Printing Self-Heating Carbon Fiber Composites for UAV Wings with V-One
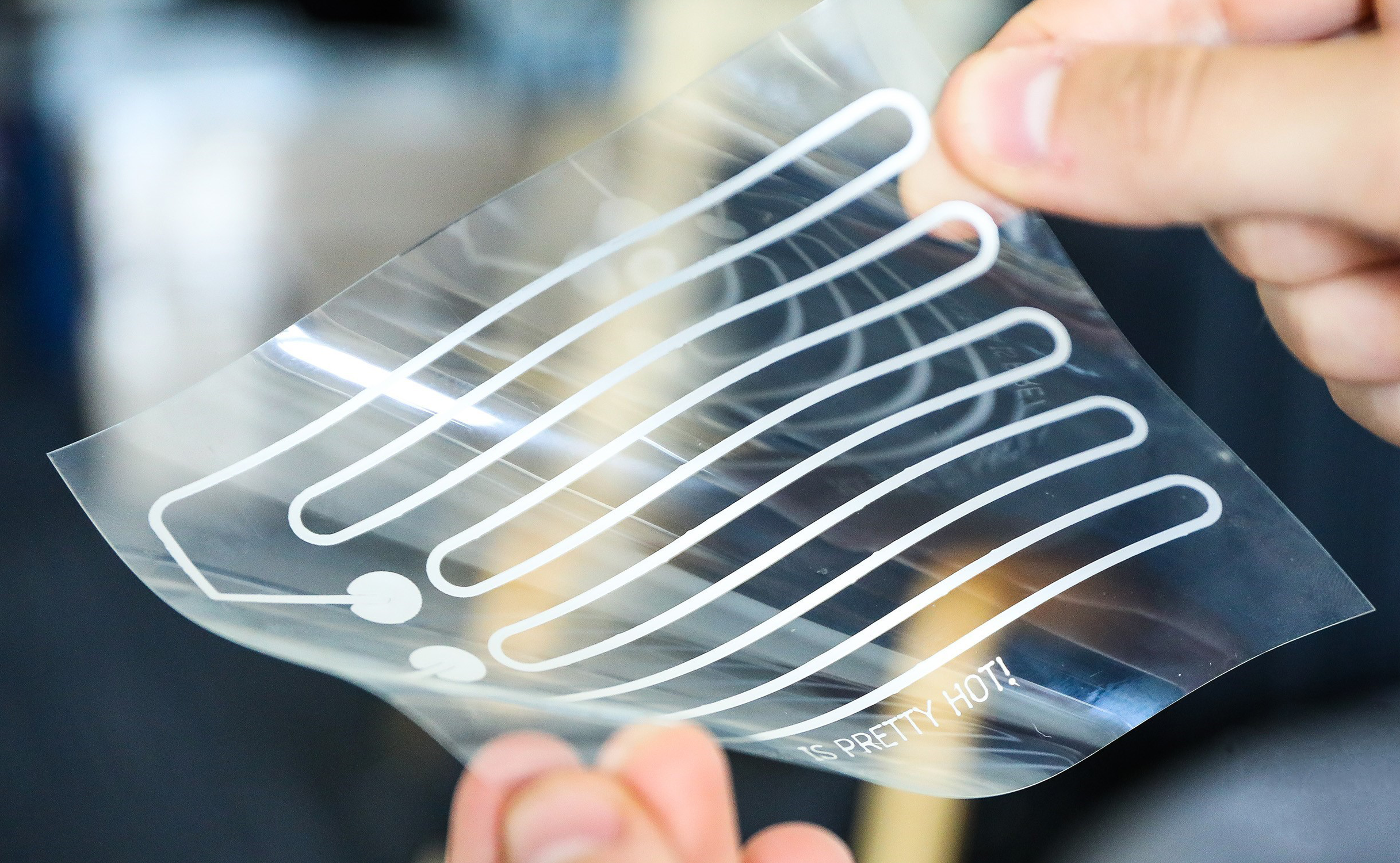
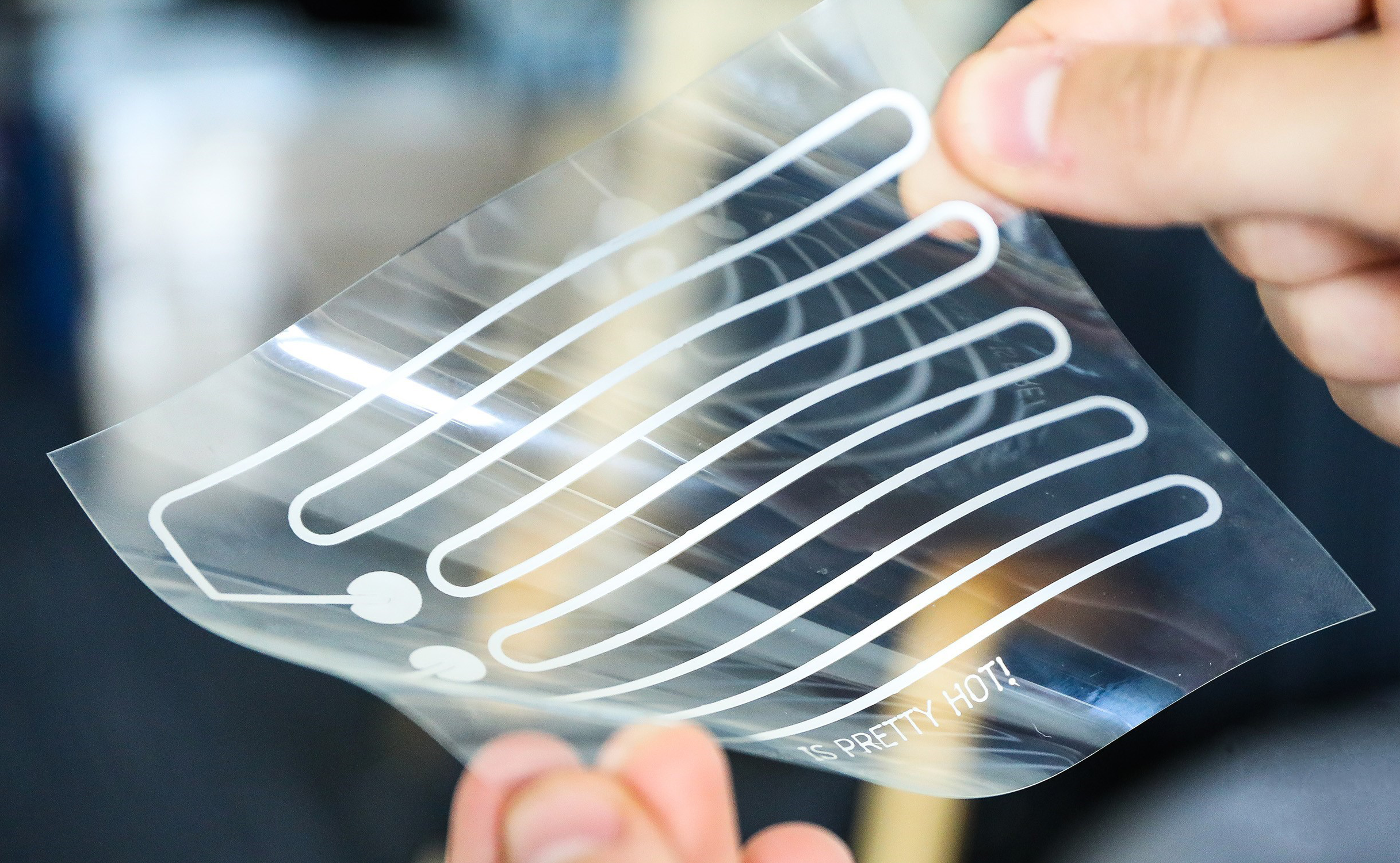
Ice buildup on UAV wings
Today we’re going to dive into how Mohamad K. Idris and his colleagues at York University developed self-heating carbon fiber composites to be used on Unmanned Aerial Vehicles (UAVs).
Idris is a PhD student in the Electrical Engineering and Computer Science (EECS) department at York University. He received his MASc from York University and his BSc from Istanbul Şehir University, Turkey. His research interests are additive manufacturing of carbon fiber-based electronic devices, and the fabrication and compact modeling of organic thin-film transistors (OTFTs). He is currently working in the E-AM Lab at York University under the supervision of Dr. Gerd Grau.
The problem that Idris et al. addressed in this project is the accretion of ice on UAV wings, which can have a major impact on flight in the rapidly-growing UAV industry. Ice accumulation on aircraft wings is by no means a new problem: commercial aircraft have been confronting this for decades. But given a number of factors, including the small size of the craft, the problem is exacerbated and the available solutions limited for UAVs. By using printed electronics techniques, Idris et al. were able to produce an extremely lightweight and effective solution for deicing the wings of UAV aircraft, and preventing the accretion of ice in-flight.
Printing silver electrodes on carbon fiber weaves
The team printed silver electrodes on carbon fiber using Creative Materials’ 120-07 ink. The carbon fiber was later infused with epoxy to manipulate it into a shape that would integrate into the UAVs’ wings. By experimenting with different carbon fiber weaves and modifying the print settings, the group was able to find a combination of settings and materials that gave them optimal results in a repeatable and scalable fashion.
