Flexible PCBs
Prototype custom flexible PCBs entirely in-house
Flexible printed circuit boards (FPCBs) include single- or double-sided PCBs, multilayer PCBs, and rigid-flex PCBs [1]. They are bendable circuits made from flexible materials like polyimide. FPCBs are commonly used in industries such as consumer electronics, automotive systems, medical devices, and aerospace because they fit into compact or curved spaces.
Lightweight, adaptable designs are crucial for the development of flexible electronics. Using direct ink writing (DIW) machines, flexible PCBs can be printed by depositing conductive inks onto flexible substrates, enabling efficient and customizable production.
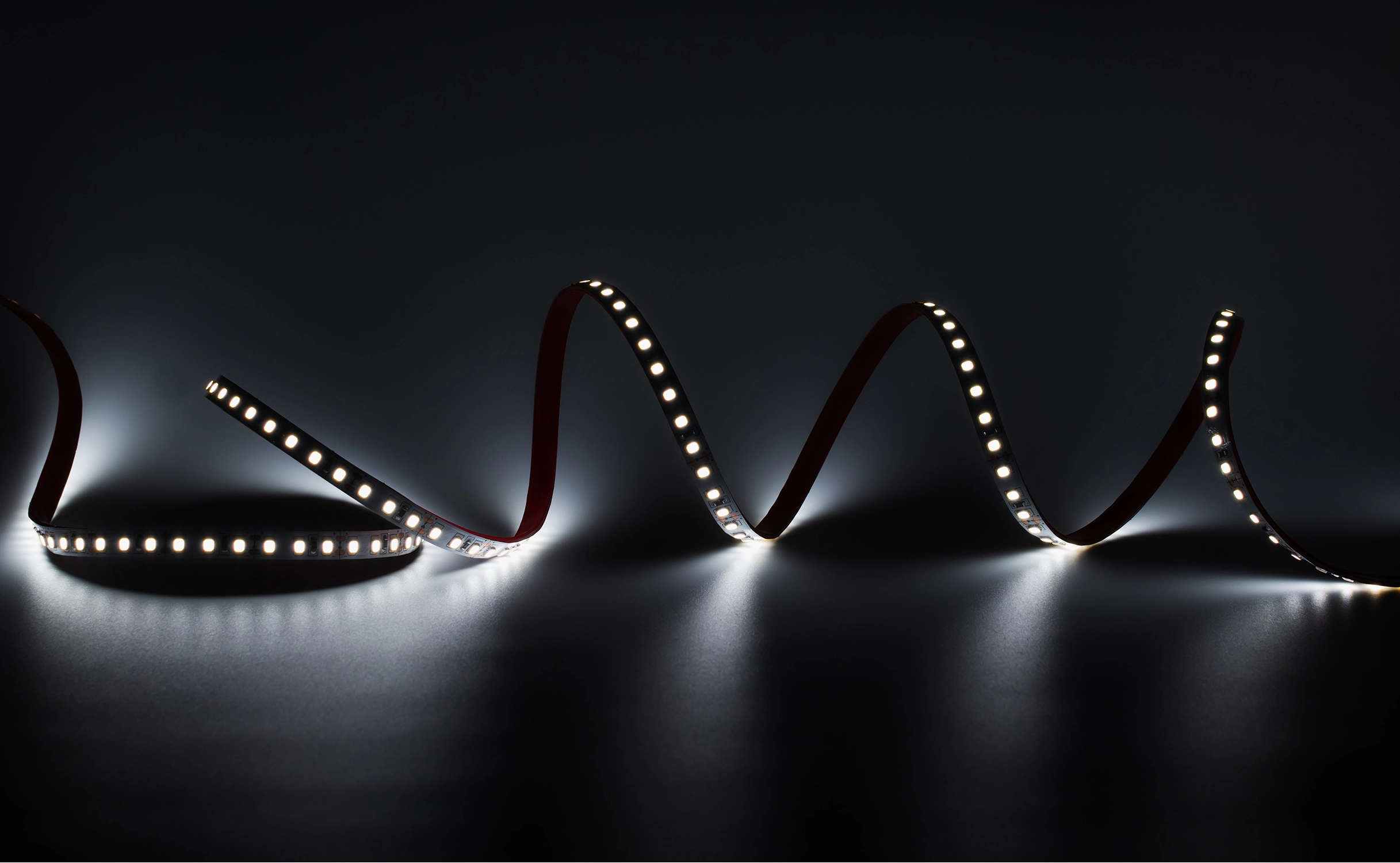
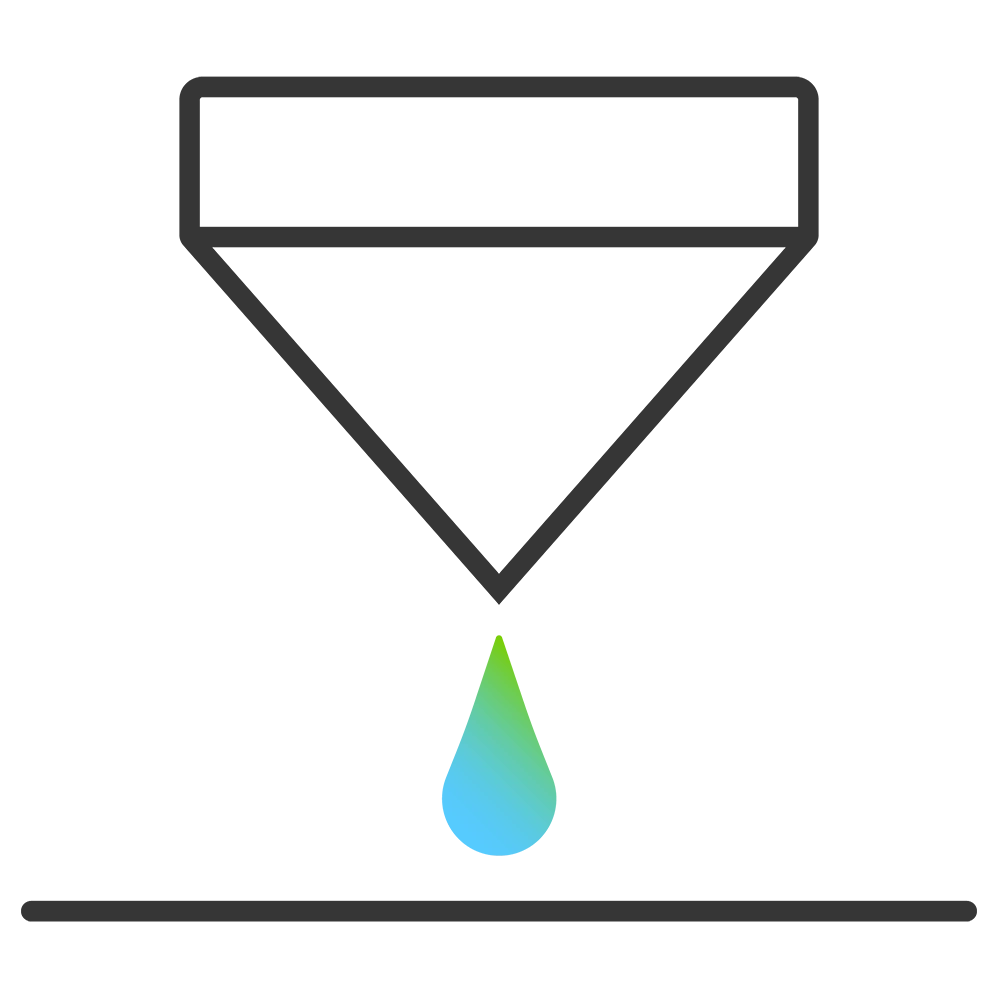
- Consumer electronics
- Medical devices
- Wearables
- Automotive
- Aerospace
- Defense
- Copper-based inks
- Silver-based inks
- Carbon-based inks
- Conductive polymer ink
- Polycarbonate (PC)
- Polyethylene terephthalate (PET)
- Polyimide (PI)
Market size and driving forces
The flexible circuit board market was USD $24.25 billion in 2024. With growing interest in this sector, it is projected to reach USD $70.11 billion by 2034, with a compound annual growth rate of 11.20%. The Asia Pacific region has the biggest market share, while North America is expected to be the fastest-growing market in the next decade [2].
