What Are Functional Inks?
Functional inks are the backbone of printed electronics, transforming ordinary substrates like plastic, paper, or textiles into smart, interactive devices. Functional inks add specialized properties — conductivity, sensing, or thermal regulation — to create circuits that power everything from wearable sensors to electromagnetic interference (EMI) shielding.
Types of functional inks
Functional inks are typically divided into three categories based on their main use: conductive, non-conductive, and specialty inks.
Conductive inks
Conductive ink forms the electrical connection of printed electronics. These inks are composed of conductive fillers — such as silver, copper, or carbon — dispersed in a liquid vehicle containing binders, solvents, and additives that determine the viscosity, surface tension, wettability, and adhesion of the ink [1].
Metal-organic decomposition (MOD) inks
MOD ink contains metal-organic precursors dissolved in organic solvents, or complexing agents like amines or carboxylic acids. When heated, these compounds break down, forming a pure conductive metal layer. MOD inks are compatible with a variety of printing technologies, including direct ink writing (DIW), inkjet, aerosol jet, and screen printing [2].
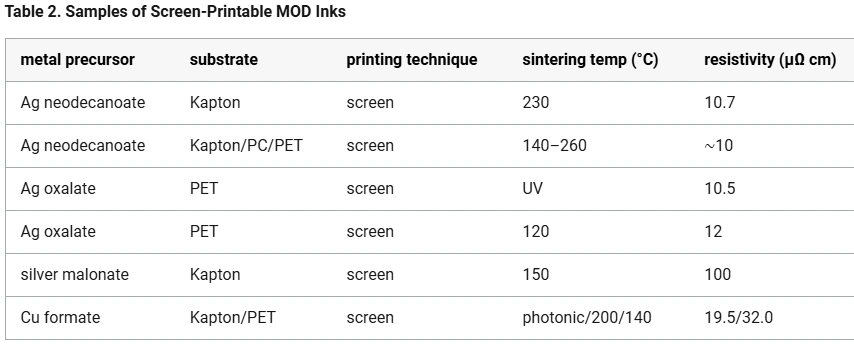
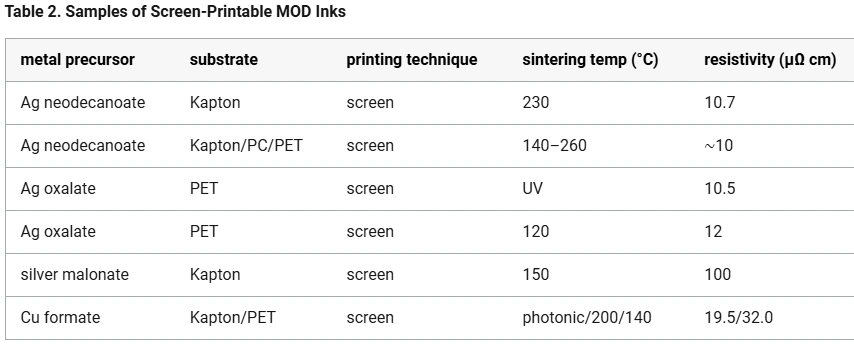
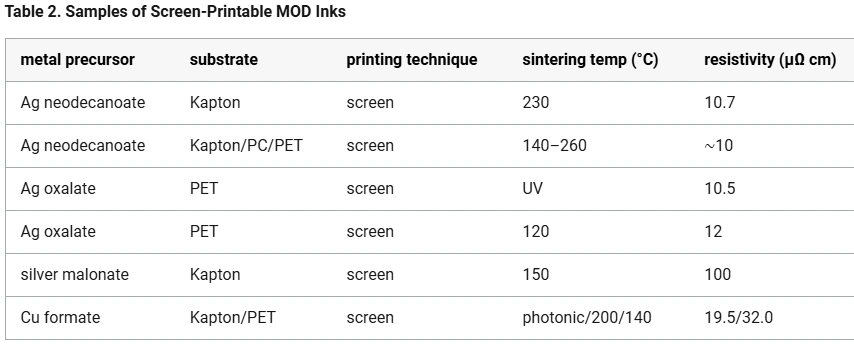
These inks stand out because they can be processed at lower temperatures (usually below 150°C), making them perfect for flexible substrates like plastics. Silver MOD inks can achieve very high conductivity, similar to solid silver, after heating at just 90°C. Copper MOD inks also perform well but need special environments to prevent oxidation [1].
However, MOD inks typically experience significant volume loss after solvent evaporation, potentially leading to voids and conductivity issues, and require multiple print-and-sinter cycles to achieve the desired conductivity [2].
Nanoparticle metal inks
Nanoparticle inks use tiny metal particles (silver, copper, platinum, or gold) suspended in solvents. These inks offer excellent conductivity due to their high metal content (70-97.5% by weight). They're popular because they quickly solidify under laser or photonic sintering, making them great for flexible electronics [1][3].
