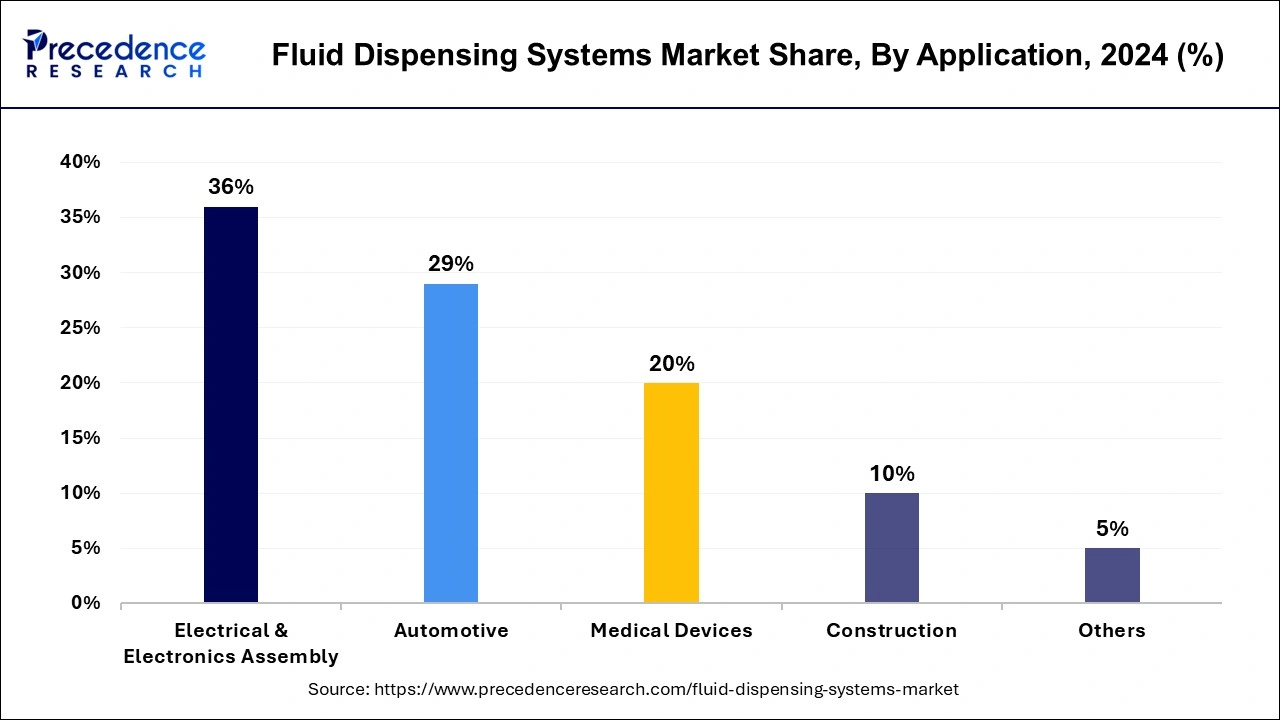
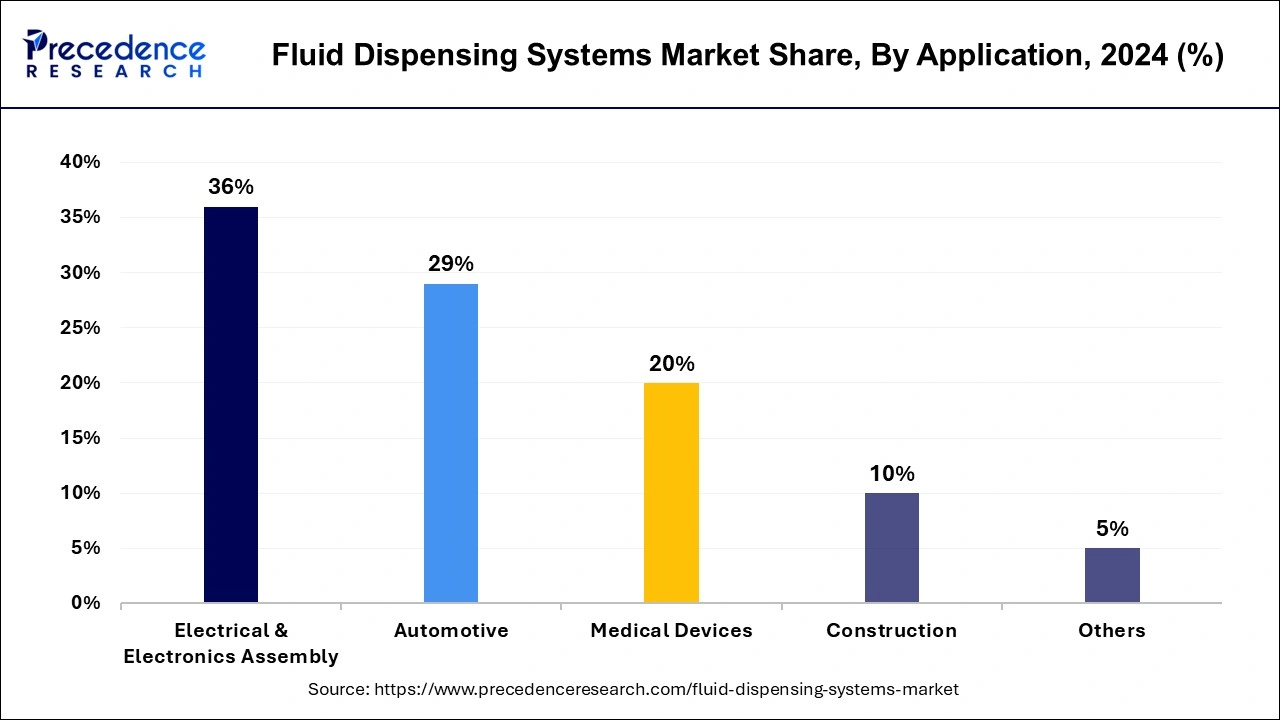
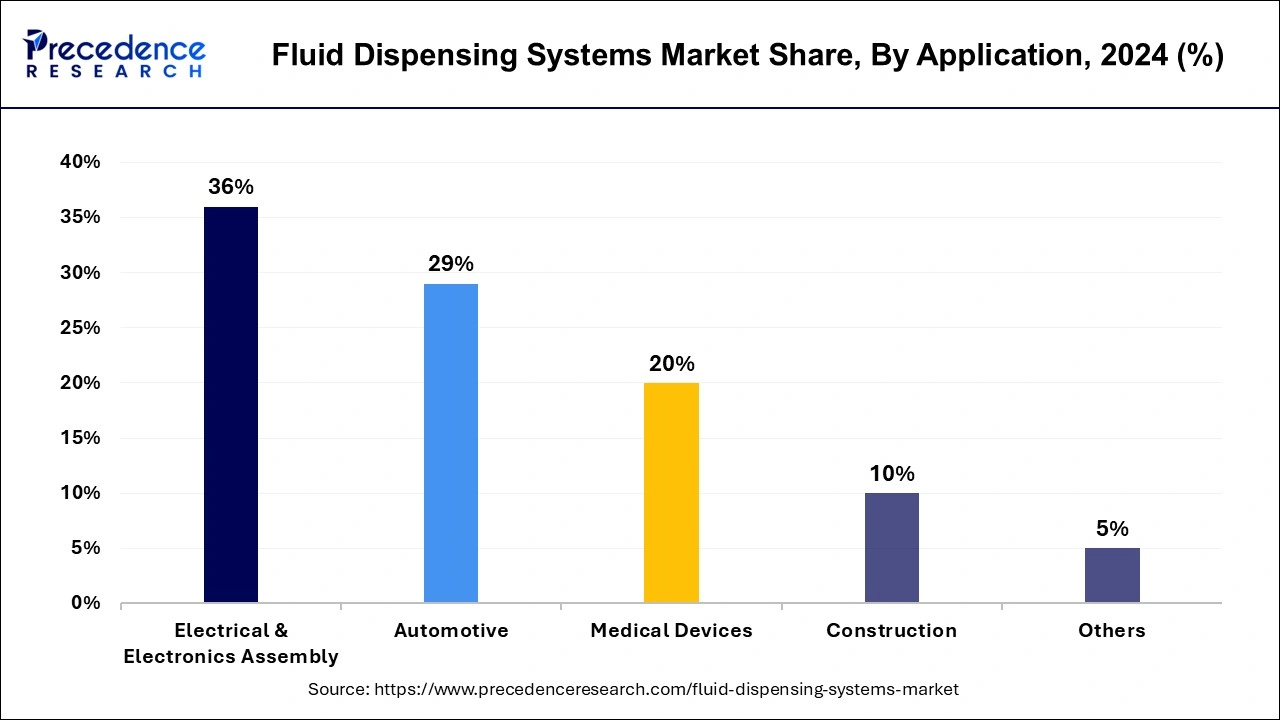
Materials used in fluid dispensing
Precision fluid dispensers enable a diverse range of material compatibility. Some of the most common materials used in these systems are:
- Flux: A chemical compound used in preparing metal surfaces for soldering.