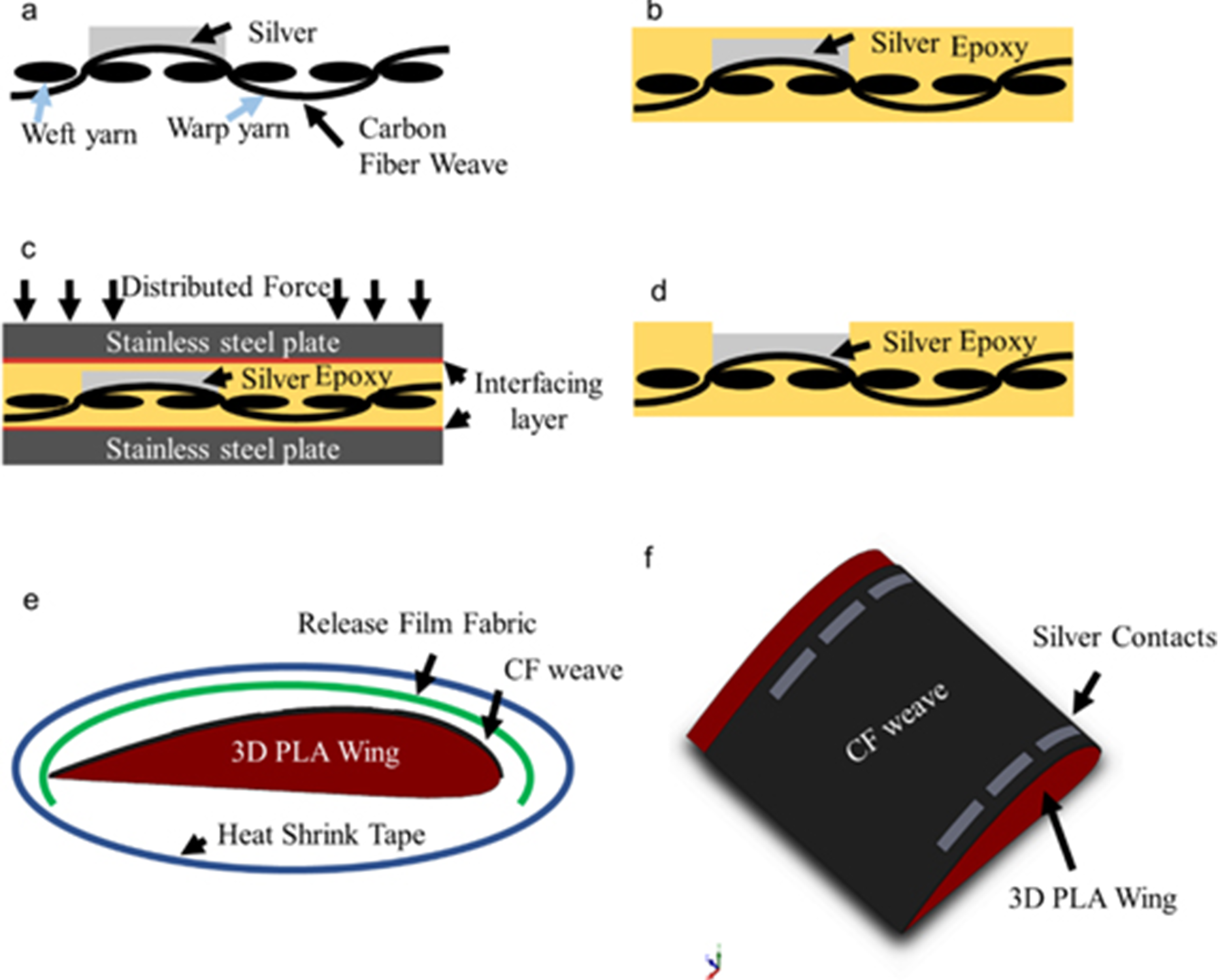
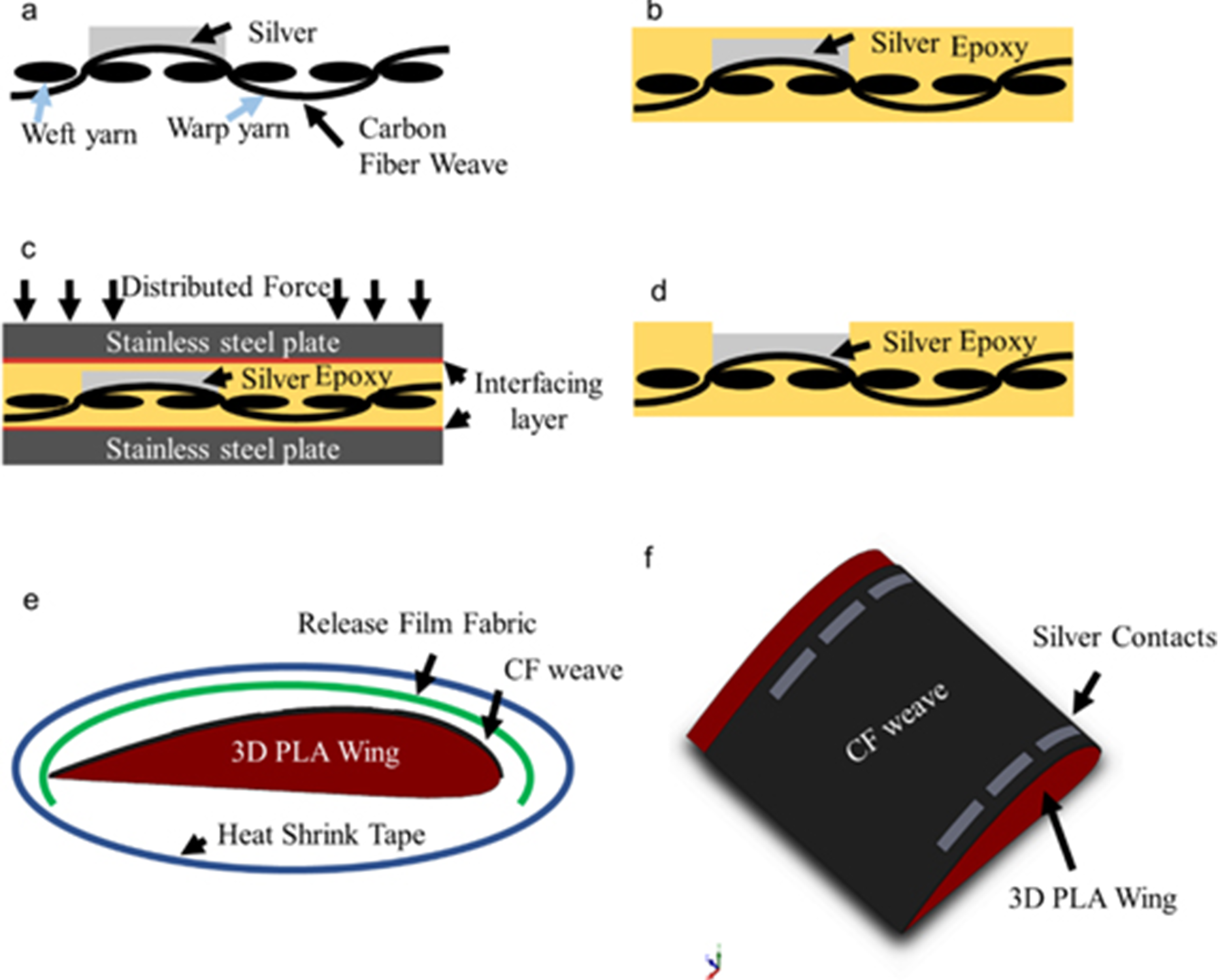
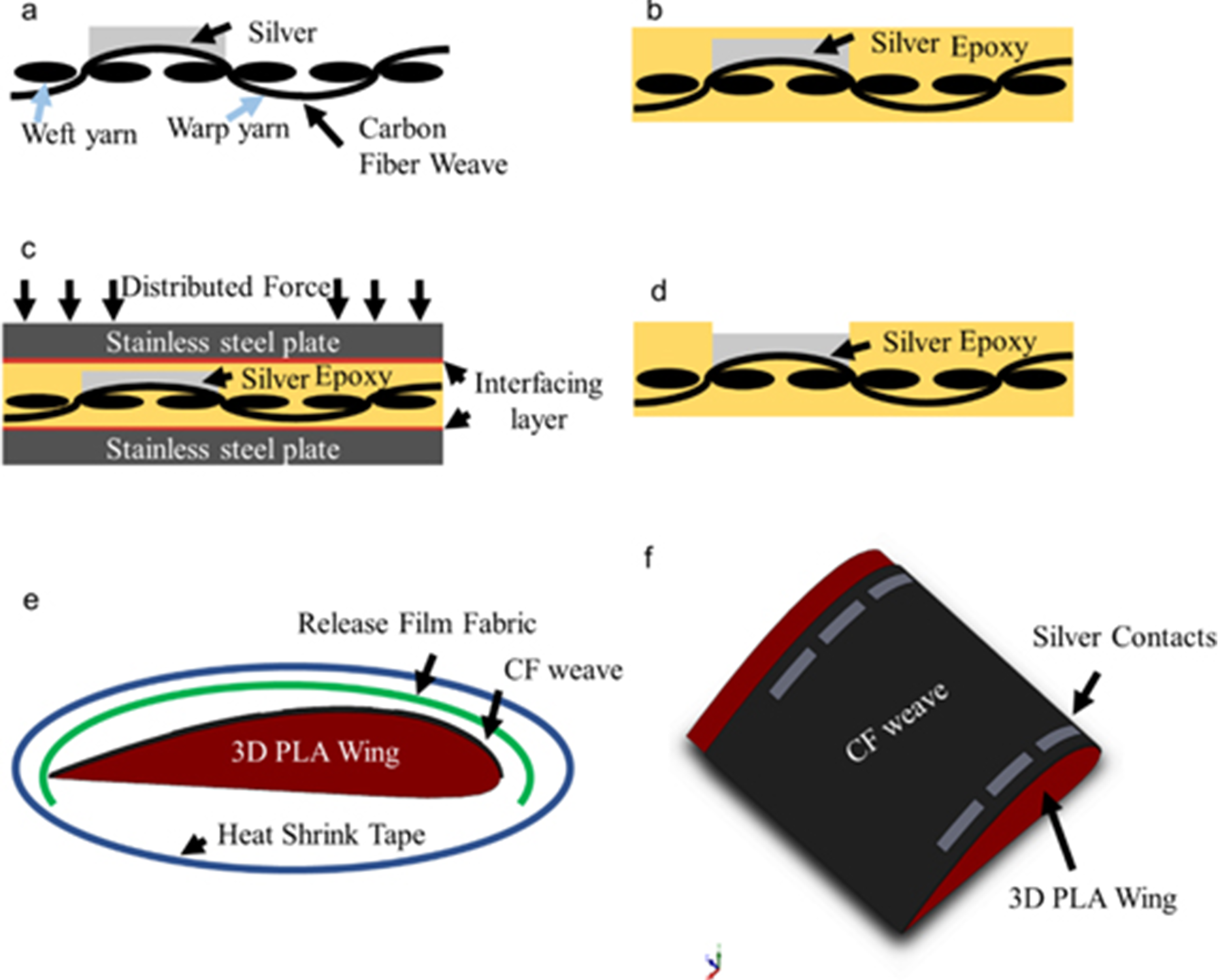
