The Ultimate Guide to Choosing Materials for a New Electronics Product
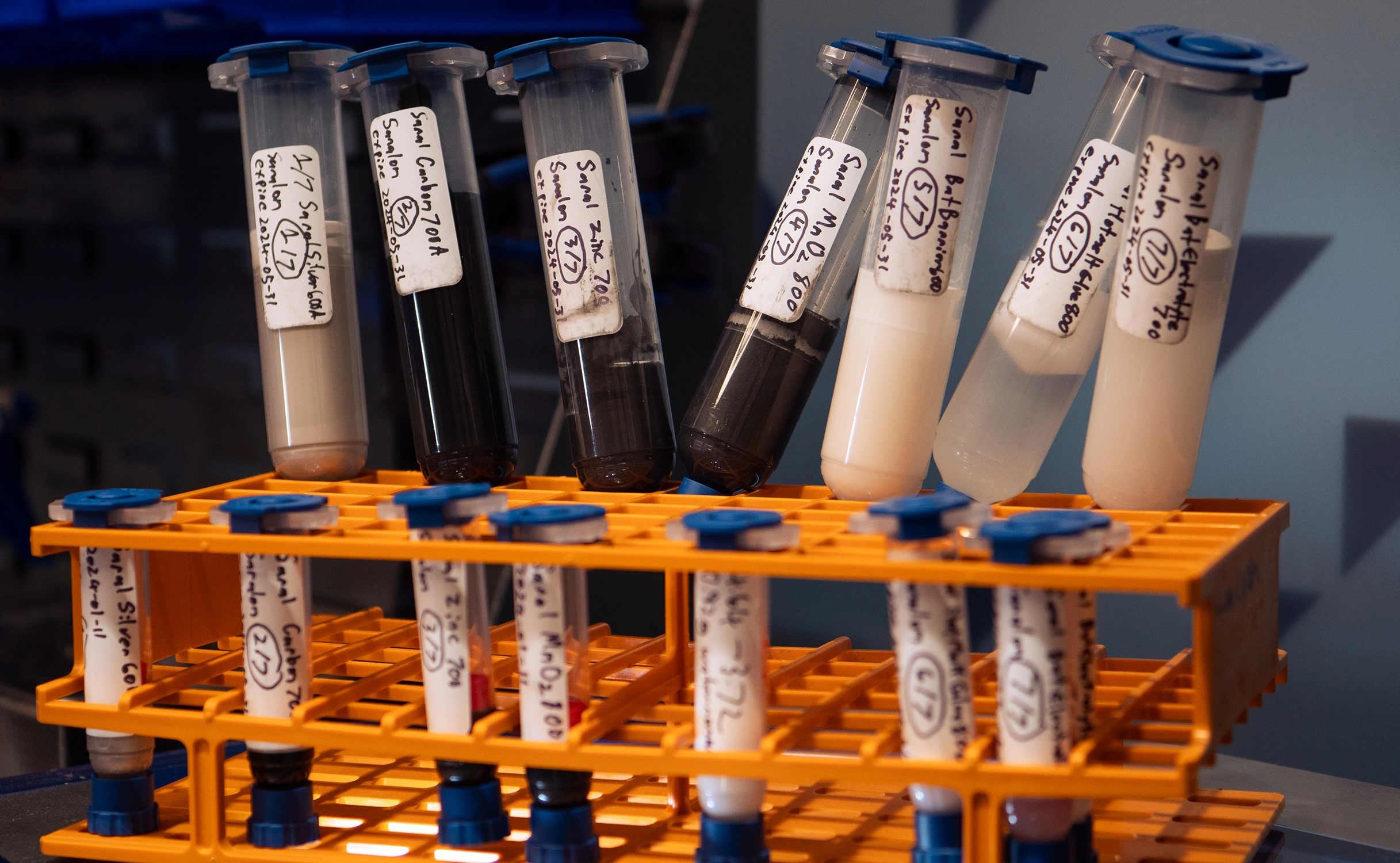
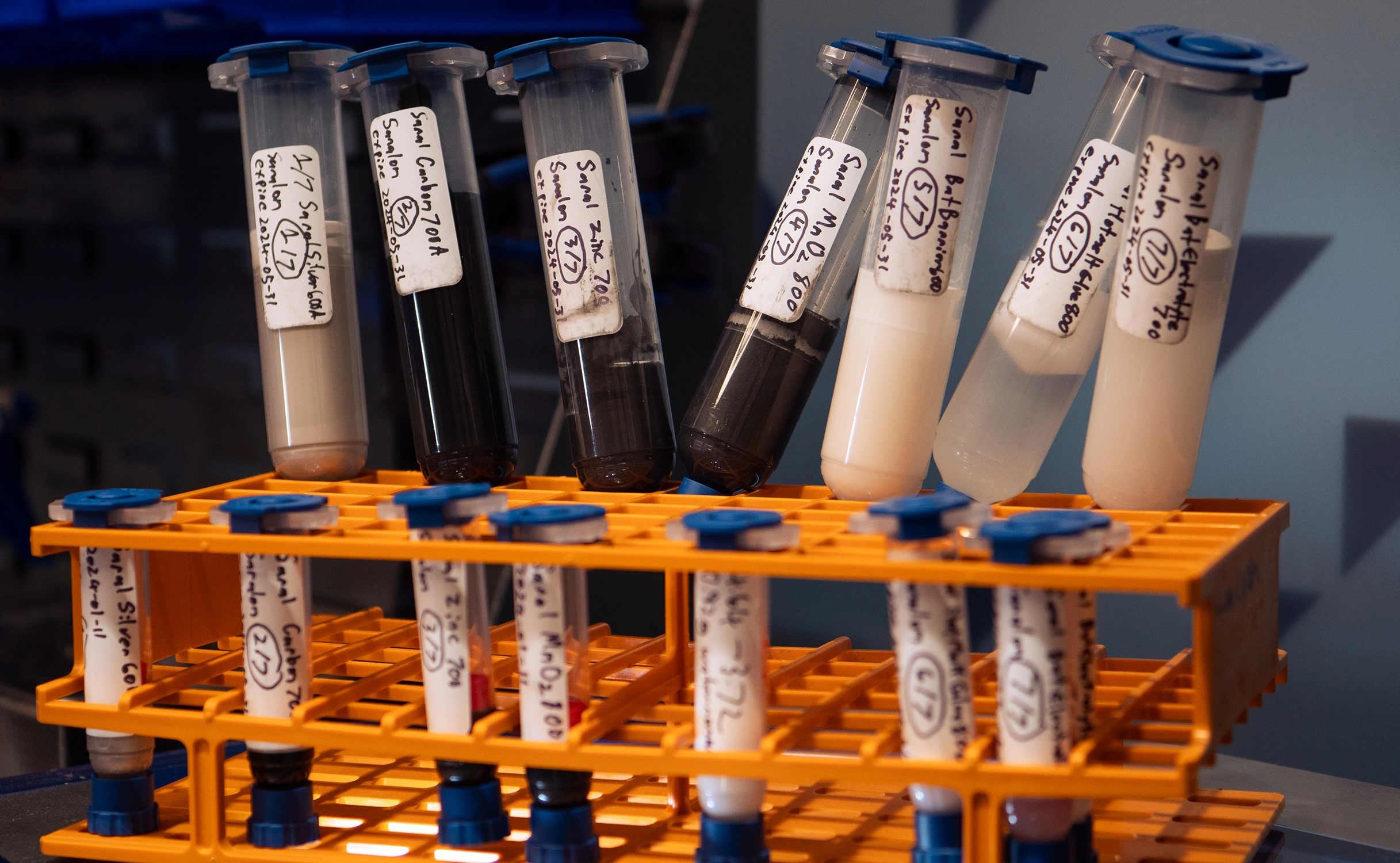
Building a new electronics product
We get it. You have this amazing idea and you think you know how to go about bringing it into reality — you’re excited to get started and you just want to do something. But before you launch out and boldly go where no person has gone before, there are a few things you should keep in mind.