Flexible printed circuit boards market size 2023 to 2024 (USD billion)
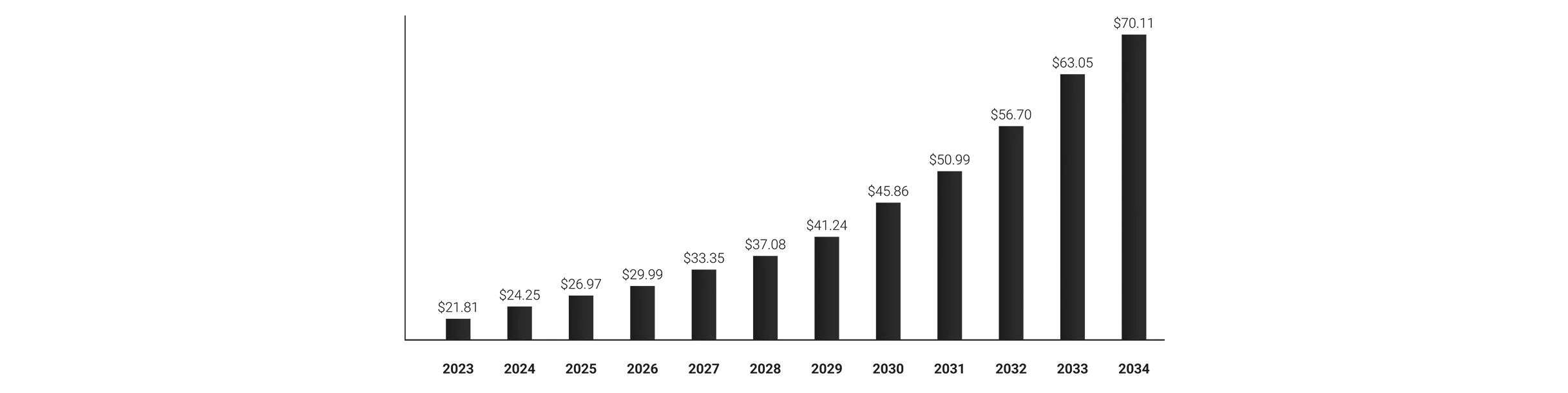
The rapid growth can be attributed to the following factors [3]:
- The demand for miniaturization and thin form factors
- Market expansion in consumer electronics, automotive, medical, and flexible display industries
- Environmental concerns
Benefits
Researchers [4] have identified the following benefits in utilizing flexible PCBs, compared to traditional rigid PCBs like FR1 and FR4:
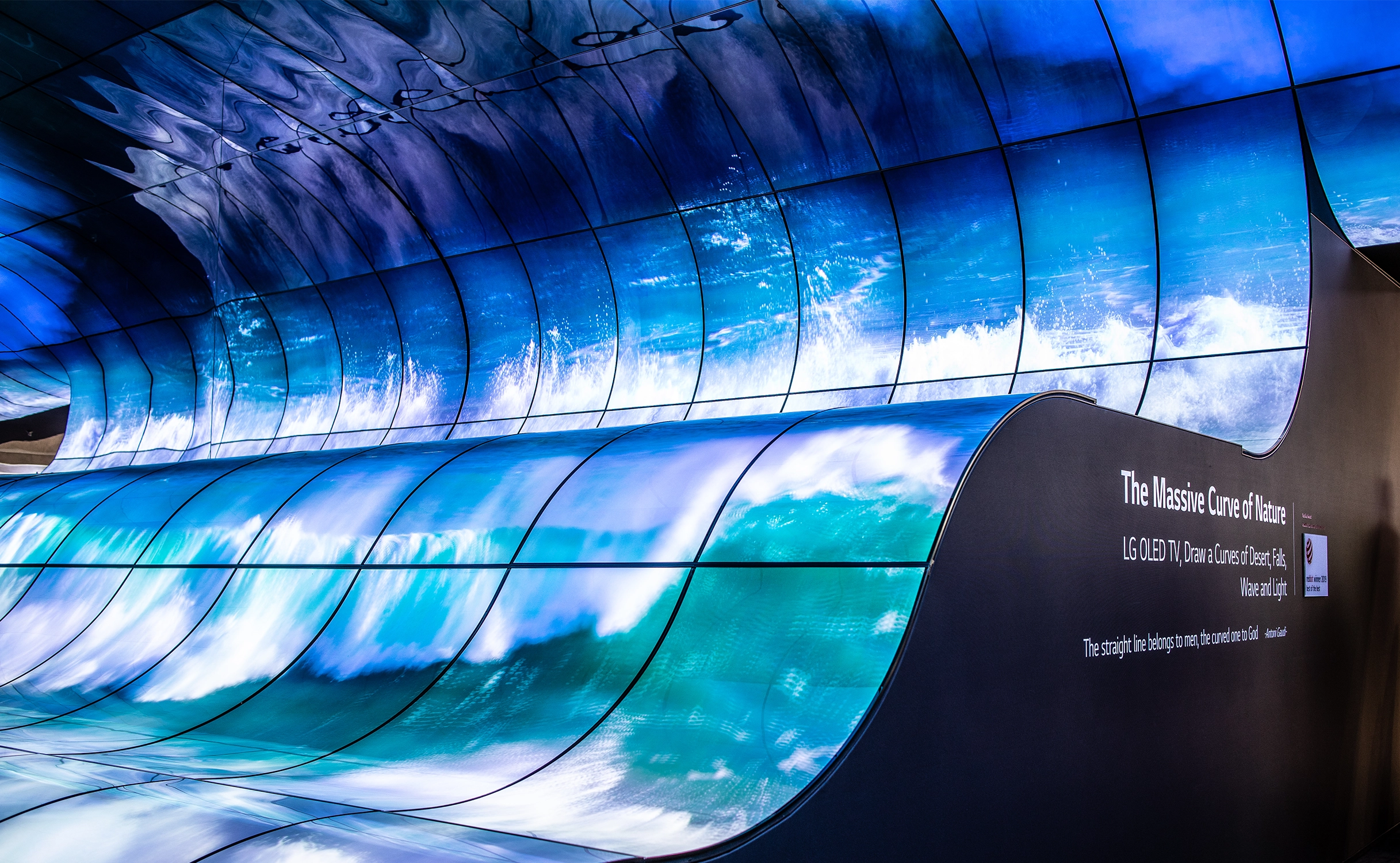
Design freedom and biocompatibility
Flexible circuits offer unmatched design freedom, enabling the creation of compact, lightweight, and highly adaptable electronics. These flex circuits can conform to irregular surfaces, wrap around curved objects, or be integrated into compact spaces, making them essential in bio-compatible applications such as wearables, robotics, and medical devices. Their adaptability allows for innovations in form factor, such as foldable smartphones or skin-like electronic patches.
Design freedom and biocompatibility
Flexible circuits offer unmatched design freedom, enabling the creation of compact, lightweight, and highly adaptable electronics. These flex circuits can conform to irregular surfaces, wrap around curved objects, or be integrated into compact spaces, making them essential in bio-compatible applications such as wearables, robotics, and medical devices. Their adaptability allows for innovations in form factor, such as foldable smartphones or skin-like electronic patches.
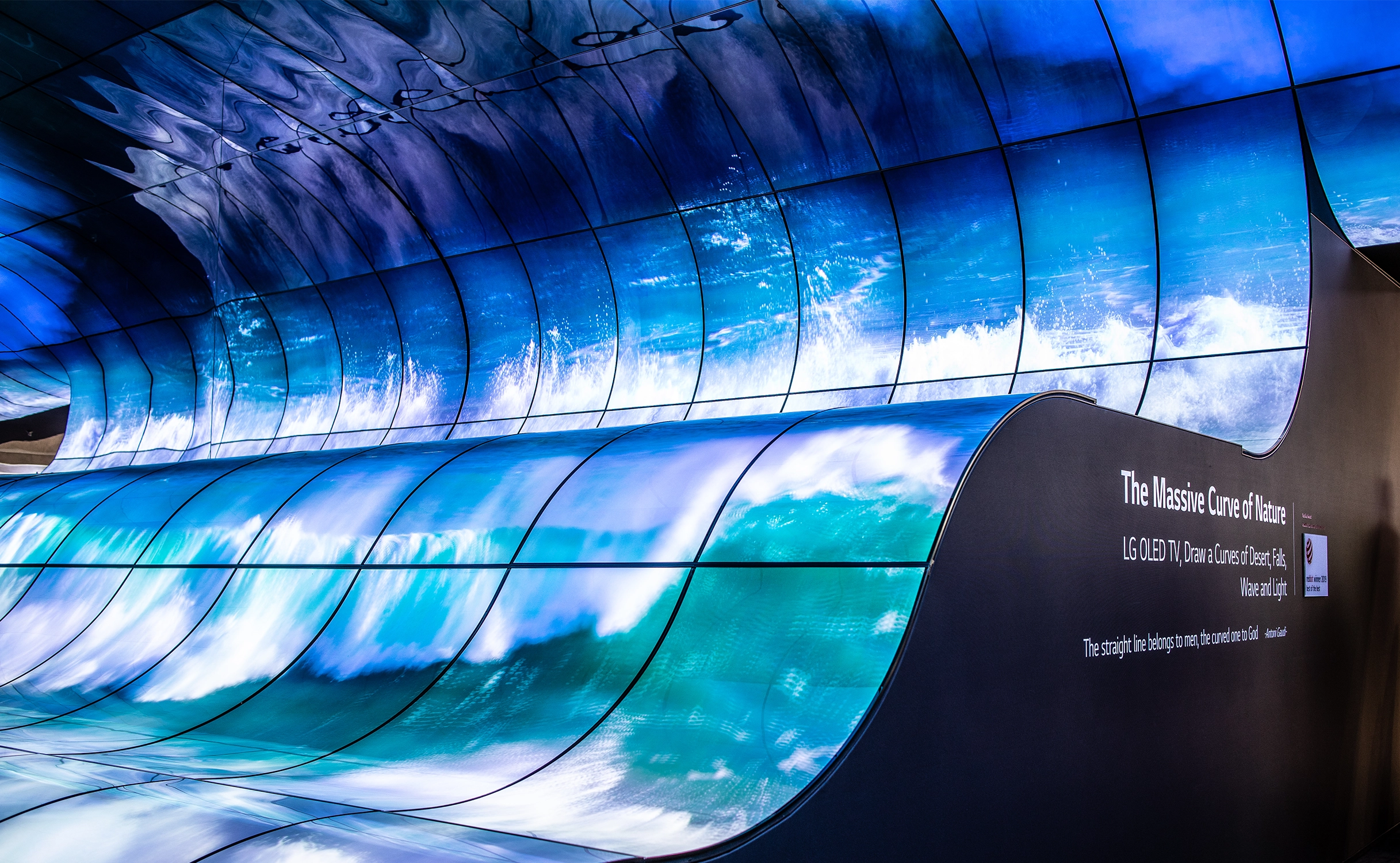
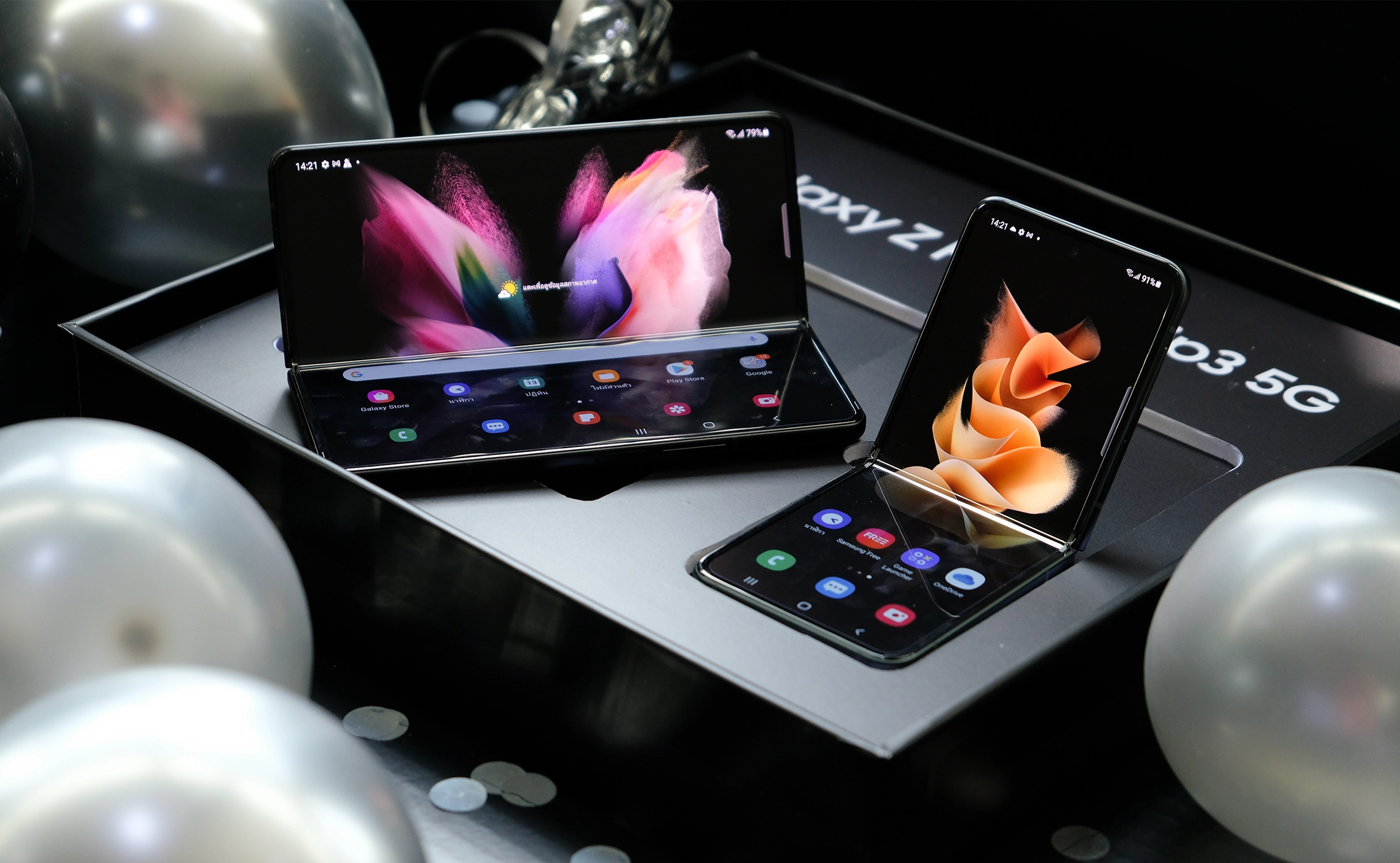
Space efficiency and lightweight design
