The Role of Conductive Inks in Additive Electronics Manufacturing
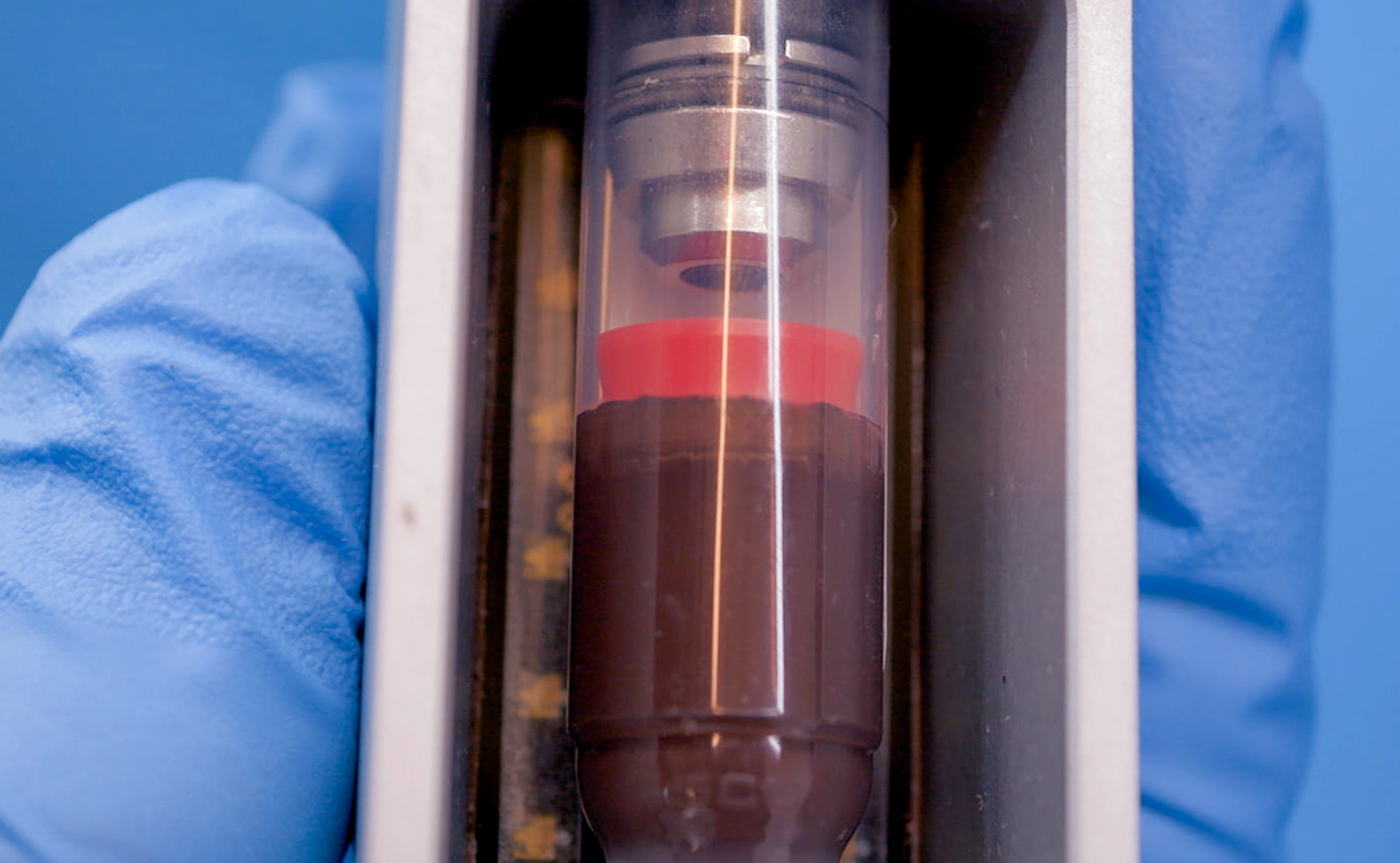
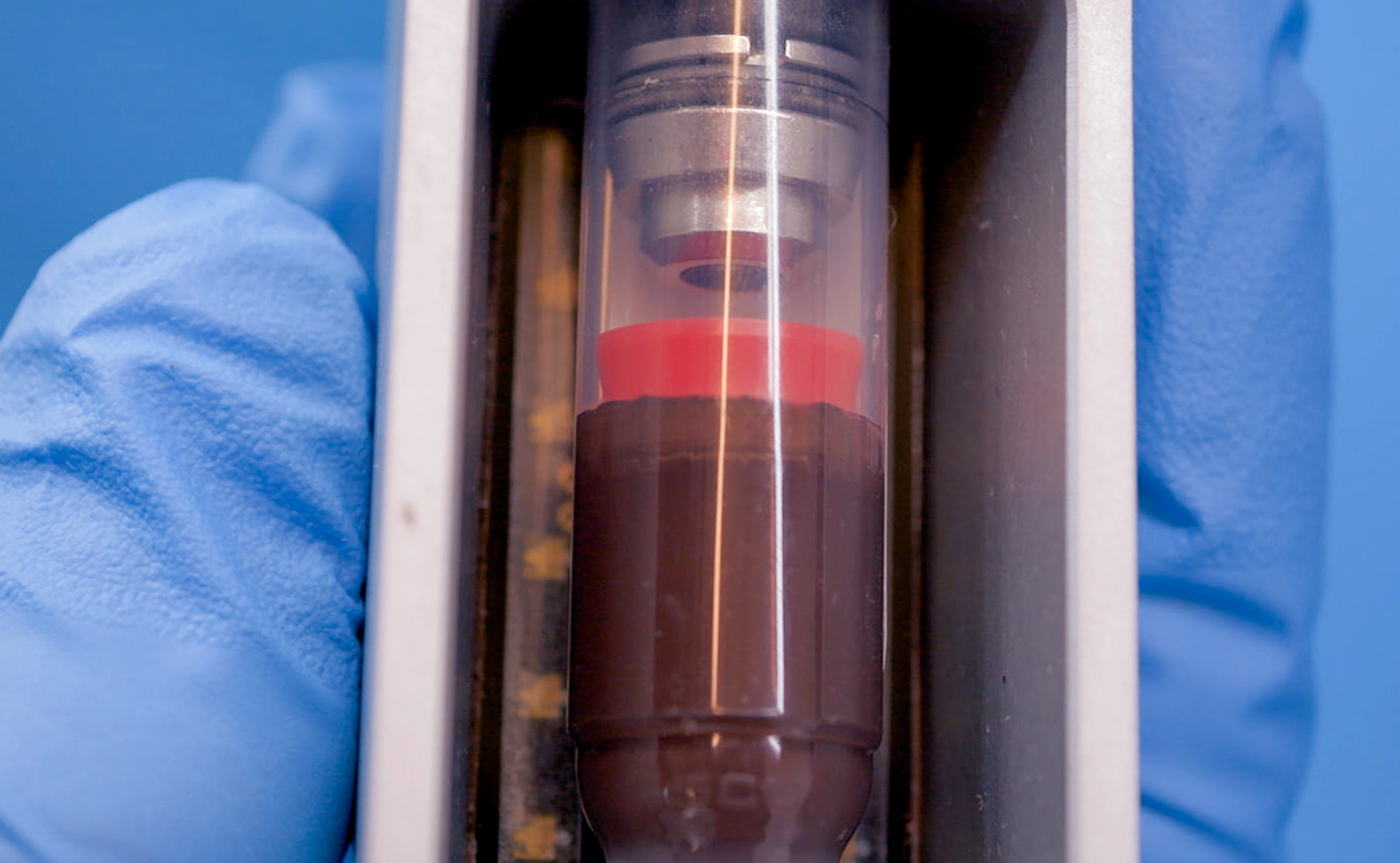
In a future characterized by flexibility, stretchability, sustainability, and affordability, conductive inks serve as tools to foster electronics innovation. In this blog, we will explore the role of conductive inks in today’s printed electronics landscape.
What are conductive inks?