Here at Voltera, we’re firm believers in DFX — Design For Everything. You need to know what you’re trying to accomplish! Your proof of concept needs to be able to translate to a final product. There’s nothing worse than a proof of concept that you can’t do anything with — either because the materials themselves are too expensive or hard to come by, or the machinery needed to produce the design is cost-prohibitive. But we’re getting a bit ahead of ourselves.
There are many functional materials that could come together to produce printed sensors, electronics, and other design features. Conductive ink is one of the most important ones, and so it’s going to be a major focus of this article. There are thousands — if not tens of thousands — of conductive inks to choose from, and which one you choose depends on a variety of factors. So how do you get started? How do you choose the materials that will work best for your brainchild?
Here are four major things to consider when choosing the materials for your new electronic product:
- What substrate are you going to use?
- What conductive ink will you need to make your product work?
- How is your conductive ink processed or cured?
- What printing technology will work with both of those materials?
But here’s the thing — you can’t choose your ink without considering your substrate, and vice versa. And you can’t pick either your ink or your substrate without first considering what printing technology you’re going to use! Basically, it’s an intertwined web and we’re here to help you sort it all out.
Let’s get started.
Substrates
In materials science, the term substrate refers to whatever material it is that you’re hoping to put your feature, or design on to. We’re going to start with the materials that you’re likely already familiar with in traditional electronics, and then branch out into some that we think you should consider — especially if you’re pushing the boundaries of what’s currently possible with electronics.
Traditional PCBs
FR4
The most widely used PCB material — it’s a flame retardant (FR), glass-reinforced epoxy laminate, approximately 1.60mm thick. It uses eight layers of fiberglass material and has a maximum temperature threshold of 120 to 130o C for the glass transition temperature. It has good strength to weight ratios, nearly zero water absorption, and is commonly used as an electrical insulator.
The biggest thing to consider with this material is that if you’re doing any drilling of through-holes for your project (aka you need a two-sided board), you might want to go with an FR1 board due to the fiberglass dust that would be generated with an FR4 board that can be hazardous to your health.
Of course, with proper masking and ventilation, this is definitely something that you can work around — it’s just something to consider.
FR1
These boards are cousins to the FR4, but instead of containing fiberglass, they’re made of paper and phenolic resin which makes them cost-effective and easy to build. It does however affect their heat resistance — they can be prone to scorching or warping when heated during the reflow process, or with thermally cured conductive inks. The other thing to consider here is that you can’t do plated through holes on FR1 in traditional PCB manufacturing paradigms, so you can’t do vias for double-sided boards.
Spoiler alert: With the V-One you can drill through holes in an FR1 board with the drill attachment and, using rivets, can achieve functionally plated through holes for double-sided boards!
Flexible printed electronics
Polyimide Films (AKA Kapton)
In the same way that we call facial tissues Kleenex, most folks refer to polyimide films as Kapton. These are a great substrate when your application is going to require the handling of extreme temperatures, vibration, radiation, or other demanding environments. It’s extremely versatile — it can be metalized, punched, or formed — and because it can be laminated on both sides, bonded to itself, metals, paper types, or other films, or even filled — it’s pretty much customizable for any situation. It’s also ideal for applications where size and weight play a role in the final look and feel of the product — such as microelectronics, or wearable electronics. Kapton flex circuits are already in lots of places where space savings matter — like inside your Airpods, your smart phone, smart watch, and laptop!
PET
Polyethylene terephthalate (PET) — the chemical name for polyester — is a clear, strong, and lightweight plastic. It’s incredibly common in packaging food and beverages (hello, 2L bottle of Coke!). DuPont was the first to synthesize PET in North America, so if you’ve heard the term Dacron, you’ve heard about PET.
As an inert and fully recyclable material, PET stands to have the least environmental impact of any of the substrates. Given the toxicity and harm created by the traditional copper etching process for PCBs, that’s definitely something to consider. But what it comes down to most folks is the overall cost at scale. PET is way cheaper than polyimide! But there’s a tradeoff — it’s less thermally and dimensionally stable, with a temperature max of between 140-160o C.
Stretchable printed electronics
TPU
Thermoplastic polyurethane (TPU) is a class of polyurethane plastics that have many properties that make them alluring in the world of flexible electronics: elasticity, transparency, resistance to oil, grease as well as abrasion resistance. Its stretchable nature also makes it an ideal choice for use in the textiles industry and in wearable electronics.
TPU powders are also used in processes like LASER Sintering and 3D inkjet printing — more on that later!
PDMS
Polydimethylsiloxane (say that three times fast!) is a substrate that’s particularly useful for things that need to stretch. That being said, it’s not something that you can readily purchase — many researchers will cast their own PDMS because of its use in stretchable applications, in addition to its good thermal stability, transparency, and biological compatibility. The learning curve on the process of casting PDMS is steep, but once you know how to do it — it’s pretty easy!
Modified paper printed electronics
When people think of printing something, even electronics, they think about printing on paper — but paper is porous! Generally speaking, you don’t want your substrate to absorb any of your conductive ink. To solve that problem, there are a bunch of coated and processed papers that are being developed to allow for applications in smart packaging, wearable technology, and textiles in general, for example.
Inks
Choosing an ink is an engineering decision — it means starting from your requirements, looking at your available options, and then optimizing for your desired outcomes and available resources.
Some questions you can ask yourself when choosing your conductive ink:
- What are your performance criteria?
