Printed Electronics: What is Inkjet Printing?
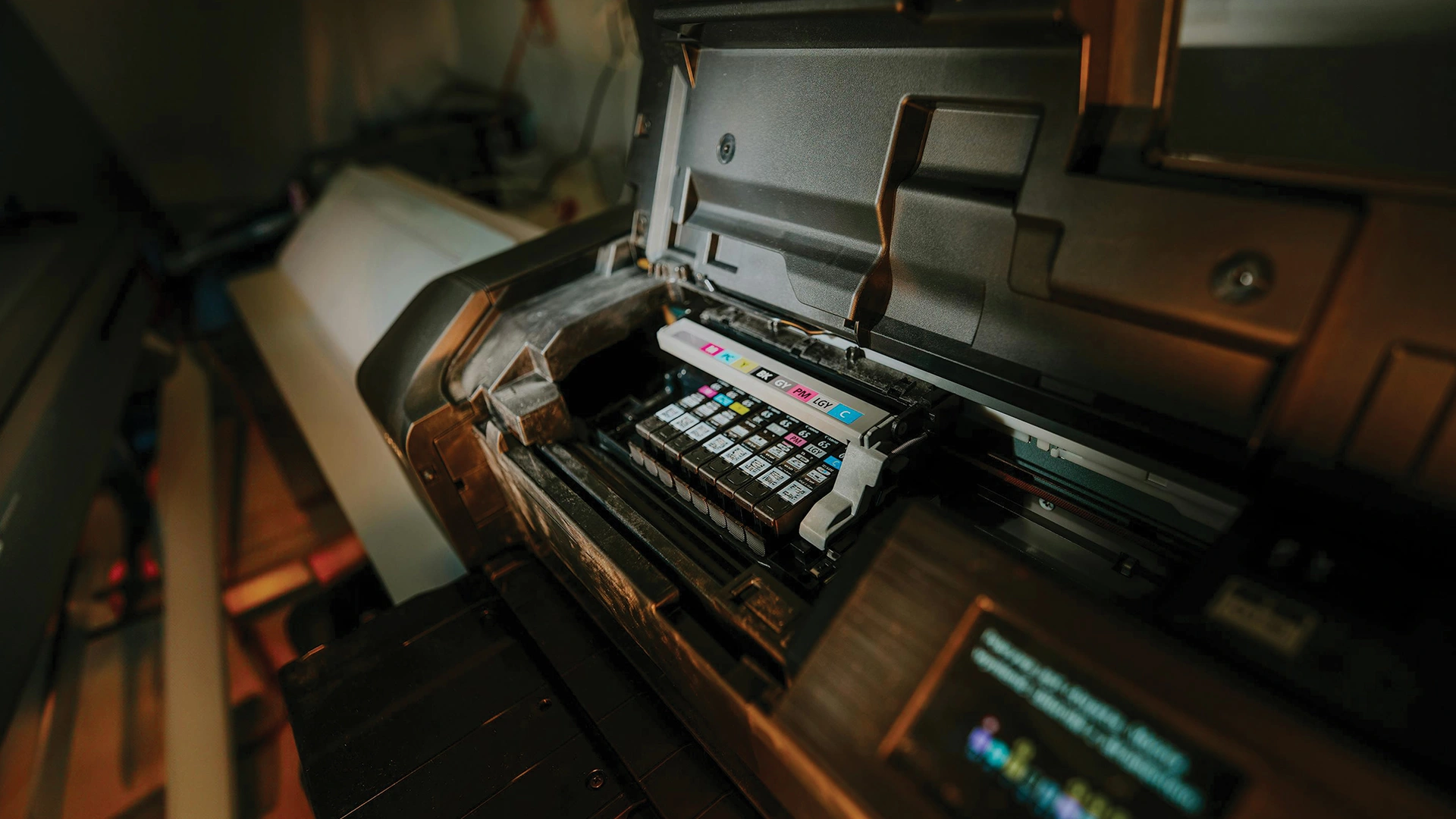
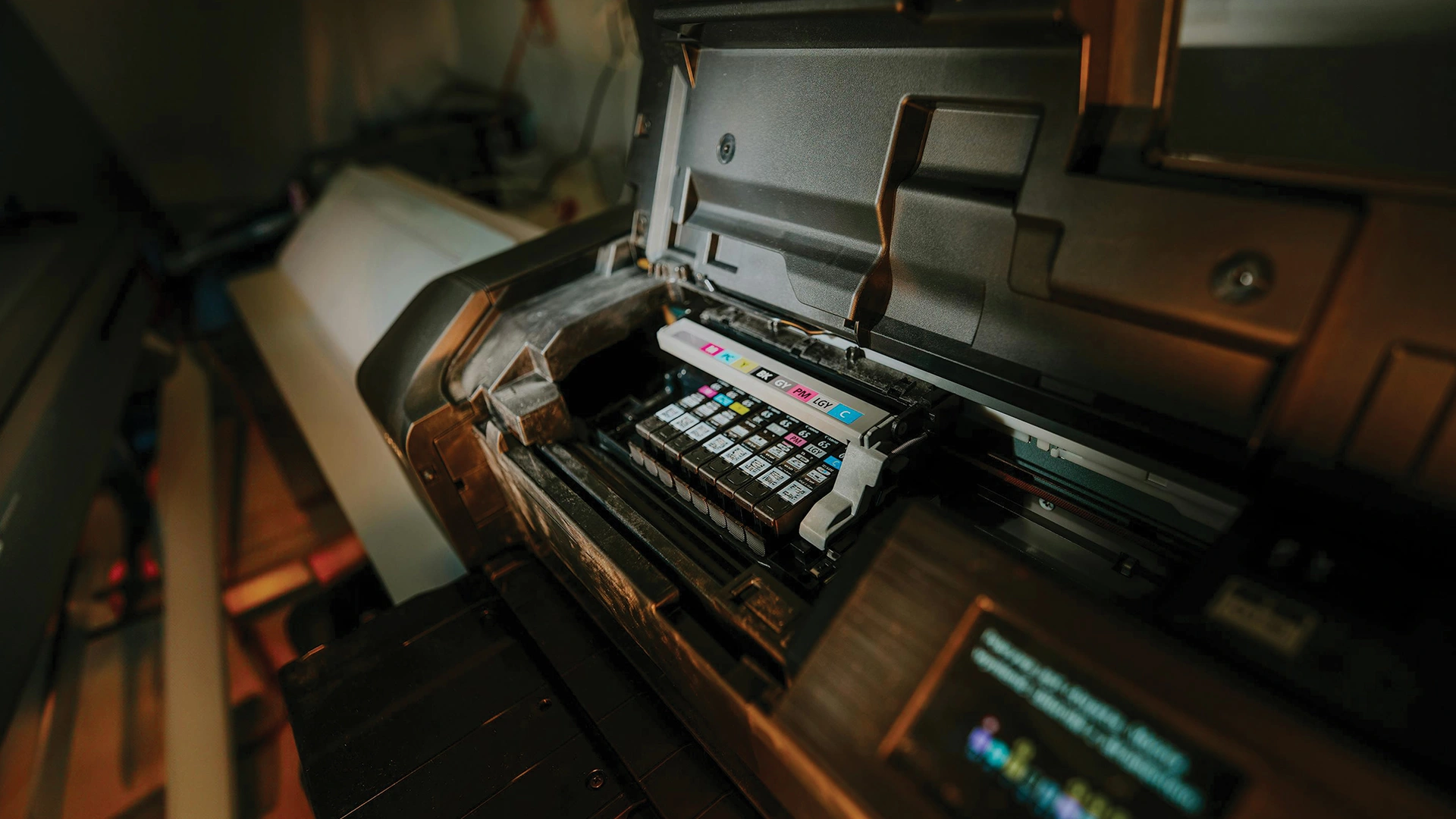
Last time, we talked about conductive ink, the lifeblood of all additive electronics projects. Today, we're going to talk about how to choose the right dispensing technology for your application, and the tradeoffs you'll need to consider.