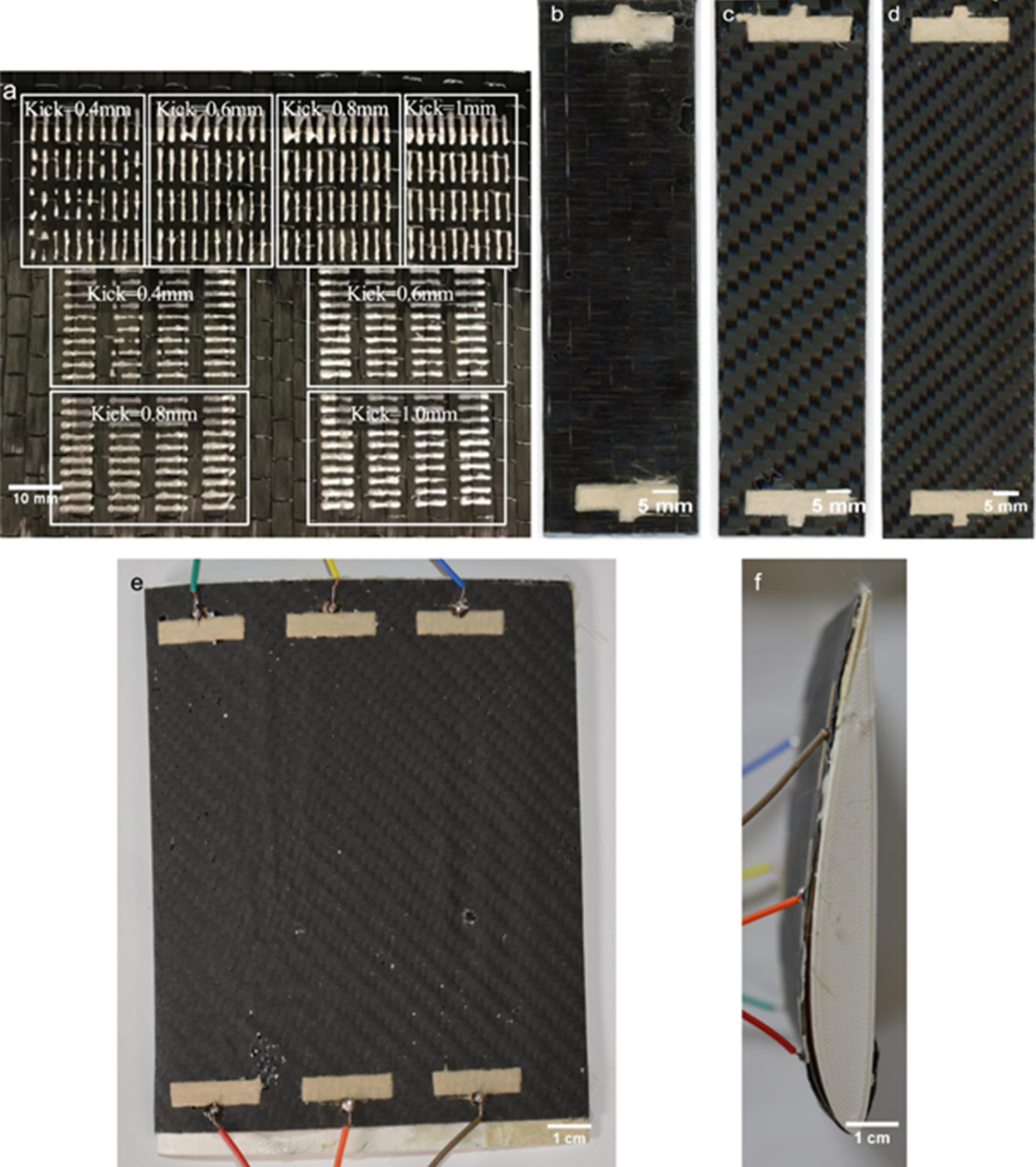
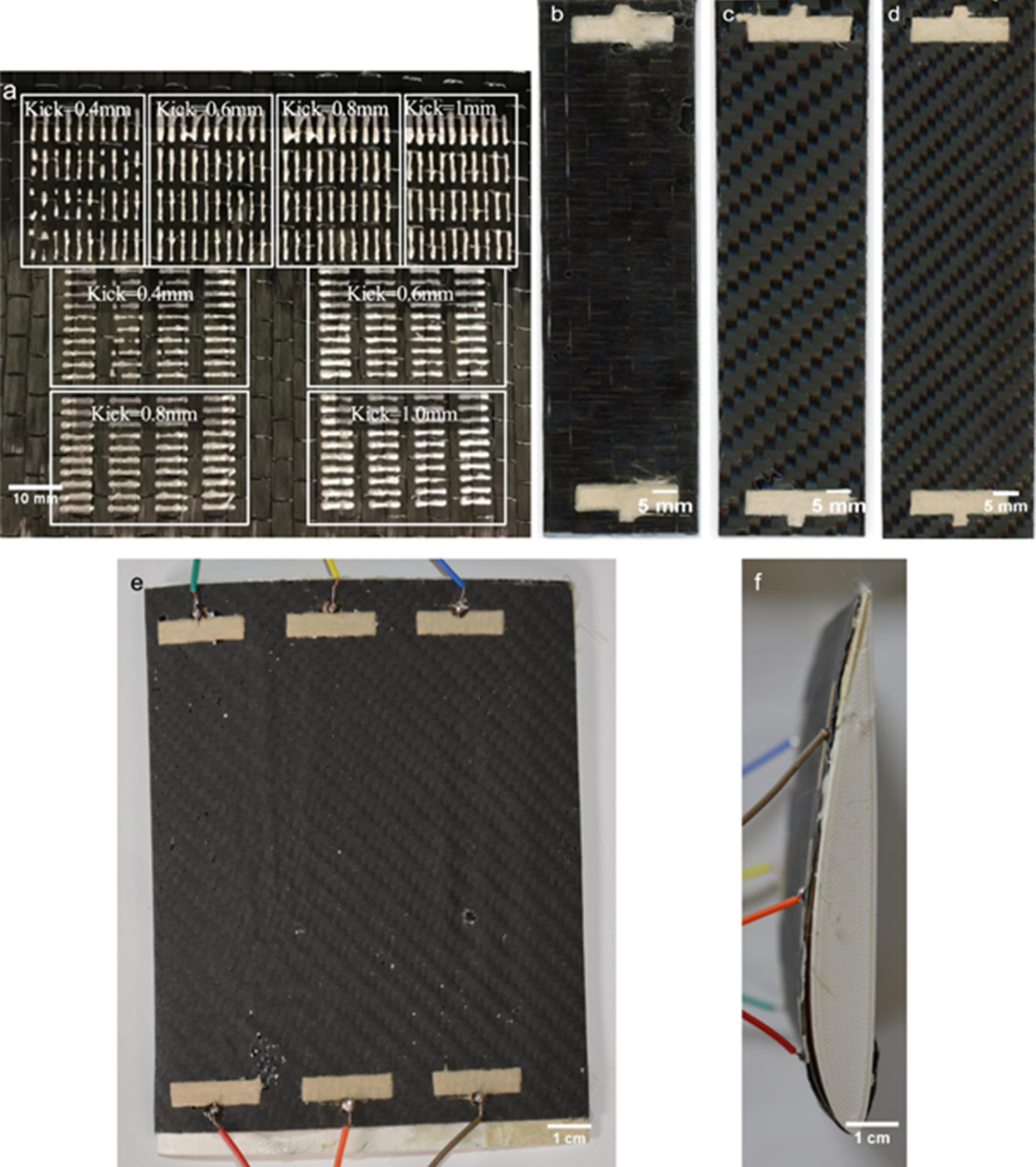