Conductive inks are printable materials that are capable of conducting electricity. These inks contain conductive particles or flakes such as silver, copper, and carbon, and enable electrical conduction. Most inks aren’t conductive right from the beginning — they need to be processed to evaporate the solvents which strengthens the connection between the metal particles. After printing, they are cured in different ways to render them electrically conductive. Typically, the main curing process we use on V-One for low temperature inks is thermal curing. This process applies heat to initiate polymerization, solidifying the ink and changing the volume of the traces. However, there are alternative methods for processing conductive inks, such as ultraviolet (UV) curing. UV curing exposes the uncured ink to UV light, converting the monomers to polymers which hardens the liquid.
To learn more about what conductive inks are made of, see What is Printed Electronics? Conductive Inks.
Advantages of conductive inks in additive manufacturing:
The increasing demand for flexible and stretchable electronic devices requires conductive materials that can satisfy the characteristics of the devices. Traditionally, subtractive manufacturing processes like chemical etching, require an extensive production process that is costly, wastes material, and is environmentally harmful. Conversely, conductive inks are used in additive manufacturing processes — providing an extensive list of benefits to users:
Testing and design acceleration
Because conductive inks are additive in nature:
- They accelerate the design and iteration stage for developing electronics.
- They avoid multi-step procedures related to chemically stripping materials (keep reading — there’s more on this process below.
Instead, they utilize a more streamlined process of printing only what’s needed where it is needed. This approach eliminates material waste and enables users to develop and test their prototypes faster.
Material versatility of conductive inks
Conductive inks are comprised of a wide variety of materials, providing users with a diverse range of application compatibility. With various resistance thresholds and temperature ranges, conductive inks allow for compatibility with flexible and stretchable applications, on a wide variety of films and substrates. Here are a few examples of the inks and their potential applications:
- Silver conductive inks are easy to print and offer excellent conductivity and low resistance, making them ideal for applications requiring high flexibility. Typical applications where silver conductive inks are used include aerospace electronics, alternative energy solutions, biosensors, RFID tags, and automotive sensors.
- Silver/silver chloride (Ag/AgCl) inks are an environmentally friendly option, commonly used in biomedical electronics. Their smooth finish and ability to achieve different resistance and sensitivity levels by adjusting their ratio, makes them specifically suitable for on or in-body applications like health monitoring patches and sensors.
- Carbon inks offer high thermal stability at a lower cost compared to silver conductive inks. Their chemical inertness makes carbon inks suitable for printing resistors and conductors on non-conductive materials such as plastics, ceramics, and paper. Carbon-based inks are useful for applications like windshield defrosters, resistors, computer keyboards, and capacitive sensors where conductivity and stability are required.
- Gold and platinum conductive inks offer very high conductivity and longevity, and are used in applications where the higher conductivity can justify the high price. These conductive inks durability can be attributed to their resistance to corrosion and oxidation. Some common applications where gold and platinum conductive inks are used include photovoltaics and thin film transistors.
Sustainability and material waste
Subtractively manufactured electronics involves chemical etching, a process that subjects material to chemicals to remove excess material until the final form is obtained. This process results in significant material waste and also exposes handlers to toxic chemicals such as sodium hydroxide or ferric chloride.
A much safer option is printing conductive inks additively onto a substrate or film in the desired pattern — resulting in no exposure to toxic chemicals or creation of material waste.
Applications of conductive inks
There are numerous applications for conductive inks. We’ve highlighted a few below that been developed on our materials dispensing systems, NOVA and V-One:
Remote controlled robotic hand with strain gauges
This project involved designing a remote controlled robotic hand, printed using a highly conductive stretchable silver ink from Celanese. The process of building a remote controlled robotic hand involved designing strain gauges that could stretch while maintaining conductivity and exhibiting a measurable change in resistance. Using this stretchable conductive ink opens the door for designing strain gauges on nearly any flexible material.
Insole pressure sensor
This application saw the full design and build of an insole with a force sensitive resistor capable of detecting pressure and weight distribution in a shoe. Using the same stretchable silver conductive ink as the robotic glove above, traces were printed onto a sheet of thermoplastic polyurethane (TPU) which then comes into contact with a carbon sheet under pressure — allowing for resistance to increase in various regions of the print.