There are many different printing options out there for additive electronics: inkjet, screen printing, direct ink writing, flexographic, gravure, aerosol, etc… It can be challenging to pick a printing technology to start an additive electronics project because each technology has their own benefits and drawbacks. Picking the wrong technology at the start of a project could require significant investment upfront or massively extend timelines further into the project.
For the next few posts, we'll take a closer look at a few common technologies for ink dispensing to help you choose the right option for your project. We'll start with a printing technology most people are familiar with from the world of desktop printing: inkjet.
What is inkjet?
Inkjet printing is a common printing technology used in most home office printers. One of the main draws of inkjet for prototyping additive electronics devices is that it is digital. This means that whenever a design change occurs, the new design can be printed on the spot without additional tooling, speeding up iteration time. The digital nature of inkjet relies on ejecting tiny droplets from hundreds of tiny nozzles on a print head in quick succession to form any pattern on a substrate.
The way in which the droplets are created varies depending on the form of inkjet being used. Although all forms of inkjet are suitable for home use, not all forms of inkjet are suitable for additive electronics. There are two main inkjet approaches: thermal inkjet and piezo inkjet.
Thermal inkjet
Thermal inkjet (sometimes referred to as bubble jet) uses resistive heating to quickly vaporize a small amount of ink. The quickly expanding vaporized ink inside the ink channel forces a small amount of ink to be ejected from the nozzle. However, using conductive inks with thermal inkjet is generally avoided for one main reason: heat! With every drop that’s ejected, a small amount of ink is cured inside the nozzle, clogging it in short order.
Piezo inkjet
Piezo inkjet, on the other hand, does not expose the inks to heat but instead uses piezo elements to send a shockwave through the ink to eject a droplet. Piezo elements are a type of ceramic that will deform when exposed to a voltage potential. Piezo inkjet printers leverage this property by sending voltage waveforms that have been tuned specifically for the geometry of the fluid path, the ink being ejected, and the size of the droplets, which typically range from 1.5pl to 30pl.
Working with droplets that are so small requires a high magnification camera and strobe light system for waveform optimization. However, waveforms can only be adjusted on industrial or laboratory inkjet systems whereas home office inkjet printers have fixed waveforms intended for regular color ink.
Materials in inkjet
Conductive inks
The conductive inks suitable for use with inkjet technology have water-like consistencies, with viscosities in a similar range (~1 cp). The compatible viscosity window for inkjet technology is much narrower than other printing technologies because high resolution prints require small droplets and small droplets are easier to make if the fluid has a low viscosity. Inkjet can typically achieve resolutions from 300-1,200 DPI. Minimum printed feature size will largely depend on ink properties, droplet size, as well as the substrate being used.
The low viscosity inks consist of 60% to 95% solvent content with the remainder being metallic particles. With such a high solvent content, most of the deposited material will evaporate during the curing process leaving behind a thin layer ranging from 1 µm to 5 µm thick. Since resistance is a function of cross-sectional area, a thinner layer thickness will result in a higher resistance limiting the amount of current a printed pattern can handle. The benefit of thin patterns is that less material is used lowering the overall material cost. The combination of these two factors makes inkjet a good candidate for low power applications where low-cost is a driving factor.
Conductive inks for inkjet tend to be more susceptible to improper storage conditions than thicker inks used in other printing technologies. The purpose of the solvent is not only to provide a carrier fluid allowing the conductive particles to be printed, but it also includes additives to stabilize the ink under proper storage conditions. Improper storage conditions will allow large agglomerates to form which could clog nozzles. Most inkjet systems also require a filter to remove any large particles and contaminants from entering the print head.
Substrates
Aside from viscosity and stability, the surface interactions between the ink and the substrate material is a critical factor which can have a huge impact on the final output. Substrates used in inkjet applications are either non-porous, like PET and polyimide (Kapton), or porous like paper: both pose their own unique challenges.
For non-porous substrates, if the surface energies of the substrate and ink are too dissimilar, the ink will refuse to wet the surface leading to poor resolution and adhesion. For porous substrates, the fluid may soak into the substrate and not form any conductive pathways. Luckily, most substrate manufacturers offer substrates with special coatings to help improve wetting characteristics as well as adhesion. These coatings can have a game changing impact and they should not be overlooked.