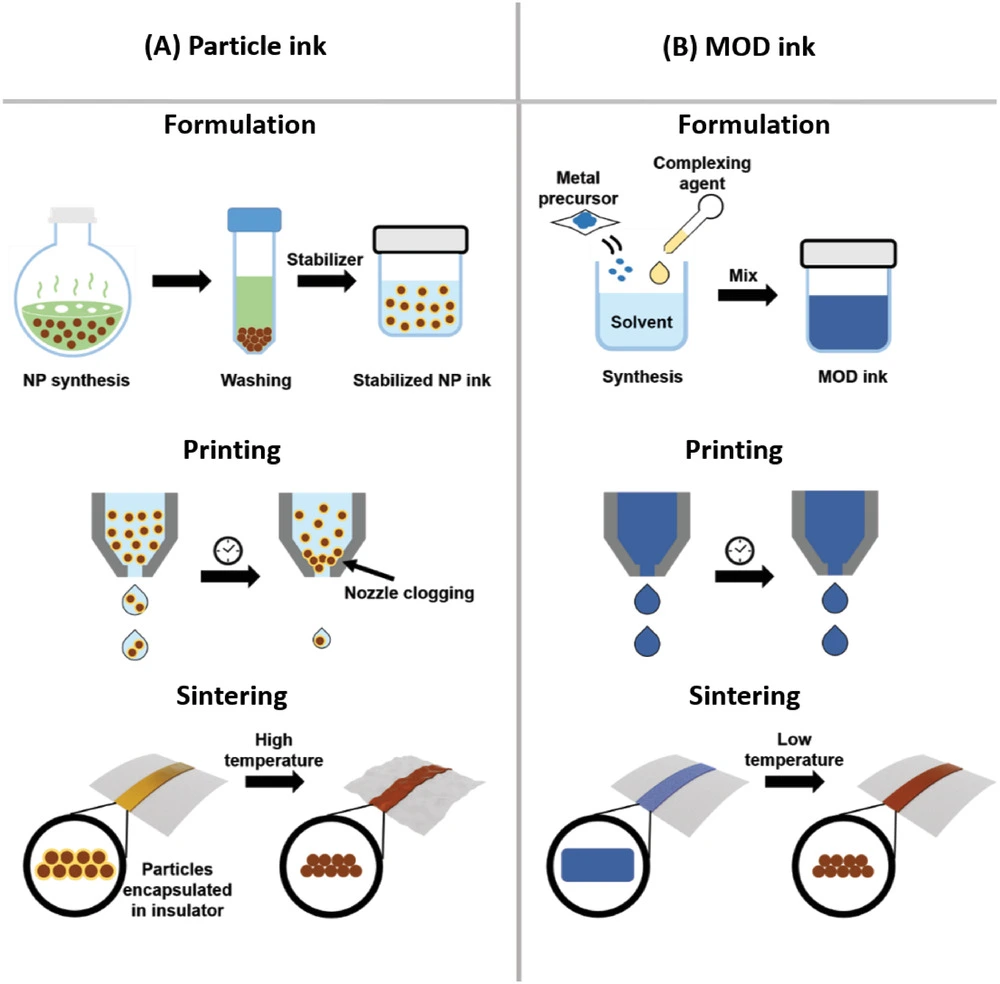
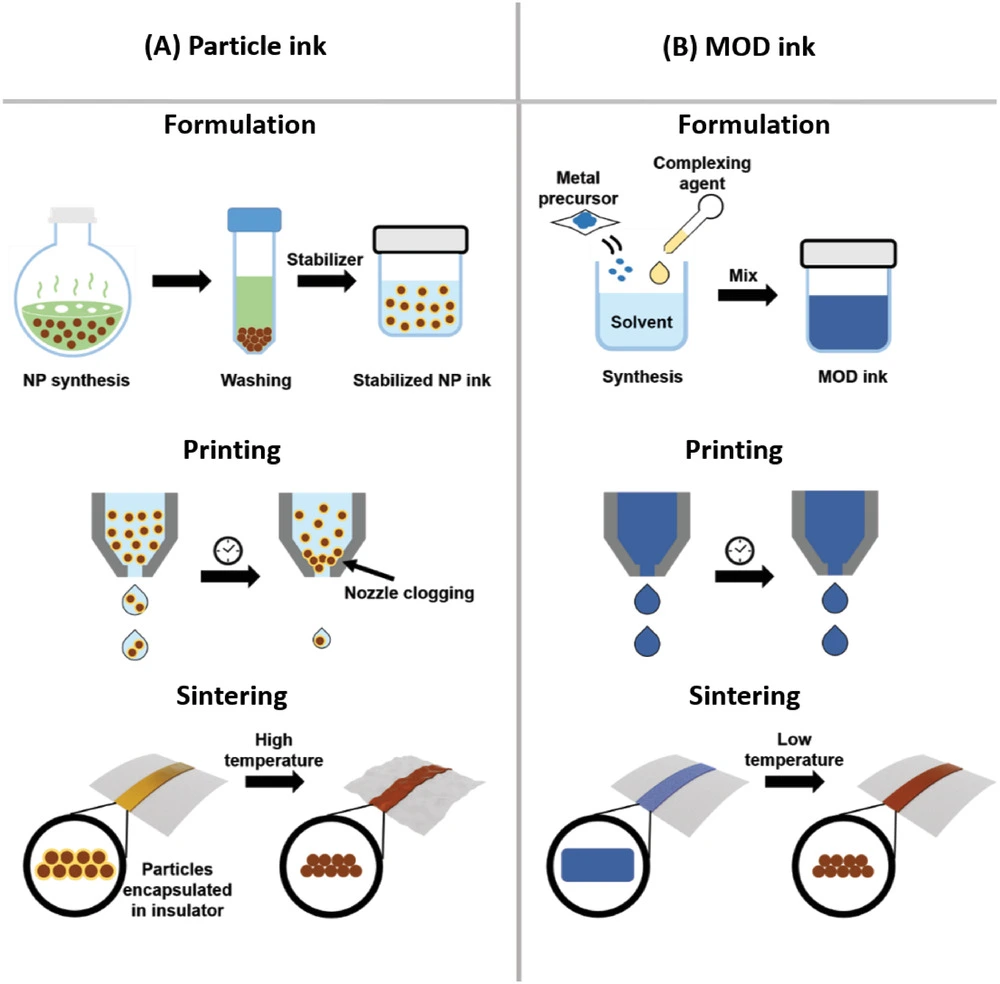
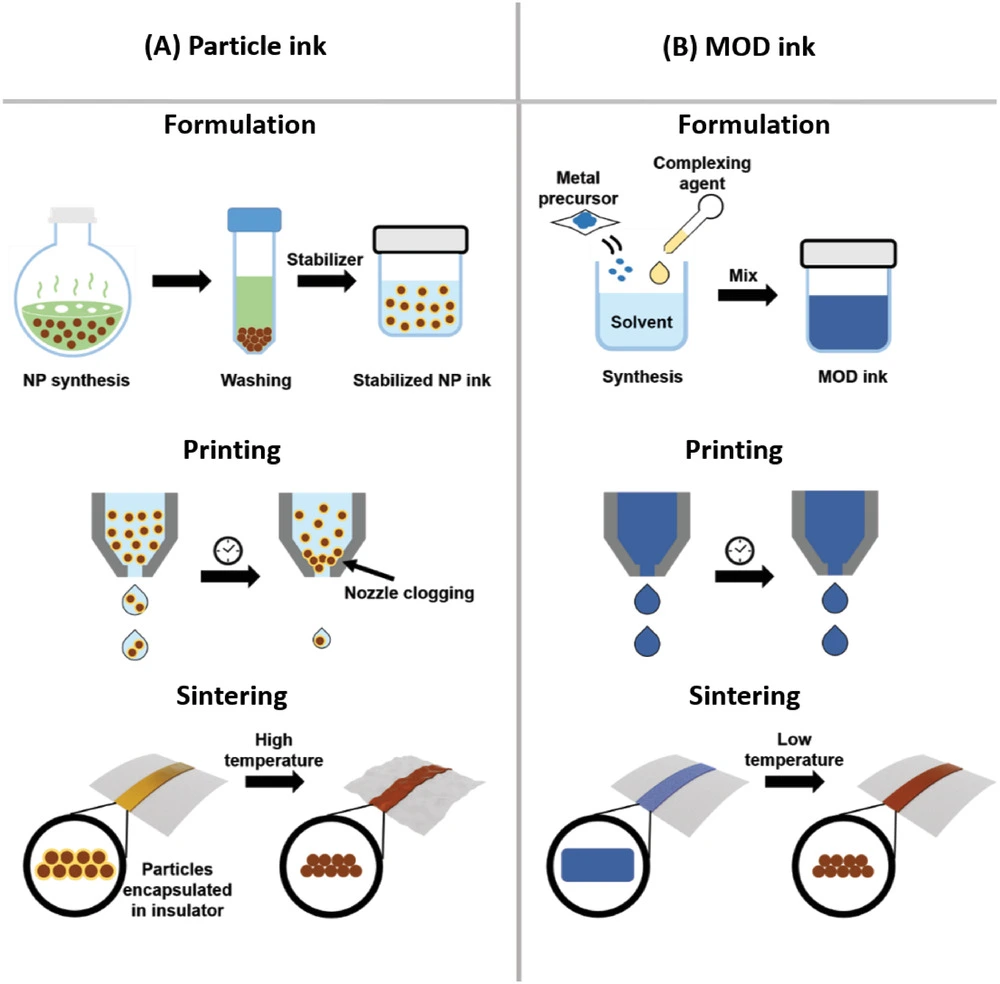
However, nanoparticle inks can be tricky to produce. They often contain chemicals (surfactants) to prevent particle clumping, which must be removed at high temperatures, making it a challenge when working with heat-sensitive substrates like plastics [1].
Non-conductive inks
Non-conductive inks don’t carry electricity but are crucial for protecting and supporting electronic circuits. These inks include encapsulants to protect against moisture, bioinks that are safe for human skin, insulating inks for electrical isolation, and adhesive inks for bonding.
Adhesive inks
Adhesives hold layers of printed electronics together or attach electronic components directly to printed surfaces. Recent innovations include silicone-based adhesive inks that quickly cure without shrinking, ensuring stable and durable structures. This advancement greatly reduces curing time, prevents distortion, and improves adhesion between layers, solving common issues with traditional adhesives formulations [5].
Specialty inks
Specialty inks provide unique capabilities beyond electrical conductivity. Thermal inks help regulate temperature, enabling products like self-warming clothing or anti-fogging mirrors. Optical inks control light for anti-glare screens or OLED displays. EMI shielding inks, typically made with silver or carbon, protect electronics in industries ranging from consumer electronics to aerospace.
Glass inks
Glass ink is an exciting specialty ink used for advanced optical applications, like lenses or fiber optics. Recent research demonstrated how DIW technology can print water-sensitive borosilicate glass inks using fine glass powder mixed in hydrogel. Although currently opaque due to air pockets formed during heat treatment, ongoing research aims to make printed glass clearer, unlocking its potential for high-quality optical devices [6].