- How do you plan to make it?
- How much are you willing to spend?
- How does it have to interact with the user and the environment?
- Does it need to comply with any regulations?
But first, some basics about what a conductive ink actually is.
A conductive ink is a material that can be:
- Printed — additively patterning your surface in some way.
- Processed — usually, by applying heat, this is what actually turns conductive ink into a conductive material.
- Conductive — Conductive inks are a subset of functional inks — inks that are useful outside of an aesthetic or structural need. Their job is to provide a path for electrons to get from point A to point B.
Conductive inks have two major parts:
- Filler — this is the conductive substance in the ink — typically metal particles — which give your ink its electrical properties
- Vehicle — everything else! Binders, dispersants, solvents, and additives — everything that suspends your particles, allows the ink to flow and dry, and gives it structural stability and flexibility.
- Binders: The binder matrix is a polymer (or a mix of polymers) that provides the ink with structural properties like adhesion, flexibility, mechanical robustness, and working temperature. There are others, but there’s already a lot going on in this article!
- Solvents: The solvent dissolves your binder and the metal particles in your conductive ink. This is important because it contributes to the flow characteristics that your conductive ink will display, which has an effect on the print quality and overall ease of use.
- Dispersants: The dispersant is what makes sure that your ink will flow and cure properly, as well as stay shelf-stable. This can be an important factor for the overall cost of your materials (less shelf-stable equals more waste), and ease of use — clumped, agglomerated particles are a bad time!
- Additives: This is usually the name we give everything else in the composition in the conductive ink. Often, these are modifiers used to tune the flow properties of the conductive ink for optimal printing.
Silver
As you can imagine, there are a number of different metals which might be able to imbue a conductive ink with electrical properties, but silver tends to be the main component of most conductive inks.
Why?
We’re glad you asked!
When it comes to choosing a filler, silver often wins out because of the factors most people care about:
- Good conductivity at a low cost
- Easily accessible
- Easy to use
- Superior stability
Basically, silver gives you the best bang for your buck in terms of conductivity, but also — silver conductive inks are ubiquitous! Most major conductive ink suppliers offer silver-based inks, so you’ll have far more options for different chemistries and configurations to suit your specific needs.
Copper
Traditional PCBs created using subtractive methods like etching are typically made using copper, so it deserves a mention here. While copper is a cheaper metal than silver when purchased in bulk, and because they’ve been used for decades in traditional electronics, we tend to know all of its properties like the back of our hand, using copper in conductive inks has its drawbacks.
- Conductive inks are not bulk metal.
You can’t evaluate the cost of copper vs silver in the bulk market and come away with any kind of meaningful comparison for your materials. A conductive ink’s overall cost includes processing costs for the raw materials, research and development, and any capital costs you might incur to use it (think: printer!).
- Copper oxidizes.
Copper conductive inks will oxidize when curing in air, which stops the copper particles from conducting electricity. In order to prevent this, you’d need to pump in a reducing agent, like nitrogen gas — which significantly increases the cost and the complexity of using it.
For these reasons — silver usually comes out on top in the conductivity/cost balance equation.
There are four major factors that you want to consider when choosing a conductive ink:
- Conductivity
- Viscosity
- Cost
- Curing method
Conductivity
For conductivity, the main things that you want to keep in mind are your filler type, particle size and the percent composition of metal contained in the conductive ink itself. A higher metal content generally means an increase in conductivity, as does a smaller particle size — but see the cost section below why this can be a problem.
EXAMPLE: If you need a highly conductive ink — stay away from a carbon filler as it’s considered a resistive material and stick to something like silver. You’re also going to want something with a smaller particle size, and generally, a higher metal content. The best bet is to speak with your conductive ink supplier to go over your use case and they’ll be able to guide you to the best possible option. Don’t know who to go to? Contact us! We’ll put you in touch with some of our best contacts.
Viscosity
For this one, you really don’t care about the specific composition of your conductive ink, you just want to make sure that the viscosity value is within the acceptable range for the printing technology you’re hoping to use. Inkjet technology requires a less viscous conductive ink than, say, screen printing — this is why we say you can’t choose your conductive ink and your printing technology in the dark; you have to consider both together.
Cost
It’s all well and good if you’ve done this really cool thing using a platinum filler in a conductive ink, but if you’re looking to make a product out of it, you’re not likely going to see a return on your investment! Micrometer-sized flakes (1-5 µm in size) of some of these more expensive materials can be readily obtained and are less expensive than larger particle sizes — but still don’t compare to your more traditional filler materials like silver. There’s also an in-between size called “submicron” which spans the 300-1000 µm range if you’re looking for a larger particle size, but looking to save a buck. In the end, you have to evaluate your idea with the practical applications of that idea in mind. Designing for design’s sake is a fool’s errand and no fun at all.
Curing Method
How does your ink process? In order for your conductive ink to become… conductive, you’re going to need to process, or cure, it. If your ink needs to be cured at high heat, but you’re looking to create something that’s flexible — you’re going to have a bad time. PET will melt at high temperatures! Generally speaking, you’re going to want to use thermally curable ink. It can be one of the easiest and most cost-effective methods of processing screen printable conductive inks. That’s not to say there aren’t some conductive inks out there that require some pretty precise processing, but thermally cured inks are by far the most available on the market.
In the end, if you’re designing with what you’re trying to accomplish in mind and make sure that your application and your material fit well together, you’re going to be on the right track to dispensing the right materials to bring your idea to fruition. Again this comes down to some of the more practical applications, so keep in mind how your ink needs to be cured and how that will affect the substrate the ink is printed on. Even FR4 boards will warp and/or scorch at sufficiently high temperatures! If high temperatures are a requirement, take a look into using ceramic substrates, or fired ceramic thick film.
PRO TIP: Choose your ink and the substrate at the same time.
Not doing this is like picking your t-shirt and your pants in isolation of one another — not the best way to have a party-ready ensemble! There’s no sense in picking an ink that requires a substrate that’s really hard to get your hands on or is prohibitively expensive. Of course, that doesn’t even take into consideration the more practical reasons for choosing a particular ink, like its resistivity, or the way the ink needs to be processed in order to lock the conductive particles in place. Stretchable inks are also often tuned for specific substrates, so you have to buy them together — unless you’re the brave type. As you can see, choosing your ink and your substrate at the same time can be an important piece of your particular product puzzle.
Now that you’ve chosen your substrate and your conductive ink, now it’s time to consider exactly how you’re going to print that beautiful, viscous conductive ink onto that carefully chosen material.
Let’s dive in!
Printing technology
Picking the wrong technology at the start of a project could lead to costly mistakes — capital investment upfront in terms of purchasing the equipment, and lost time when you have to pivot to make the design work with another printing technology.