By consolidating multiple electronic components and wiring into a single flexible assembly, a flexible PCB significantly reduces the need for bulky connectors, lowers part counts, and simplifies component assembly. Circuits may include a single layer or compact multilayer structures with two or three copper layers (four conductive copper layers are possible, but are typically reserved for applications requiring higher density without frequent bending) laminated to a dielectric substrate film, bonded with adhesive material, and treated with a protective finish. The result is a thinner, lighter, more cost-effective product, essential in miniaturized electronic devices like smartphones, tablets, or aerospace systems.
Space efficiency and lightweight design
By consolidating multiple electronic components and wiring into a single flexible assembly, a flexible PCB significantly reduces the need for bulky connectors, lowers part counts, and simplifies component assembly. Circuits may include a single layer or compact multilayer structures with two or three copper layers (four conductive copper layers are possible, but are typically reserved for applications requiring higher density without frequent bending) laminated to a dielectric substrate film, bonded with adhesive material, and treated with a protective finish. The result is a thinner, lighter, more cost-effective product, essential in miniaturized electronic devices like smartphones, tablets, or aerospace systems.
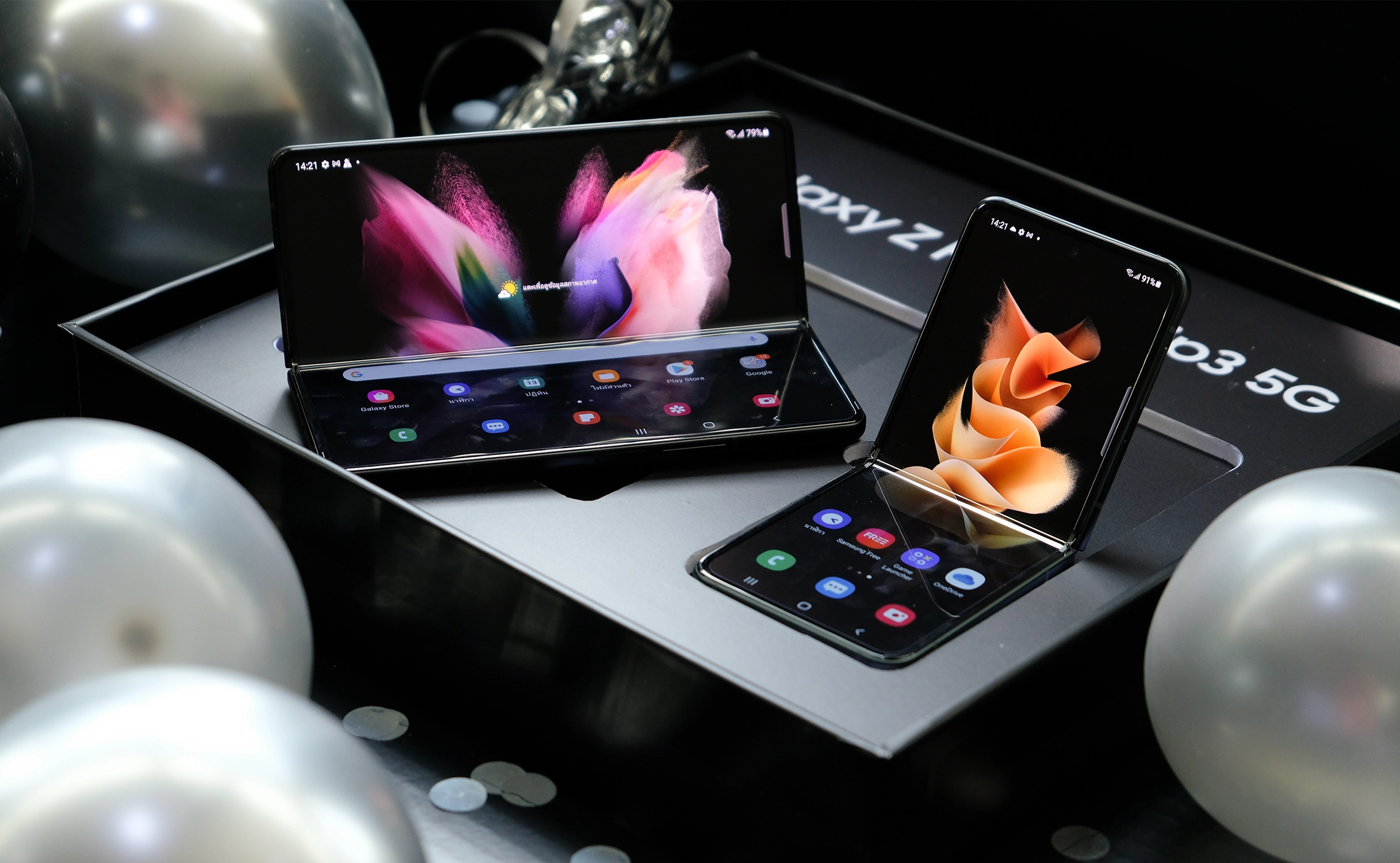
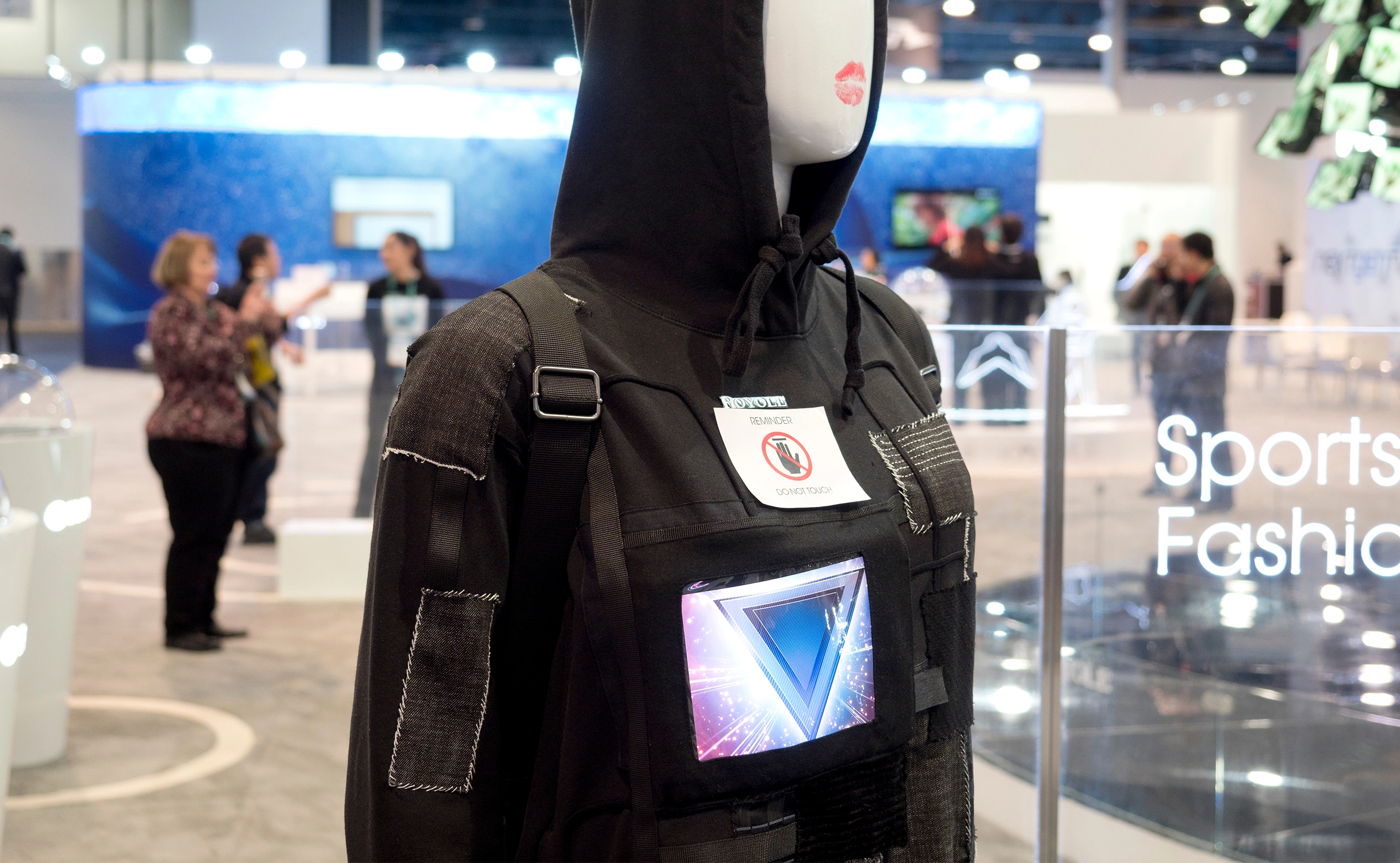
Durability and flexibility in high-stress environments
Flexible PCBs are designed to withstand mechanical stress from constant bending, vibrations, and/or movement, making them durable in dynamic environments. This dynamic flexing will enhance reliability in wearables, the automotive industry, or applications where regular movement and stress are common. Printed interconnects, in particular, can improve resilience by eliminating the weak points often associated with traditional bonding.