Assembling an inkjet printed board
Attaching electrical components to printed features created with inkjet technology can be tricky. Soldering is generally unsuccessful because printed features are so thin that without a robust binder within the structure to keep the metal in place, the molten solder will very quickly dissolve the metallic particles, destroying the printed pattern in the process. Component attachment is more successful using solder alternatives such as conductive epoxy or anisotropic conductive adhesives.
Getting started
It is possible to use conductive inks with a home office piezo-based inkjet printer but mileage will vary. An easy way to identify the underlying technology of any inkjet printer is to examine the ink cartridge. If the nozzles are removable with the cartridge, the printer uses thermal inkjet. Otherwise the printer is piezo. Thermal print heads are much cheaper than piezo print heads so manufacturers build them into the ink cartridge and replace them each time the ink runs out to keep the nozzles as clean as possible. That being said, there are a few things to note before using a home office printer for additive electronics:
- The print head must be flushed after every use to avoid inks drying out or destabilizing within the print head. Since nozzles cannot be easily replaced on piezo-based inkjet printers it's best to avoid clogged nozzles as much as possible.
- Avoid using the same cartridge location to dispense different inks. When a cartridge is loaded onto the print head, it will supply ink to a subset of nozzles on the print head. If that cartridge is replaced with a new type of ink, it will supply material to the same subset of nozzles. Mixing inks inside the print head is a recipe for clogged nozzles.
- The printer’s droplet waveform won’t necessarily be optimal for conductive ink. The printer will likely be able to still eject droplets, however those droplets may be inconsistent in size or be ejected in arbitrary directions leading to a fuzzy printed pattern.
- Home office printers do not have the ability to align a new print with existing printed patterns. The new pattern will be printed at an offset from the previous one. Office printer paper feed systems are only really designed to detect the leading edge of a piece of paper and does very little to ensure precise lateral alignment. If you want to build up thickness to improve resistance or use multiple materials you are likely going to be left wanting more.
- Very thin or thick substrates could be problematic for the printer’s paper feeder system. Home office printers were intended to be used with paper. A very thin film could wrinkle in the inner working and jam the paper feed system. On the flip side, a thick substrate may not be able bend enough to be fed through the printer.
The limitations of a home office printer for additive electronics often push developers to quickly move on to pursue laboratory inkjet systems which address the limitations listed above and gives them access to a lot of the settings under the hood. These laboratory systems cost at least $25,000 and can cost six figures, but they can be helpful in improving the transition from prototype to production for applications that require inkjet technology.
Challenges in scaling inkjet
According to IDtechEX, inkjet only made up less than 2% of all commercial additive electronics products in 2017 while screen printing made up the remaining 98%.
A contributing factor to this discrepancy is that the initial costs associated with setting up a production facility for inkjet are significantly higher than screen printing. In addition, screen printing infrastructure already exists and continuous improvements to screen printing technology have kept it competitive from a resolution perspective.
Prototyping
A common situation we have heard from our customers is that they pursued inkjet initially because the idea of being able to prototype in-house without delays is extremely attractive. When they invested in more sophisticated laboratory equipment and got further into development and closer to scaling up their design, they realized that their application didn’t directly benefit from the core strengths that inkjet has to offer and that their direction was based solely on the tools available for prototyping. This realization led them to pivot the core materials and printing technology used in their design to not only improve it but make it easier to scale. However, this decision came at the expense of their precious timelines, along with the significant capital investments required to pivot their entire technology stack (and the money wasted on inkjet prototyping when the entire process needed redoing anyway).
Conclusion
To summarize, inkjet uses small droplets of ink to create high resolution patterns on flexible substrates such as plastics and paper. The small quantity of ink involved produces thin conductive layers making inkjet ideal for low cost and low power applications. By investing in the right equipment, the digital nature of inkjet makes the transition from prototype to production easy.
Although not the most widely used printing technology for additive electronics, inkjet printing is a mature technology and is a good candidate if the application calls for it. However, since the project requirements addressed by inkjet's value are quite specific, it's important to compare and contrast the project requirements with the benefits and limitations of this printing technology and associated materials before committing to it to avoid unnecessary investments and unexpected delays.