Here’s a quick TL;DR of how these technologies stack up in one graphic:
Let’s take a look at the different options so you can make the best choice for your project.
Inkjet
If you think this sounds like the technology of your home office printer — you’re right! One of the main draws of using this technology in printed electronics, and rapid prototyping in general, is that it is digital. Whenever your design changes, it can be printed on the spot without additional tooling — which drastically reduces iteration time.
The technology relies on ejecting tiny droplets from hundreds of tiny nozzles on a print head in quick succession to form a pattern on the substrate.
PROS:
- High-resolution printing: Inkjet technology can typically achieve resolutions from 300-1200 DPI (~20-30 µm). The minimum printed feature size will largely depend on the conductive ink properties, droplet size, as well as the substrate you’re printing on.
- Low material cost: Because inkjet printing technology requires the use of low viscosity inks (60-90% solvent content), most of the deposited material will evaporate during the curing process, leaving behind a thin layer of metal — ranging from 1µm to 5µm thick.
- Digital Solution: Like direct-write technology, Inkjet printing uses a digital file (think: vector images) to print your design. This means that when you make design changes, all you need to do is upload the new design file and you’re good to go. Super time and cost-effective!
CONS:
- Higher resistance: The fact that the layer of metal is so thin has a trade-off in that it results in a higher resistance, which lowers the amount of current a printed pattern can handle.
- Susceptible to breaking, or incomplete circuit printing: Also as a result of that thin layer of metal, and how viscous the ink needs to be, the chances of there being a break in your circuit are much higher with inkjet printing technology than some of your other options. The traces are also less robust and therefore more likely to break.
- Susceptible to improper storage conditions: The purpose of the solvent is not only to provide a carrier fluid allowing the conductive ink particles to be printed, but it also includes additives to stabilize the ink under proper storage conditions. Improper storage will allow large agglomerates to form which can clog nozzles.
- Difficult to solder components to: The printed features are usually so thin that without a robust binder within the structure to keep the metal in place, molten solder will very quickly dissolve the metallic particles, destroying the printed pattern in the process. Conductive epoxy or anisotropic conductive adhesives are an option though!
- COST!: Laboratory inkjet printing systems cost at least $25,000 and can run into the six-figure territory pretty quickly.
- Scalability: According to IDtechEX, inkjet technology made up less than 2% of all commercial printed electronics products in 2017, while screen printing made up the remaining 98%. A major contributing factor to this is that the initial costs associated with setting up a production facility for a product created using inkjet technology is significantly higher than screen printing technology. Add to that, that screen printing infrastructure already exists and that continuous improvements to the technology are occurring, and you can see why screen printing is more attractive.
Screen printing
This is a technology that goes way, way back — like, 1000 AD, way back. Advances in the technology of screen printing are what makes it so versatile, and its versatility is what makes it one of the most well-established manufacturing technologies around. We’ve been using it for everything from printing graphic t-shirts to additive electronics! Screen printing for additive electronics uses a finely woven mesh to transfer conductive ink onto a substrate. The screen uses a masking material (or emulsion) to block holes in the mesh to prevent ink from being deposited onto the substrate in that area as the wiper, or squeegee passes over the screen.
PROS:
- Compatible with a wide range of materials: Screen printing is compatible with conductive inks ranging in viscosity from 1000 cP to over 100,000 cP. You can also make almost any filler material work — carbon, silver, nickel… you name it!
- More metal means thicker printed layers: Unlike inkjet where the majority of the conductive ink is composed of solvent which will evaporate during the curing process, conductive inks used in screen printing have only a small percentage of binder and solvent by weight. This means you get layers with a typical thickness ranging between 10-35 µm.
- Lower resistance: The larger cross-sectional area of traces with a screen-printed pattern means that they will have a lower resistance when compared to other printing technologies
- Versatile: Whether you’re looking for high power or high-temperature applications, or low temperature and better adhesion to your substrate, screen printing has a lot of versatility compared to other printing processes.
- Low initial investment: Since only a few pieces of equipment are needed, you can get set up with a manual screen-printing process for less than $500 — making it one of the technologies with the lowest upfront cost to get started. Additionally, since the majority of the screen-printing infrastructure is already in place, getting a screen-printed product to market can be significantly cheaper than alternative printing technologies.
- Consistency: Maintaining the same process and materials throughout development and into production really shortens the time to market and allows designers to have confidence in the design when it comes time to scale.
- Scalable: You can take advantage of the existing infrastructure of the screen printing industry that’s mostly been used in textiles (think: graphic T’s), in order to print your design. This means that high-volume printing is in your reach with this technology!
CONS:
- Resolution: The resolution you can get with screen-printing with conductive ink can be comparable to the resolution that you can achieve with inkjet, which is a feature size of around 25-50µm — but that’s pushing the limits of screen printing technology. In practice, you’re looking at 200-300µm from a commercial printer.
- Tooling costs: Every time your design changes (or a new material is being used) a new screen must be made to reflect that change or to be optimized to work with the new material. In the early stages of development, the costs associated with new screens and the added time between iterations can really add up. This is especially true for projects that call for layered patterns — they’ll require multiple screens per iteration.
- Difficult materials experimentation: Ideally, you want to use the same process during research and development that you would use in production. But, a compound effect of the tooling costs, screen printing makes it very difficult for developers to try out new materials before deciding on the one that will work best for their application — which makes it problematic for a research and development stage.
- Material waste: During the printing process, a fair amount of conductive ink must be spread across the screen to ensure proper coverage. The screens also have to be washed with the proper cleaning solutions after every use. Ink can be salvaged, but there will inevitably be waste of some of your conductive ink during the printing process.
- Materials safety: With the amount of conductive ink and proper cleaning solutions required for screen-printing, the proper personal protective equipment can represent added cost as well. Reviewing material safety data sheets before choosing your conductive ink will be an important step. If you’re working in an environment where the materials can’t be handled safely, bringing screen-printing capability in-house may not be the right option — and then you’re looking at outsourcing, which represents an added cost.
Gravure
The opposite of relief printing where the image is raised from the surface of the plate used for printing, gravure is when the image is formed in the recesses, or depressions, on the surface of the printing plate. Once the grooves are etched into the plate to form the image, you place ink into the recesses, place the plate on your substrate, and the ink is deposited onto your substrate from the recesses.
