Warming Your Coffee with In-Mold Structural Electronics
Is there anything better than a good cup of coffee (or tea!)? It's divine when it's hot, and deliciously refreshing when it's iced.
…But room-temperature coffee? Not so great.
For most adults around the world, brewing a hot cup of coffee is an established part of our morning routine. But when you have a busy day, it’s easy to get preoccupied and neglect your coffee until it cools to an unpleasant temperature.
Duru Uluk, a Voltera test engineering intern, set out to find a solution to this problem. Her goal was to create an induction mug heater using in-mold electronics (also known as in-mold structural electronics).
What are in-mold electronics?
In-mold electronics (IME) processes involve printing conductive inks on moldable plastic films, which are then formed into a desired 3D shape. In the full IME process, after thermoforming, the part is passed along to injection molding, where it is molded in plastic and the electronics become part of the entire structure.
In IME, the electronics are printed using a standard process of screen-printing traces onto thermoformable plastics, but new innovative materials — like specially formulated functional inks optimized for high single-stretch operation — allow the traces to stretch into the new thermoformed shape and maintain conductivity.
What are the applications of in-mold electronics?
This technology is particularly exciting for automotive and aerospace applications, where thousands of feet of copper wire could be replaced with conductive traces integrated directly into the vehicle’s panels to reduce the vehicle’s weight and improve efficiency. Incorporating IME into vehicle construction also presents opportunities for new design concepts, features, and functionality — like the ability to incorporate strain sensors directly into panels to monitor for damage, interactive surfaces in the interior vehicle panels, or to heat and de-ice the wing of an airplane during flight.
In the image below, all the red components identify the wire in a vehicle:
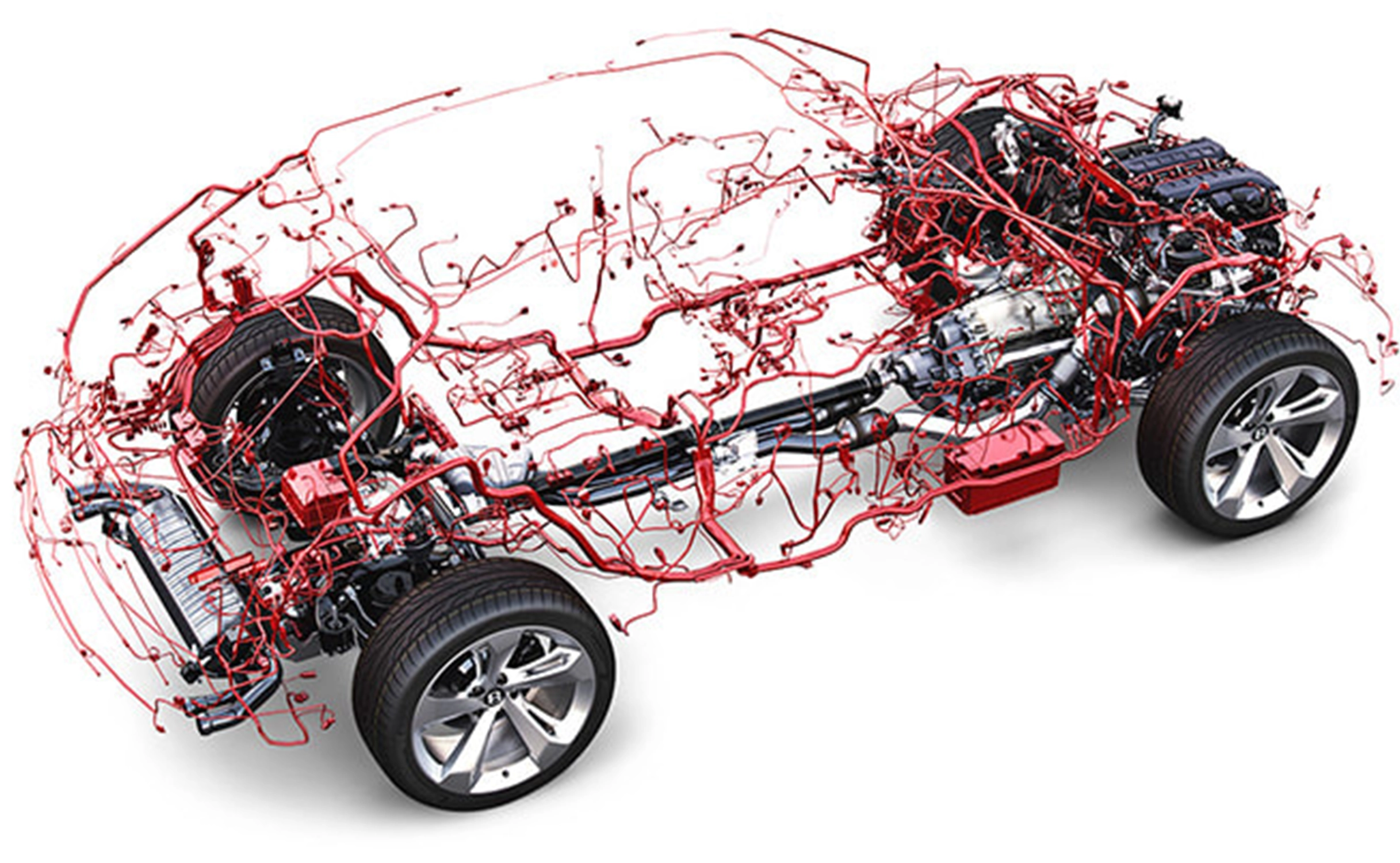
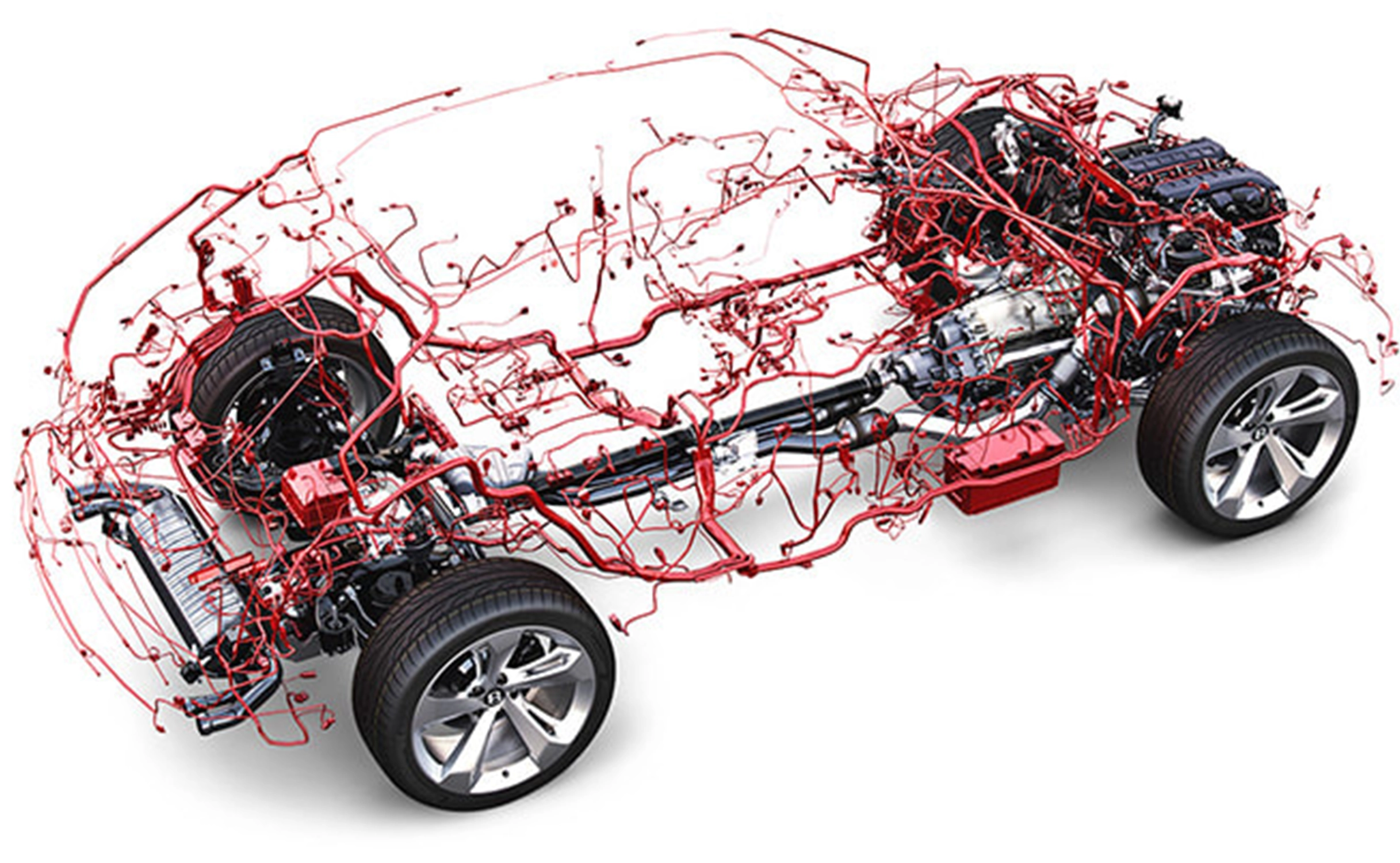
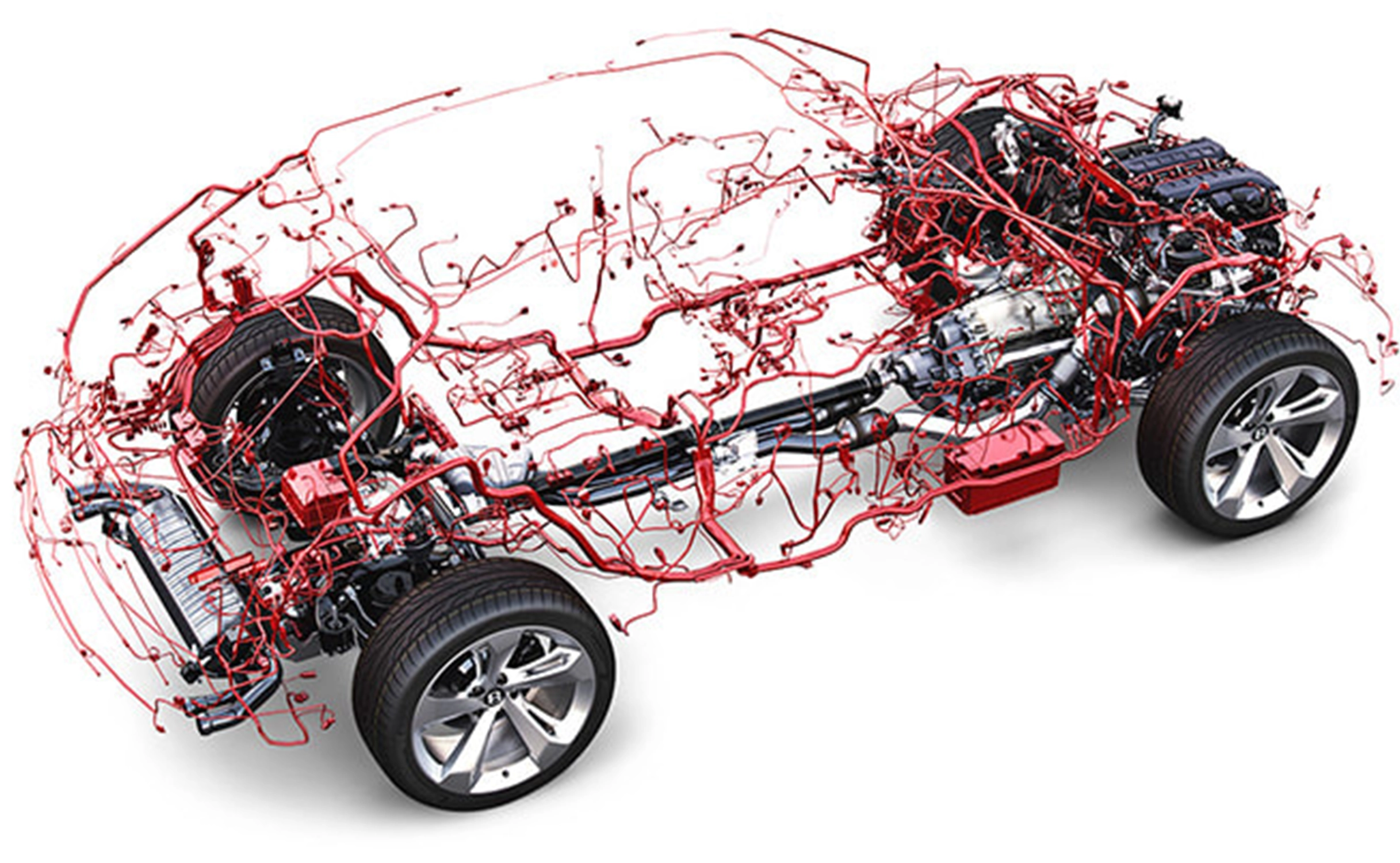
- One vehicle has 5000 feet of wires = 50 lbs of copper.
- Transporting 50 lbs burns 12 L of gas per year.
- 70,000,000 new cars produced per year.
- 840,000,000 L of gas is burned to transport copper cables per year.
In addition to this example of copper wire, IME offers plenty of other opportunities to reduce the mass of many vehicle components, like the headlight assembly, dashboard, center console, and more.
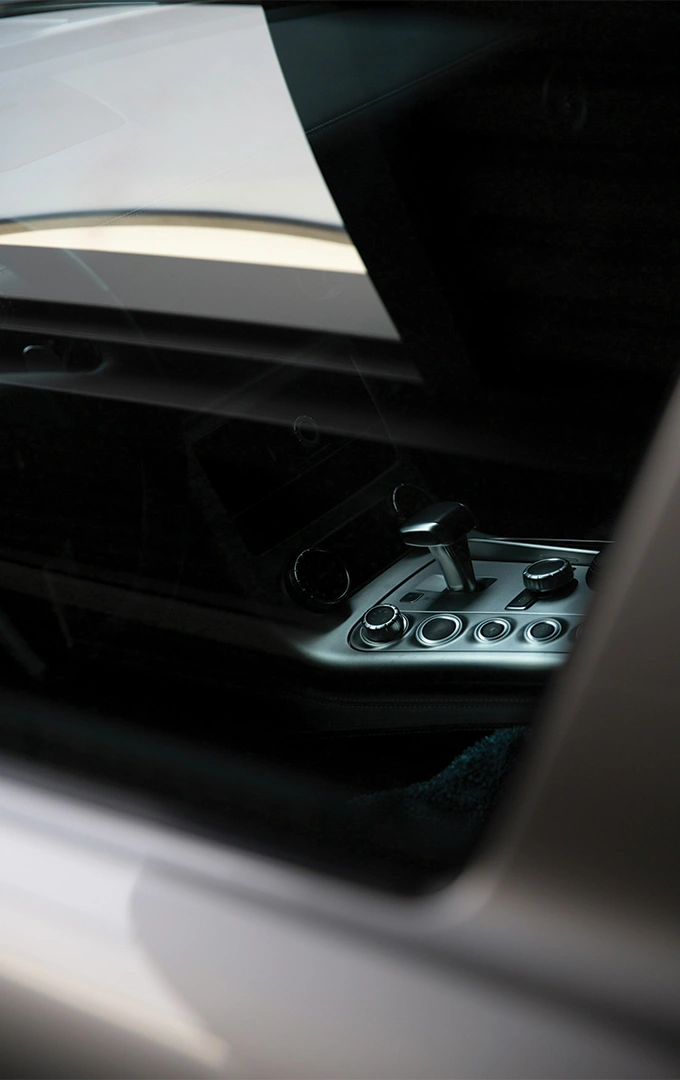