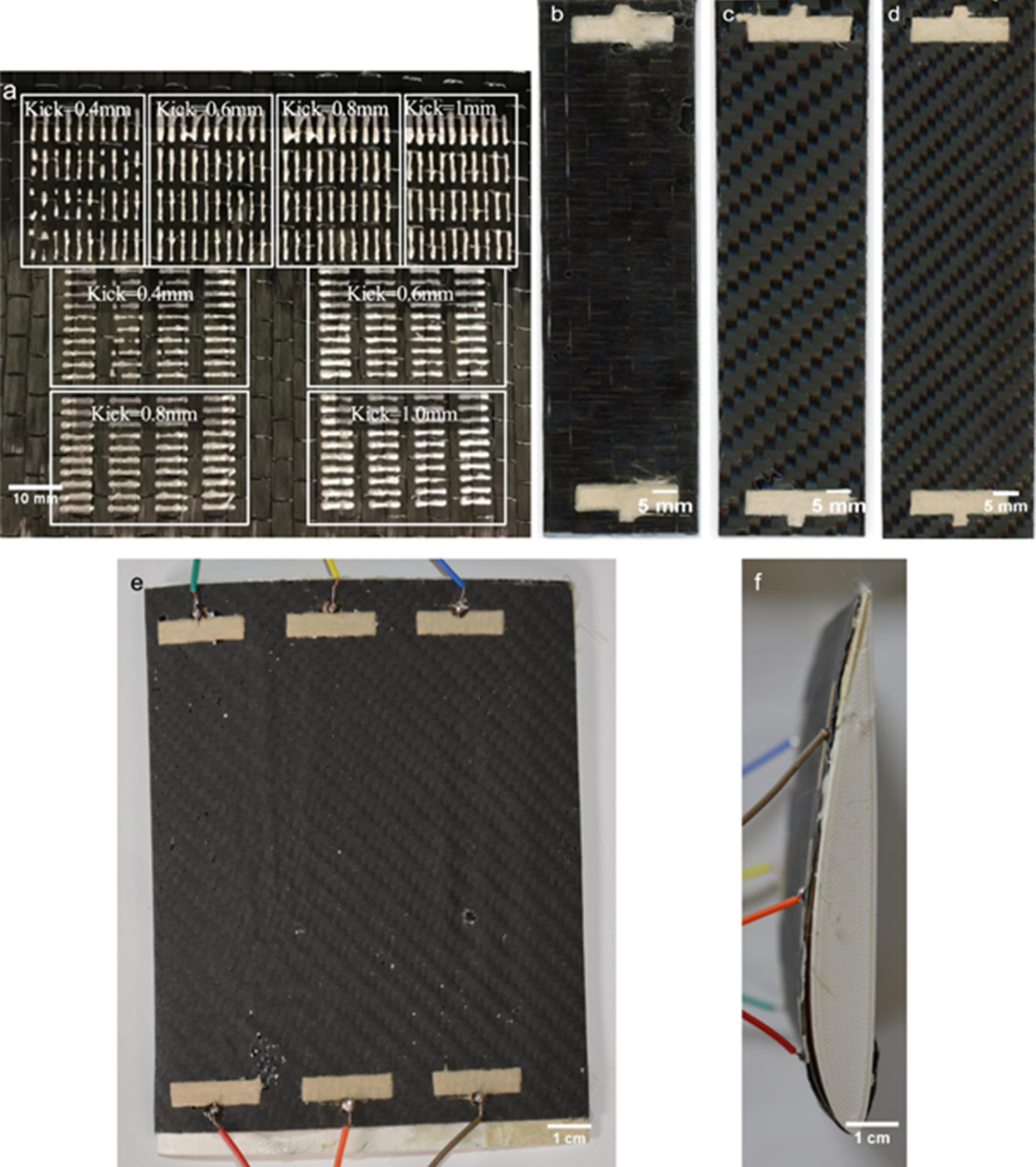
How V-One is helping additive electronics research
We interviewed Mohamad and asked him about his interest in additive electronics as well as how the V-One is helping him in his research.