- Conductive ink: Printable materials that are capable of conducting electricity.
- Lubricant: Oily materials that help reduce friction in surfaces that contact each other.
- Solder paste: Powdered metal solder that is suspended in flux.
- Adhesive: Substances that are capable of holding at least two surfaces together permanently.
- Sealants: Materials that attach at least two surfaces together, filling the space between them.
- Conformal coatings: A film applied over components that provides protection against contaminants and environmental factors.
- Epoxy underfill: An epoxy-material used in PCBs to connect a chip to the board through capillary action.
In the same research report referenced above, the graph below shows the growth of fluid dispensing systems of various materials in the global market.
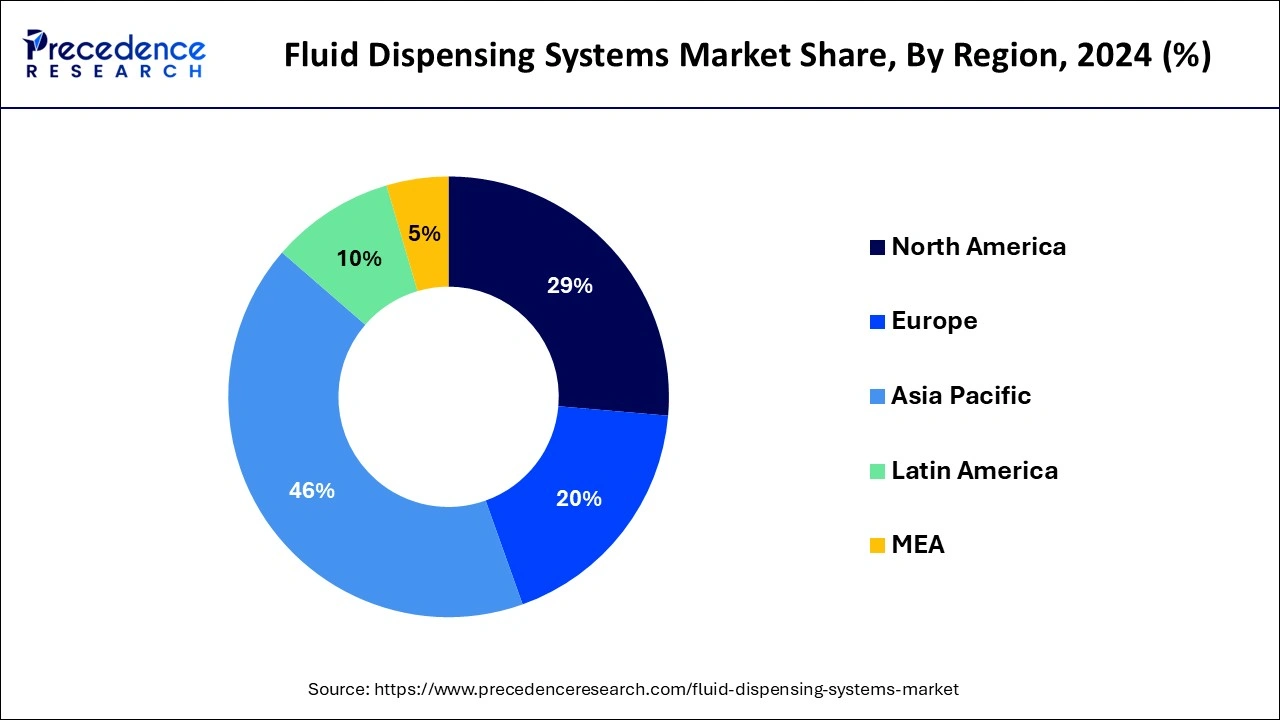