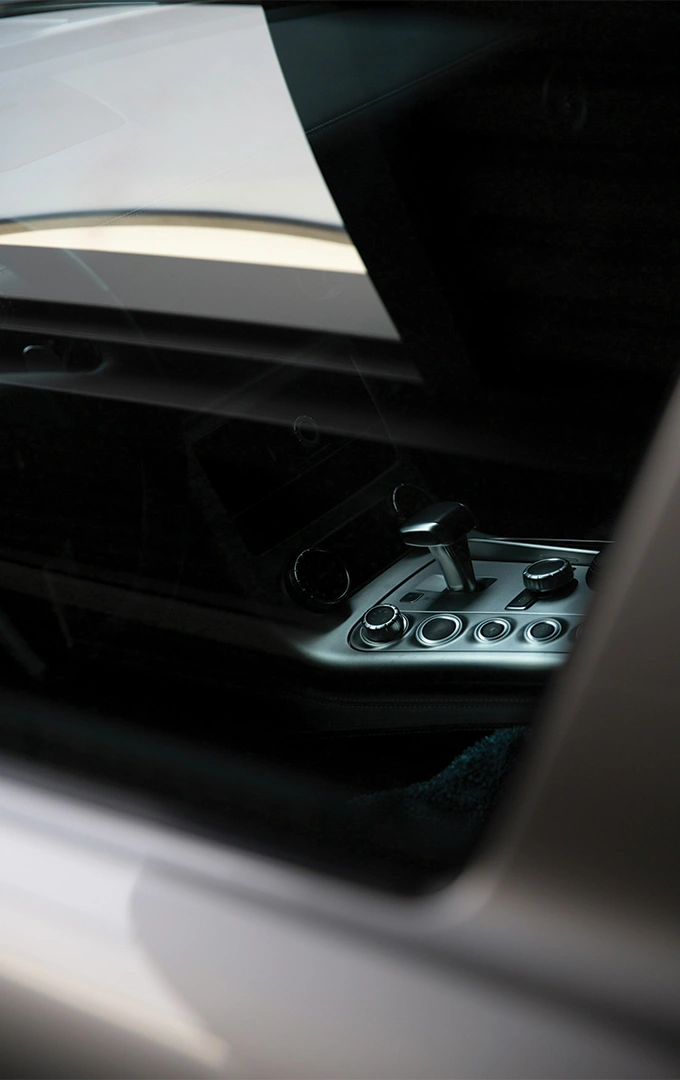
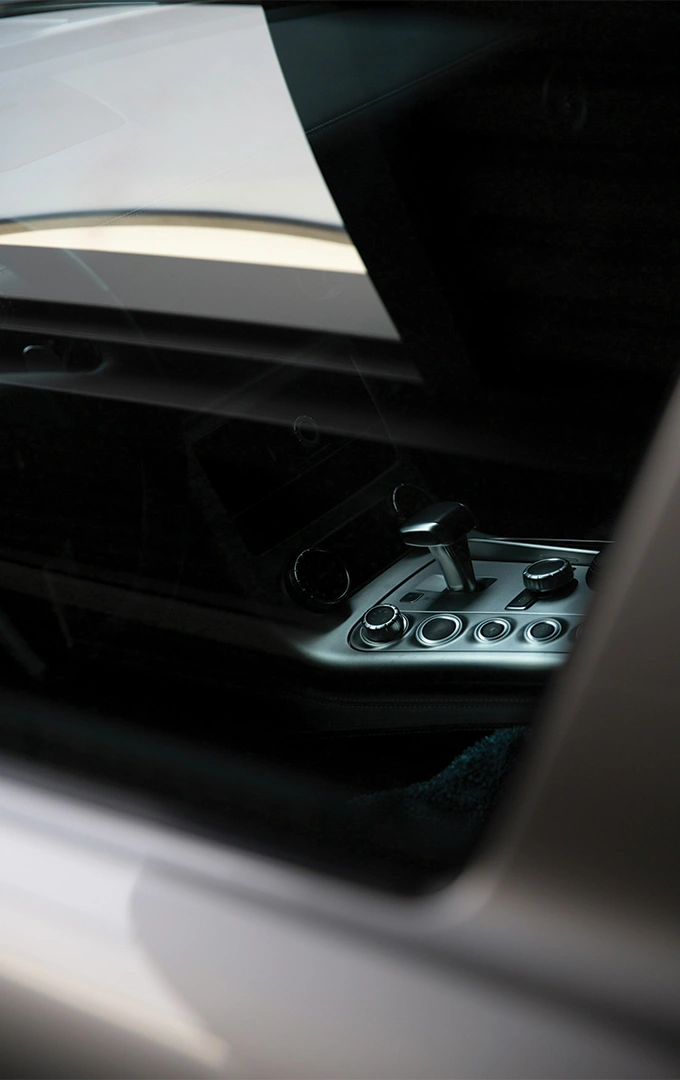
IDTechEx anticipates the mainstream adoption of in-mold electronics in automotive interiors to begin in 2023, and is forecasting that electronics will be printed onto 3D surfaces, like door panels, in 2026.
Printing a mug heater with NOVA
But let’s get back to Duru’s coffee conundrum.
Using NOVA, a Mayku Formbox, and a Formlabs 3D printer, Duru designed and built a mug heater with in-mold electronics technology.
“During my co-op term at Voltera, Matt (Ewertowski, Product Manager) was my supervisor and also just a super cool person to talk to. We had conversations about different applications of NOVA and how flexible substrates open doors to a lot of different project ideas,” Duru recalled. “He suggested the idea of using the Mayku Formbox alongside NOVA for an in-mold electronics project. I did some research about making molds, molded electronic applications, and coil heaters — and from there it seemed feasible enough to continue with a demo.”
So, Duru got to work. First, she used the Formlabs Form 2 3D printer to create a resin mold, and then used NOVA to print traces onto the Mayku Formbox substrates. Finding the optimal baking temperature for the Mayku substrates was a bit of a challenge, since they aren’t intended for