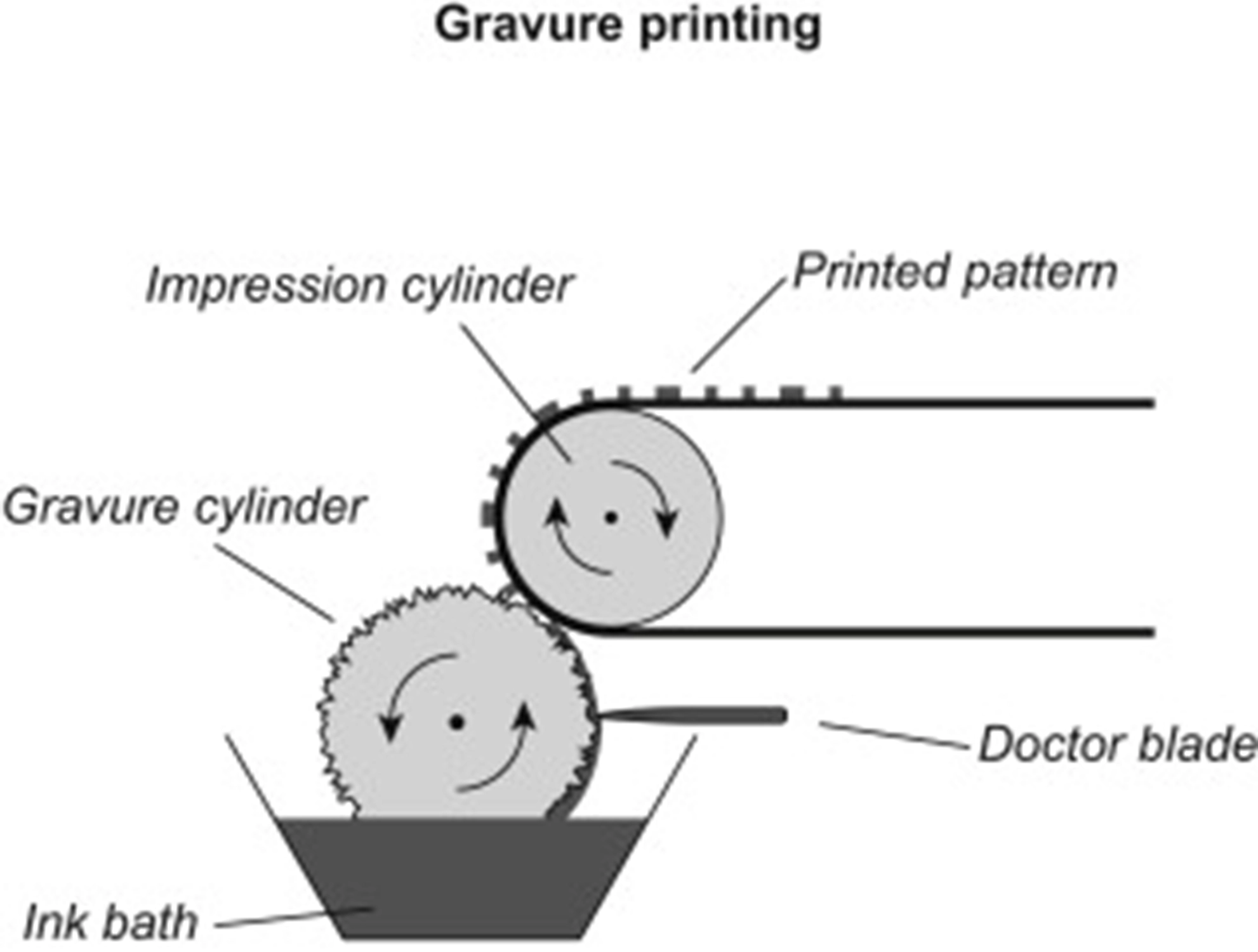
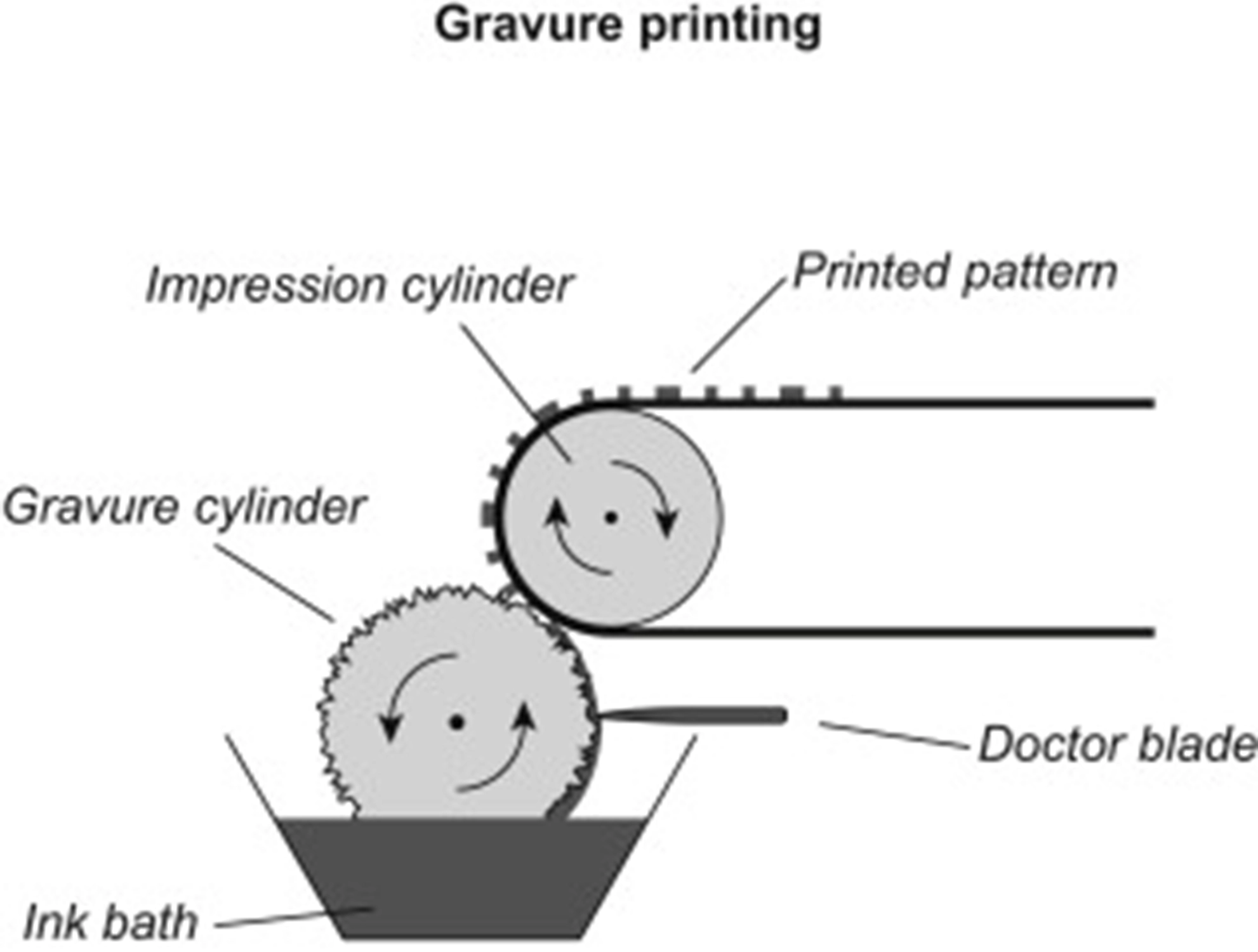
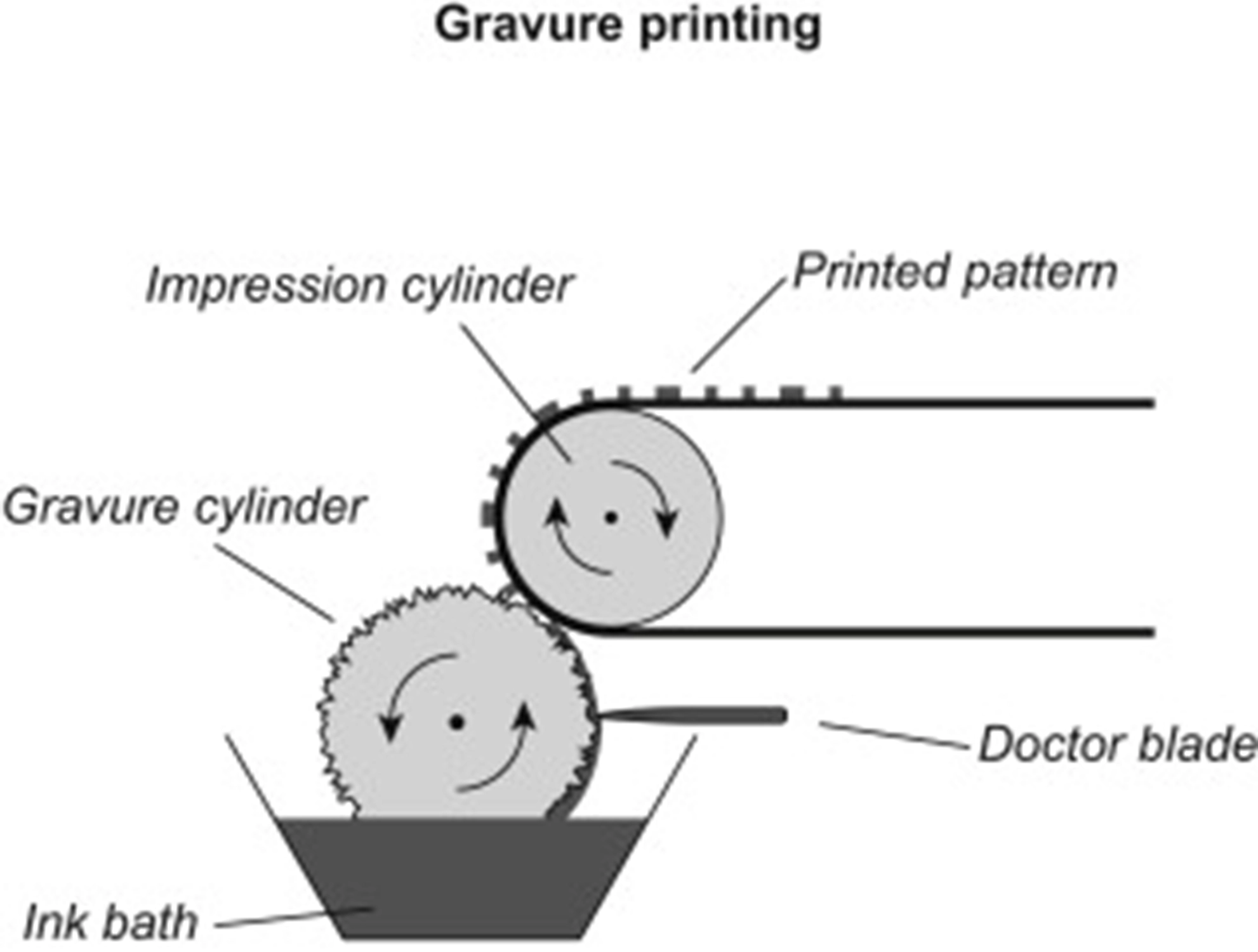
PROS:
- Great for high volume printing: Because this technology relies on the laser etching of the metal plate, it delivers results that are incredibly precise — and repeatable.
CONS:
- Expensive!: Because this method relies on the laser etching of your design onto a metal plate, iterating becomes increasingly expensive — you need a new plate for each iteration. The cost at the outset to tool a factory for this kind of printing can be cost-prohibitive and you’re committed to a certain volume in order to get any return on your investment.
- Substrate limitations: Because traditional gravure printing technology relies on the porosity of the substrate and capillary forces to basically suck up the ink from the surface of the metal plate used to deposit the ink in the design of your choice, this is what makes it a less than ideal technology for printed electronics; absorption of your ink into your substrate can make conductivity a nightmare. Thus, you’re going to be limited to non-porous substrates.
- Need a low viscosity conductive ink: As a result, of the previous point, you’ll need to work with a low-viscosity conductive ink so that the substrate can easily pick up your conductive ink in the little time it’s exposed to it. Again, this just imposes some limitations on which conductive ink you can choose for your design.