Durability and flexibility in high-stress environments
Flexible PCBs are designed to withstand mechanical stress from constant bending, vibrations, and/or movement, making them durable in dynamic environments. This dynamic flexing will enhance reliability in wearables, the automotive industry, or applications where regular movement and stress are common. Printed interconnects, in particular, can improve resilience by eliminating the weak points often associated with traditional bonding.
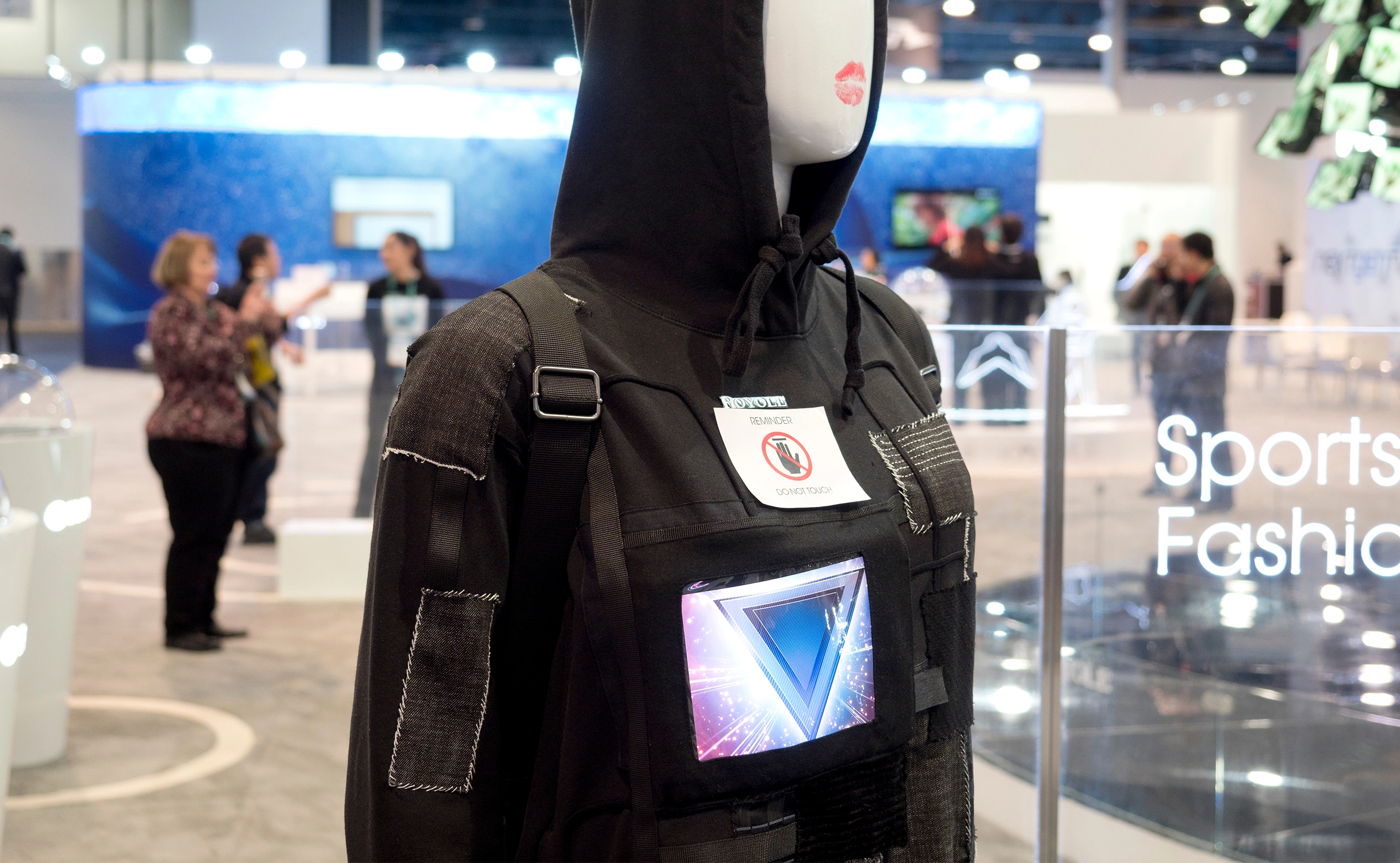
Challenges
While flexible PCBs are an ideal solution for applications in a variety of main electronics sectors, their wider adoption relies on overcoming the following challenges [4][5]:
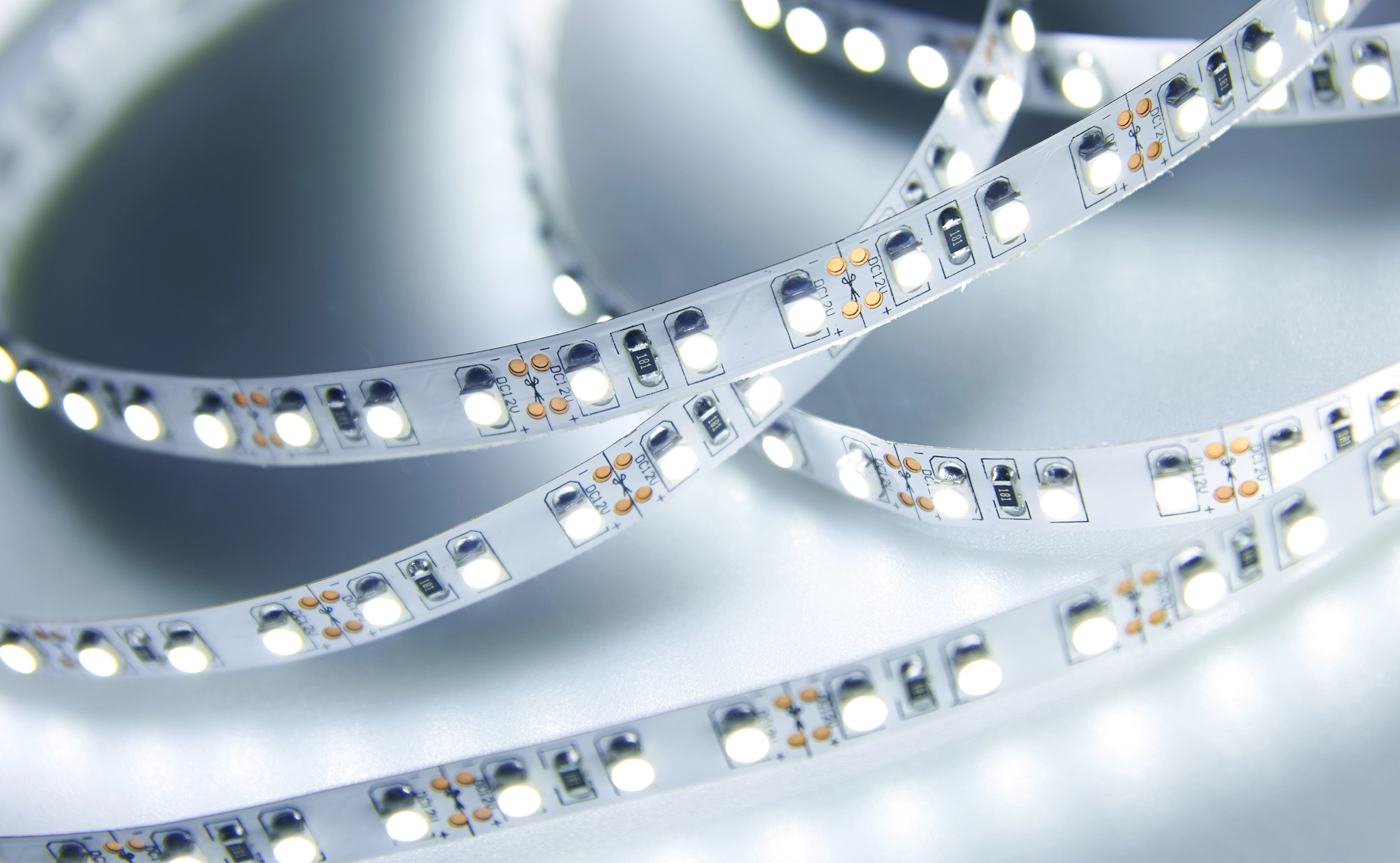
Mechanical interference and stress
Precise control of the PCB's curvature is essential to prevent excessive bending or folding, which could introduce mechanical stress and cause material fatigue, cracks, or fractures over time. Designers must carefully plan the layout to prevent wiring errors and avoid unwanted physical interaction with other elements in the system.