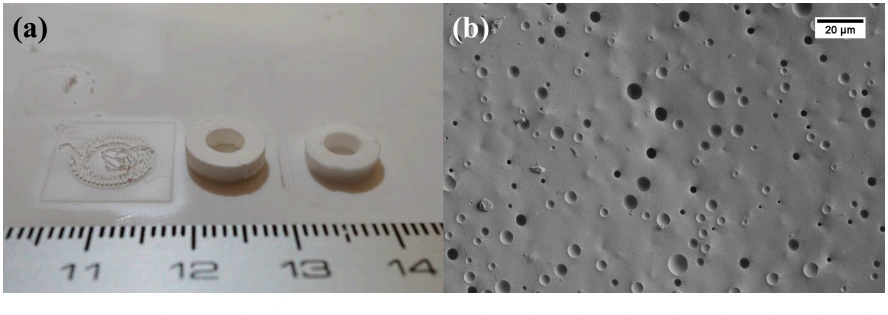
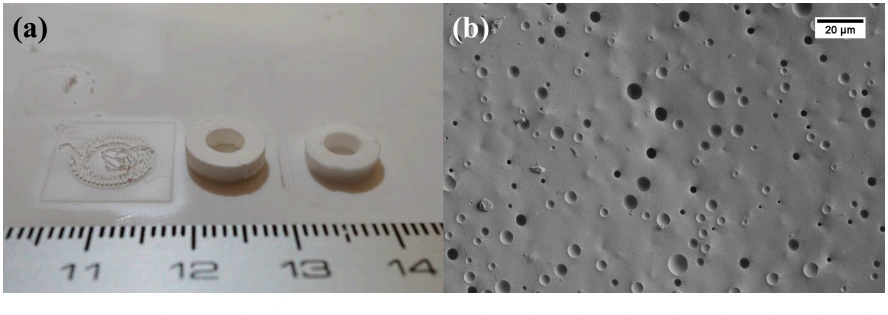
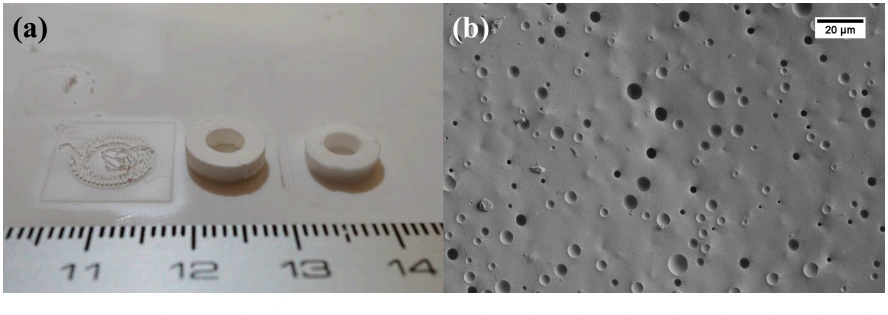
Choosing the right substrate for functional inks
The choice of material you print on significantly impacts ink performance. Rigid substrates like glass or ceramics tolerate high temperatures, and are ideal for MOD inks in precision electronics. Flexible substrates like polyimide films, paper, or textiles match well with lower-temperature inks, enabling flexible and wearable electronics.
Formulating functional DIW inks
Direct ink writing has been identified as the most versatile additive manufacturing technique for developing functional inks, allowing single-layer microscale circuits to multi-material, multilayer structures [7].
Successful DIW inks balance printability with functionality, which involves careful control of ink flow (rheology), ingredients, and curing [8].
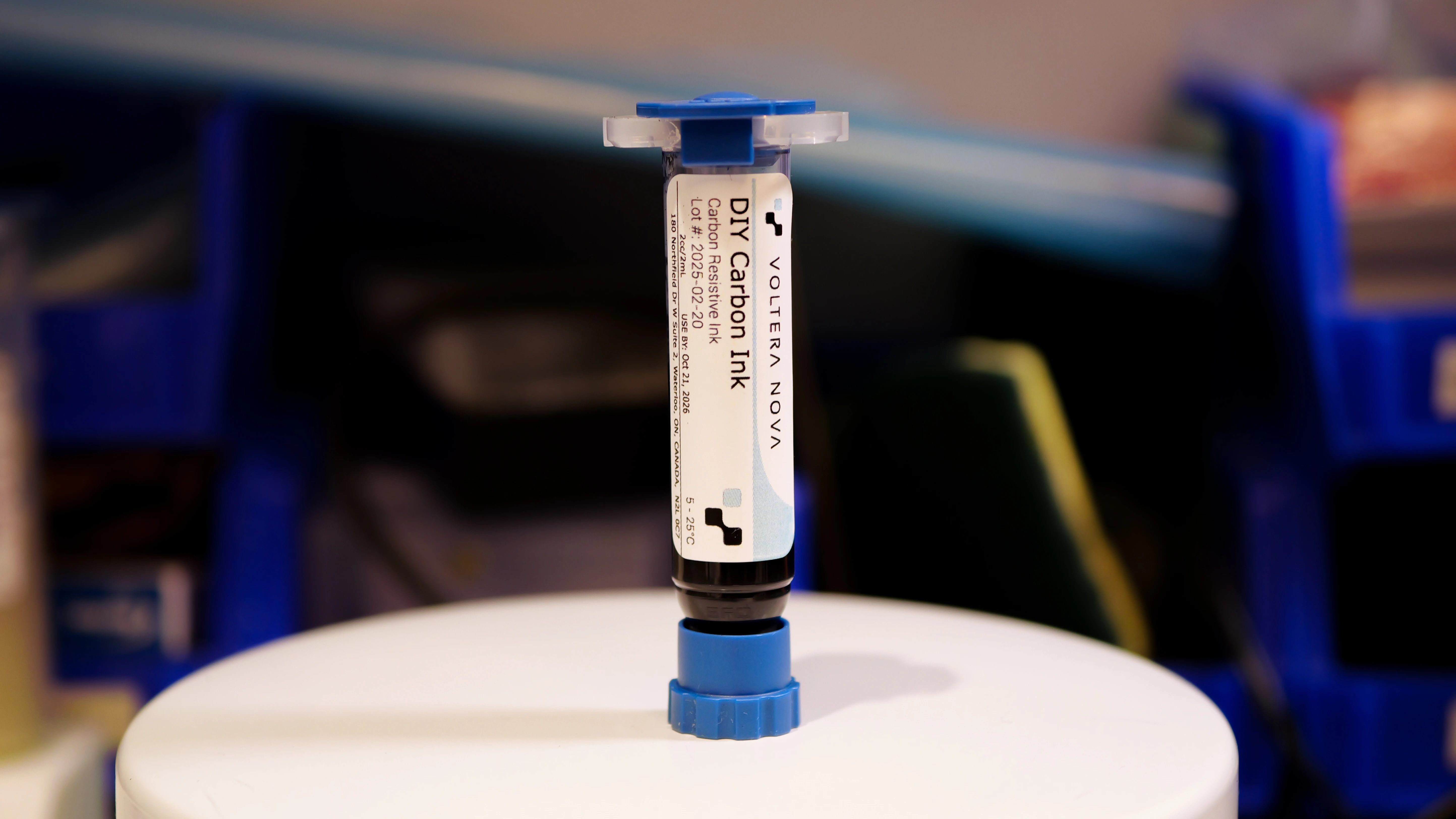