IME, but with some experimentation and a bit of help from Mayku, she eventually found the right temperature and baking time to avoid substrate deformation. Once the curing temperature was refined, Duru encountered trace breakage during the forming process. Through some trial and error, Duru refined the design of the mold and the traces until she was successful in creating a design that could be thermoformed and maintain conductivity.
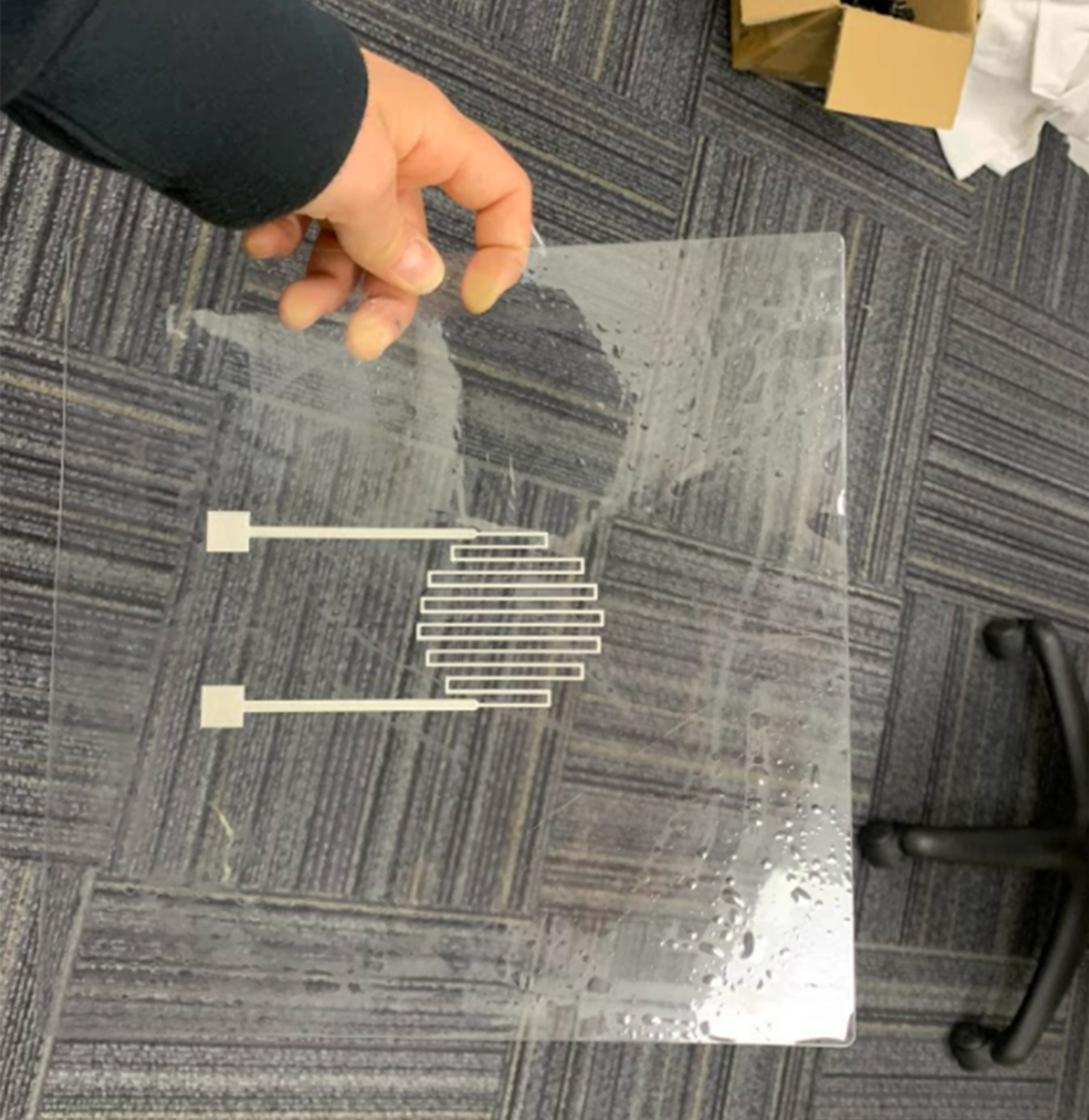
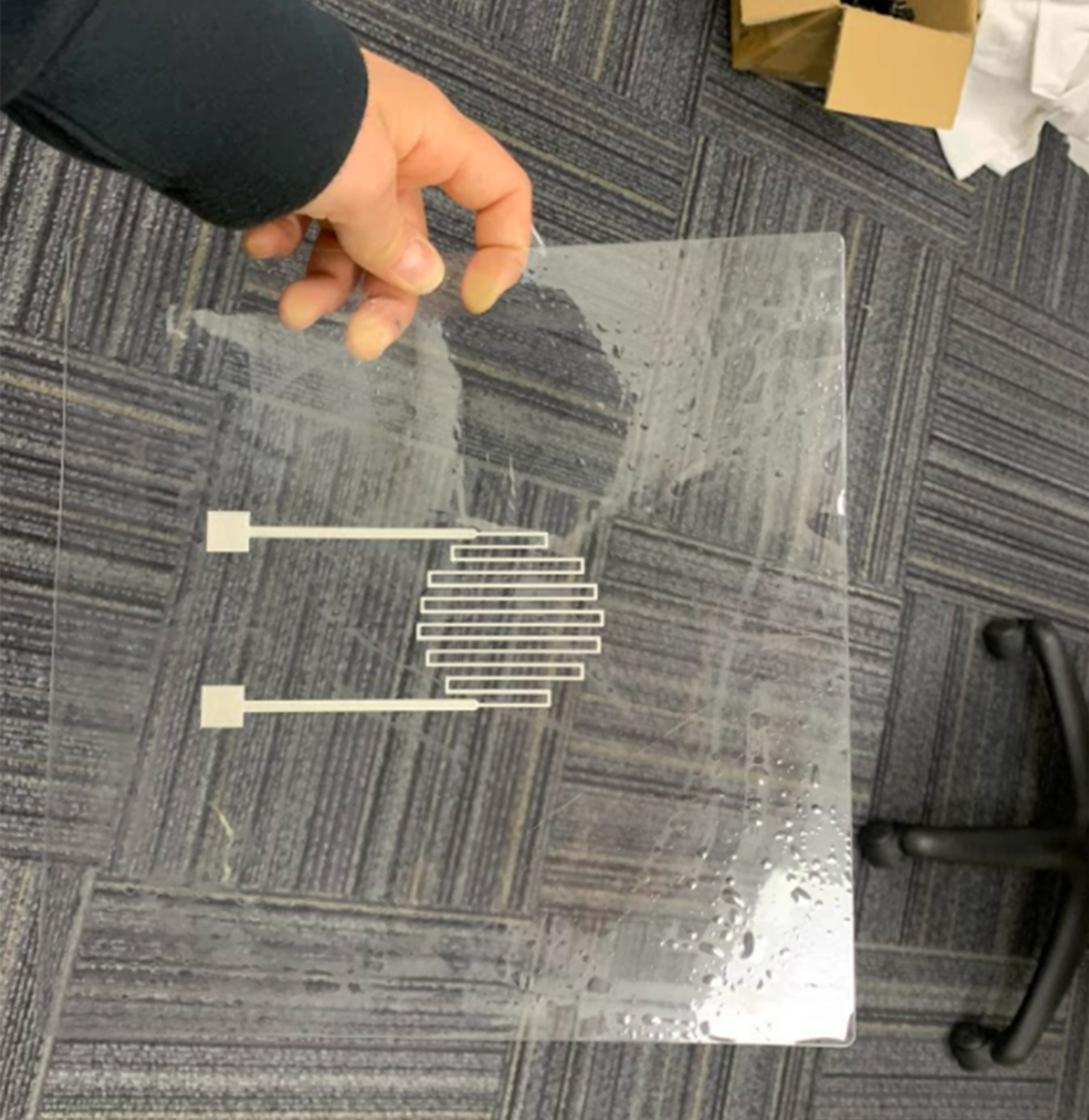
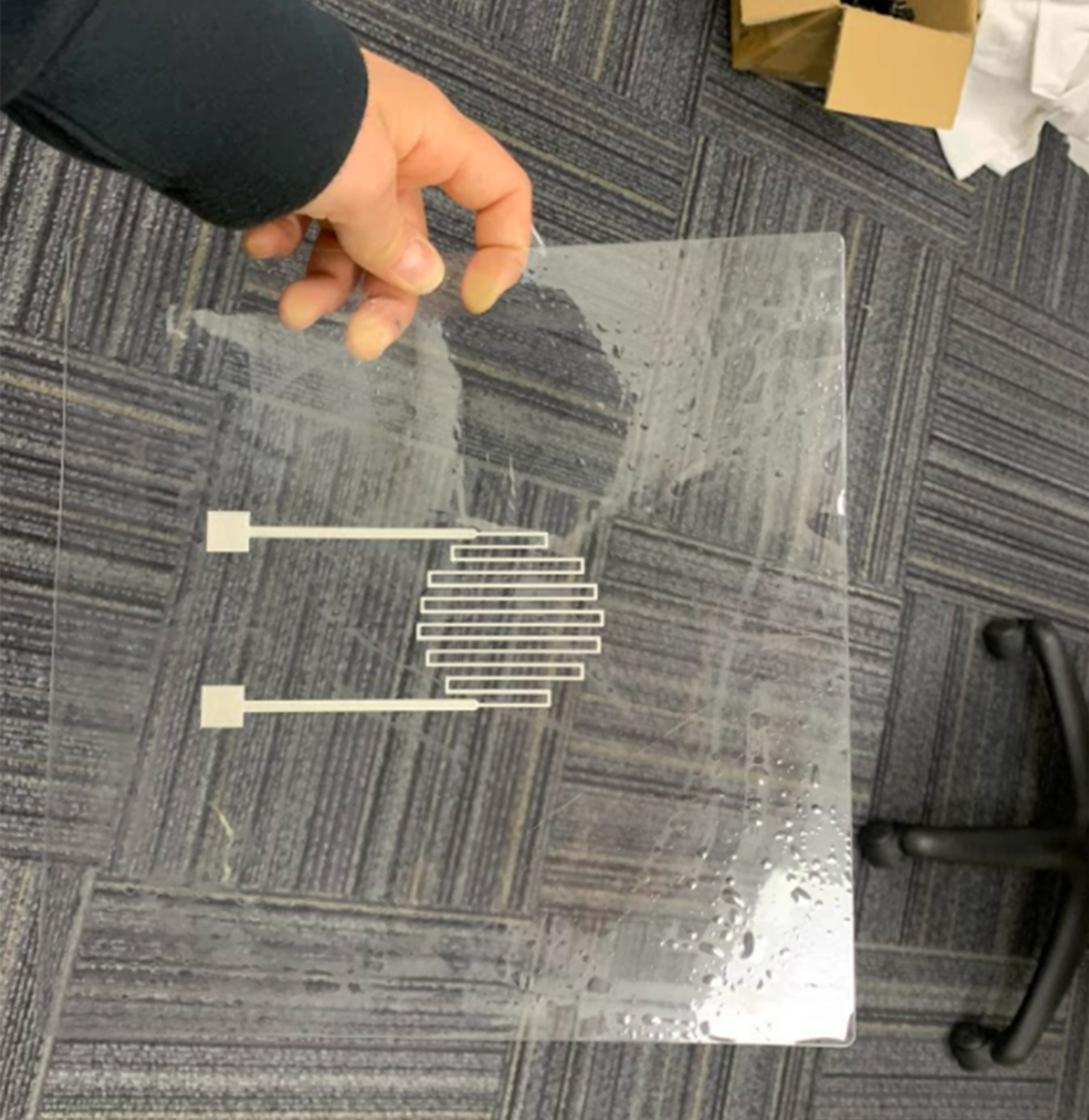
Designing a fully conductive trace without breaks
“It took several iterations to achieve a design that ensured a fully conductive trace with no breaks. When the baked print goes into the Mayku Formbox, the substrate is being heated and deformed,” she explained. “There are so many factors to consider. Will the conductive ink be damaged? Will the substrate be damaged? That required a lot of correspondence with people to get information about melting points and what not, including Insulectro, who supplied us with the ink — they really helped out. But the biggest issue was of course the sharp angle of the mold, causing the trace to be deformed to a point where it is no longer conductive. And that’s why I had to gradually reduce that angle and on the trace edges.”