Aerosol This printing technology uses an atomizer to create a dense mist out of your conductive ink — with droplets ranging from 1-5 microns in diameter — surrounded by a sheath gas that focuses the ink into a tight stream of droplets. The result is a high-velocity particle stream that can print at a distance of 2-5 mm from your substrate surface.
PROS:
- Really fine resolution patterns: Because the droplets can be so small using aerosol, the resolution of your designs can get quite high!
- Can print on complicated geometries (3D Objects!): Aerosol machines can print your design on three-dimensional objects, so if this is a practical application of what you’re designing, it’s definitely an option to consider.
CONS:
- Low volume, low throughput: This technology isn’t something that you would use for mass production — you’d need to invest in multiple machines, which due to the cost of the machines, is cost-prohibitive.
- Steep learning curve: As you can imagine, working with sheath gasses isn’t a skill set most folks pick up in applied learning courses during their degree, so expect to need to learn a lot in order to work with this technology. This can play a big factor in the number of iterations and the time between iterations — which of course can play a factor in the time it takes to get you to proof of concept and/or publication.
- Cost: As mentioned in the scalability point, the cost of these machines makes them cost-prohibitive for most design applications. In addition, you’re looking at increased materials cost due to the requirement of the sheath gas to focus the conductive ink to get that fine resolution that is a selling feature of the technology.