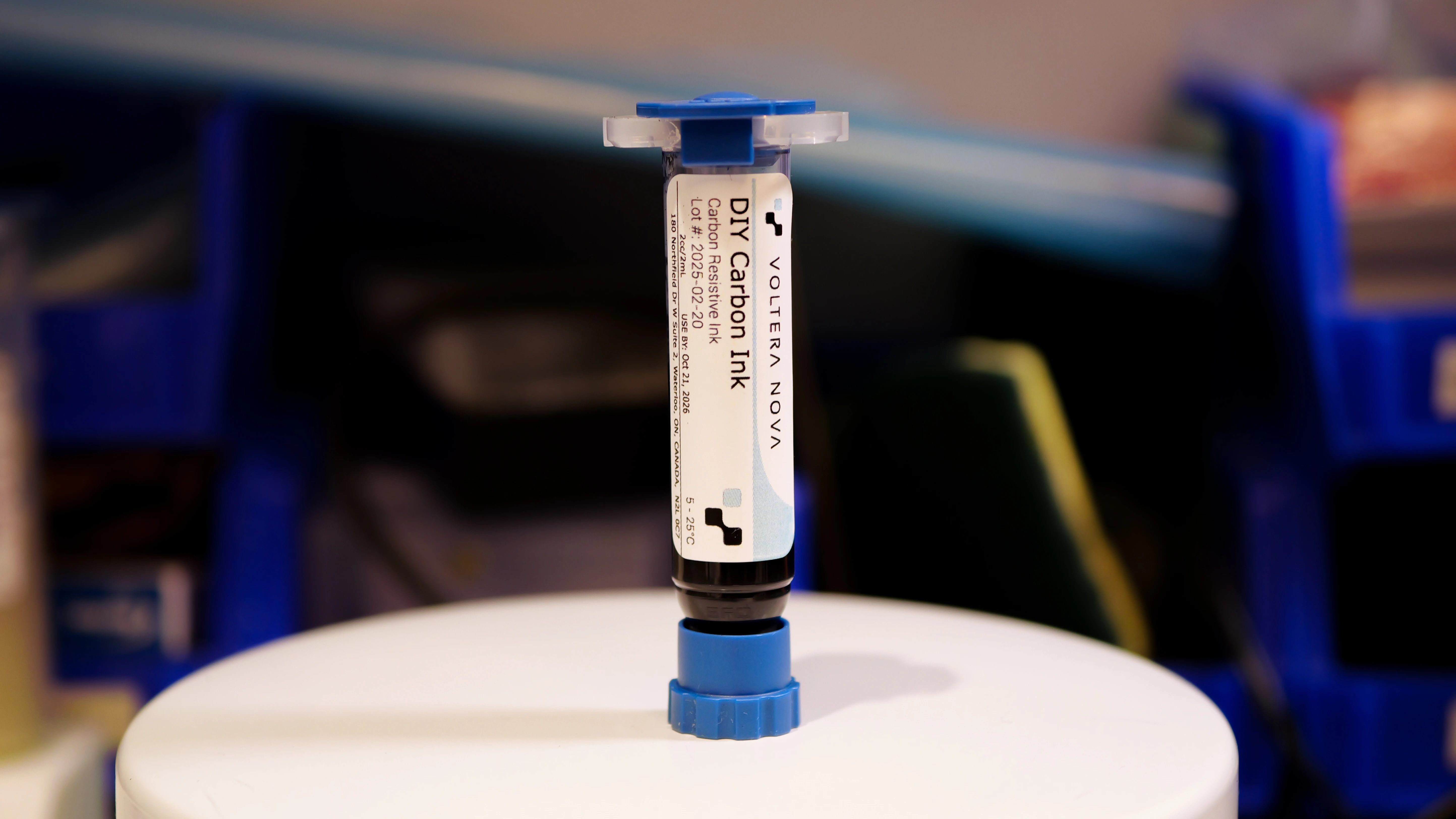
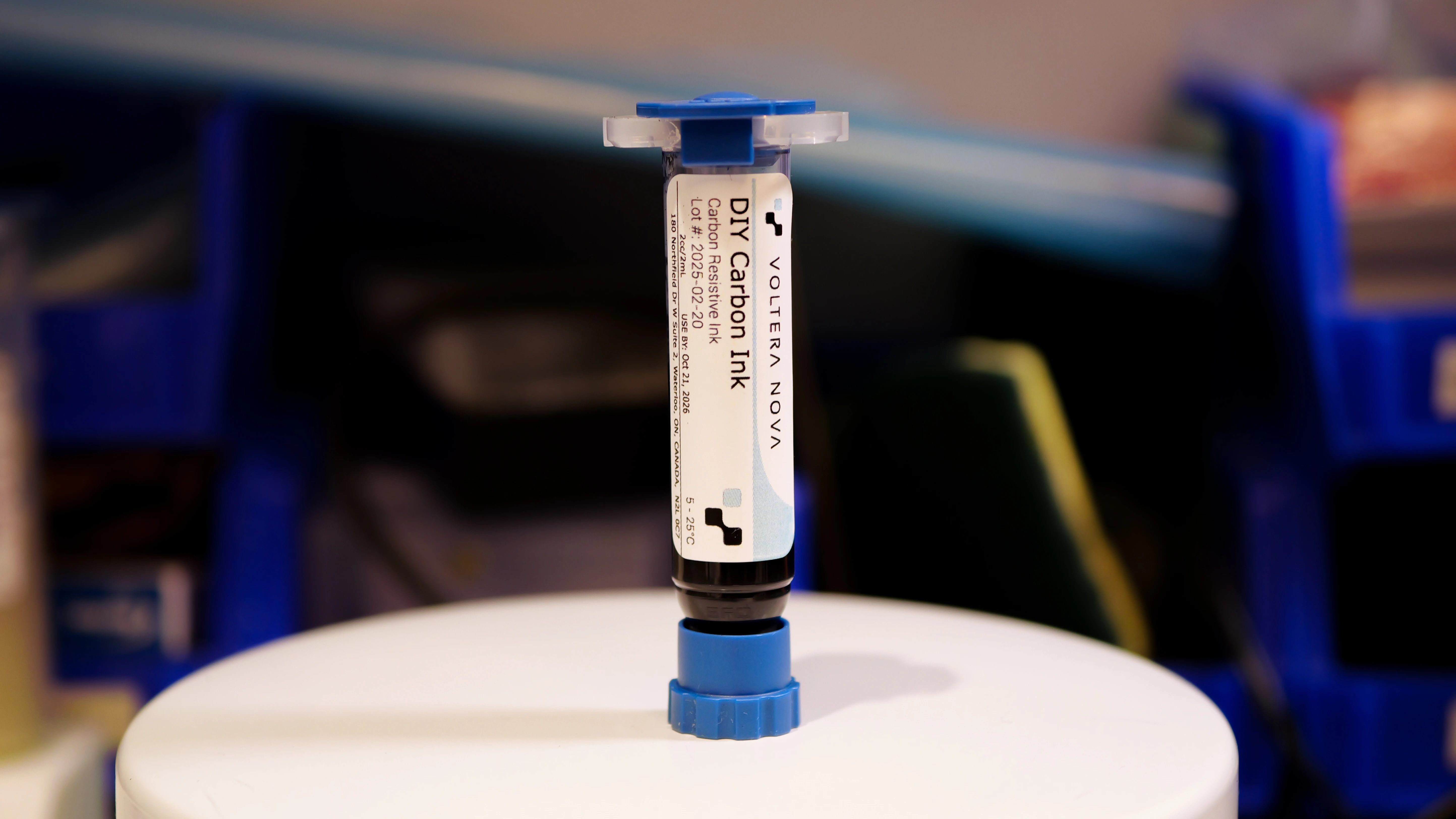
Rheological properties
To print smoothly, inks must flow easily when pressure is applied but quickly stiffen after printing. This characteristic, known as shear-thinning, typically involves adding fine particles like silica or ceramic powders, which temporarily separate under pressure and quickly regroup afterward, helping the ink hold its shape [8].
Ink composition
Ink composition is a careful balance of binders, solvents, and functional additives tailored to the ink’s end use. For example, while conductive inks prioritize high filler loading for electron flow, adhesives emphasize polymer elasticity.
Curing and post-processing
Different inks require specific curing methods after deposition. For instance, air-dry inks solidify as solvents evaporate, while UV-cure inks rapidly harden under ultraviolet light. Choosing an appropriate curing method is essential to maintain the ink's intended functionality.
Functional ink supplier and partnership with Voltera
Major suppliers include ACI Materials, Creative Materials, NovaCentrix, and VFP, offering everything from medical-grade nano inks to high-recovery adhesives.
At Voltera, we regularly create specialized electronics with functional inks, including:
- Electroluminescent display (optical ink)
- Flexible multilayer battery (insulating, metal, and adhesive inks)
- Wearable heating element (stretchable resistive ink)
- ECG electrodes (biocompatible gold ink)
Conclusion
Functional inks are reshaping printed electronics, enabling lightweight, flexible, and multi-functional products. From precise MOD inks to specialty glass and adhesive inks, these materials power innovation across IoT, healthcare, wearables, and beyond. With advancements continuing, the future holds greener, more efficient inks driving the electronics of tomorrow.