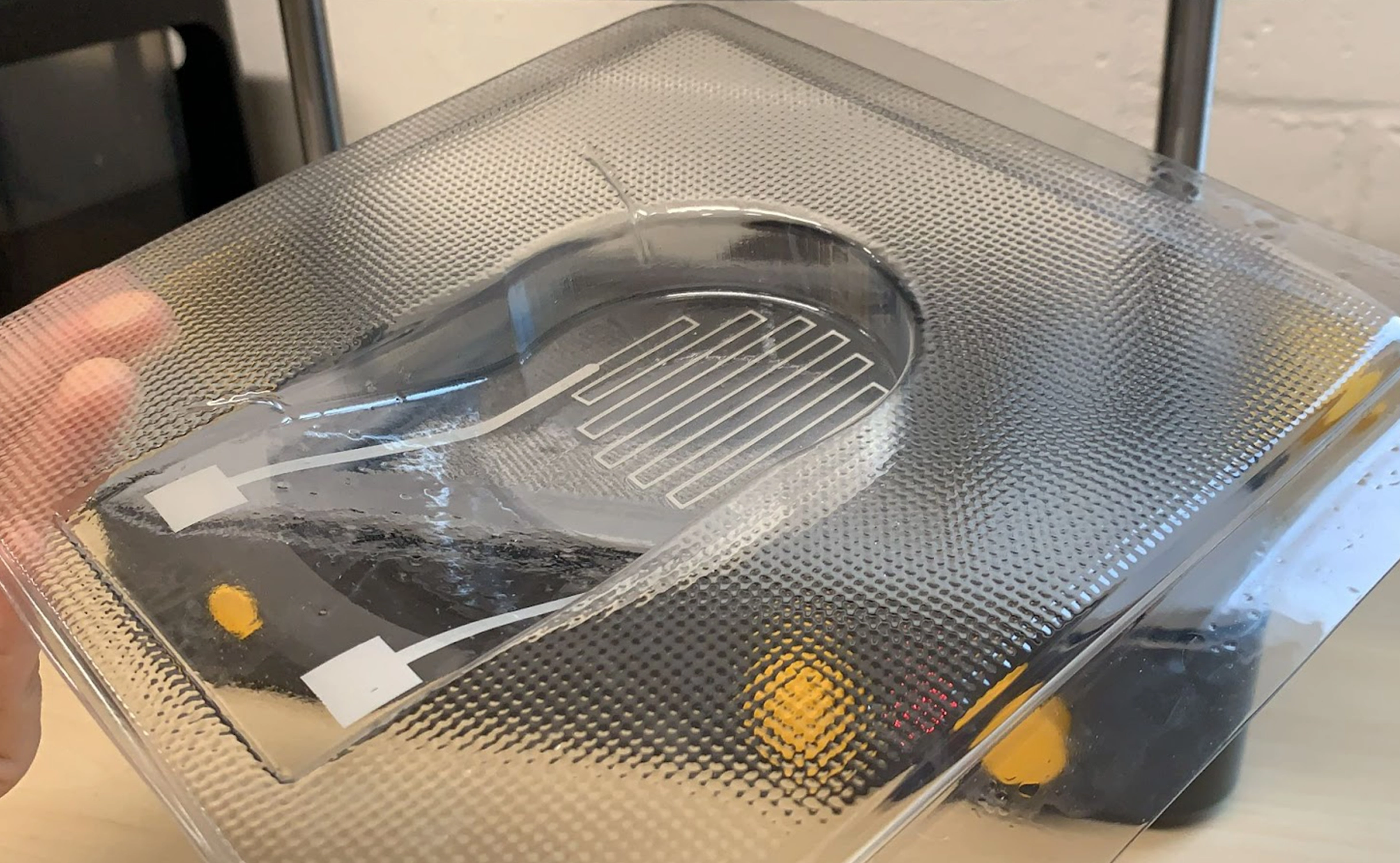
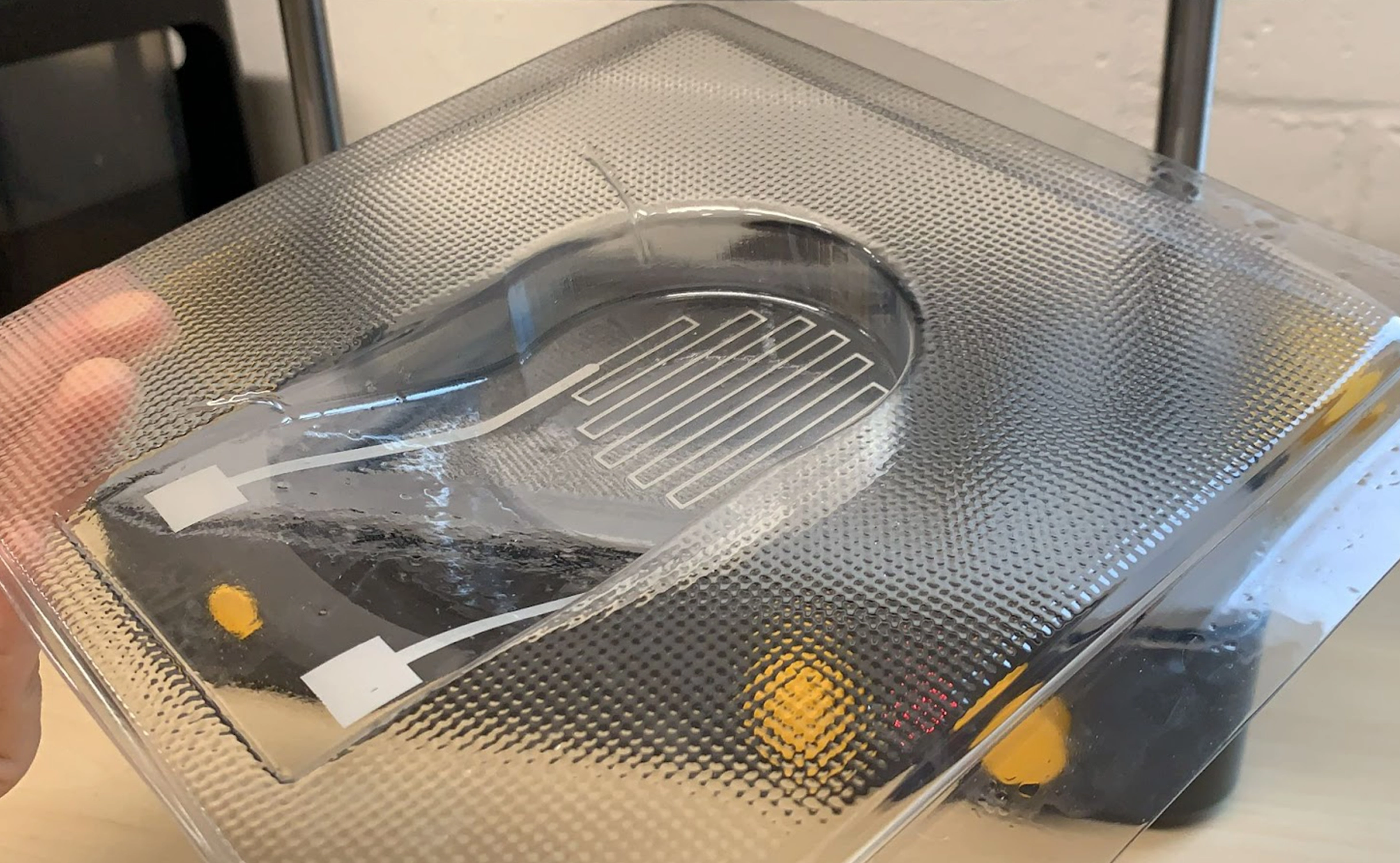
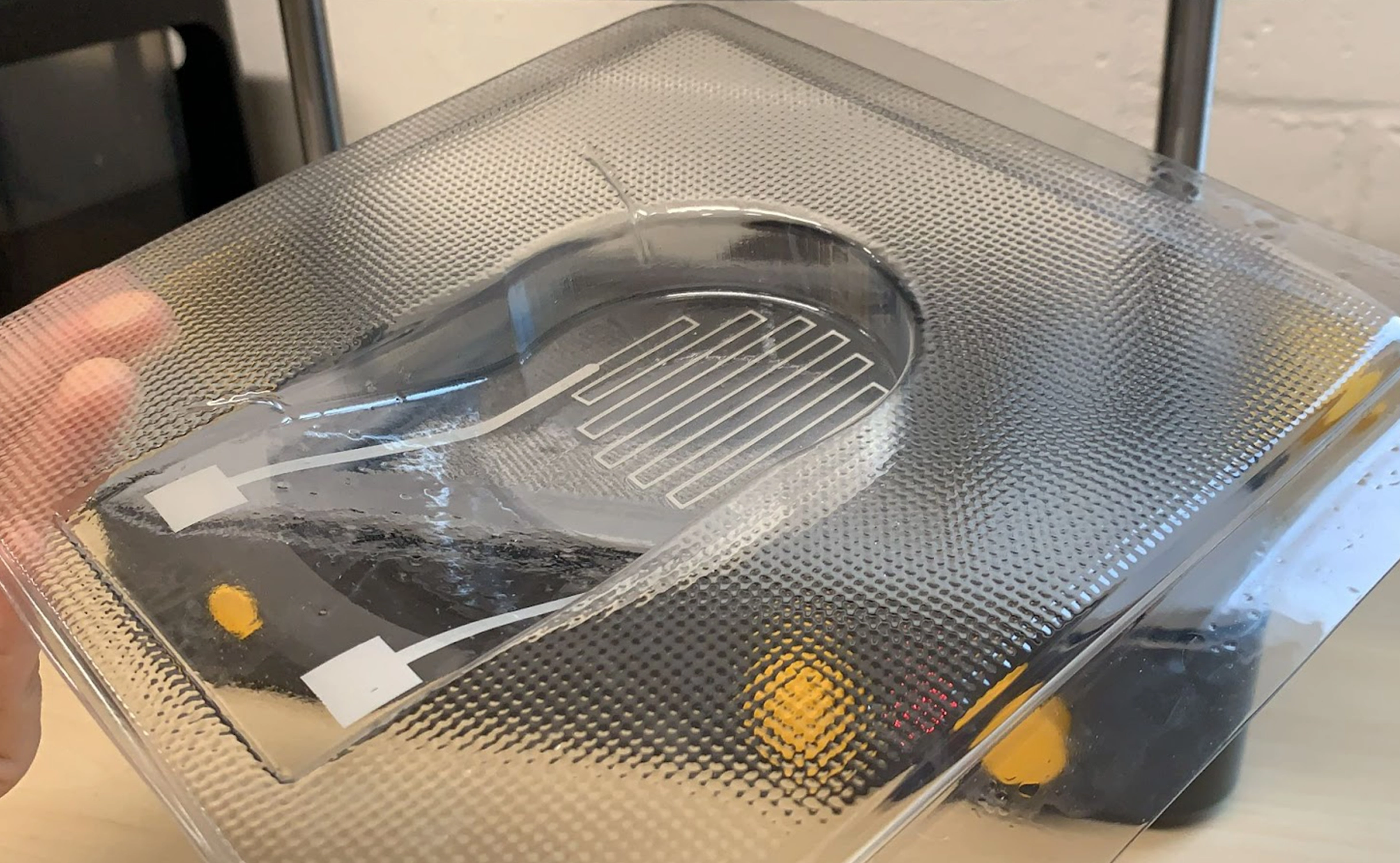
Working with NOVA
Despite the challenges of the project, Duru loved working with NOVA. “Everyday I was excited to use the NOVA just because of how cool it is. The user interface is super easy to use, the modular design and the way everything magnetically clicked into place, the sounds, the lights, etc.” she noted. “I also love NOVA’s ability to work with various substrates. I worked a lot with flexible substrates during my time at Voltera, so the vacuum feature was being used frequently.”