Getting into the field
Q: What interests you about your field/how did you get into it?
I discovered electronics additive manufacturing in graduate school. It was very interesting to work in a lab and actually build and test my electronic devices firsthand compared to the common simulation design-based electronics engineering.
Additive electronics manufacturing
Q: What interests you about additive manufacturing?
I find additive manufacturing very interesting because it makes prototyping and testing easy and feasible. Which, as a result, helps me understand the behaviour of the complex carbon fiber weaves that I use for my research. Non-additive manufacturing techniques require high temperatures and expensive material. If I had to create a new mask every time I wanted to tweak my design or wait for a manufacturer to make my devices and ship them to me, I would probably be stuck on my simulations for a long while.
Researching with the V-One
Q: How is the V-One helping you in your research?
My research concentrates on designing and manufacturing carbon fiber weave large-area electronic devices. Electrically connecting to the carbon fiber weaves in strategic locations enables the device functionality and controls its efficiency. The V-One helped me design and prototype several devices by printing connections of various shapes, sizes, and locations on the carbon fiber weaves.
Prototyping with the V-One
Q: How did the V-One help accelerate this specific project?
Printing on textiles is considered challenging. In my opinion, the printing methods most compatible with textiles are screen printing and dispense printing. However, when it comes to designing, prototyping, and creating several masks, screen printing is expensive and takes a long time. The V-One does not require masks. It was user friendly and very easy to use. It allowed me to tweak the printing parameters to match the textile material that I was using, thus accelerating the design and manufacturing of my electronic device. It also made the process cheaper, faster, and more dynamic.
For more from Voltera users pushing the printer in bold new directions, check out our other customer stories!
Note: York University has since purchased NOVA for improved user experience in prototyping flexible, stretchable, and biocompatible electronics.
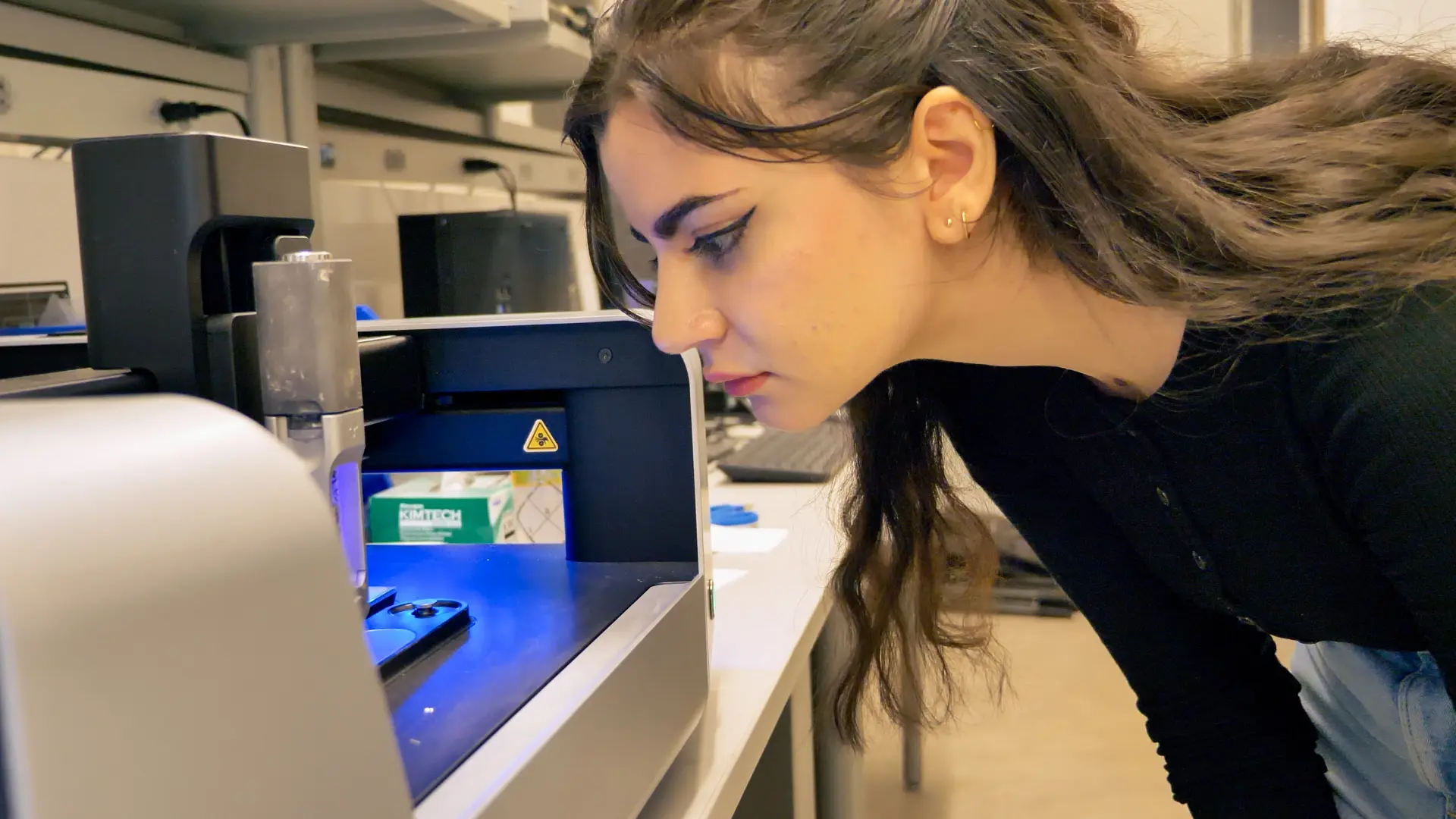
Check out our Customer Stories
Take a closer look at what our customers are doing in the industry.