Mechanical interference and stress
Precise control of the PCB's curvature is essential to prevent excessive bending or folding, which could introduce mechanical stress and cause material fatigue, cracks, or fractures over time. Designers must carefully plan the layout to prevent wiring errors and avoid unwanted physical interaction with other elements in the system.
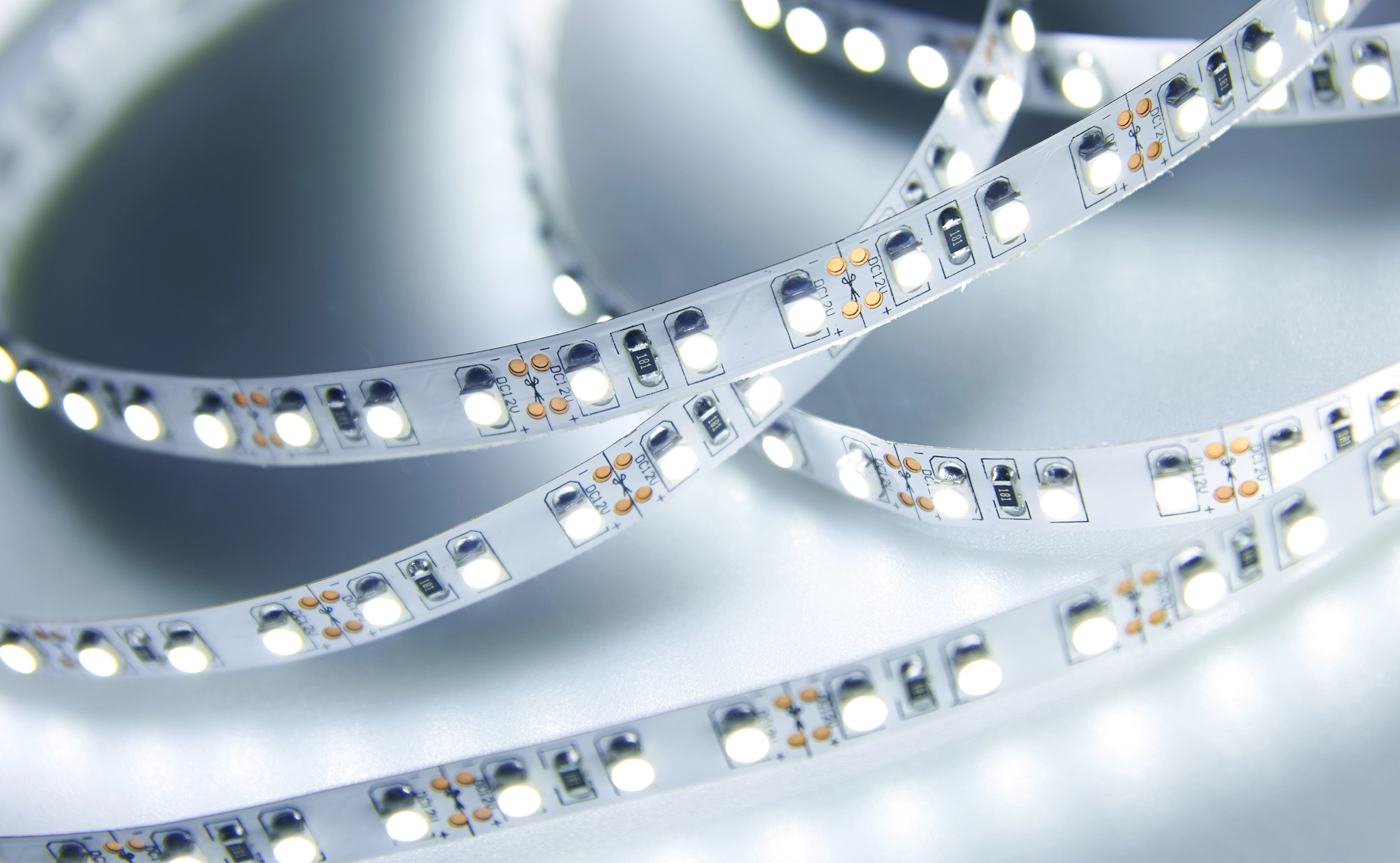
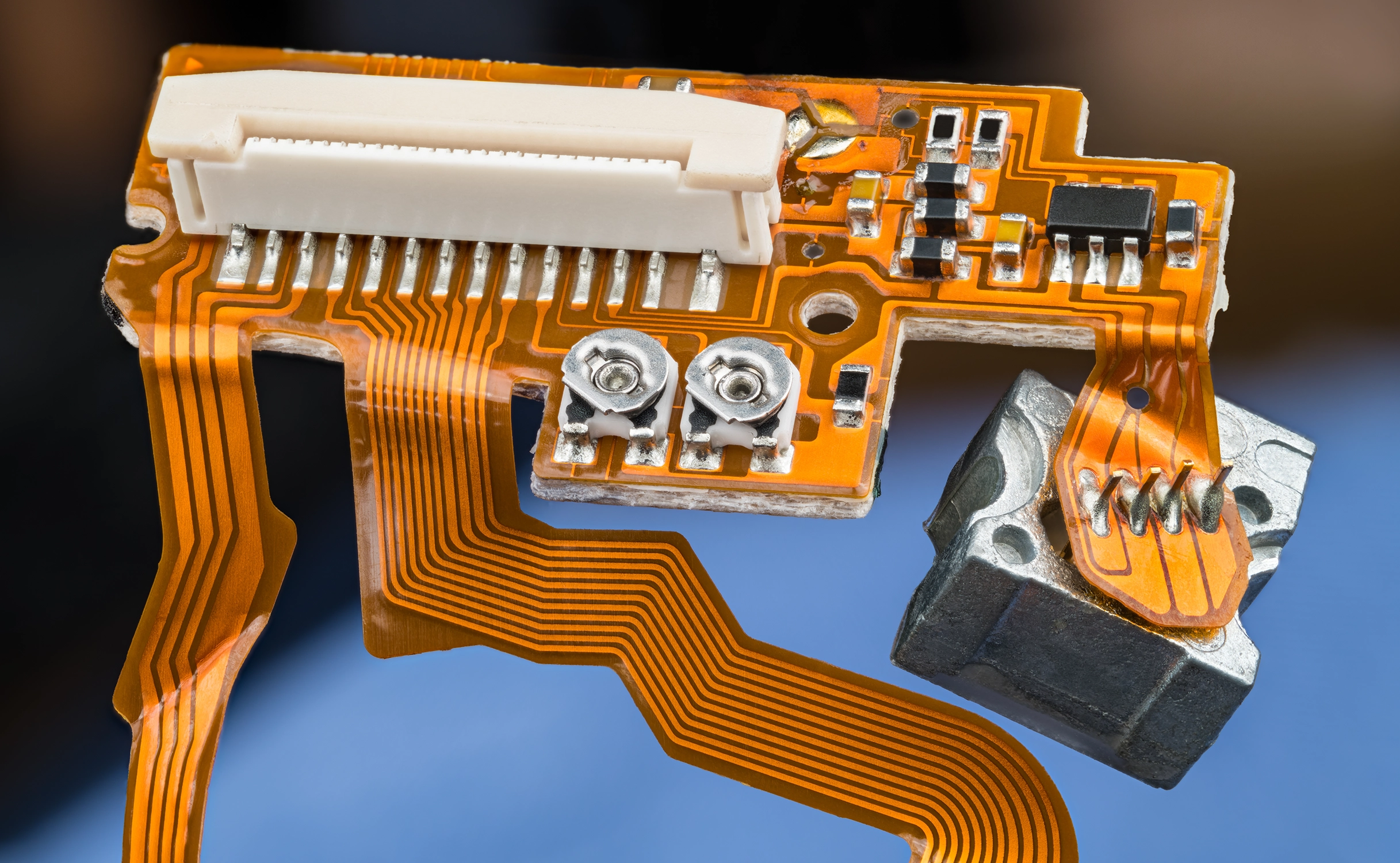
Signal integrity and electromagnetic interference
In densely packed designs, flexible PCBs may suffer from electromagnetic interference (EMI) in high-density applications, leading to signal degradation, especially in high-frequency applications such as radio frequency communication or IoT devices. Maintaining signal integrity becomes more challenging as PCBs are flexed or bent in ways that alter their electrical properties. To mitigate these issues, designers should carefully plan the PCB layout and consider how to shield components effectively. While these efforts are important, they also increase complexity and assembly costs.