As mentioned above, screen printing is by far the most dominant technology being used in additive electronics. This blog takes a closer look at screen printing and explores why it is so dominant in additive electronics.
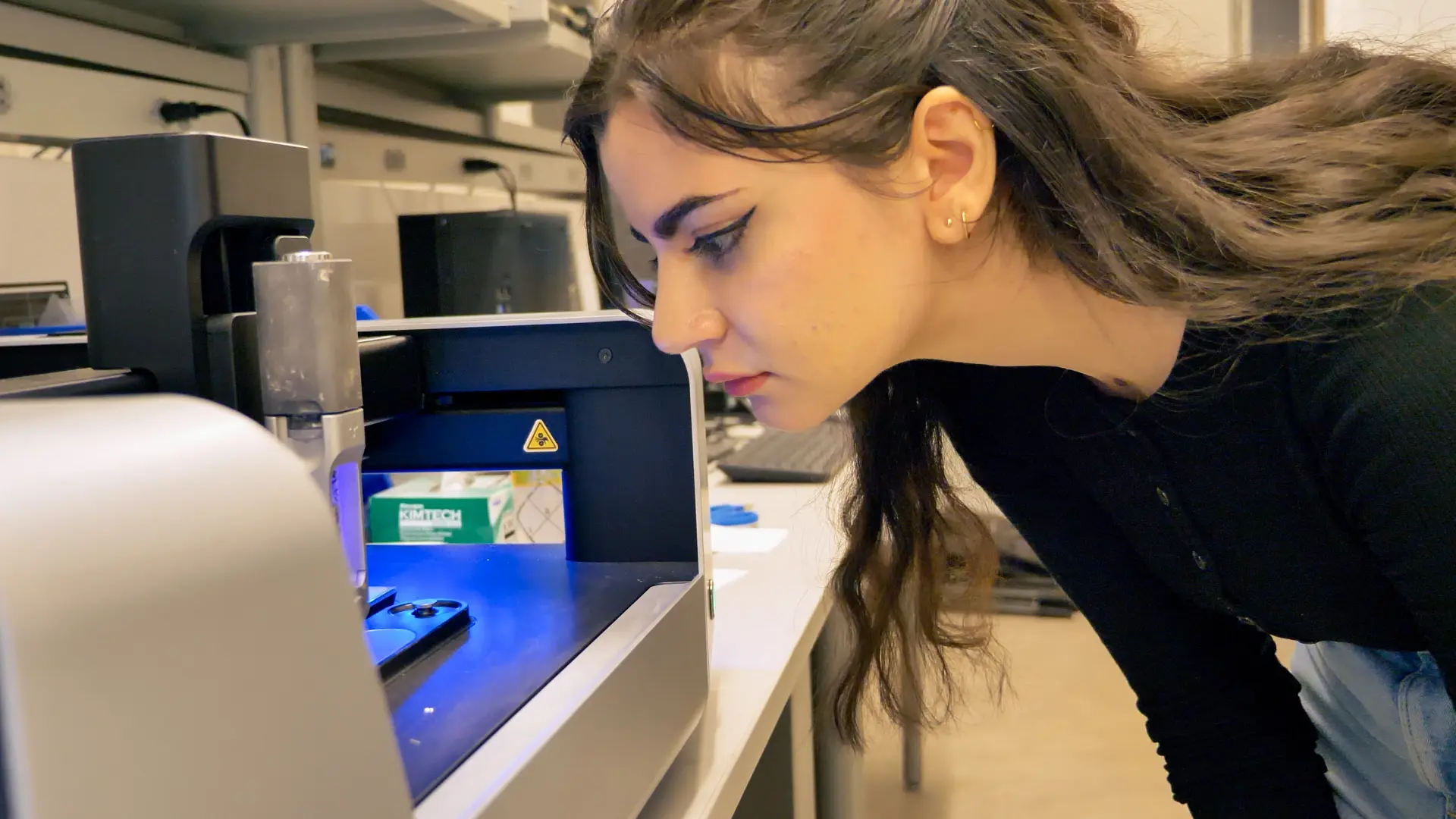
Check out our Customer Stories
Take a closer look at what our customers are doing in the industry.