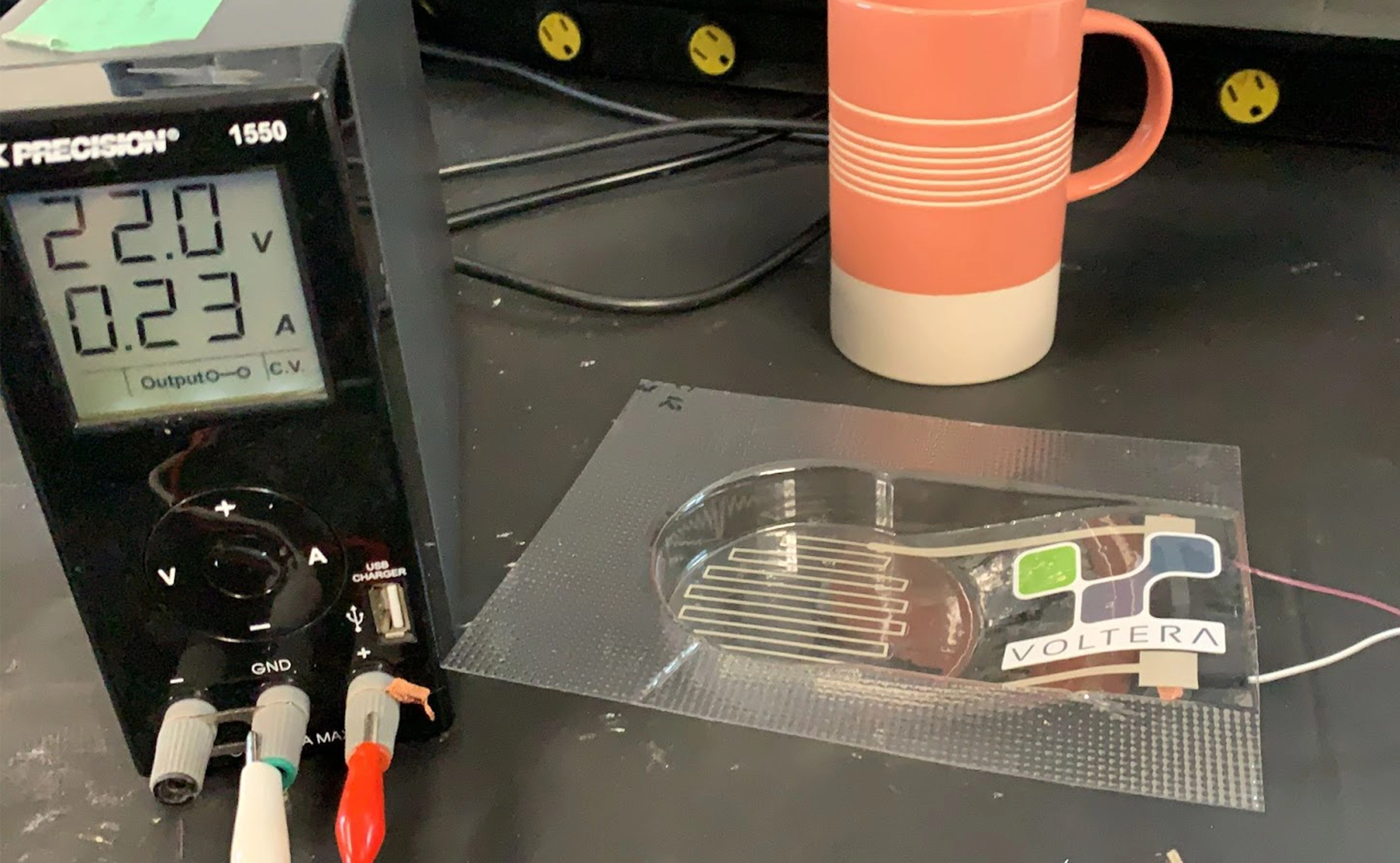
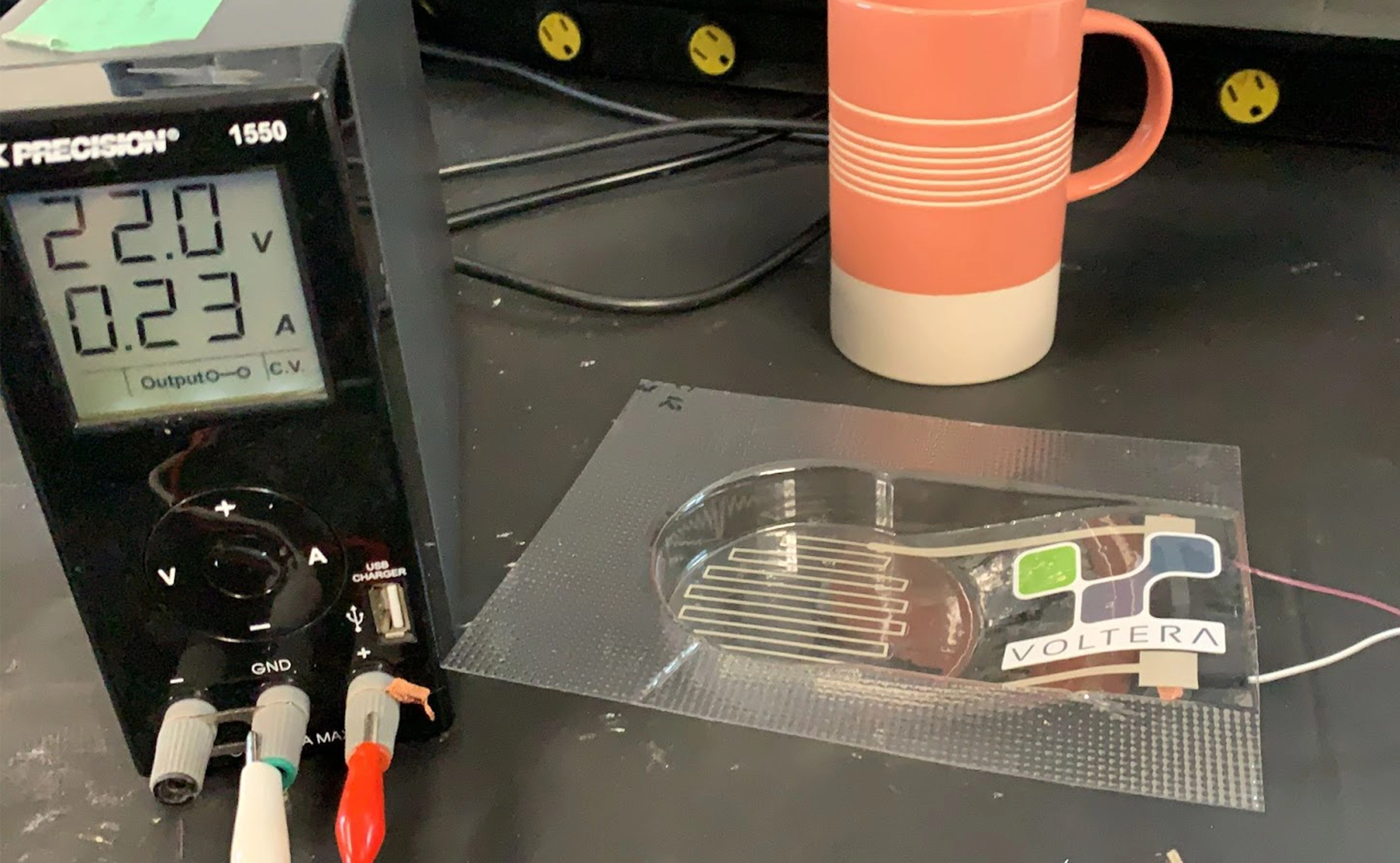
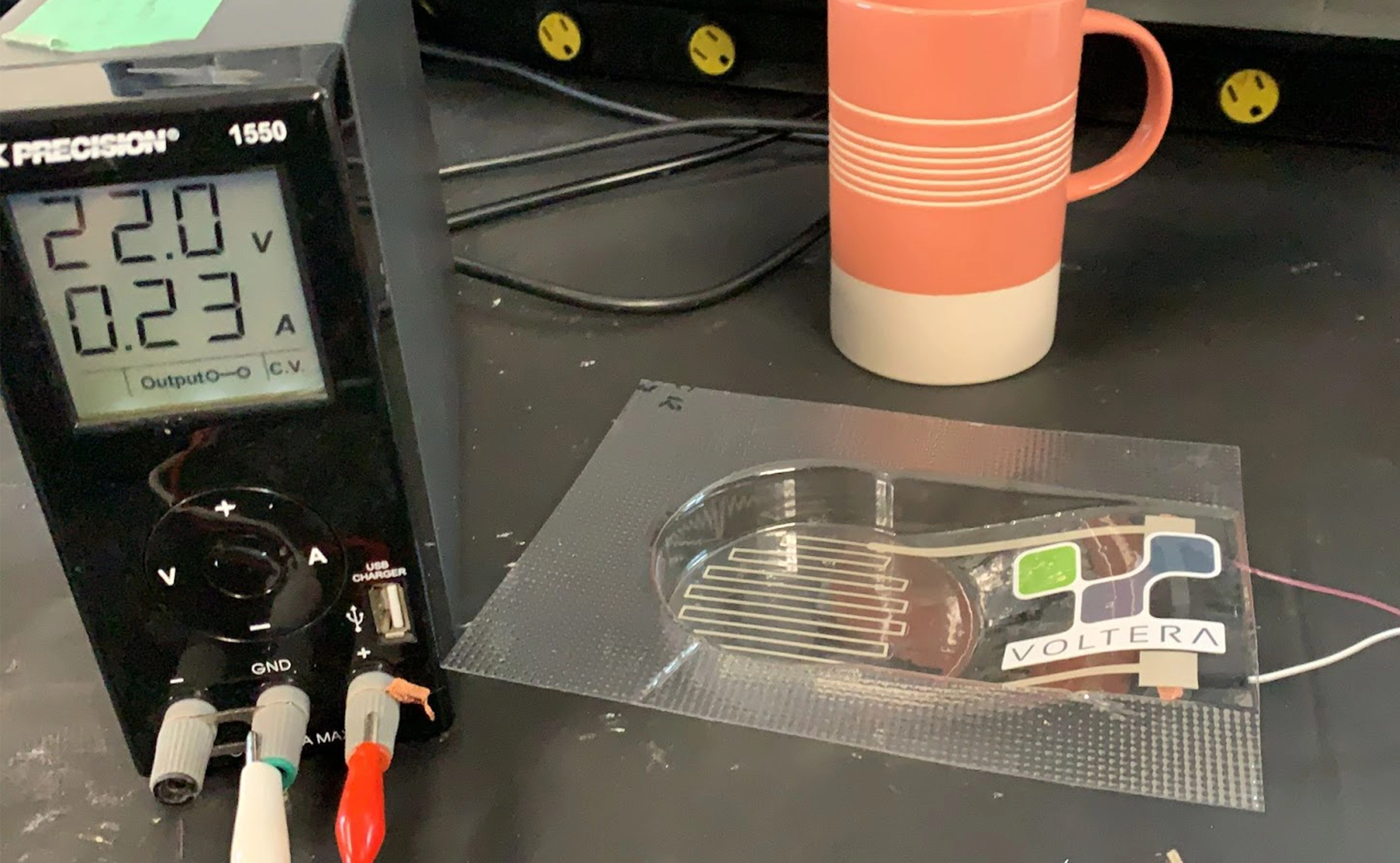
Future applications for in-mold electronics
In Duru’s eyes, there are so many exciting applications for the technology. “In biomedical applications, for example, you could use in-mold electronics to build medical tools or prosthetics that are ergonomic and accessible, with electronic components integrated through in-mold processes — to easily incorporate electronics into things that have awkward shapes, or have been challenging to design using traditional methods. And in cases like these, being able to use NOVA to build electronics that fit a specific, custom shape may be a great advantage.”
The experience of working with NOVA was inspiring for Duru, and piqued her interest in electronics innovation. “During my time working with NOVA I gained a big interest in additive electronics and learned a foundation of knowledge (about conductive inks, substrates, rheology) that I still bring up at every chance I get,” she said. “I also got inspired to tinker more. Having access to benchtop tools like the NOVA would enable people to tinker freely and try new things — which is beneficial to the engineering iteration process.”