Signal integrity and electromagnetic interference
In densely packed designs, flexible PCBs may suffer from electromagnetic interference (EMI) in high-density applications, leading to signal degradation, especially in high-frequency applications such as radio frequency communication or IoT devices. Maintaining signal integrity becomes more challenging as PCBs are flexed or bent in ways that alter their electrical properties. To mitigate these issues, designers should carefully plan the PCB layout and consider how to shield components effectively. While these efforts are important, they also increase complexity and assembly costs.
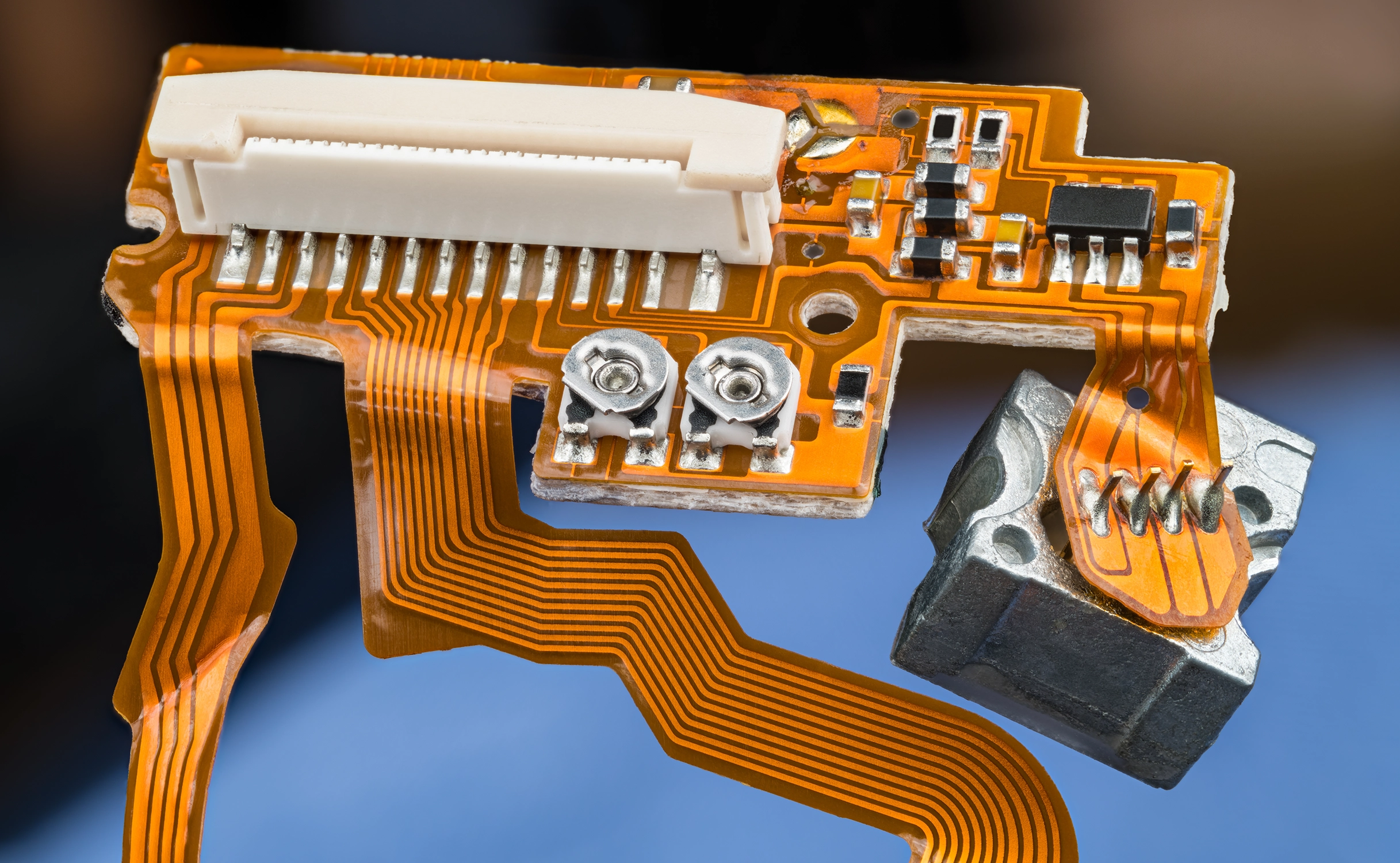
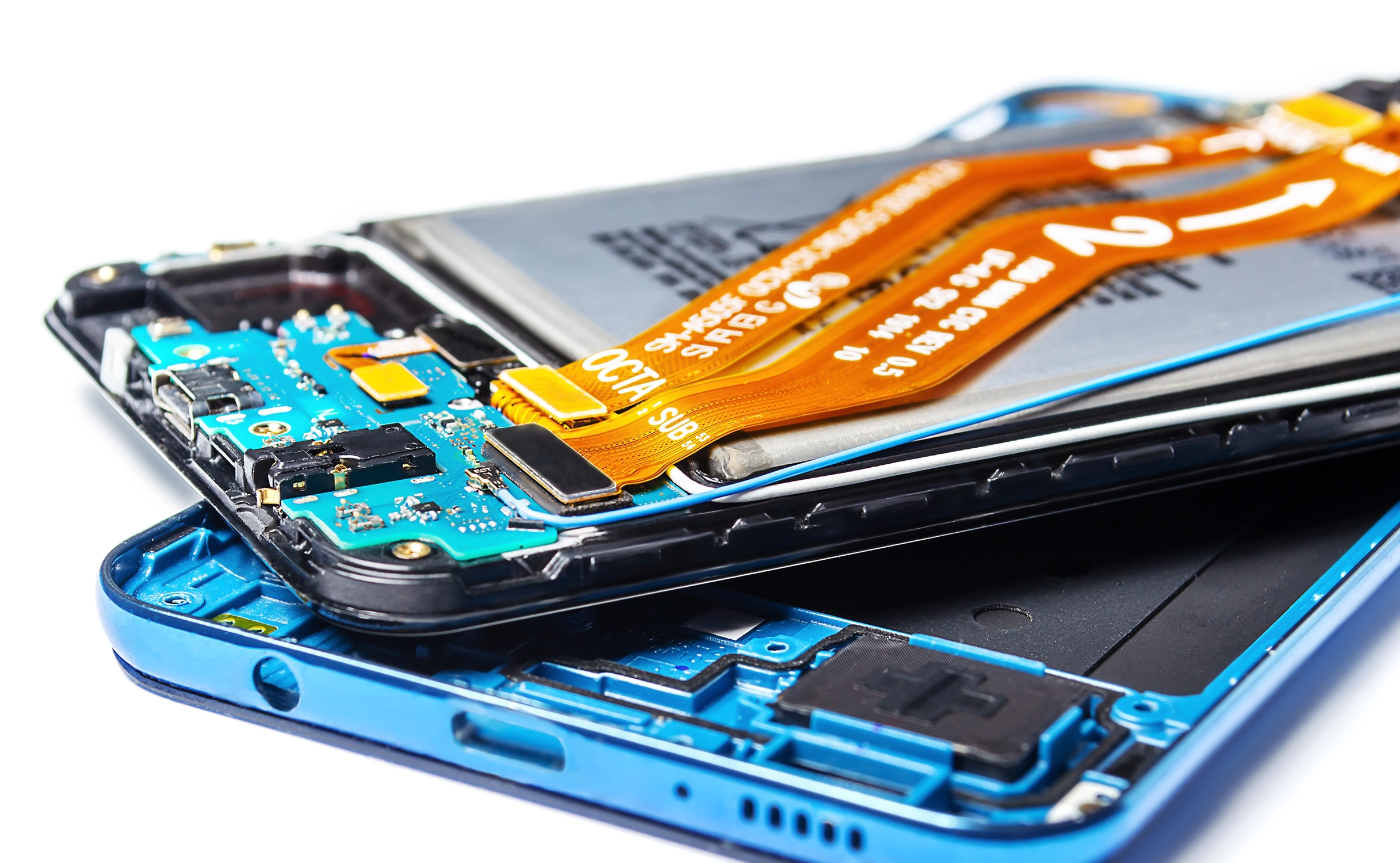
Thermal management
Thermal management in flexible PCBs is critical, especially when exposed to high temperatures. Flexible substrates, such as polyimide or PET, may not have the same or better thermal conductivity as other materials, leading to overheating and eventual degradation. Managing heat dissipation without compromising flexibility is a persistent challenge, particularly for high-performance or power-intensive devices.
Thermal management
Thermal management in flexible PCBs is critical, especially when exposed to high temperatures. Flexible substrates, such as polyimide or PET, may not have the same or better thermal conductivity as other materials, leading to overheating and eventual degradation. Managing heat dissipation without compromising flexibility is a persistent challenge, particularly for high-performance or power-intensive devices.