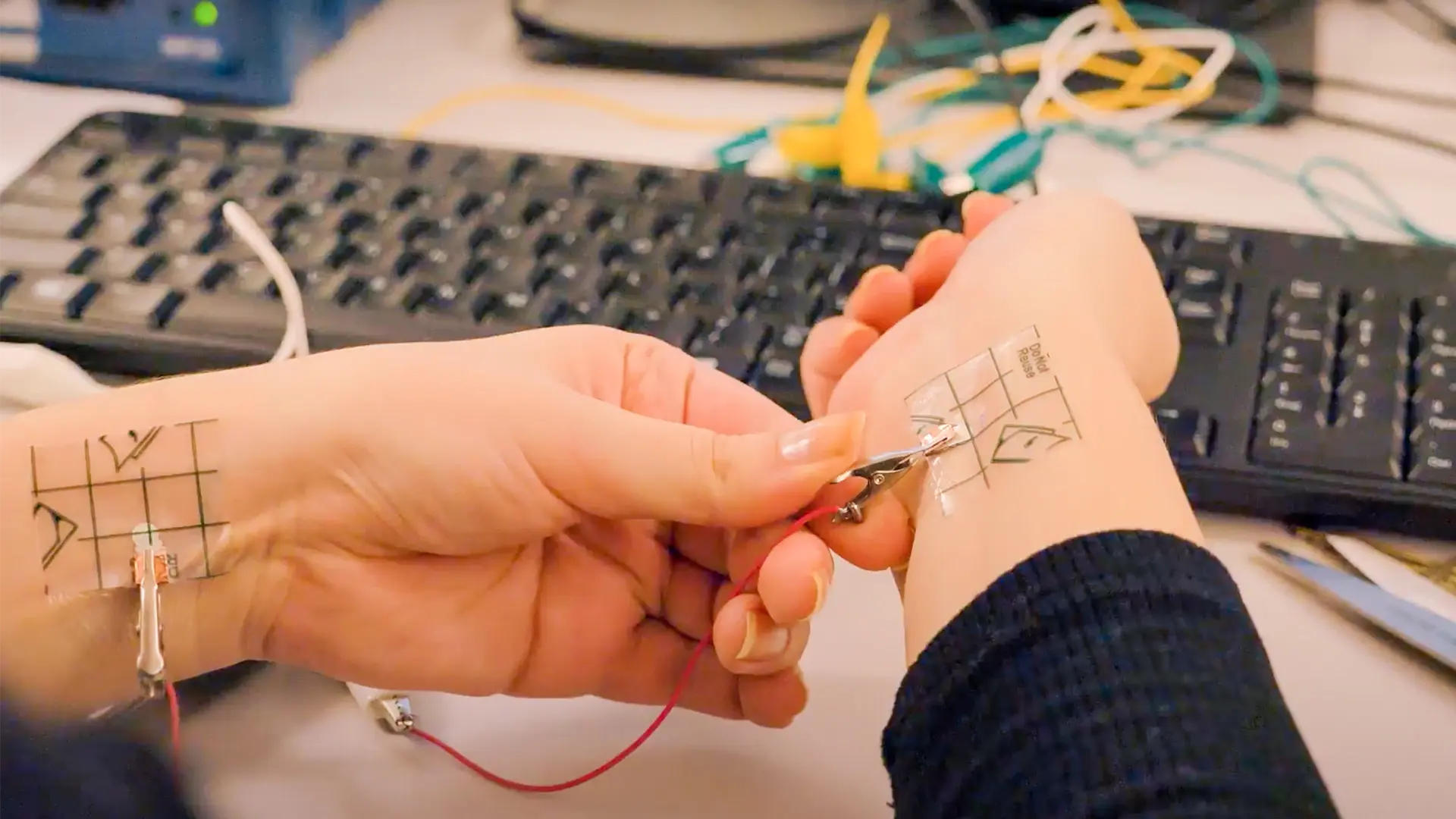