Flexography
Also known as “flexo printing”, flexography is basically a modern version of the letterpress, and can be used for printing on almost any kind of substrate — plastic, cellophane, paper, metal… the list goes on. It uses a flexible printing plate on rotating cylinders that spin at high speeds to transfer the ink through small holes to the substrate. The pros and cons list of this one is pretty much the same as for Gravure as they’re very similar technologies.
PROS:
- Great for high volume printing: Like Gravure, Flexo printing offers great repeatability and precision. The high-speed nature of the technology makes printing in high volumes a breeze, so if this is an important factor for your design considerations, give flexography a good look.
- Substrate flexibility: The fact that you can use flexographic printing technology on substrates like paper and cellophane, it’s an ideal choice for things like smart packaging.
CONS:
- Hard to get into: This technology isn’t as straightforward or well adopted in the industry of printed electronics, and you need to be looking to print in pretty high volumes in order to make it worth your while. So learning the technology, getting the exposure you need to be able to prototype and iterate quickly with it, can take some time. Unless you’re looking to get into smart packaging, we’d steer clear of this one!
Direct write
Also known as 3D printing by direct extrusion, direct-write technology uses pneumatics, pistons, or screws to apply force and dispense conductive ink from a cartridge. For this technology to work properly, you’re going to want a conductive ink somewhere in the 1-200 kcP (Pa·s) range, though improvements in the technology (👀) will open up these boundaries. Something a bit thicker usually works best. You also want to pick a filler material you’re going to get the most options from. This is why silver is used most often, or carbon for projects that require more resistive materials.
PROS:
- Digital in nature: With direct-write technology, we at Voltera often say that you can “print anything on everything” — as long as you have a design file, a printer, the ink, and a substrate, you’re good to go! This makes the technology highly flexible and adaptable to whatever situation or use case you can imagine.
- Can work around raised features: Because direct-write printing technology only puts ink where you want it, it allows you to work around other raised features or components on your substrate.
- Gives you access to the z-axis: Direct-write printing technology is one of the only technologies that allows you to easily configure the thickness of your material when printing on your substrate. This would even allow you to put different thicknesses in different areas of your board!
- Easy to change materials: When you’re at the forefront of technology research and design, you need to be able to change your trajectory on a dime; for a multitude of reasons, you may discover that the material you thought would be perfect for your idea turns out to be a complete mismatch. Therefore, it’s crucial to have a printing technology that can support a variety of materials, so that change doesn’t mean a complete return to the drawing board. This includes things like solder pastes and adhesives!
- Less expensive: With machines at under $5000 to get you started down the path of printed electronics, the up-front investment for direct-write automated technology comes in at the lowest of all of the technologies that we’ve outlined for you here. And because of the flexibility mentioned in the last point, all you’re doing is paying for the materials, the machine is the same regardless of what you’re printing with!
- Easy adoption: The technology is simple and easy to use — you don’t need a degree in materials science to get started; at least not when you’re using a Voltera machine 😉. Here at Voltera, we also use video and text tutorials to make access even easier and walk you through any support issues you may run into on your journey in the world of printed electronics.
- Results are good: The resolution of direct-write technology is quite good. Not inkjet good, but definitely on par with screen printing — and some would argue it’s even better.
- Iterating is easy: With direct-write technology, you can print a new design in as little as a few hours, whereas for most other printing methods, you’re looking at a much longer turnaround time. This can make iterating really cumbersome, and this can mean a lot of added time when you’re considering time to publication or proof of concept. Additionally, as with inkjet, because it’s a digital technology you don’t need to retool whenever your design changes — just upload your new design file and you’re good to go, drastically reducing iteration time.
CONS:
- Scalability: High-volume printing is not something that you’re going to do with this — you’ll want to do something that’s more economical to scale like screen printing. The good news is that because the technologies are so similar and use the same conductive inks in terms of viscosity, you can actually use direct-write technology to iterate on your design (because it’s faster and more economical), and then switch to screen printing once you’ve got all of the bugs out of your board. You can leverage the existing technology in the screen printing industry to scale your design!
The reason we’ve given you a bunch of technologies to think about is that even though you’ve chosen your ink and your substrate together (way to go!), not all conductive inks will work with every printed electronics technology out there. So this is important:
Choose an appropriate ink for the technology you want to do your printing with.
Removing barriers in additive electronics
Here at Voltera, we’re obviously big fans of direct-write technology and conductive inks — they’re kind of our bread and butter. But we didn’t choose this method lightly! Technologies like inkjet or aerosol printing don’t scale very well; so if you want your product to be available en masse, then you’re going to want to choose a technology that won’t require a huge capital investment to produce your final product. Also, conductive inks that are useable with direct-write printing technologies are easily available, because they’re largely the same as the ones used in screen printing, which has been around forever. They don’t push the minimum feature size that much, and the technology to produce your product is well adopted; factories won’t need to retool in order to produce your final product because you’re taking advantage of the existing screen printing infrastructure.
Still need help?
Here at Voltera, we like to help you pick an ink so that you don’t need a Ph.D. in materials science to create something awesome. We’re all about making materials more accessible. If you can, we recommend reaching out directly to the ink manufacturer! They love their inks and they want you to be happy that you chose theirs for your product design — so they’ll give you answers to the practical and theoretical questions you might have about their brainchild; especially the tips and tricks that didn’t make it into the datasheet.
We have great relationships with conductive ink manufacturers, so if you’re not sure who to reach out to, get in touch and we can connect you!
Last, but definitely not least, reach out to a member of our team to find out whether we have the right tool for your job.