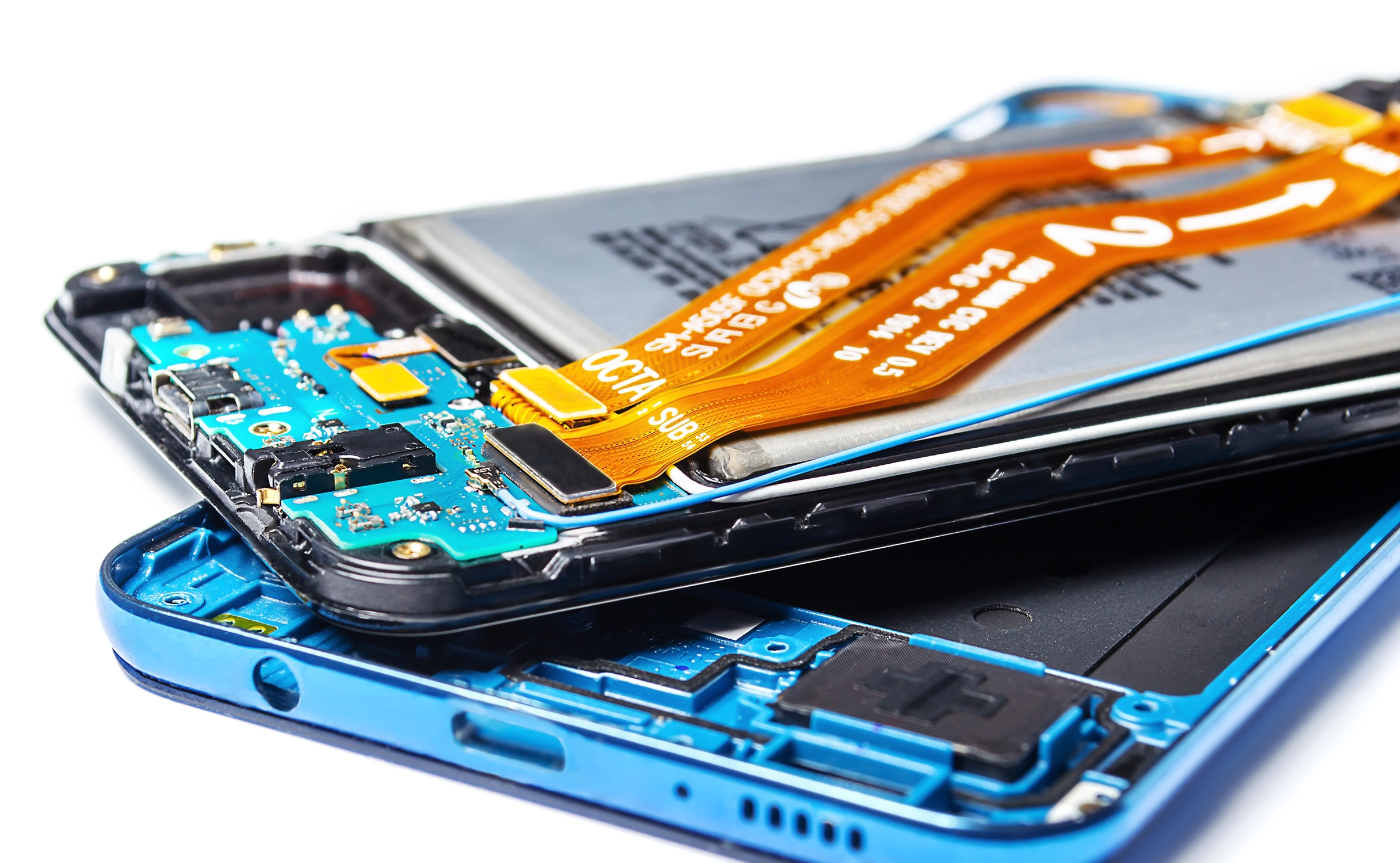
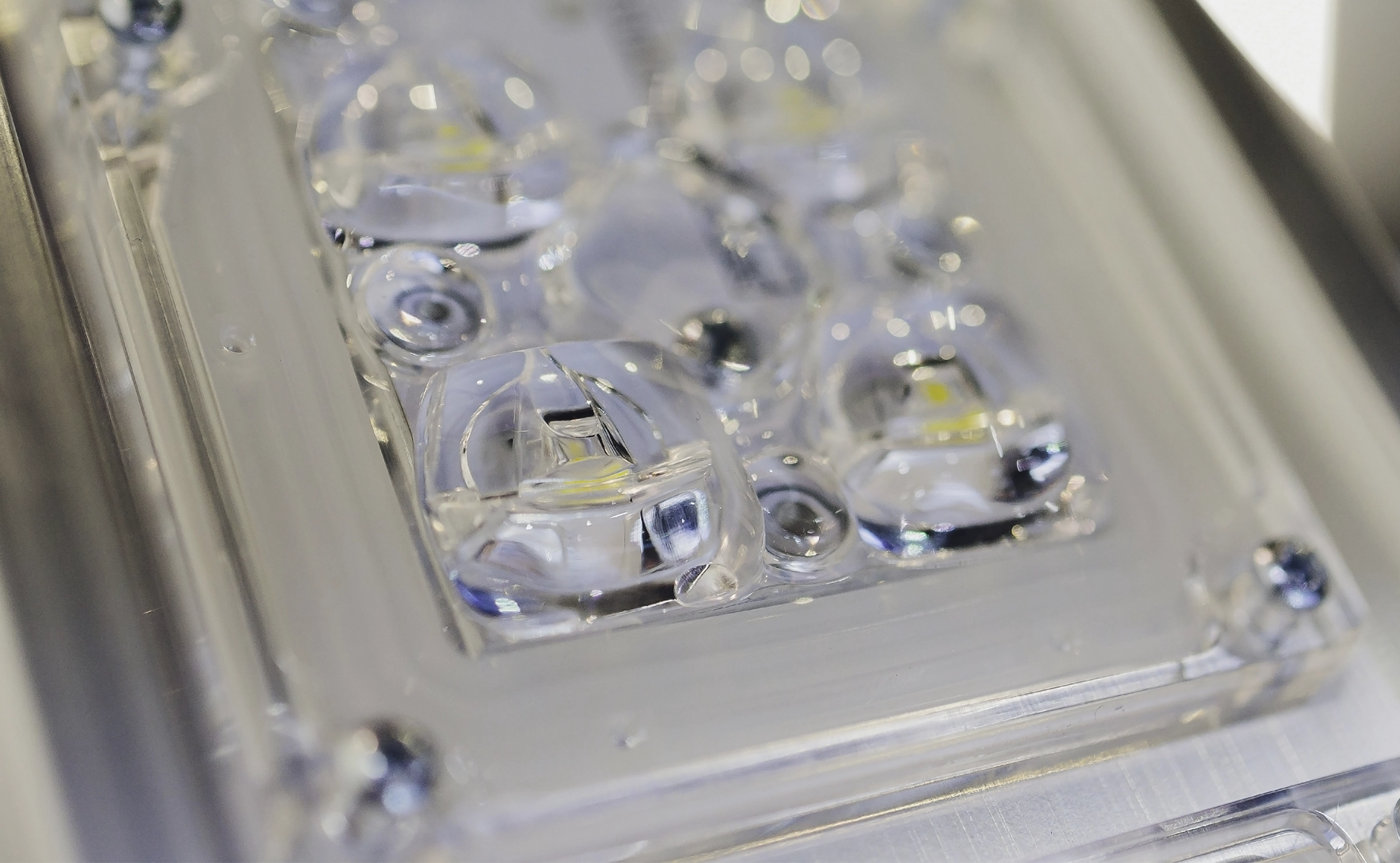
Assembly complexity and material trade-offs
The use of specialized materials can present unique challenges. Thin dielectric substrate films and layered adhesive material can lead to warping, cracking, or misalignment. To ensure durability and accuracy, designers should consider a protective finish compatible with copper plating and soldering. Selecting materials with better thermal management helps protect electrical connections in demanding environments, but often increases complexity and cost.
Assembly complexity and material trade-offs
The use of specialized materials can present unique challenges. Thin dielectric substrate films and layered adhesive material can lead to warping, cracking, or misalignment. To ensure durability and accuracy, designers should consider a protective finish compatible with copper plating and soldering. Selecting materials with better thermal management helps protect electrical connections in demanding environments, but often increases complexity and cost.