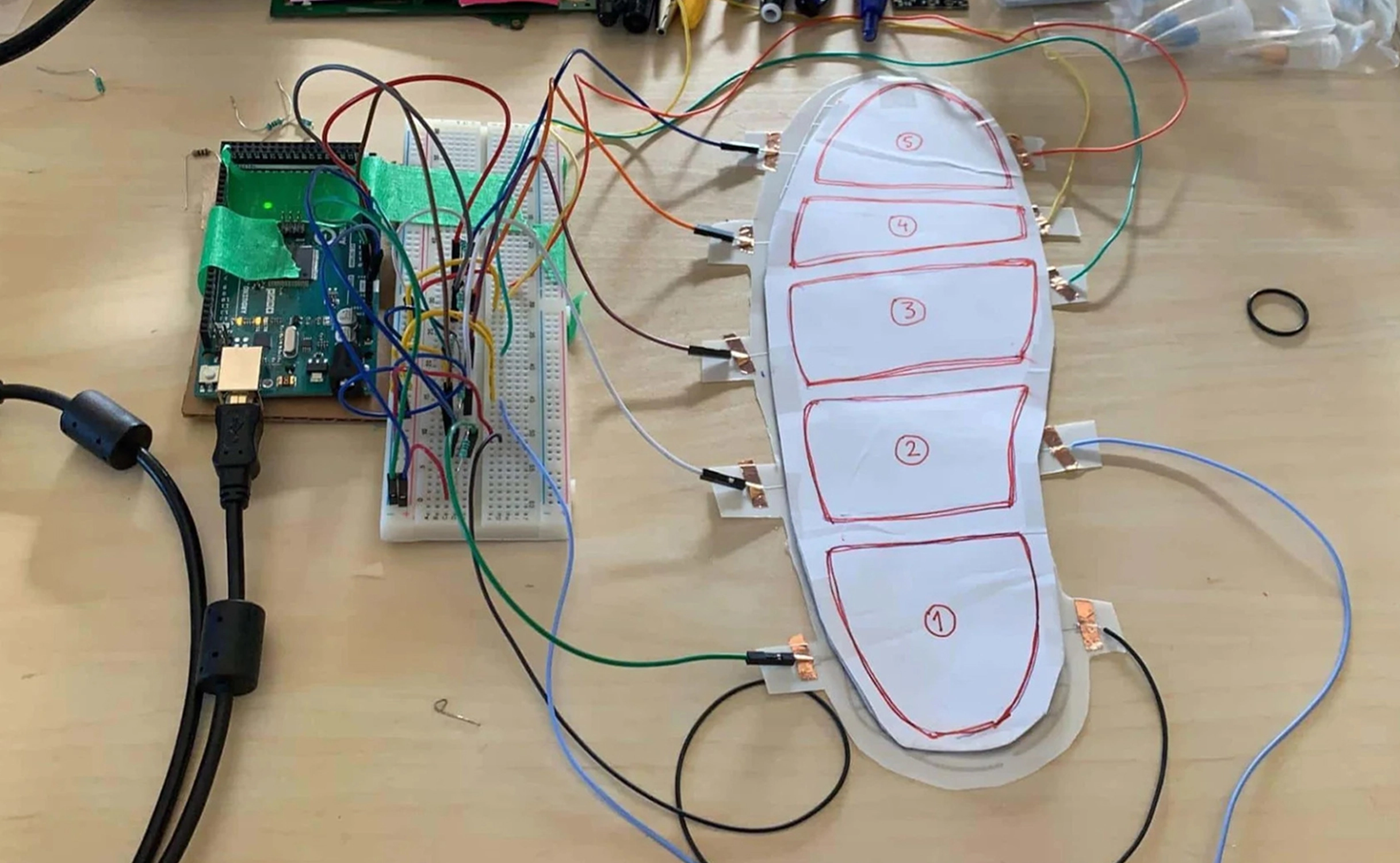
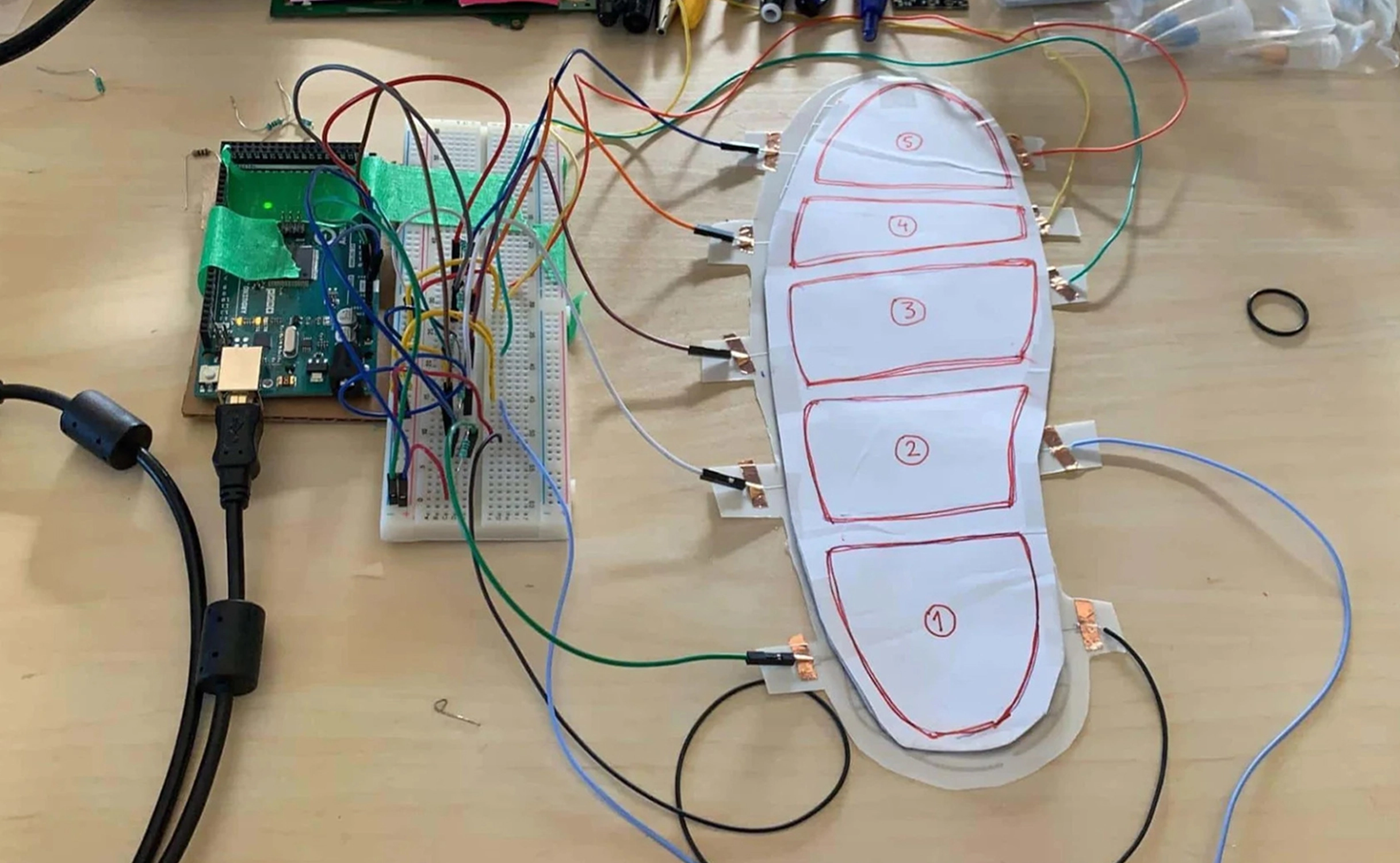
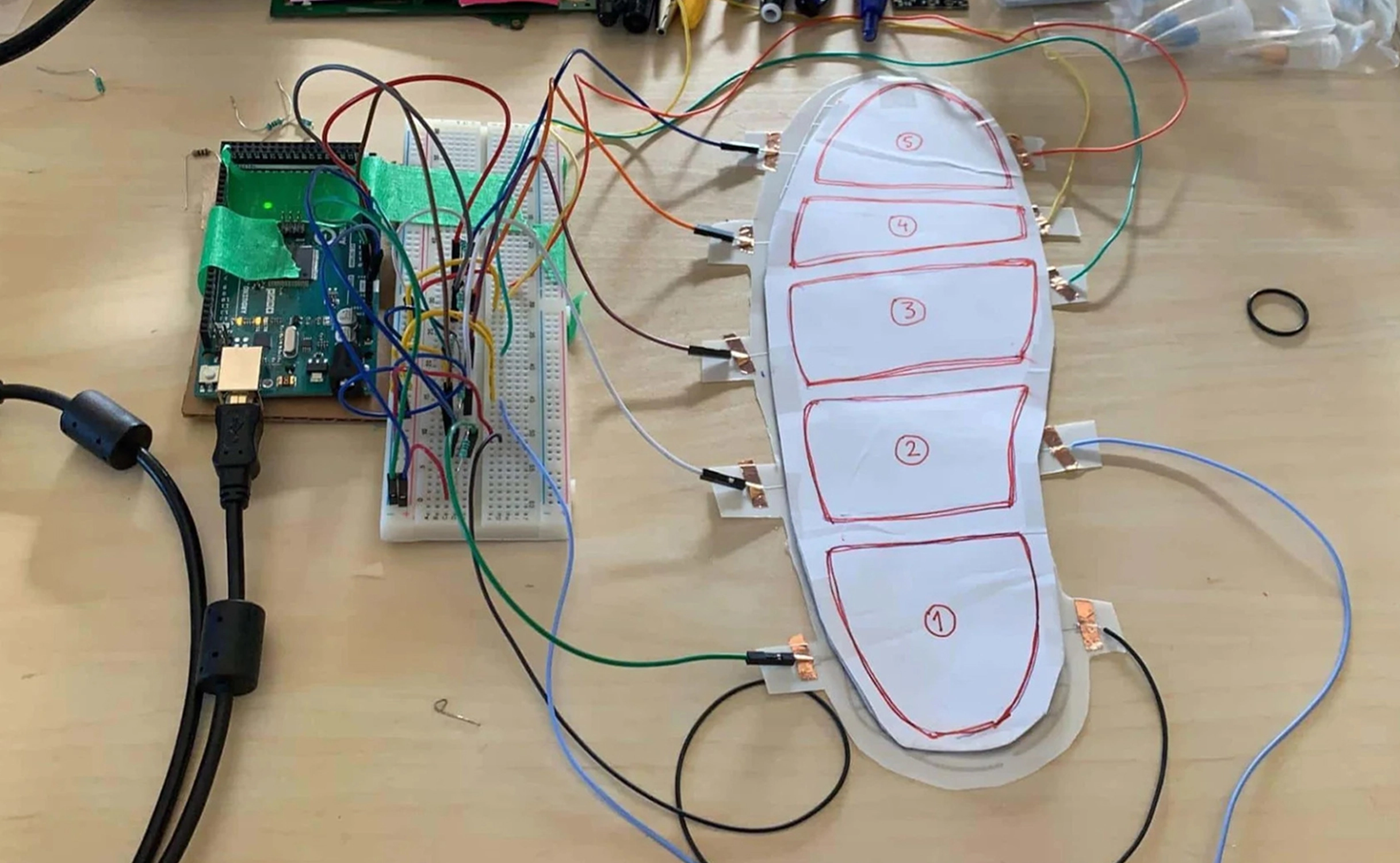
Biomedical sensors with silver-silver chloride ink
Another industry where we continue to see the application of conductive inks flourish is biomedical health monitoring. In our webinar Printing Biomedical Sensors, we demonstrated printing a biomedical sensor using Creative Materials’ 124-36 silver-silver chloride on TPU.
Didn’t get a chance to attend the webinar? Watch the recording on our YouTube channel:
RFID Tags with nano copper ink
Another common application for conductive inks is printing RFID tags. In this example, the tags were printed using Copprint’s LF-301 nano copper ink on paper in the desired pattern. This process resulted in better performance than an off-the-shelf tag we purchased from a market volume leader in RFID. With NOVA, we were able to produce one fully printed RFID tag antenna in less than 15 minutes.
Choosing an ink
Each ink has its own unique specifications and applications. Making a decision on which ink to choose can seem intimidating, so we are going to help simplify this process for you:
When choosing an ink, there are a few main aspects to consider to ensure your application achieves the results you're looking for. The main consideration is what you're trying to achieve with your application. This main decision will lead to other secondary considerations such as the substrate you plan to print on, the technology you intend to print with, and your budget. For a detailed breakdown on ink compatibility, see A Compatibility Guide for Inks and Substrates.