Until next time…
The Voltera Team
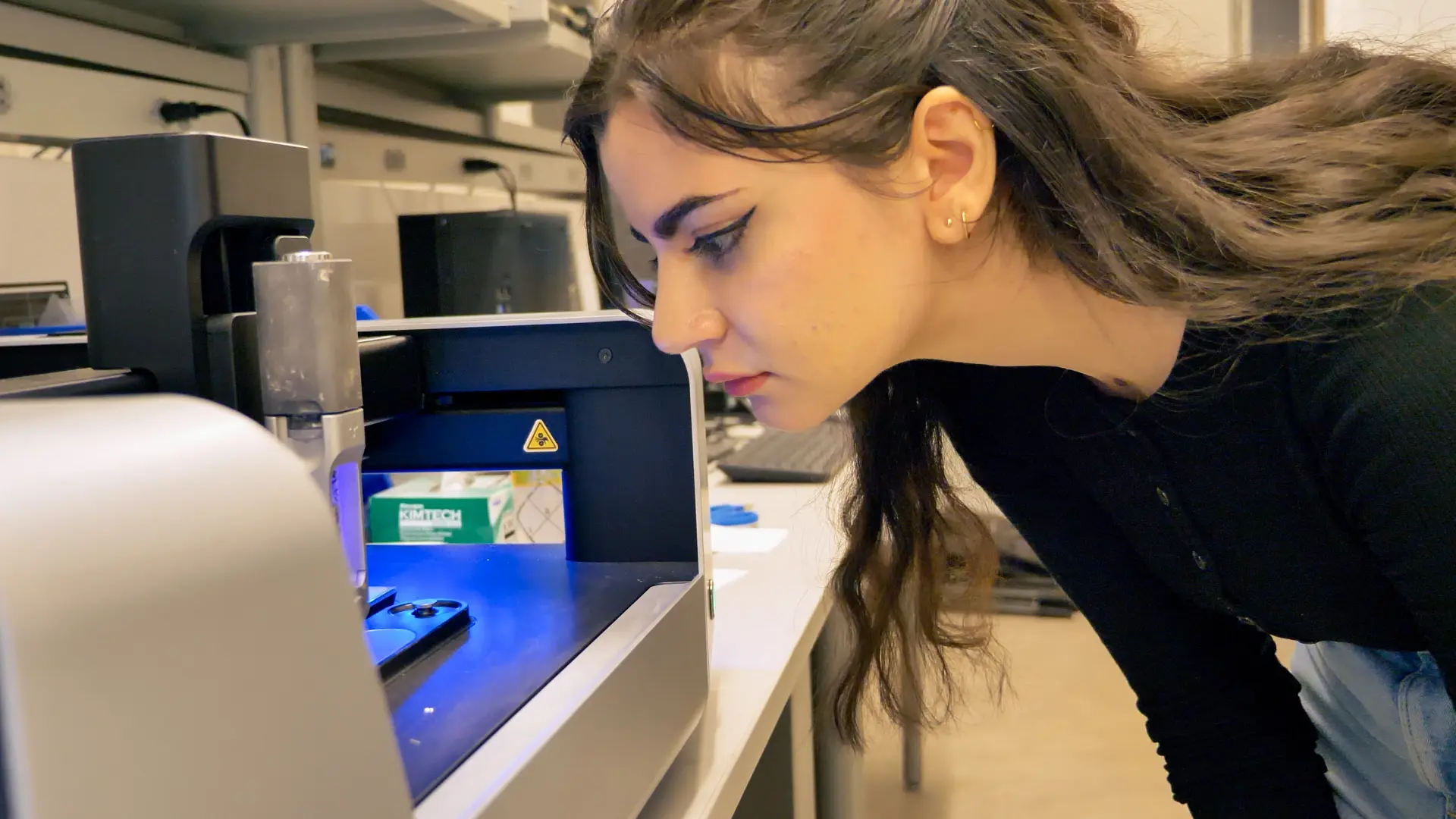
Check out our Customer Stories
Take a closer look at what our customers are doing in the industry.
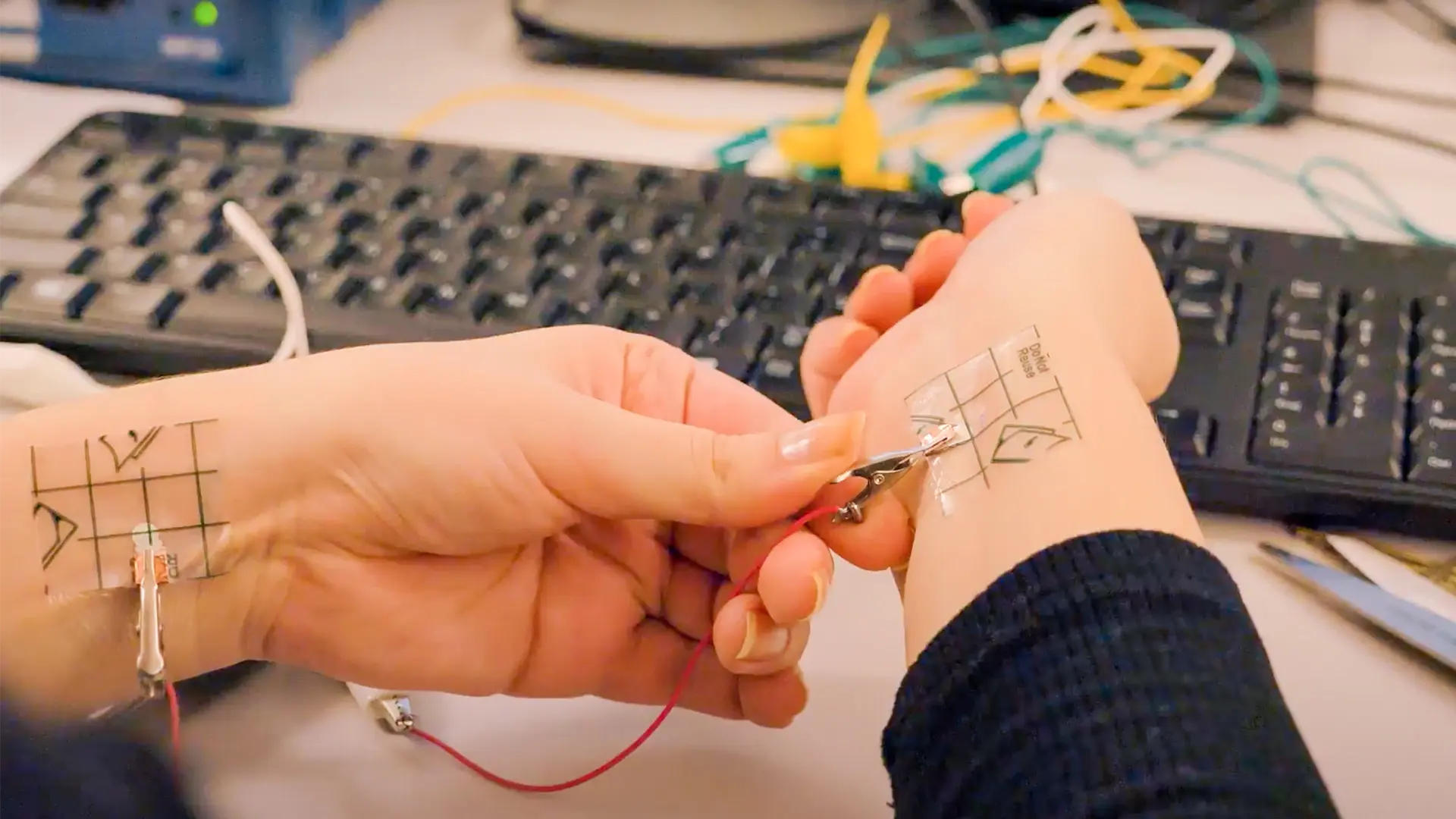