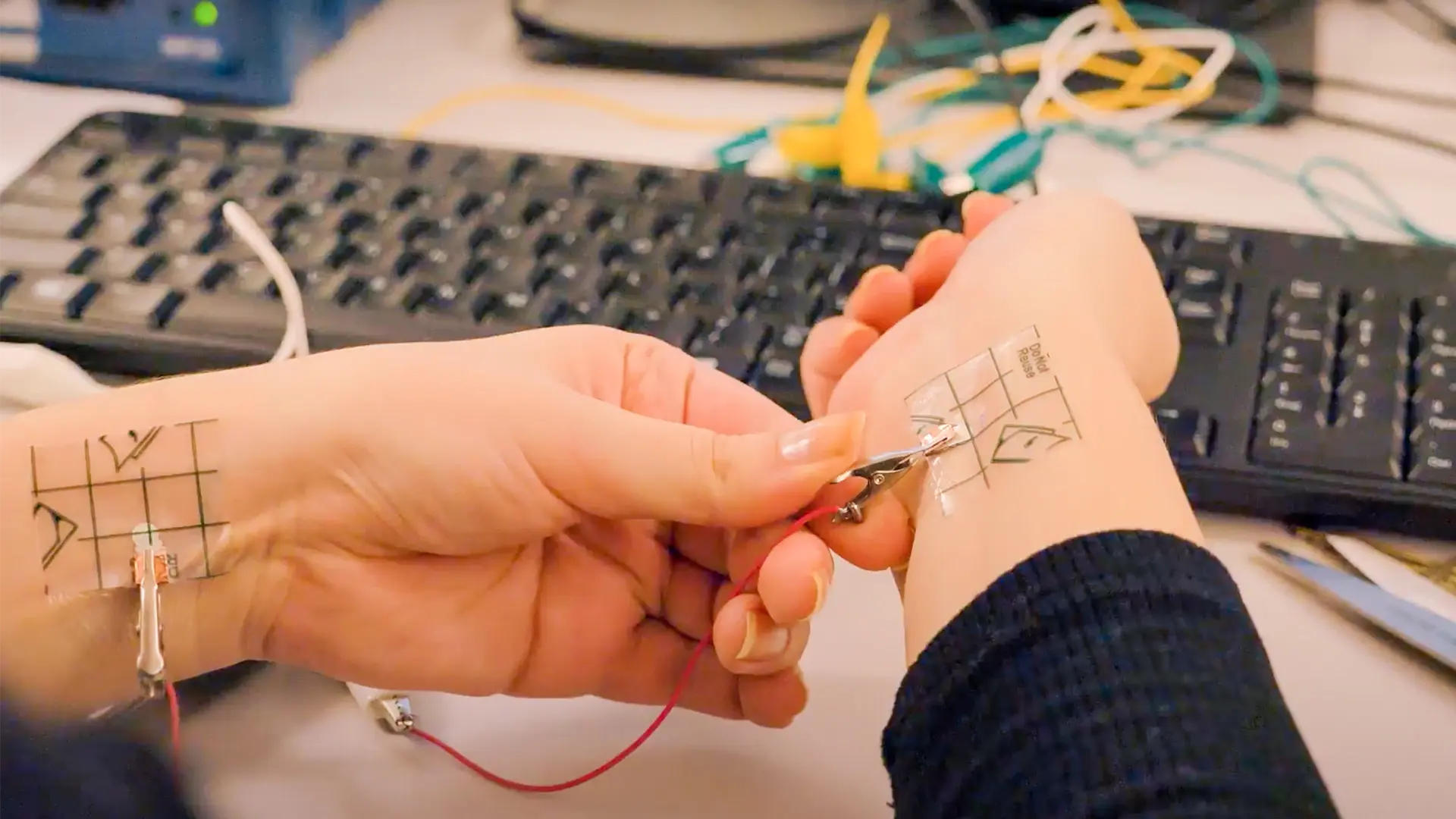