Some conductive ink suppliers include:
If you have questions about ink compatibility with our NOVA or V-One dispensing systems, please contact us at support@voltera.io.
Conclusion
The innovation of technology can’t exist without the innovation of processes. As electronics continue to move into a more flexible, sustainable, affordable, and reliable future, conductive inks serve as tools to make these innovations achievable.
To discuss whether a NOVA or V-One dispensing system might be right for your application, book a meeting with one of our application specialists.
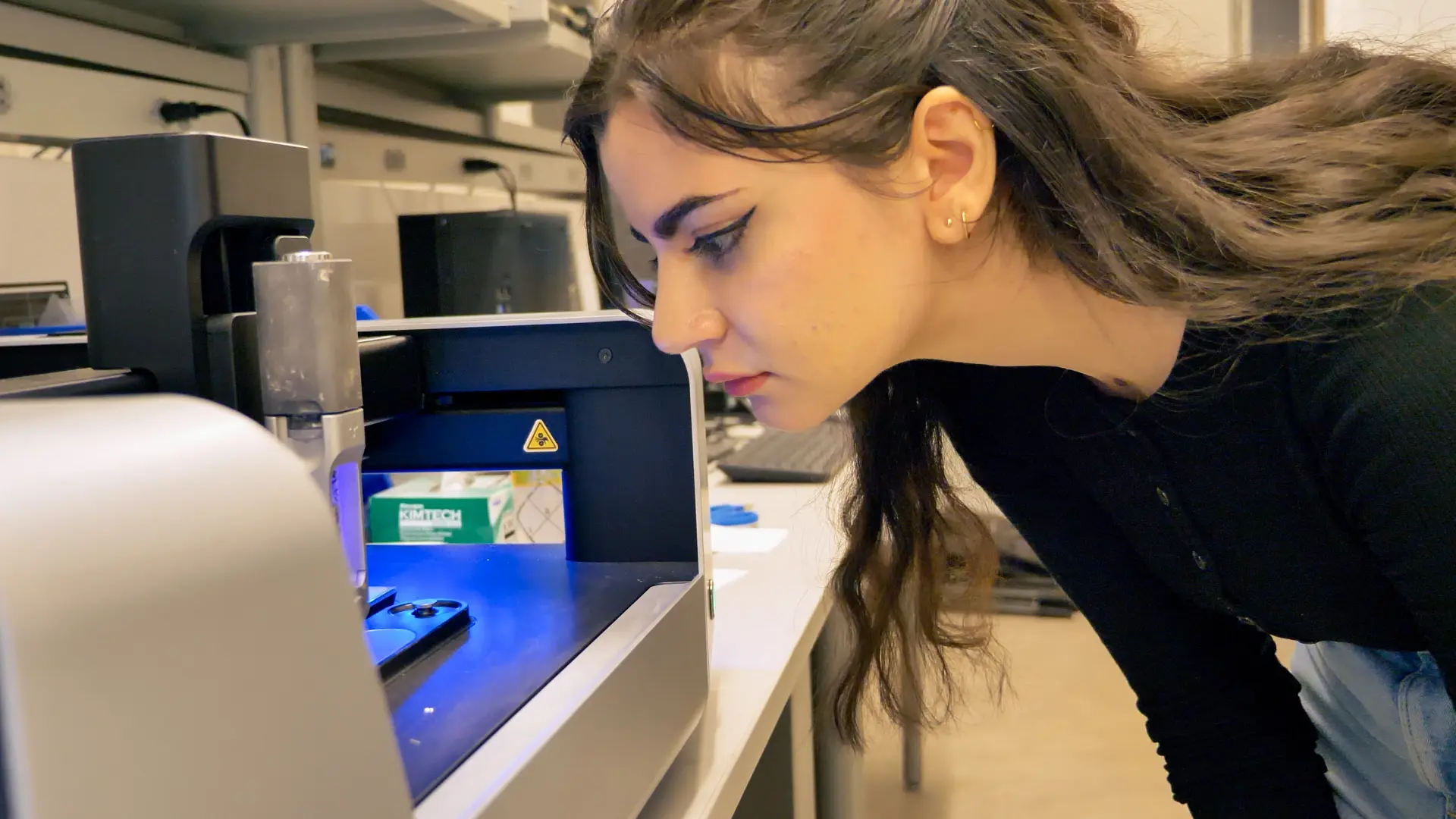
Check out our Customer Stories
Take a closer look at what our customers are doing in the industry.