Want to learn more? Explore these resources:
- Blog: The Ultimate Guide to Choosing Materials for a New Electronics Product
- Video: Developing a Custom Carbon Ink for Printing a Variable Resistor on PET
- Application: Functional ink development
- White paper: Developing a Custom Carbon Ink for Printing a Variable Resistor on PET
Want to discuss your own functional ink development needs? Book a meeting to speak with a technical representative.
References
[1 ] Douglas, S. P., Mrig, S., & Knapp, C. E. (2021). MODs vs. NPs: Vying for the Future of Printed Electronics. Chemistry – a European Journal, 27(31), 8062–8081. https://doi.org/10.1002/chem.202004860.
[2] Kell, A. J., Wagner, K., Liu, X., Lessard, B. H., & Paquet, C. (2023). Advanced Applications of Metal–Organic Decomposition Inks in Printed Electronics. ACS Applied Electronic Materials. https://doi.org/10.1021/acsaelm.3c00910.
[3] de Souza, F. M., & Gupta, R. K. (2023). Smart Multifunctional Nano-inks: Fundamentals and Emerging Applications, https://doi.org/10.1016/B978-0-323-91145-0.00004-9 p. 659.
[4] Choi, Y., Seong, K., & Piao, Y. (2019). Metal−Organic Decomposition Ink for Printed Electronics. Advanced Materials Interfaces, 6(20). https://doi.org/10.1002/admi.201901002.
[5] Garcia, V. J., G. M. Fazley Elahee, Collera, A. K., Thornton, T., Cheng, X., Rohan, S., Howard, E. L., Espera, A. H., & Advincula, R. C. (2023). On the direct ink write (DIW) 3D printing of styrene-butadiene rubber (SBR)-based adhesive sealant. MRS Communications, 13(6), 1266–1274. https://doi.org/10.1557/s43579-023-00436-0.
[6] Nan, B., Przemysław Gołębiewski, Ryszard Buczyński, Galindo-Rosales, F. J., & Ferreira, F. (2020). Direct Ink Writing Glass: A Preliminary Step for Optical Application. Materials, 13(7), 1636–1636. https://doi.org/10.3390/ma13071636.
[7] Yang, G., Sun, Y., Limin qin, Li, M., Ou, K., Fang, J., & Fu, Q. (2021). Direct-ink-writing (DIW) 3D printing functional composite materials based on supra-molecular interaction. Composites Science and Technology, 215, 109013. https://doi.org/10.1016/j.compscitech.2021.109013.
[8] De Smedt, S., Attaianese, B., & Cardinaels, R. (2024). Direct ink writing of particle-based multiphase materials: From rheology to functionality. Current Opinion in Colloid & Interface Science, 75, 101889. https://doi.org/10.1016/j.cocis.2024.101889.
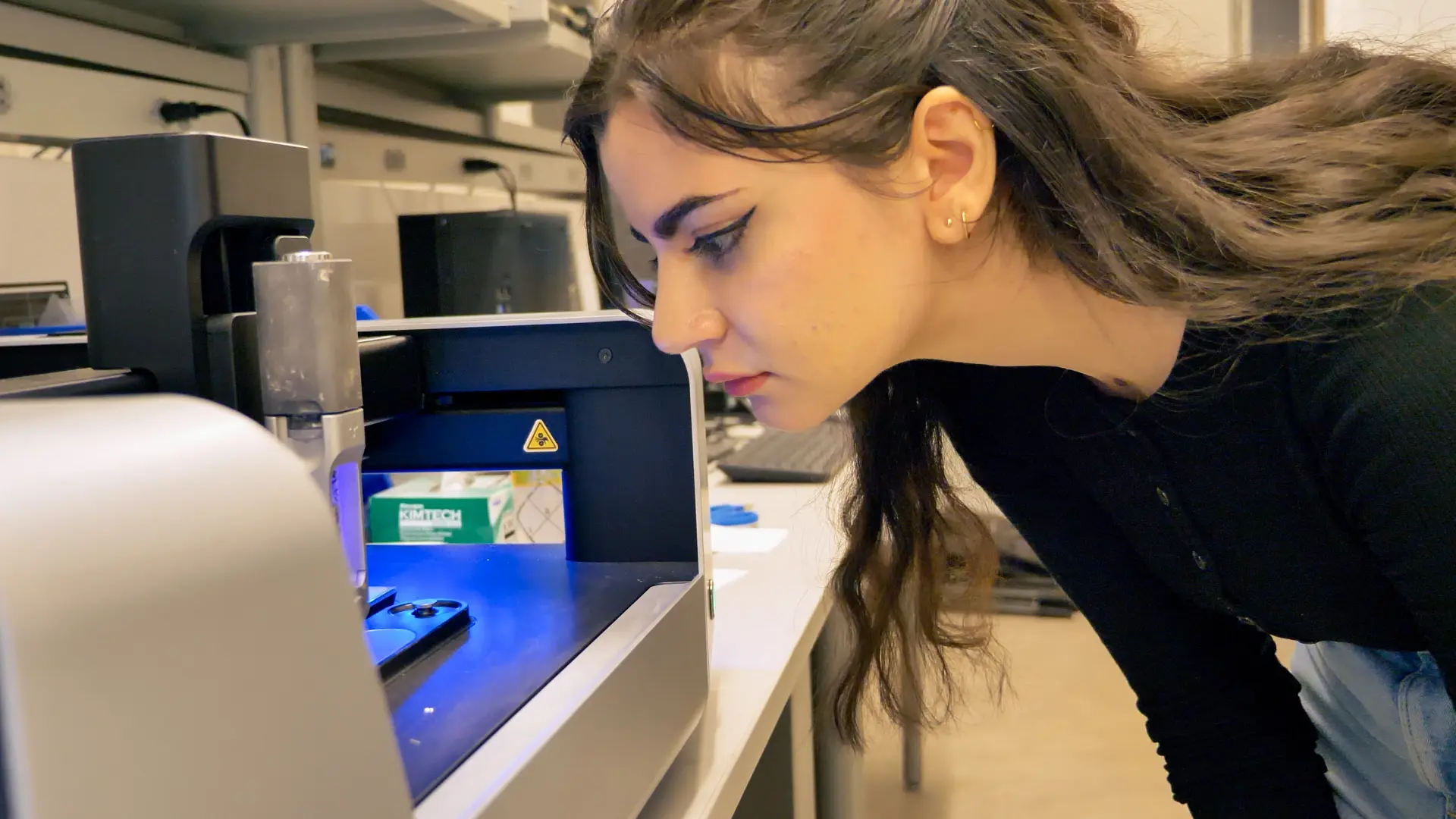
Check out our Customer Stories
Take a closer look at what our customers are doing in the industry.