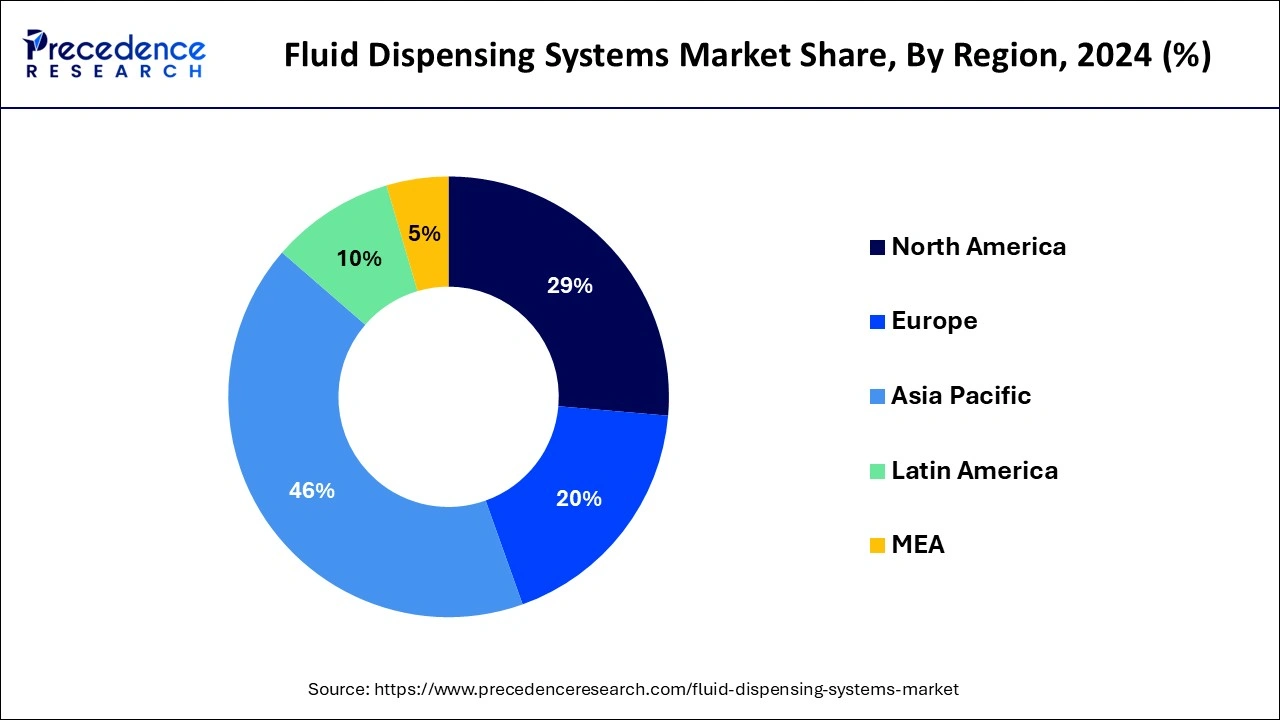
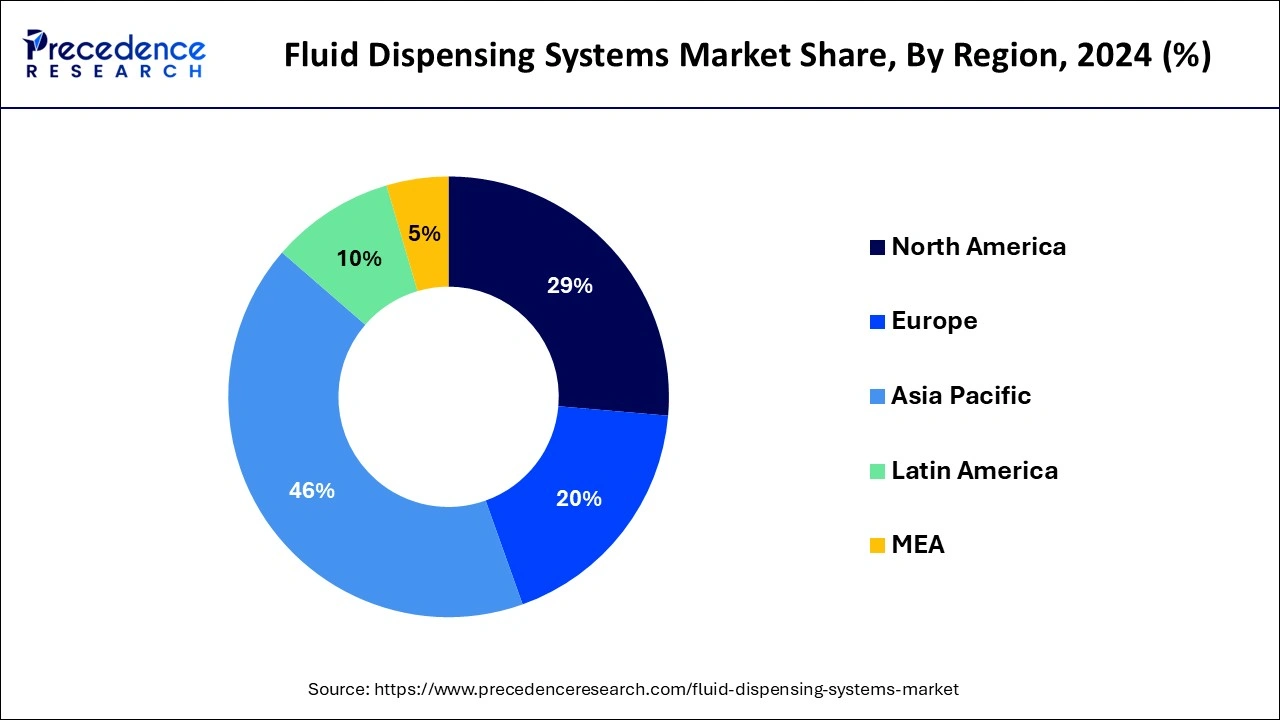
Though the Asia-Pacific region accounted for 46% of the global revenue for fluid dispensing equipment in 2024, the global demand is projected to increase for systems that are compatible with lubricant, solder paste, adhesives, and sealants. This is primarily driven by advancements in electronics and automotive manufacturing [1].
Benefits of precision fluid dispensing
The primary benefit of precision fluid dispensers is the ability to print high-resolution patterns and features quickly. They are designed to implement control methods to ensure high quality results are achieved. Many applications developed using these systems require consistent prints in high volume orders, so repeatability is key.