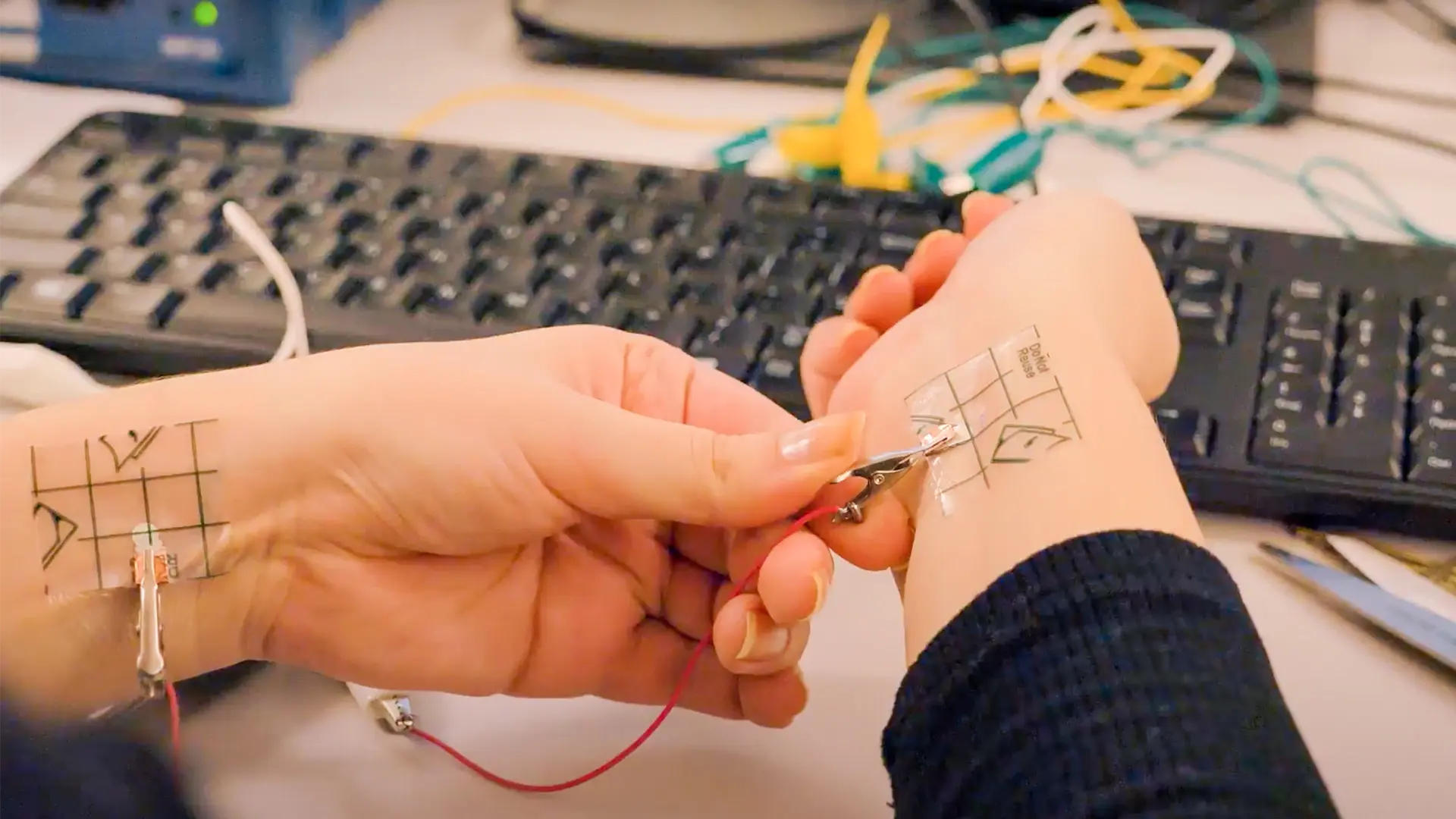