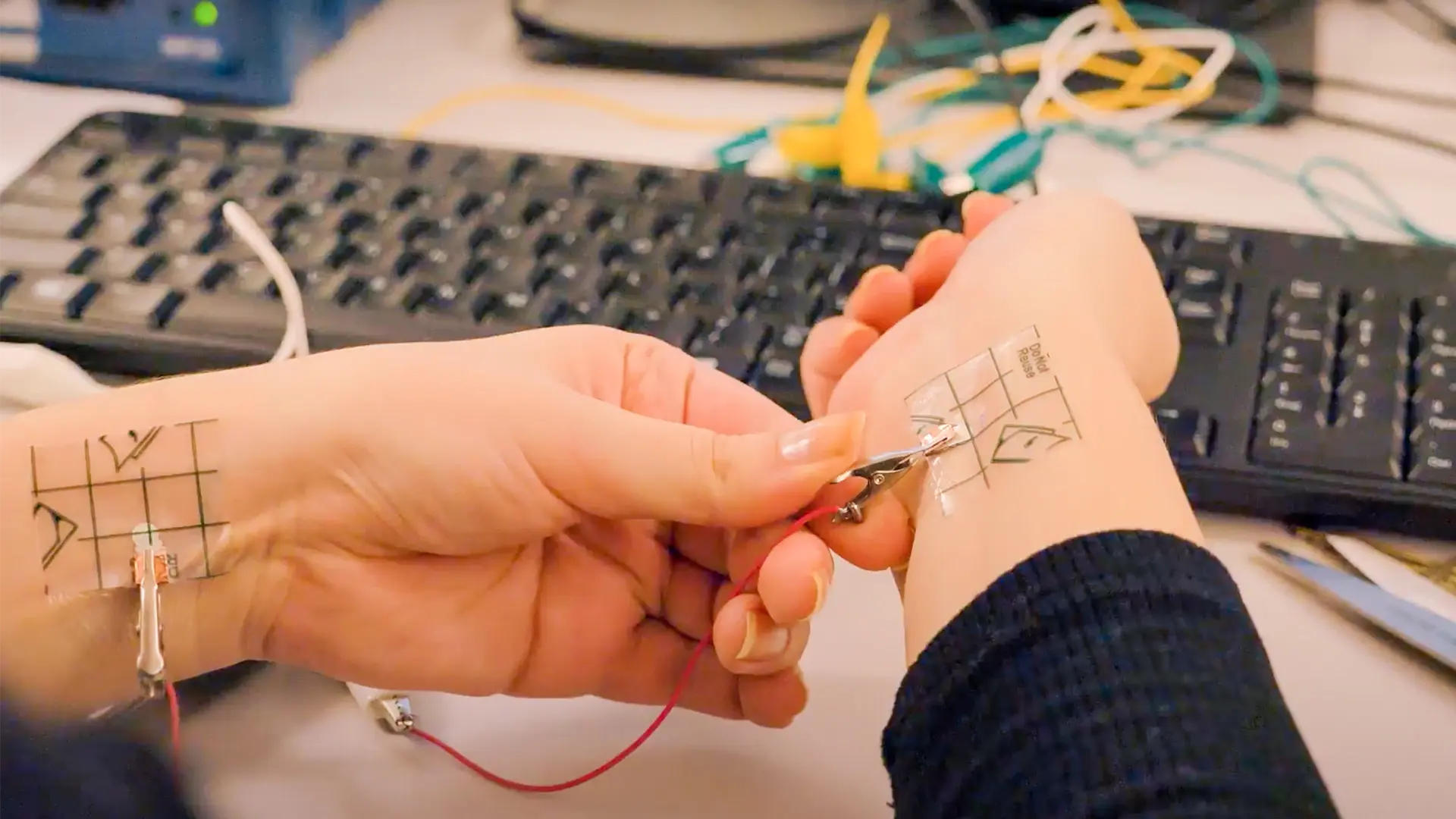