These systems can also be integrated into production lines to significantly reduce development time. They offer customizable features like interchangeable dispensers and programmable settings. Swappable dispensers allow users to disperse different types of material that would otherwise take longer to complete using manual processes, or even require a different tool altogether. A user can switch from a precision nozzle designed for depositing an adhesive ink, to a nozzle designed for spraying a coating in a matter of seconds.
Challenges with precision dispensing systems
One of the primary challenges that exists is finding the right system for your application. Unless you’re a material scientist, it is easy to become overwhelmed by technical specifications, even if you know your application’s requirements. There is no one-size-fits-all materials dispensing system on the market; each has its own advantages and disadvantages, most often tailored to specific applications. Even after settling on a system to purchase, it's extremely common to face difficulties with material reliability and flow.
Let’s say you have your system, the material, and a substrate. How do you tell the system where to deposit the fluid? How much should it deposit? When and where should it start and stop?
Balancing these aspects while also adjusting settings to manage consistency, material leakage, and quality results, is often no easy task — especially without an intuitive user interface.
NOVA: Voltera’s precision fluid dispensing system
NOVA is a precision materials dispensing system that dispenses screen-printable materials (1,000 to 1,000,000 cP) on flexible, stretchable, conformable, and biocompatible materials, as well as rigid substrates. It is ideal for:
- Flexible hybrid electronics R&D
- Novel materials research
- Precise material dispensing
- Seamless transition to mass production
In 2025, we released Plan, a software feature that enables multilayer printing and print job editing for NOVA, further improving user experience for printing multi-material and multilayer circuit designs.
Benefits of NOVA
- Achieve repeatable results with close-loop pressure feedback, temp-controlled dispensing, and an optimized algorithm for multilayer printing.
- Stack up to four layers of materials and visualize multilayer print sequences before execution.
- Experiment with a wide range of printable materials, from conductive inks and adhesives to solder paste on both flexible and rigid substrates.
- Change designs on the fly and iterate without screens or stencils, eliminating delays and reducing costs while prototyping in-house.
- …and more
For technical specifications of NOVA, click here.
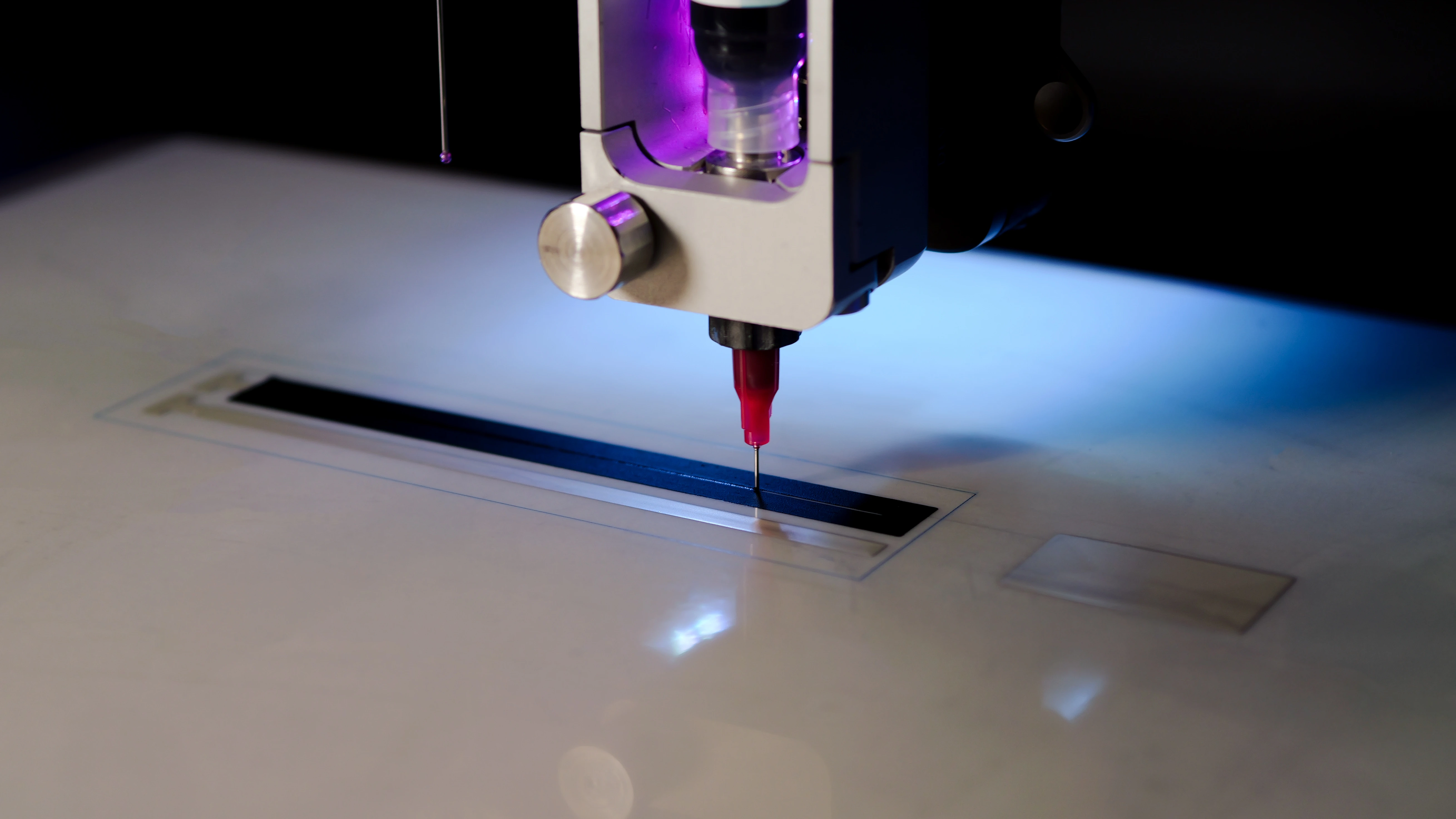
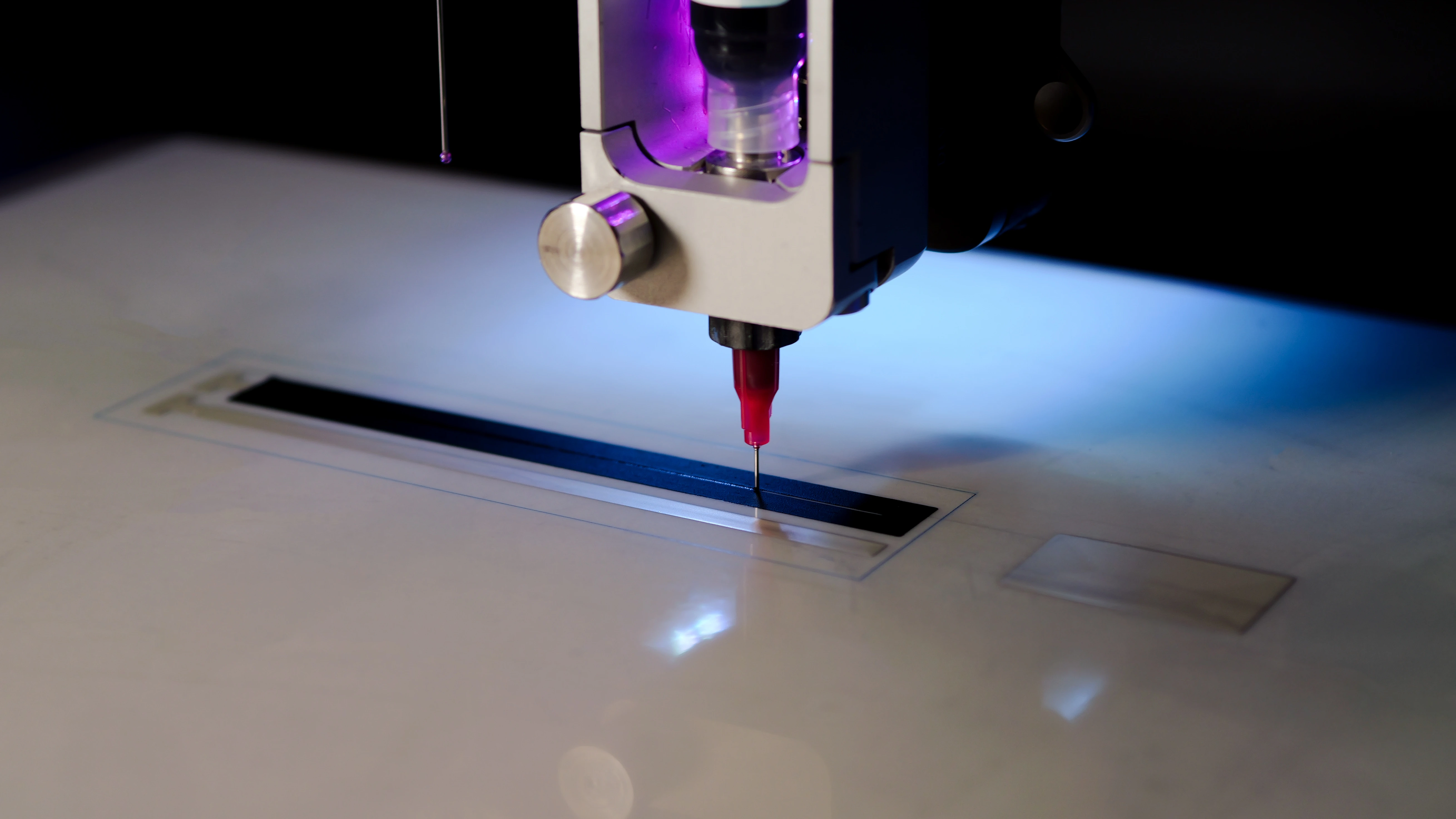
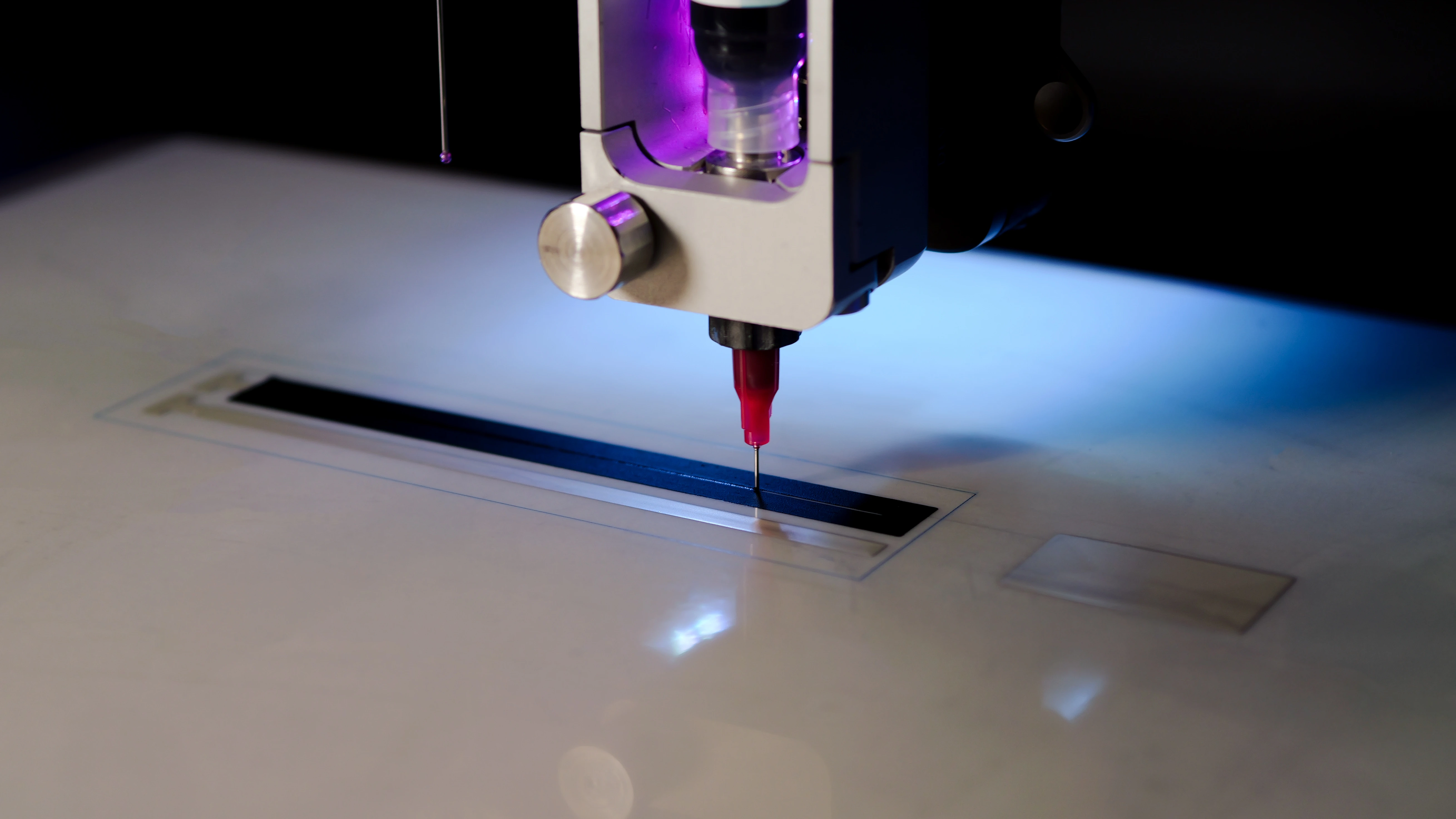
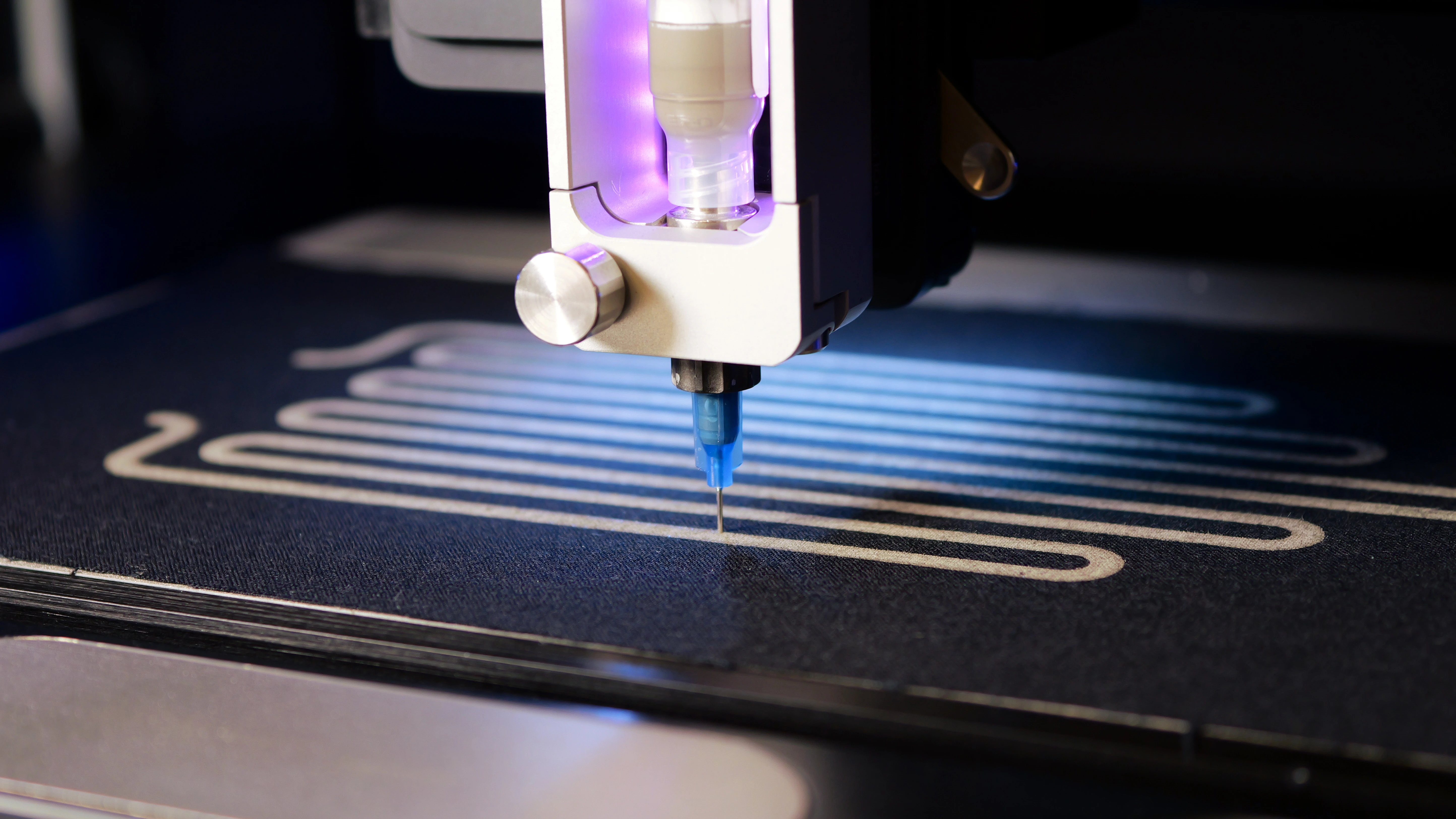
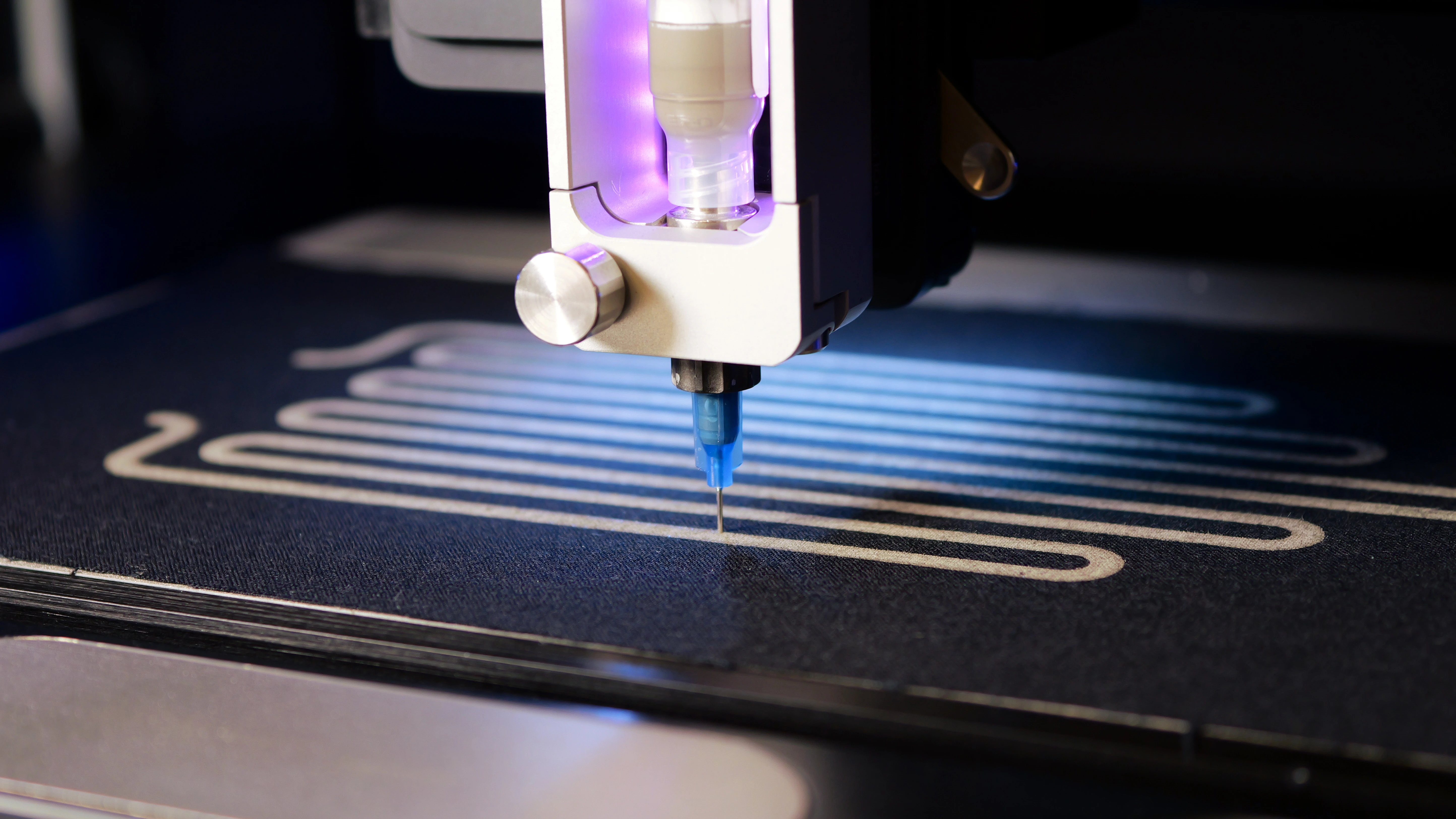
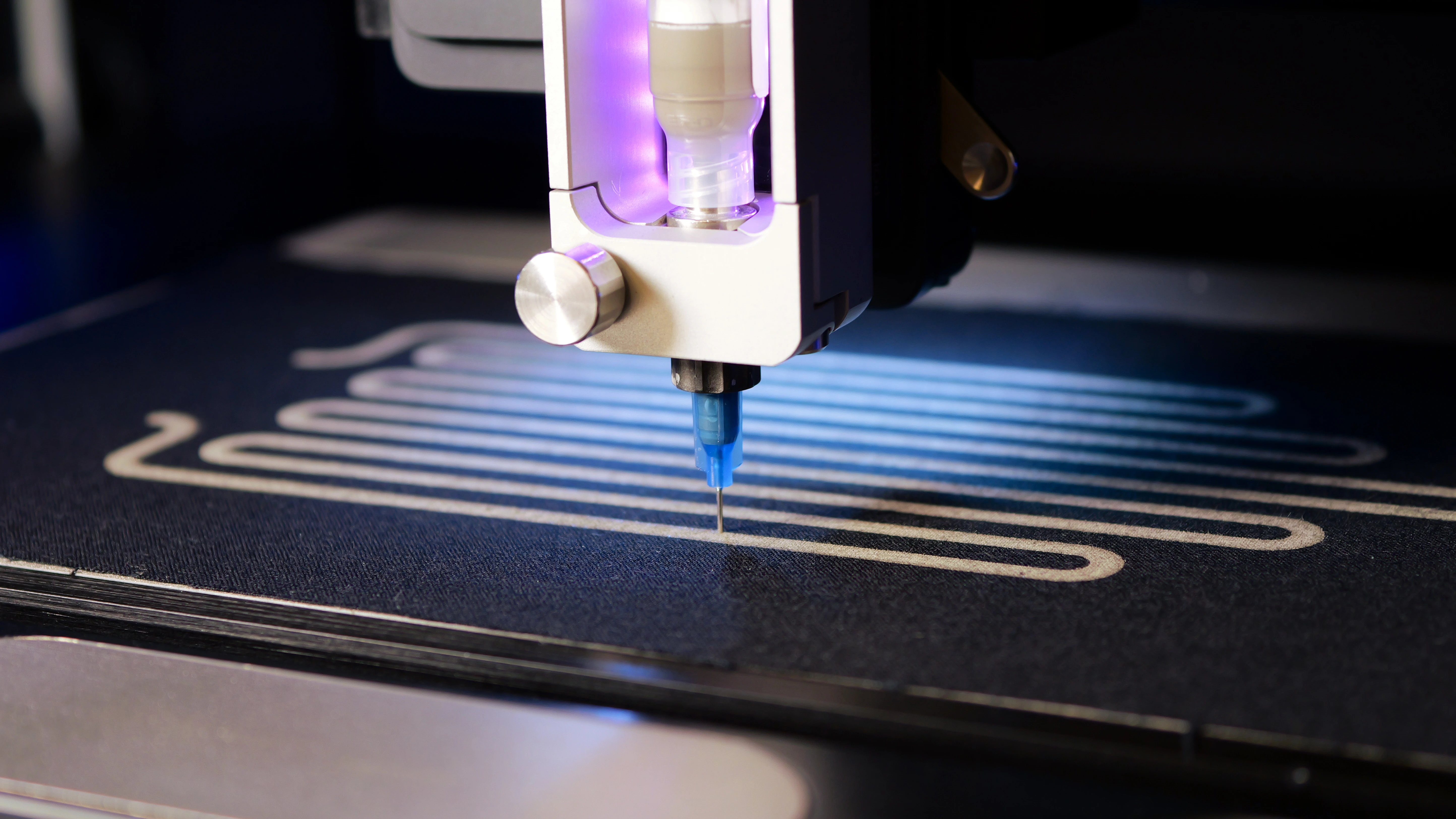
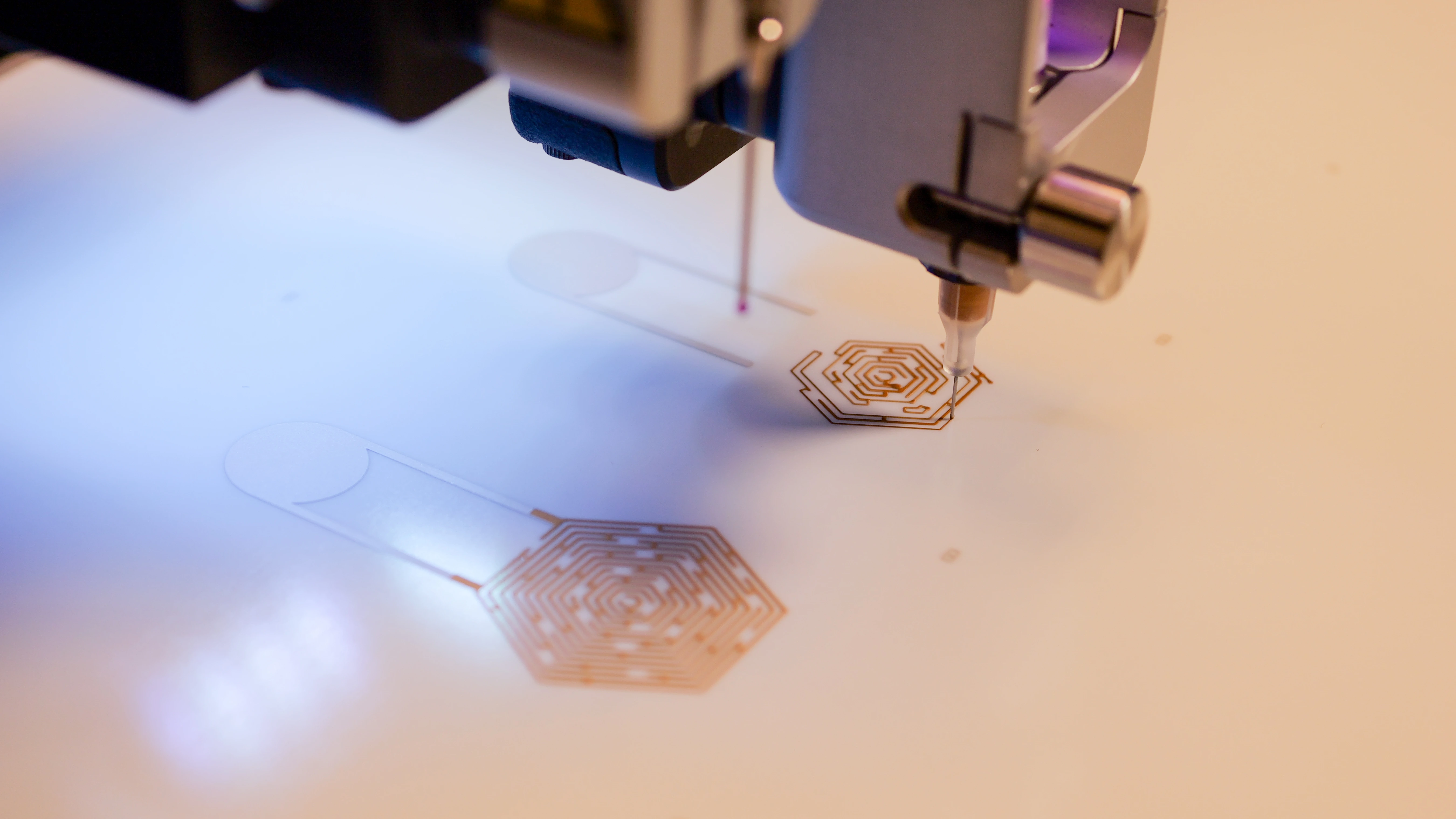
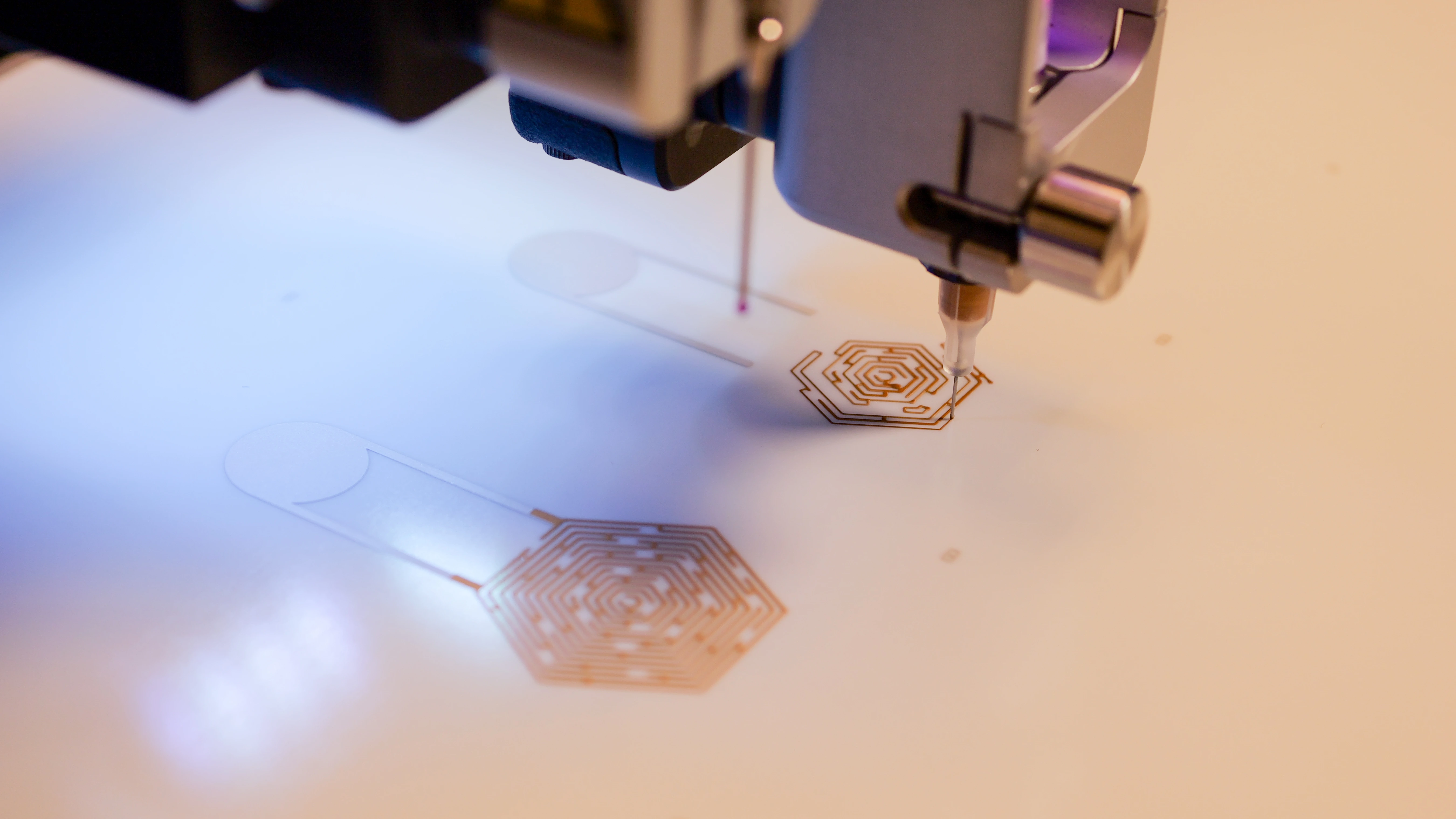
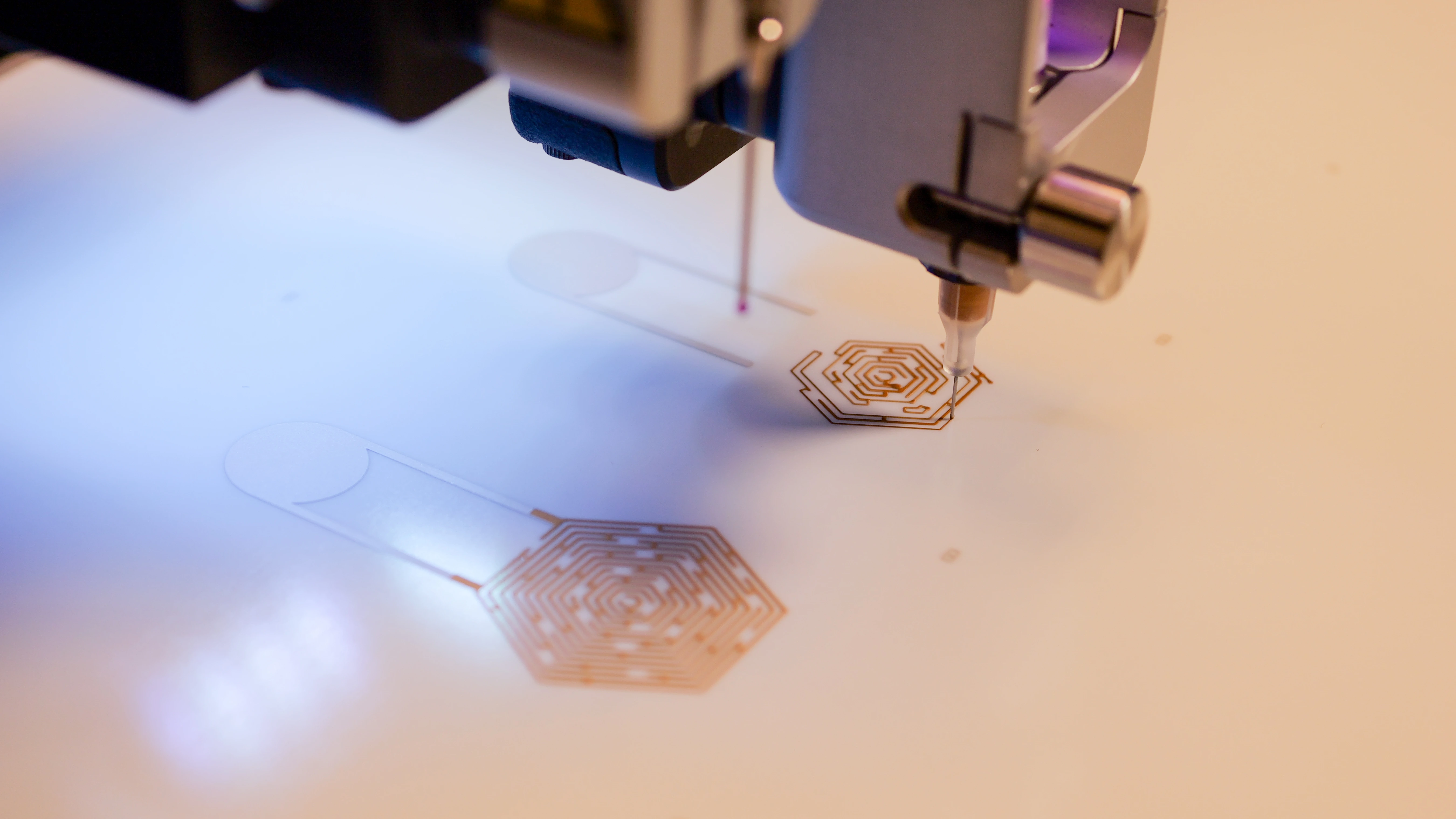
Conclusion
As additive manufacturing continues to revolutionize research outcomes and product development, innovators are searching for the right solution to meet their goals. They’re looking to accelerate development timelines and find cost effective methods for achieving reliable, high quality results.