The experience of an intern at Voltera
Working at Voltera also impacted Duru’s career aspirations. “Many of my co-op placements have been R&D specific. During my future career I think I’d like to work in spaces where I have access to tools like NOVA while doing R&D work and product development. My perspective has shifted to appreciate the potential of additive electronics in biomedical applications — for example the in-sole pressure sensor project I did, or things like wearable biomarker sensors.”
And now, thanks to her in-mold mug heater, Duru can iterate for hours and never have to worry about her coffee getting cold.
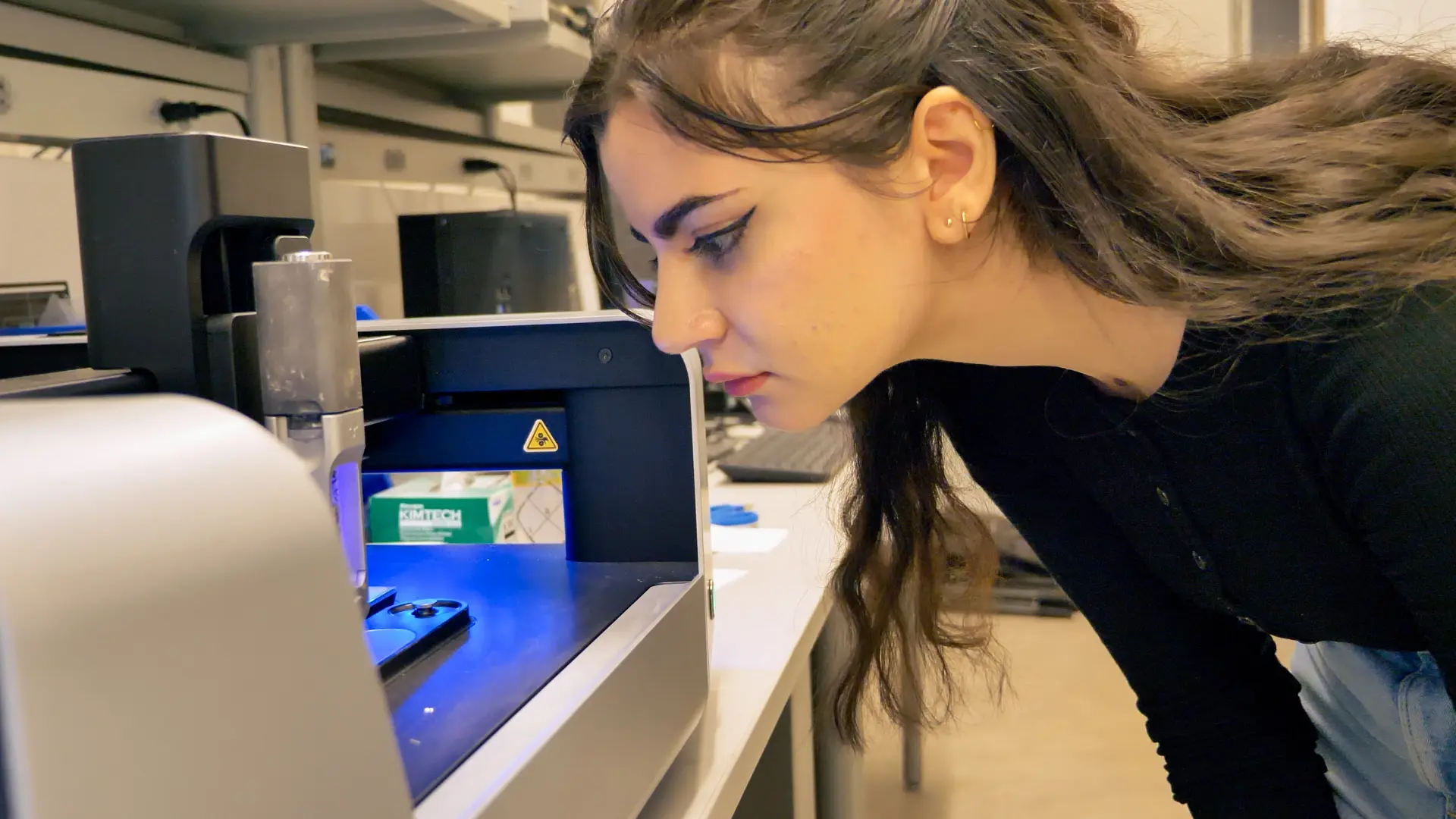
Check out our Customer Stories
Take a closer look at what our customers are doing in the industry.
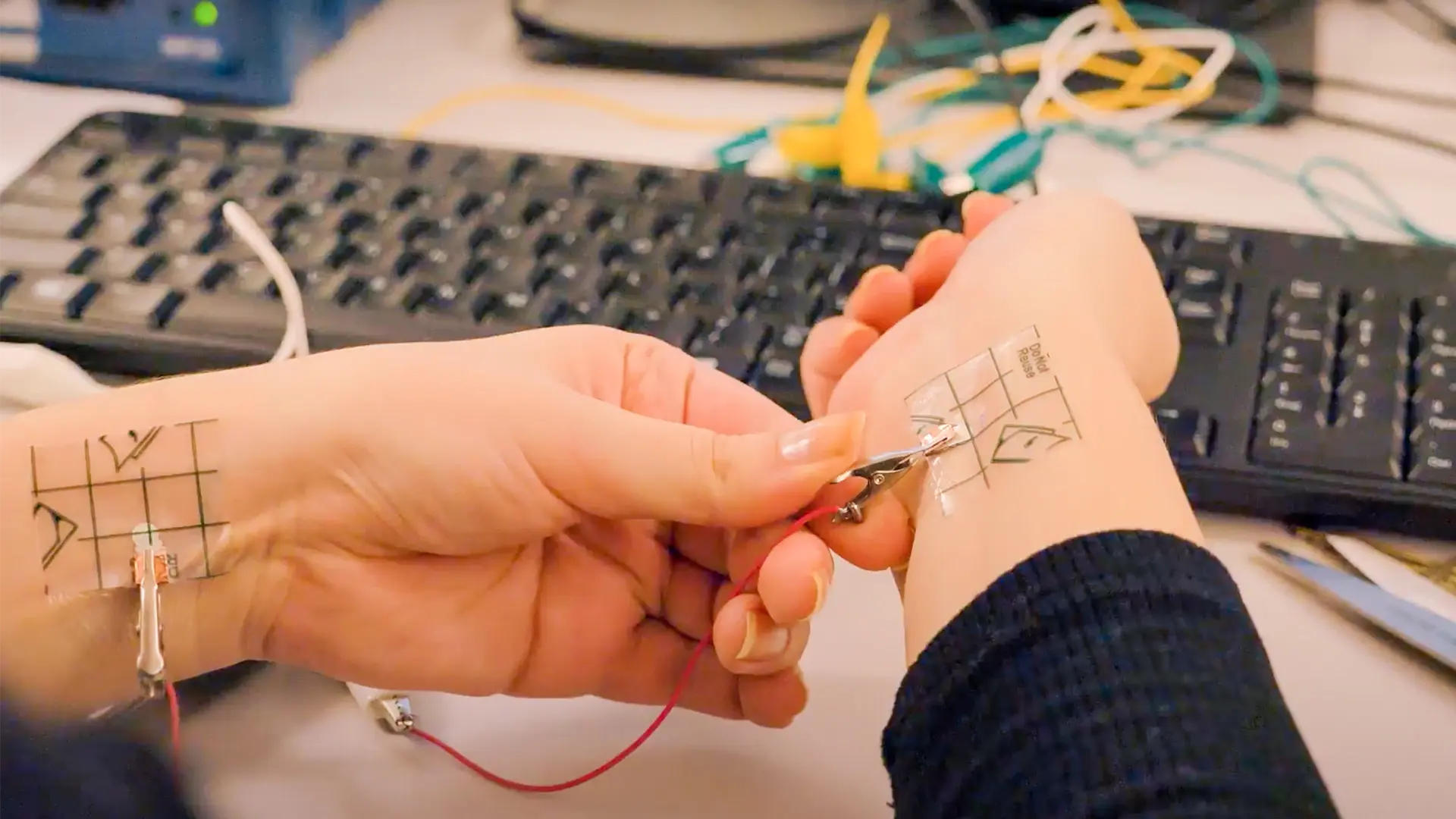