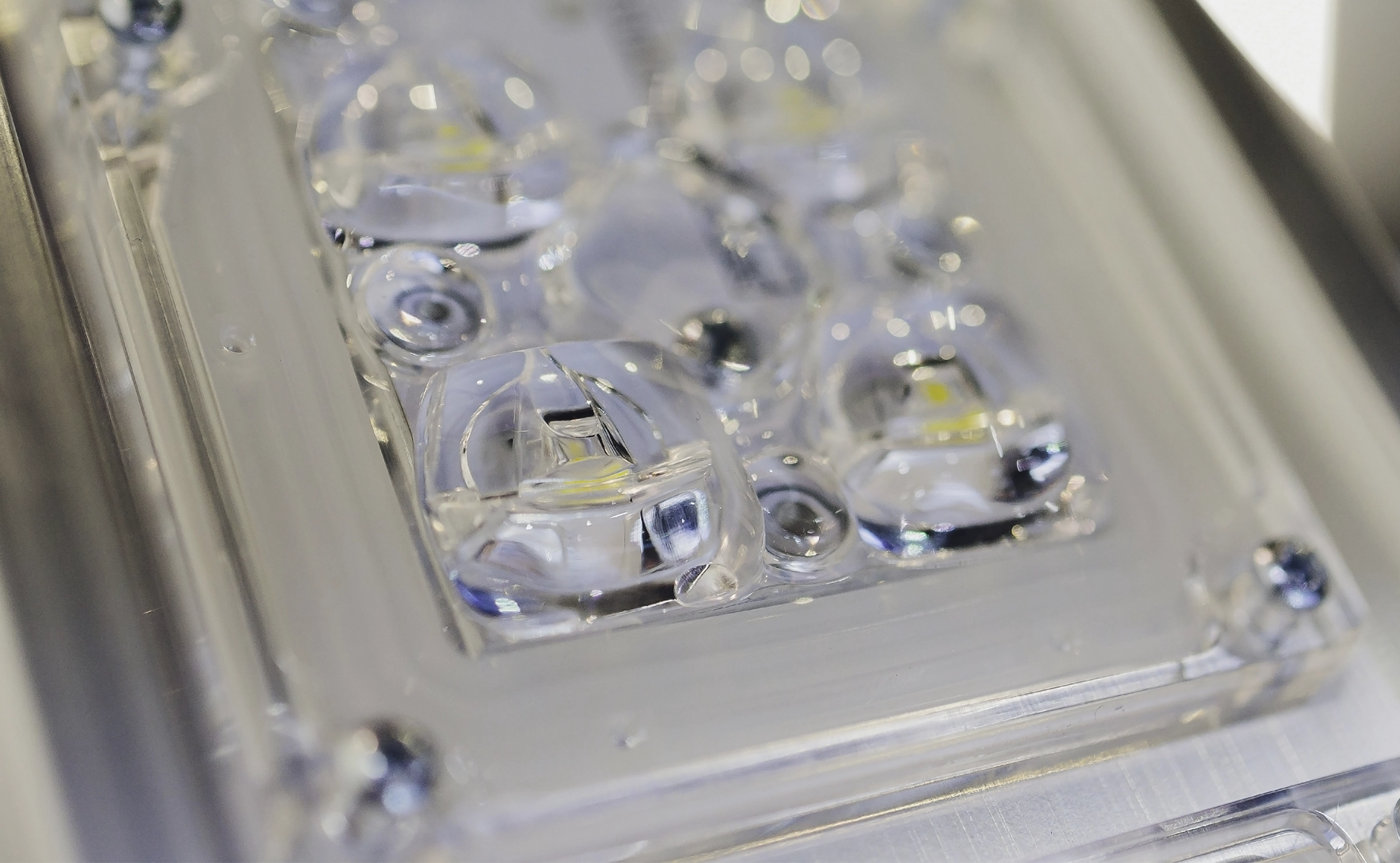
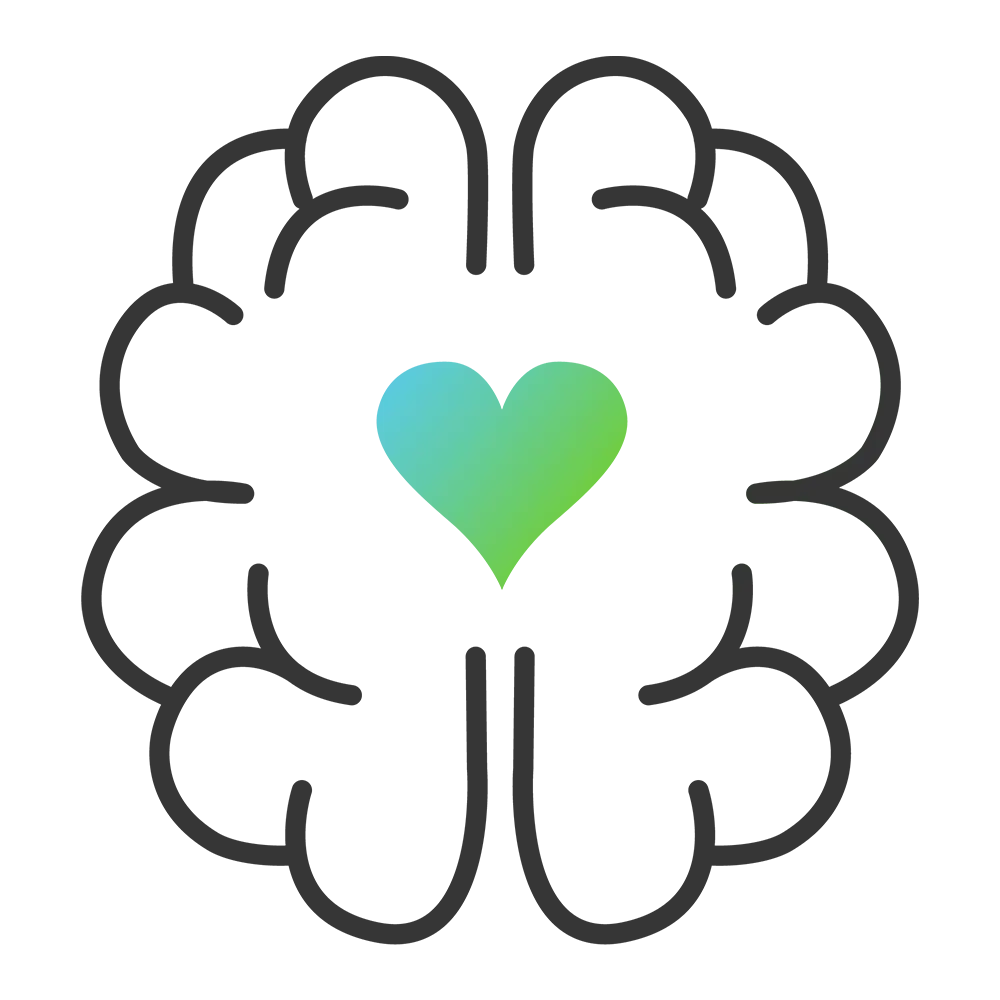
Future outlook
The demand for flexible PCBs is set to rise as industries push for more lightweight, compact, and high-performance electronics. Advances in flexible materials, ink formulations, and manufacturing techniques such as DIW will further enhance the capabilities of flexible PCBs. Emerging fields like wearable electronics, foldable cell phones, and flexible medical devices will experience many benefits from these innovations, driving market growth and creating new possibilities for advanced electronic products.
Our white papers
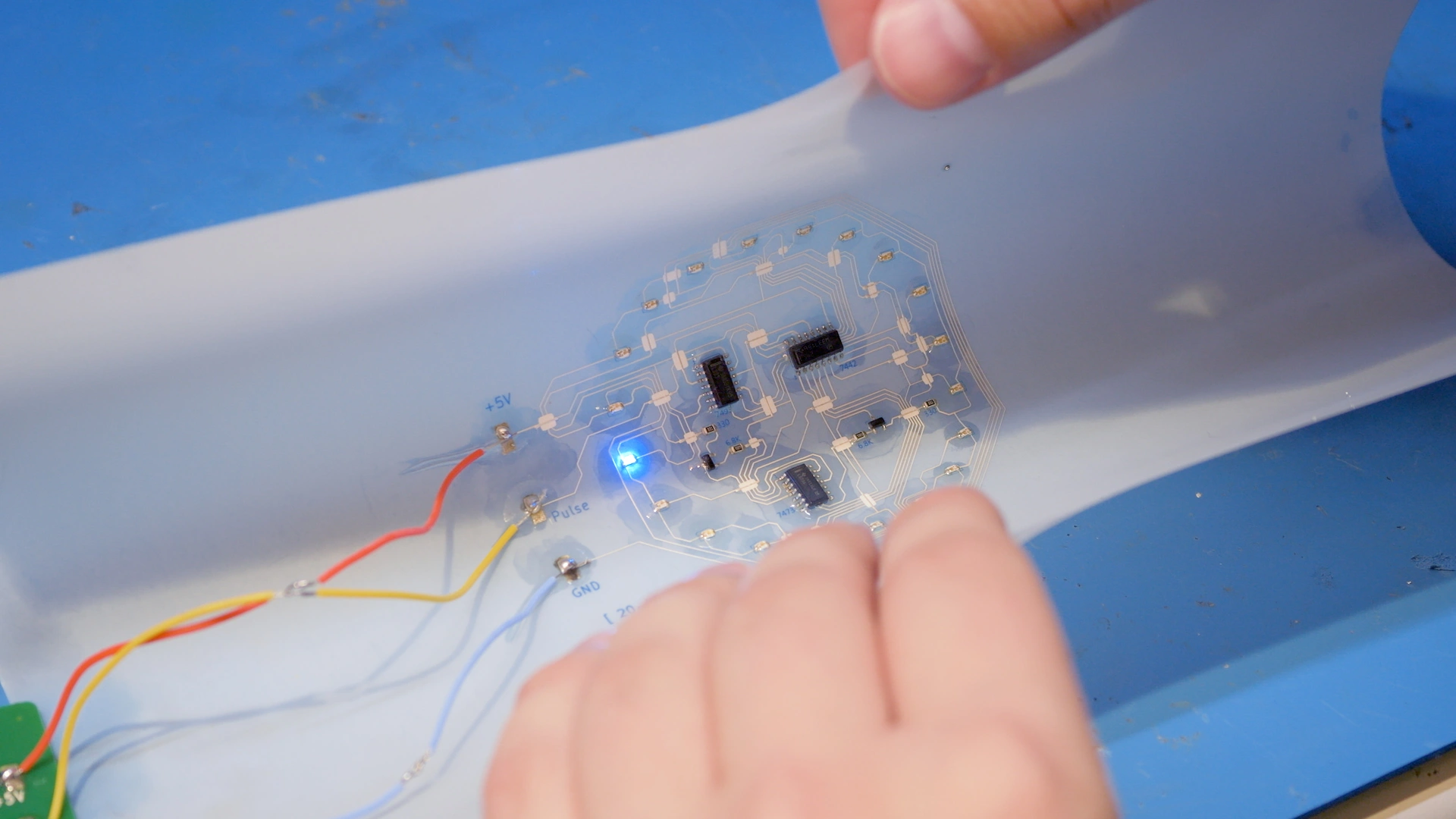
Printing a Flexible PCB with Silver Ink on PET
This project demonstrates how we redesigned an LED roulette circuit from FR4 to PET to withstand flexing with components populated.
Additional resources
References
[1] Grand View Research, Flexible Printed Circuit Boards Market Size, Share & Trends Analysis Report By Type (Software, Service), By End Use (Consumer Electronics, IT & Telecom, Industrial Electronics), By Region, And Segment Forecasts, 2019 - 2025, 2018.
[2] Precedence Research, Flexible Printed Circuit Boards Market Size, Share, and Trends 2024 to 2034, 2024
[3] Verified Market Research, Global Flexible Printed Circuit Boards Market Size By Application, By Type, By End-User Industry, By Geographic Scope And Forecast, 2023
[4] Meng, L., Ding, L., Khan, A.M. et al., Mathematical modeling of flexible printed circuit configuration: a study in deformation and optimization, Scientific Reports, 14, 14128, 2024
[5] Dahiya, Abhishek Singh, et al., Printed Interconnects for Heterogeneous Systems Integration on Flexible Substrates, Advanced Materials Technologies, 2024
Frequently asked questions
Can I combine rigid and flexible PCBs in one design?
Which materials are commonly used in flexible PCB board construction?
What should I keep in mind during flexible PCB design?