If you would like to see if NOVA is a fit for your application, book a meeting with one of our application specialists.
References
[1] Precedent Research, Fluid Dispensing Systems Market Size, Share, and Trends 2025 to 2034, 2025.
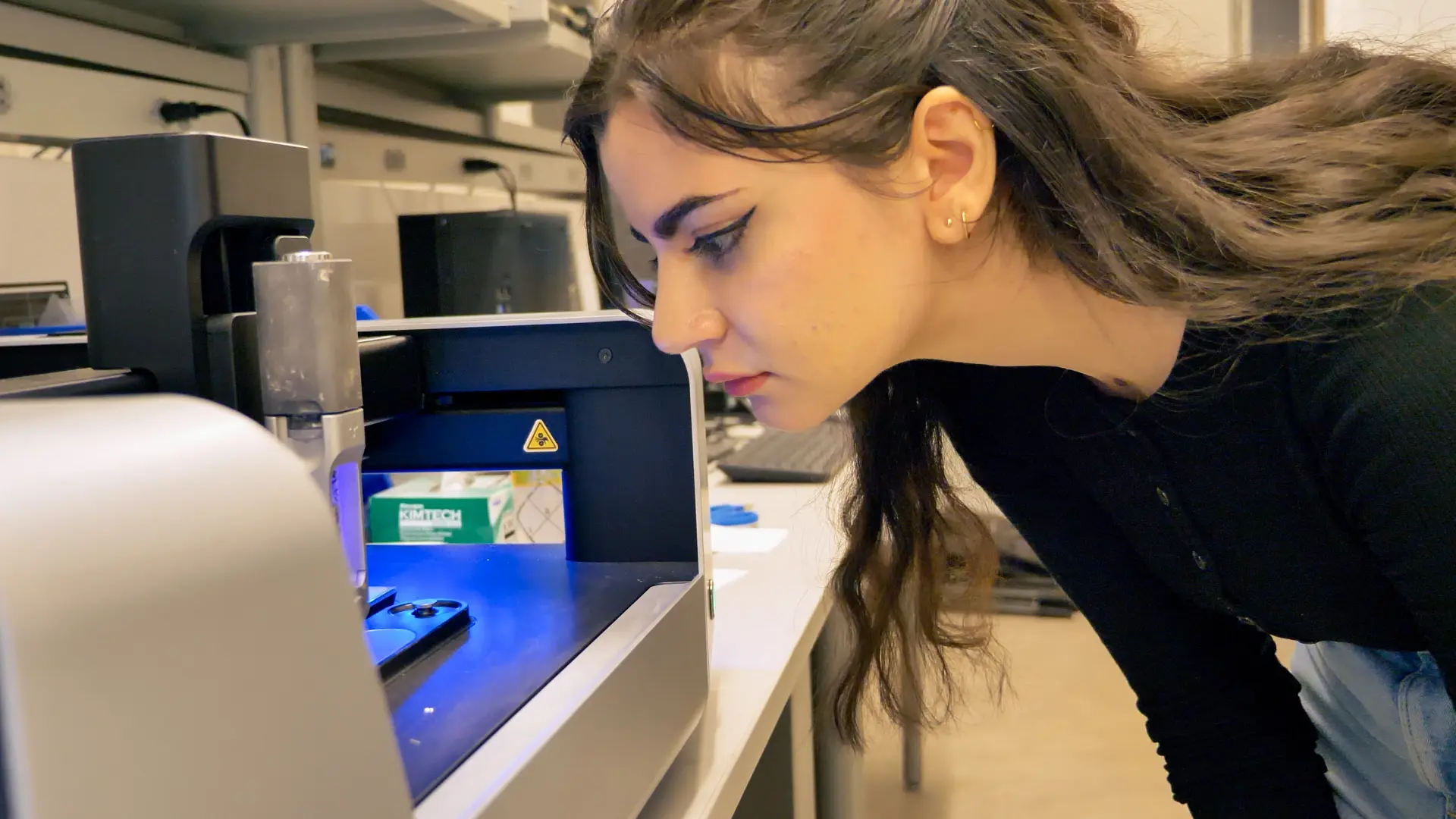
Check out our Customer Stories
Take a closer look at what our customers are doing in the industry.
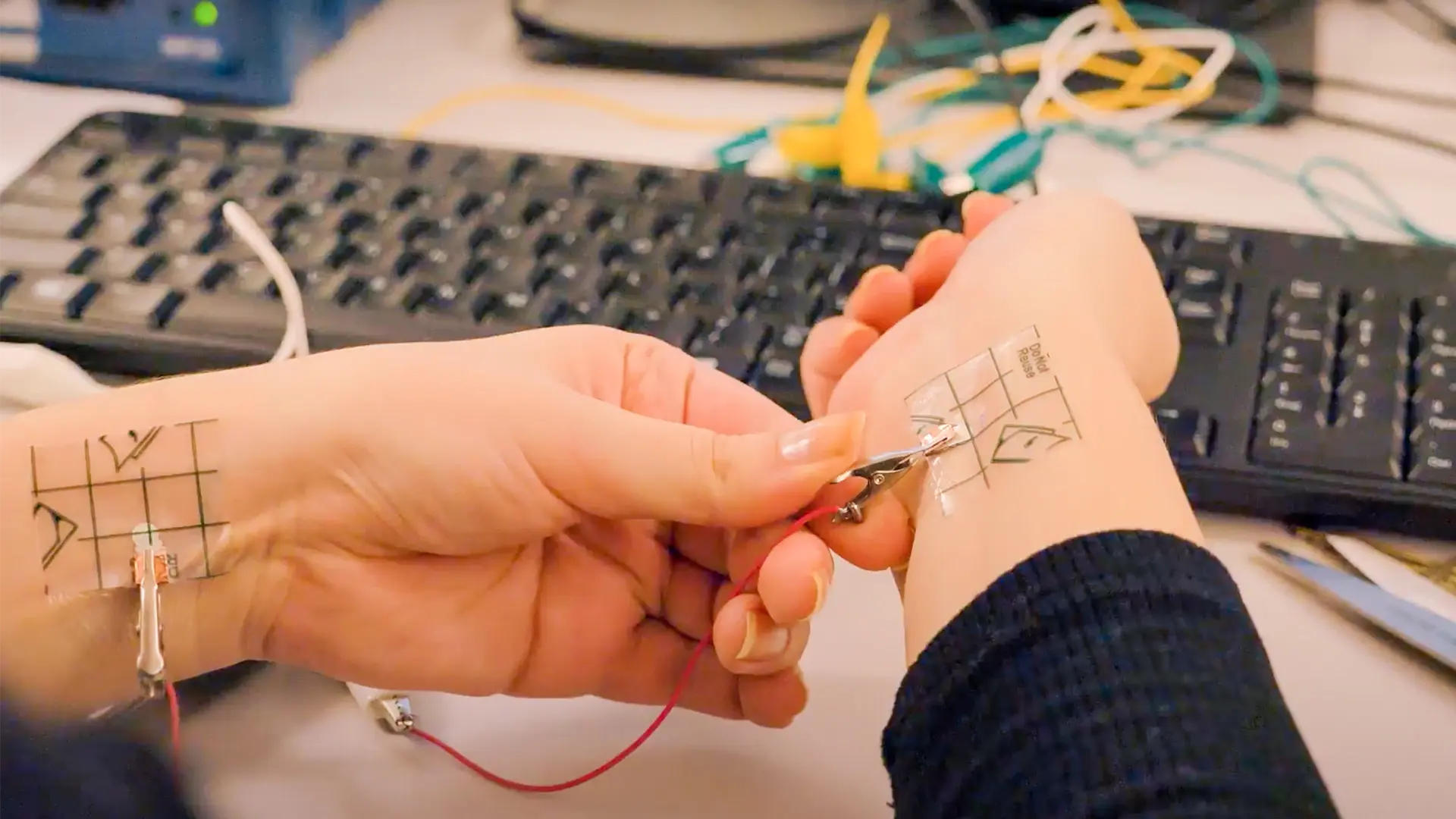